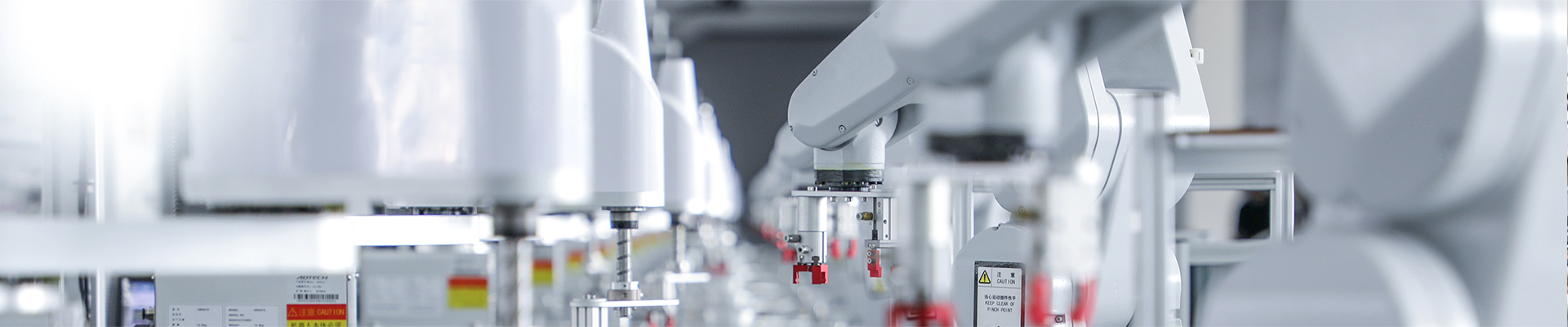
High-Strength, Low-Elongation Synthetic Ropes
High-strength, low-elongation synthetic ropes have revolutionized various industries, including power transmission and heavy cable pulling, by offering significant advantages over traditional steel wire ropes in specific applications. These ropes are engineered to be incredibly strong for their weight while stretching minimally under load, making them ideal for precise and efficient operations.
Key Characteristics:
High Strength-to-Weight Ratio: These ropes can be many times stronger than steel wire ropes of the same diameter, yet weigh a fraction. This dramatically reduces handling fatigue, simplifies logistics, and allows for the use of lighter equipment.
Low Elongation (Low Stretch): This is a critical property. Minimal stretch under load means:
Precise Tension Control: Easier to maintain constant tension during pulling and stringing operations.
Reduced Sag and Bounce: Conductors can be pulled to precise sag specifications without excessive over-tensioning to account for stretch.
Safer Operations: Less elastic energy stored in the rope, reducing the "snap-back" hazard if a rope breaks.
Excellent Abrasion Resistance: Many high-performance synthetic fibers are highly resistant to abrasion, which is important when the rope runs over sheaves, through blocks, or across rough terrain.
Good UV Resistance: Important for ropes used outdoors for extended periods.
Chemical Resistance: Generally resistant to common chemicals, fuels, and oils.
Water Resistance/Buoyancy: Many of these fibers are hydrophobic and can even be buoyant, which is a major advantage for marine or damp environments.
Non-Conductive (Generally): Most synthetic ropes are electrically non-conductive, offering an inherent safety benefit in proximity to energized lines (though safety precautions are always paramount).
Flexibility and Handling: More flexible and easier to handle than steel wire ropes, reducing kinks and improving ergonomics.
Common Materials Used:
The most prominent fibers for high-strength, low-elongation synthetic ropes in this context are:
UHMWPE (Ultra-High Molecular Weight Polyethylene) / HMPE (High Modulus Polyethylene):
Brand Names: Dyneema® (DSM) and Spectra® (Honeywell) are the most well-known brand names for UHMWPE fibers.
Properties: Exceptional strength-to-weight ratio (often cited as 8-15 times stronger than steel), very low stretch (typically less than 1-2% at working load), excellent abrasion resistance, UV resistance, and neutral buoyancy/floats in water.
Applications: Pilot lines, intermediate pulling ropes, utility rigging, arborist ropes, marine applications, and specialized lifting slings.
Aramid Fibers:
Brand Names: Kevlar® (DuPont), Technora® (Teijin), and Twaron® (Teijin).
Properties: Very high tensile strength, extremely low elongation, excellent heat resistance (higher melting point than HMPE), good chemical resistance.
Considerations: Can have lower abrasion and UV resistance compared to HMPE unless specifically coated or jacketed. More expensive than HMPE.
Applications: Often used in reinforcing materials (e.g., power transmission belts, hoses), protective clothing, and specialized ropes where heat resistance and extreme strength are paramount. Less common for long, continuous pulling ropes due to abrasion concerns, but may be used in specific heavy-duty rigging.
High-Tenacity Polyester (HTP):
Properties: Good strength, relatively low stretch (more than HMPE but less than nylon), excellent abrasion and UV resistance, good chemical resistance, and less expensive than HMPE or Aramid.
Applications: Often used as outer jackets/sheaths to protect a core of Dyneema or Aramid, or for general-purpose pulling ropes where the absolute lowest elongation isn't critical, but good strength and durability are needed (e.g., in some distribution stringing applications or as an outer layer for bundled conductor ropes).
Applications in Wire & Cable Installation:
Pilot Lines (Pulling Lines): These are the most common application. Drones or helicopters can easily carry lightweight HMPE pilot lines across spans, which then pull heavier pulling ropes, which then pull the conductor. This multi-stage process is made far more efficient and safer by using these lightweight, strong lines.
Intermediate Pulling Ropes: HMPE ropes are increasingly replacing steel wire ropes as intermediate pulling ropes for lighter to medium-duty conductors, as they are easier to handle, non-conductive, and reduce wear on pulling equipment.
Fiber Optic Cable Installation: For delicate OPGW or ADSS cables, the low elongation of HMPE or Aramid ropes ensures precise tensioning and prevents damaging overstress.
Specialized Rigging and Slings: Used for lifting and maneuvering heavy equipment or components around substations or difficult terrain due to their high strength and light weight.
Arborist and Tree Trimming: Used by line clearance crews due to their strength and light weight.