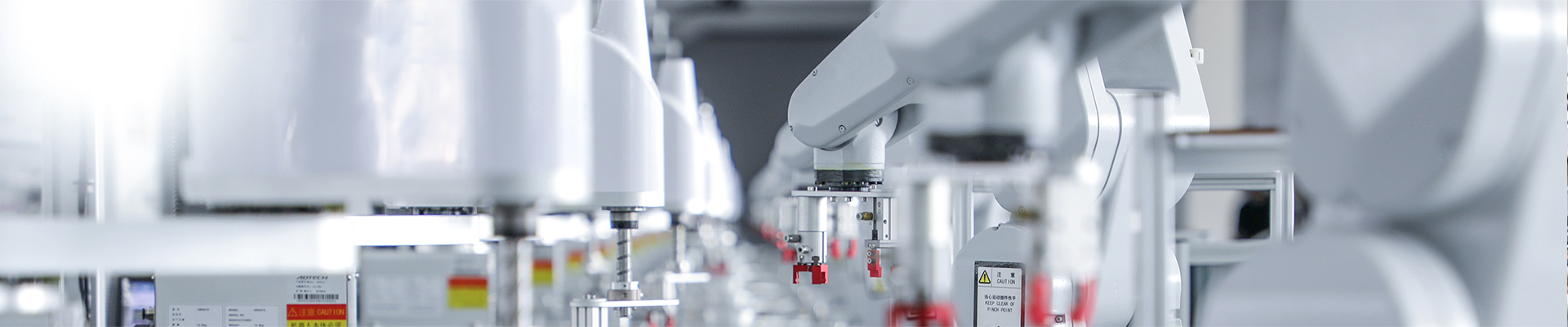
Reel Stands & Cable Winders
Reel stands and cable winders are fundamental pieces of equipment in the installation and management of power cables and conductors. While both deal with spools of wire, they serve distinct primary functions in the power utility sector.
Reel Stands (Cable Drum Jacks / Cable Drum Stands)
Purpose: Reel stands are designed to safely support large, heavy reels (drums) of conductor or cable, allowing them to be unwound (paid out) smoothly and controllably during stringing or installation operations. They are always used in pairs.
Key Features:
Support and Lifting:
Typically consist of two robust, independent upright frames (jacks) connected by a central spindle (shaft) that passes through the arbor hole of the cable reel.
Most feature a hydraulic jack mechanism on each stand, allowing for easy and controlled lifting of even very heavy reels off the ground. Manual screw jacks are used for lighter duty.
Many designs are foldable for easier transport and storage.
Braking System:
Essential for Tension Control: This is a critical feature, especially for overhead line stringing. As the conductor or cable is pulled from the reel, a braking system is required to maintain a slight back-tension, preventing the reel from over-spinning (freewheeling) and causing kinks, snarls, or uncontrolled payout.
Types of Brakes:
Mechanical Disc Brakes: Common, often with adjustable pads, providing friction to control payout speed and tension.
Hydraulic Disc Brakes: Offer more precise and consistent tension control, especially for heavier reels and higher payout speeds. They can be controlled by a manual hand pump or integrated into a larger hydraulic system.
Automatic Self-Braking: Some sophisticated models incorporate mechanisms that automatically apply brake force proportional to the payout speed or tension.
Capacity:
Rated by the maximum weight of the cable reel they can support (e.g., 3 tons, 5 tons, 10 tons, up to 20+ tons for very large transmission conductors).
Also specified by the maximum reel diameter and width they can accommodate.
Construction:
Heavy-duty welded steel framework (often painted or galvanized for corrosion resistance) is standard for durability and strength.
Spindles are typically solid steel, designed to withstand the bending moments from heavy reels.
Side supports with ball joints (as mentioned by Omac) can allow them to function on uneven ground.
Grounding bars and anchor rings are often included for safety and stability during operation.
Types of Reel Stands:
Fixed/Stationary Reel Stands: Basic stands for payout in one location.
Integrated Reel Stands with Tension Brakes: As highlighted by Dongfang, these are compact units where the stand and braking system are combined for easy setup.
Hydraulic Reel Stands with Tensioning Capabilities: These are the most advanced, offering precise hydraulic braking and sometimes even hydraulic drive (motorized rotation) for controlled payout or limited retrieval, often integrated with tensioners.
Reel Rollers / Cradle Reel Stands: A simpler, low-profile alternative for smaller, lighter reels, where the reel sits on a set of rollers, allowing it to spin. Less common for heavy-duty transmission line stringing.
Self-Loading Reel Stands/Trailers: Integrated into a trailer, these allow the reel to be loaded onto the stand without external lifting equipment, increasing efficiency and safety for mobile operations.
Cable Winders (Cable Spooling Machines / Cable Re-winders)
Purpose: Cable winders (or spooling machines) are primarily designed for winding and unwinding cables and wires onto reels or spools in a controlled and organized manner. Their function is often for storage, transport, measuring, cutting, or transferring cable between different reel sizes.
Key Functions in Cable Installation/Management:
Retrieval/Recovery: Used to retrieve previously strung pilot ropes, old conductors during reconductoring, or excess cable from a job site back onto a reel.
Storage and Organization: Neatly winding cables onto reels for long-term storage, preventing tangles and damage.
Measuring and Cutting: Many winders are integrated with measuring devices and cutting systems to prepare specific lengths of cable.
Transfer: Moving cable from a larger shipping reel to smaller, more manageable job-site reels or vice-versa.
Pre-stringing Winding: Winding specific lengths of cable or pilot rope onto smaller reels for easier deployment.
Key Features:
Powered Drive: Most industrial cable winders are motorized (electric or hydraulic) to provide precise and controlled winding/unwinding speed and torque.
Tension Control: Crucial for uniform winding. Winders often incorporate automatic tension management systems to prevent over-stretching or loose winding.
Layering / Level-Winding Mechanism: An essential feature that ensures the cable is wound evenly and neatly across the reel, preventing cross-overs and kinks that can damage the cable. This mechanism guides the cable back and forth across the reel flange.
Reel Mounting: Various methods for mounting reels, including shaftless designs, through-shaft designs, and designs with chucks to hold the reel securely.
Capacity: Rated by the maximum reel size and weight they can handle, as well as the cable diameter.
Types of Cable Winders:
Bench-Top / Manual Winders: For small cables (e.g., communication, data) or very low-volume applications.
Industrial Spooling Machines: Robust, motorized units for winding heavy-duty power cables. Can be semi-automatic or fully automatic.
Automatic Take-Up Cable Reels: Often spring-loaded or motorized, compact units for automatically retracting shorter cables (e.g., extension cords, power tool cords), more for convenience than heavy industrial use. (Jackway and YO-CHIUAN in search results seem to offer these consumer/light industrial types).