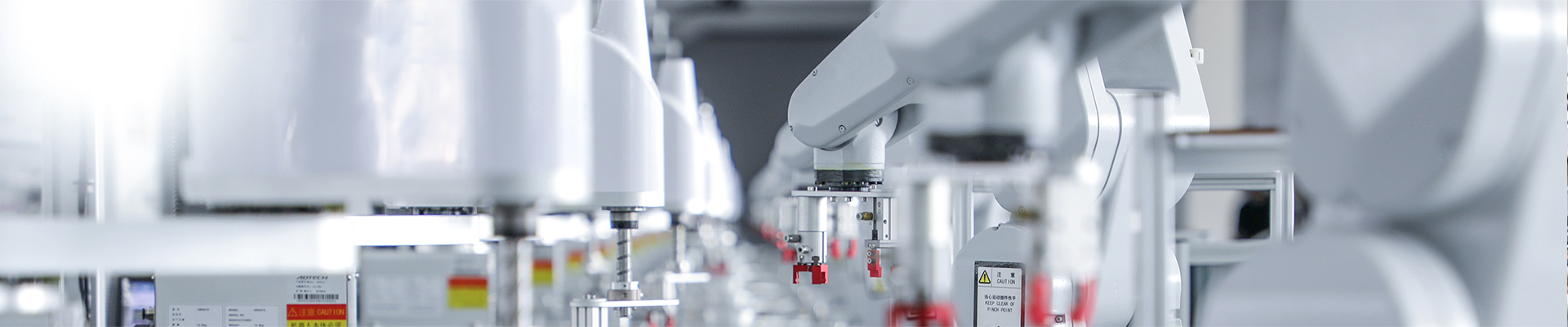
Multi-Bullwheel Tensioners
Multi-bullwheel tensioners are highly specialized and essential machines used in the construction of modern Extra High Voltage (EHV) and Ultra High Voltage (UHV) transmission lines. Their design specifically addresses the unique challenges of stringing bundled conductors.
What are Bundled Conductors and Why are They Used?
Before diving into the tensioners, it's important to understand why bundled conductors are so prevalent in EHV/UHV lines:
Reduced Corona Loss: At very high voltages, a single conductor can experience significant "corona discharge" (ionization of air around the conductor), leading to power loss, audible noise, and radio interference. Bundling conductors effectively increases the effective diameter of the phase, reducing the electric field gradient and minimizing corona.
Decreased Line Reactance: Bundling reduces the inductive reactance of the line, which improves power transfer capability and voltage regulation.
Increased Current Carrying Capacity: Multiple conductors allow for a higher current to be carried without excessive heating.
Lower Voltage Gradient: Spreading the charge over multiple conductors reduces the electric field stress on insulators.
Bundles can consist of 2, 3, 4, or even more "sub-conductors" per phase, held apart by spacers.
How Multi-Bullwheel Tensioners Work:
Multi-bullwheel tensioners are designed to handle these multiple sub-conductors simultaneously and with precise, independent control.
Multiple Bullwheel Sets: Instead of just one set of bullwheels, these machines feature two, three, four, or even six independent sets of bullwheels, each specifically designed to handle one sub-conductor of the bundle.
Independent Hydraulic Circuits (or synchronized): Each set of bullwheels is typically connected to its own dedicated hydraulic braking circuit. This allows for:
Independent Tension Control: The braking force (and thus the tension) on each individual sub-conductor can be precisely adjusted and monitored. This is crucial because even slight variations in tension across a bundle can lead to issues like twisting, uneven sag, or damage.
Electronic Synchronization: High-end models feature advanced electronic control systems that automatically synchronize the tension across all bullwheel sets. This ensures that all sub-conductors in the bundle are paid out at the exact same speed and under the precise same tension, preventing snaking or premature stressing of individual wires.
Large Diameter Bullwheels: Similar to single-bullwheel tensioners for transmission, multi-bullwheel units feature large diameter bullwheels (e.g., 1500 mm, 1800 mm, or even 2400 mm for HTLS/oversized conductors) to minimize bending stress on the conductors.
Wear-Resistant Grooves: The grooves on each bullwheel are lined with durable, replaceable materials (like MC nylon, polyurethane, or elastomer segments) to protect the expensive conductors from abrasion and damage.
Integrated Reel Stands: Many multi-bullwheel tensioners are paired with or include integrated multi-reel stands, allowing for multiple conductor reels to be loaded and paid out simultaneously in a controlled manner.
Advanced Control Systems: These machines are equipped with sophisticated HMI (Human-Machine Interface) systems, digital dynamometers for each conductor, speedometers, distance counters, and robust safety features like negative self-acting hydraulic brakes and overload protection. Radio remote control is standard.
Robust Diesel Power: Given the immense forces involved in tensioning heavy bundles, these machines are almost exclusively powered by powerful diesel engines driving the complex hydraulic systems.
Advantages of Multi-Bullwheel Tensioners for Bundled Conductors:
Simultaneous Stringing: The biggest advantage is the ability to string all sub-conductors of a bundle at the same time, drastically reducing project time and labor costs compared to stringing them individually.
Precise Tension Control per Sub-Conductor: Ensures that each wire in the bundle experiences the correct tension, preventing damage and ensuring uniform sag.
Prevents Twisting and Snaking: The synchronized payout maintains the relative positions of the sub-conductors within the bundle, preventing them from twisting around each other.
Optimized Sag and Clearance: Contributes to achieving the exact design sag and maintaining safe clearances, which is paramount for EHV/UHV lines.
Enhanced Safety: Reduces the amount of time workers are exposed to live line stringing operations and minimizes the risk of conductor damage or uncontrolled payout.
Efficiency: Streamlines the entire stringing process, especially for long spans typical of transmission lines.