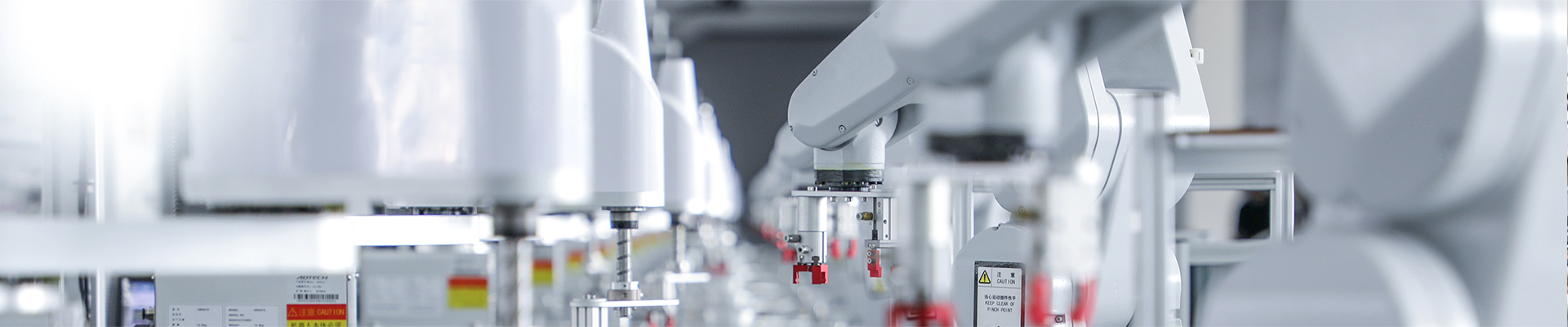
Hydraulic Conductor Tensioners
Hydraulic conductor tensioners are specialized machines that play a crucial role in the precise and safe installation of overhead power transmission lines, distribution lines, and telecommunication cables (like OPGW and ADSS). Unlike pullers, which pull the conductor, tensioners control the release of the conductor from the reel, applying a constant, pre-set braking force to keep it elevated above the ground and objects during stringing.
How Hydraulic Conductor Tensioners Work:
The fundamental principle is to apply a controlled braking force to the conductor as it unwinds from the reel. This is achieved through a robust hydraulic system:
Bullwheels (or Drums): The conductor is wrapped around grooved bullwheels (or sometimes drums for specific applications). These bullwheels are free to rotate but are connected to a hydraulic braking circuit.
Hydraulic Braking System:
A hydraulic pump and motor system (often driven by a diesel engine) provides the power.
Instead of generating pulling force, the hydraulic system creates a resistance to the rotation of the bullwheels. This resistance is precisely controlled by regulating the hydraulic pressure.
The conductor unwinds from its reel, passes over the tensioner's bullwheels, and is then pulled by a puller machine located at the other end of the stringing section.
Automatic Tension Control (ATC): Modern hydraulic tensioners are equipped with advanced control systems (often electronic and microprocessor-based) that monitor the tension on the conductor in real-time.
The operator sets a desired tension level.
The system automatically adjusts the hydraulic braking force to maintain that constant tension, compensating for variations in line speed, friction, or terrain. This is crucial for preventing excessive sag or over-stressing the conductor.
Integrated Reel Stands: Many tensioners come with an integrated hydraulic reel winder/reel stand, which allows for easy loading and unloading of conductor reels and provides a controlled payout of the conductor.
Safety Features:
Negative self-acting hydraulic brake: This ensures that if the hydraulic system loses pressure or a power failure occurs, the brakes automatically engage, preventing uncontrolled release of the conductor.
Over-tension protection: Alarms and automatic shutdowns prevent exceeding safe tension limits.
Emergency stop buttons.
Digital dynamometers: Provide accurate, real-time tension readings.
Why Tensioning is Critical:
Protecting the Conductor: Prevents the conductor from dragging on the ground, trees, buildings, or other obstructions, which could cause scratches, nicks, or other damage that compromises its integrity.
Safety: Keeps the conductor elevated, reducing the risk of accidental contact with personnel, vehicles, or equipment.
Controlling Sag and Clearances: Ensures the conductor is strung to the correct sag and maintains adequate clearances from the ground and other structures, which is vital for safe and reliable operation of the transmission line.
Precise Installation: Allows for accurate and consistent conductor installation according to engineering specifications.
Efficiency: Enables faster and more controlled stringing operations.
Types of Hydraulic Conductor Tensioners:
Single Conductor Tensioners: Designed to tension one conductor at a time. These are typically smaller units, often used for distribution lines or single-conductor transmission lines.
Multi-Conductor (Bundled) Tensioners: These are crucial for EHV/UHV transmission lines, which often use bundled conductors (two, three, four, or even more conductors per phase). These tensioners feature:
Multiple pairs of bullwheels: Each pair handles one conductor of the bundle, often with independent control for precise tensioning of each individual conductor.
High capacity: Designed to handle the combined weight and tension of multiple heavy conductors.
Synchronization: Advanced electronic systems ensure all conductors in the bundle are tensioned equally to prevent twisting or uneven sag.
Puller-Tensioner Combination Units: As discussed previously, these highly versatile machines can switch between pulling and tensioning modes, making them ideal for reconductoring projects where an old line is pulled out while a new one is simultaneously tensioned in.
Specialized Tensioners:
OPGW/ADSS Tensioners: Often smaller and more sensitive, designed for delicate fiber optic cables to prevent damage.
Winch-type Hydraulic Brake Tensioners: Less common for main line stringing but used for specific applications where a drum-based tensioning method is more suitable.