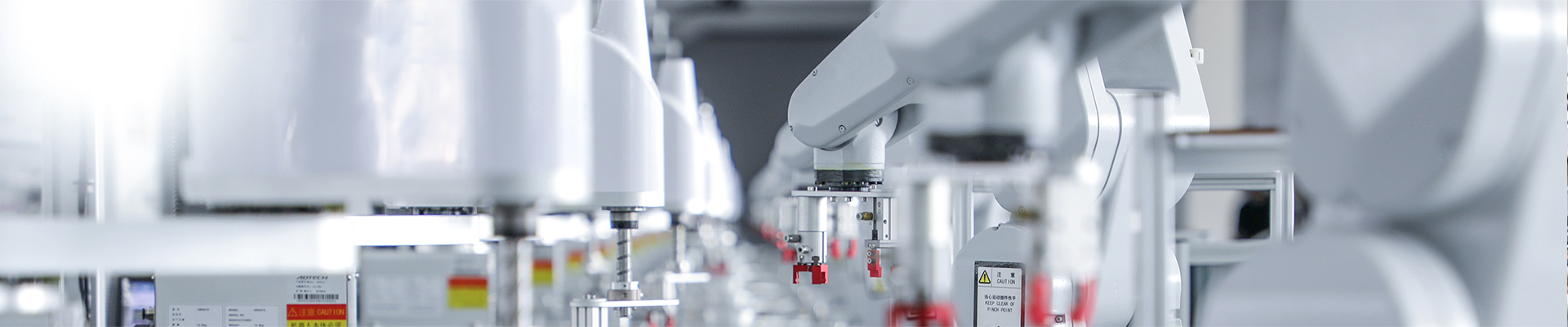
Integrated Braking Systems for Precise Tensioning
Integrated braking systems are absolutely fundamental to the precise and safe operation of modern hydraulic conductor tensioners. They are the core mechanism by which constant tension is maintained and catastrophic free-spooling of conductors is prevented.
What are Integrated Braking Systems for Precise Tensioning?
In the context of conductor tensioners, an integrated braking system refers to a comprehensive setup where the braking mechanism is built directly into the bullwheel (or drum) assembly and is precisely controlled by the machine's hydraulic and electronic systems. These systems are designed to convert the kinetic energy of the unwinding conductor into heat, which is then dissipated, all while maintaining a user-defined, constant resistance.
Key Components and How They Integrate:
Hydraulic Motor/Pump (Operating in Reverse): On a tensioner, the hydraulic pump/motor unit that would typically drive the puller's bullwheels is often configured to act as a brake. When the conductor pulls the bullwheels, the hydraulic fluid is forced through the system, creating resistance. The amount of resistance is precisely controlled by regulating the flow and pressure of this hydraulic fluid.
Bullwheels (or Drums): These are the physical interface with the conductor. They are designed with multiple grooves and a specific diameter to safely interact with the cable. The braking force from the hydraulic system is applied directly to the rotation of these bullwheels.
Hydraulic Braking Circuit: This involves a network of hydraulic lines, valves, and reservoirs. The tensioner's control system manipulates these components to precisely adjust the hydraulic pressure, thereby controlling the braking force.
Negative Self-Acting Hydraulic Brake (Fail-Safe Brake): This is a critical safety feature and a cornerstone of integrated braking systems in tensioners.
How it works: This type of brake is typically "spring-applied and hydraulically released." This means that springs hold the brake engaged by default. Hydraulic pressure is required to release the brake.
Safety Implication: If there's a sudden loss of hydraulic pressure (e.g., engine stalls, hydraulic line breaks, system malfunction), the springs automatically engage the brake, immediately stopping the bullwheels and preventing the conductor from free-spooling out of control. This is a vital safety mechanism for both personnel and equipment.
Electronic Control Unit (ECU) / PLC: This intelligent system receives real-time data from tension sensors (load cells) on the bullwheels. It then sends precise commands to the hydraulic braking system to make micro-adjustments, ensuring that the tension on the conductor remains constant at the pre-set value (Constant Tension Control System - CTCS).
Cooling System: Generating braking force converts kinetic energy into heat. Integrated braking systems, especially for high-capacity tensioners, require robust cooling systems (e.g., heat exchangers, fans) for the hydraulic oil to prevent overheating and ensure consistent performance.
Advantages of Integrated Braking Systems for Precise Tensioning:
Unparalleled Precision: The hydraulic and electronic integration allows for extremely fine and consistent control over the tension, far beyond what manual braking systems could achieve. This is critical for delicate conductors (like OPGW) and for maintaining strict sag and clearance specifications on transmission lines.
Enhanced Safety: The negative self-acting brake is a life-saving feature, preventing runaway conductors in the event of system failure. Constant tension also reduces the risk of snap-back and accidental contact.
Conductor Protection: By maintaining tension within safe limits and preventing jerking or slack, the system significantly reduces the risk of damage (scratches, nicks, stretching) to the expensive conductors.
Efficiency and Productivity: Automated tension control reduces the need for constant operator intervention, allowing for smoother and faster stringing operations. It also minimizes re-work due to improper sag.
Real-time Monitoring and Data Logging: The integrated nature allows for seamless capture of tension, speed, and distance data, which is invaluable for project management, quality assurance, and compliance.
Reduced Wear and Tear on Equipment: Smooth, controlled braking protects the tensioner itself from sudden shocks and overloads, extending its lifespan.
Versatility: Can be integrated into single bullwheel tensioners, multi-bullwheel tensioners (with independent braking control for each bundle), and puller-tensioners.
Types of Brakes (Within the Integrated System):
While the overall system is hydraulic, the actual friction elements can vary:
Disc Brakes: Commonly used within the hydraulic system, offering powerful and consistent braking performance.
Drum Brakes: Less common for the primary bullwheel braking on modern high-capacity tensioners, but might be found in auxiliary braking or older designs.
Electromagnetic Brakes: While primarily seen in some industrial applications or specialized electric vehicles, they are emerging as a component in some advanced electric-powered tensioners. However, the dominant braking method in hydraulic conductor tensioners remains hydraulic pressure acting on mechanical brakes.