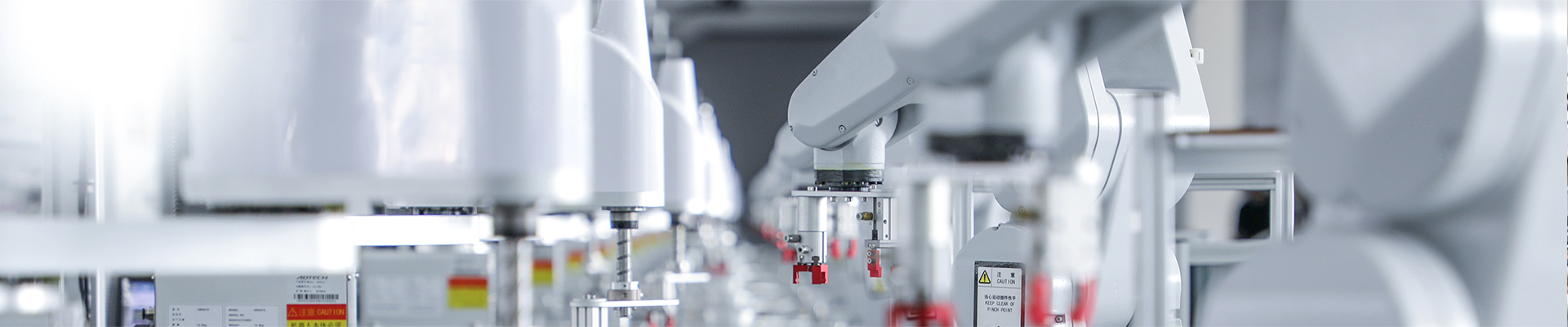
Electric Powered Pullers
Electric powered pullers for conductor stringing and power line installation are increasingly available as alternatives or supplements to traditional diesel-hydraulic pullers. They use electric motors (often AC or DC) coupled with hydraulic or direct mechanical drive systems to provide controlled, reliable pulling force for overhead transmission and distribution lines.
Overview based on recent specifications and industry standards:
Pulling capacity: Electric powered pullers cover a range of forces from about 50 kN (11,000 lbs) up to around 180 kN (40,000 lbs) or more, suitable for conductor and cable stringing on medium to high voltage lines.
Power and drive systems: These pullers employ high-efficiency electric motors combined with hydraulic transmission circuits or direct drives. Some are purely electric without hydraulic intermediates. The electric supply can be from mains power, generators, or increasingly from battery packs or hybrid systems for field portability.
Control and safety: Modern electric pullers incorporate electronic control panels with:
Pull force presetting and digital tension display
Automatic overload protection that stops pulling above preset tension
Closed-loop hydraulic circuits or electronic control of motor speed for smooth, stepless speed and tension adjustment
Emergency braking systems, often hydraulic spring-applied and electrically released
Data logging and remote control options in some advanced models
Environmental and operational advantages:
Electric powered pullers can have lower noise and pollution levels compared to diesel engines, making them suitable for urban or environmentally sensitive areas.
Easier maintenance and instant start/stop operation with electric power.
Increasing compatibility with automated and remotely controlled stringing setups.
Standards and Safety Considerations
According to the VDE Standard (VDE Spec 90014), electric powered pullers used in overhead line construction must:
Provide sufficient pulling power to resume conductor movement at full stringing force after stops.
Use bullwheels with suitable groove surfaces and sufficient diameter (at least 25 times the rope diameter) to protect rope life.
Ensure good current-carrying capacity between bullwheel and conductor or rope to avoid electromagnetic interference issues.
Have holding brakes (usually hydraulic spring-applied, hydraulically released) to maintain tension if power supply fails.
Include control panels with tension indicators and operator-set overload devices that automatically halt pulling when maximum tension is reached1.
Summary
Electric powered pullers are a modern, efficient alternative to diesel-hydraulic pullers in power line stringing. They combine electric motor power with hydraulic or direct drive systems, offering:
Controlled, stepless tension and speed adjustment
Integrated electronic safety, overload protection, and data monitoring
Reduced emissions and noise
Suitable pulling forces from moderate (~50 kN) to high (~180 kN) for transmission line work
For field applications, selecting an electric powered puller requires considering available power supply, required pulling capacity, control sophistication, and terrain-specific needs.