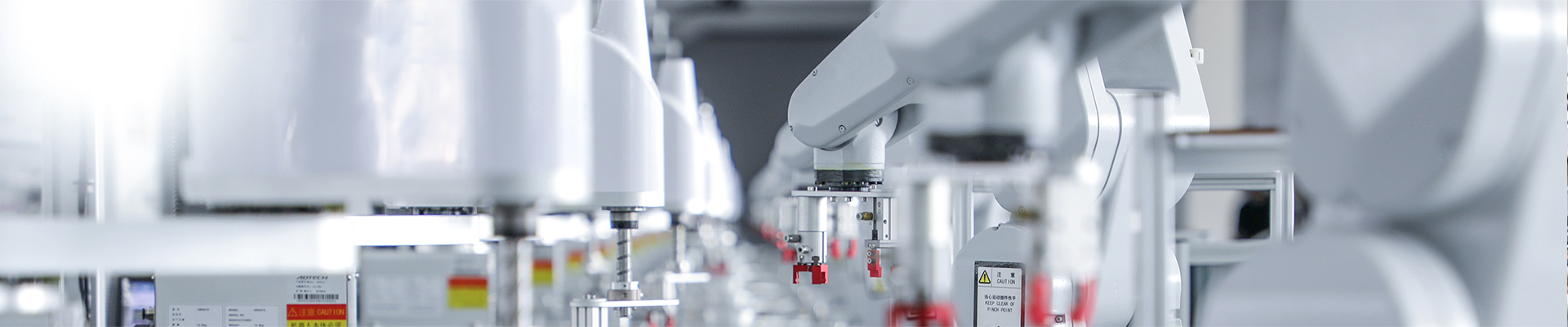
What are the specific challenges and best practices for pulling fiber optic cables, given their delicate nature?
2025-07-19Pulling fiber optic cables, whether for overhead ADSS (All-Dielectric Self-Supporting) installations or underground duct runs, presents unique challenges due to their delicate nature. Precision and care are paramount to avoid damaging the optical fibers and compromising signal integrity:
I. Key Challenges:
-
Low Allowable Pulling Tension: Fiber optic cables (especially the delicate glass fibers within) have very low maximum allowable pulling tensions compared to copper conductors. Exceeding this limit, even momentarily, can cause micro-bends, elongation, or breakage of the fibers, leading to signal loss or complete failure.
-
Minimum Bend Radius: Fiber optic cables have a strict minimum bend radius that must not be violated during pulling or installation. Kinking or bending too sharply can cause permanent signal attenuation or fiber breaks.
-
Twisting: Twisting the cable during pulling can induce torsional stress on the fibers, leading to similar damage as exceeding tension limits.
-
Abrasion and Crushing: The outer jacket, while protective, is still vulnerable to abrasion or crushing if dragged over rough surfaces or improperly handled.
-
Long Pulls & Multiple Bends (Underground): Friction accumulates rapidly in long underground pulls with multiple bends, making it difficult to keep tension below the low MAPT for fiber.
II. Best Practices and Specialized Equipment:
-
Precision Tension Control:
-
Automated Cable Pullers: Our advanced cable pullers for underground installations and hydraulic tensioners for overhead ADSS stringing offer precise, automatic tension control, ensuring the pulling force never exceeds the fiber cable's MAPT.
-
In-line Tension Monitors: Essential for real-time verification of pulling tension throughout the entire pull.
-
-
Specialized Pulling Eyes/Grips:
-
Swivel Pulling Eyes: Crucial for fiber optic cables. These allow the pulling rope to rotate independently of the cable, preventing any torsional forces from being transmitted to the delicate fibers.
-
Factory-Attached Pulling Eyes: Often preferred, as they are securely attached to the cable's central strength member (not just the jacket) and tested to safely transfer pulling force.
-
-
Large Radius Stringing Blocks (Overhead) / Cable Rollers (Underground):
-
Overhead: Stringing blocks for ADSS must have very large sheave diameters and smooth, non-metallic liners (polyurethane, nylon) to ensure the cable is gently supported and maintains its minimum bend radius.
-
Underground: Large-radius cable rollers are used in manholes and vaults to guide the cable smoothly around bends without exceeding the minimum bend radius.
-
-
High-Performance Cable Lubricants (Underground): Use only high-quality, non-damaging, and low-friction lubricants specifically designed for fiber optic cables to minimize pulling tension.
-
Cable Pushers/Feeders: These devices are often used at intermediate points in underground runs to "push" the cable, reducing the pulling tension required from the main puller.
-
Duct Integrity: Ensuring conduits/ducts are clean, clear of obstructions, and free from sharp edges or kinks before pulling.
-
Experienced Crews: Proper training and experience are vital, as even minor mishandling can result in significant damage and costly rework.
Our company offers specialized cable pulling equipment, from precision hydraulic tensioners for overhead ADSS to sophisticated underground cable pullers with integrated tension control, along with the necessary accessories like swivel pulling eyes and large-diameter rollers, all engineered to ensure the safe and reliable installation of delicate fiber optic cables.