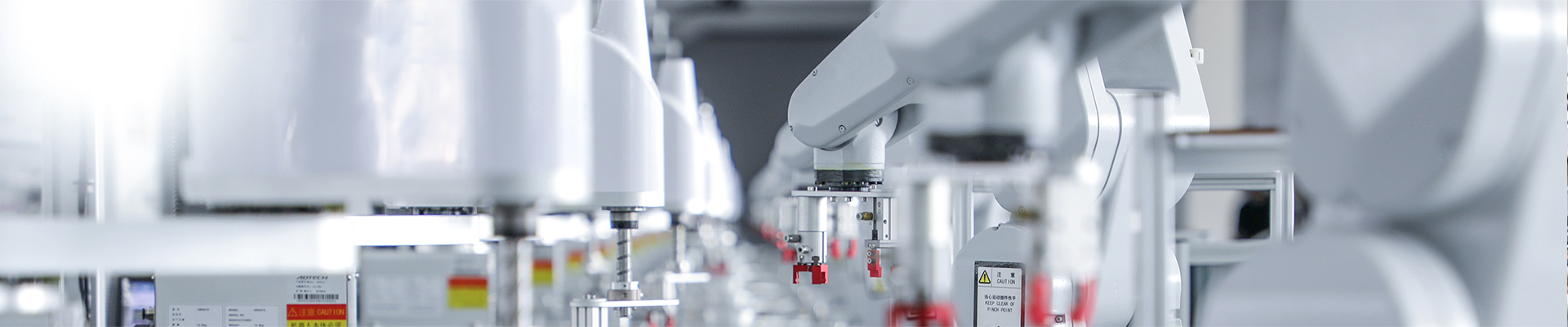
Non-Conductive Pilot Wires for Safety
Why Non-Conductive Pilot Wires are Crucial for Safety:
The primary reason for using non-conductive pilot wires is to eliminate or drastically reduce the risk of accidental electrical contact and electrocution during the initial stages of power line stringing.
Here's why it's so vital:
Proximity to Energized Lines: New power lines are often strung in corridors where existing lines (transmission or distribution) are already energized. Even if lines are de-energized, there's always a risk of induced voltage from nearby energized lines. A conductive (steel) pilot wire could become energized, posing a severe threat to ground crews and equipment.
Unpredictable Contact: During the initial pulling of a pilot wire (especially by drone or helicopter), there's a possibility of it brushing against a live conductor, structure, or even wet ground. A non-conductive rope prevents the propagation of current in such scenarios.
Wet Conditions: Rain, fog, or high humidity can make otherwise "insulating" materials conductive if they absorb moisture or are not properly designed. Dedicated non-conductive ropes are engineered to maintain their dielectric properties even when wet.
Worker Safety: Linemen and ground crews are directly handling these ropes. Using non-conductive materials significantly reduces the risk of arc flash, shock, and electrocution if accidental contact occurs. This is paramount for occupational safety.
Equipment Protection: Prevents potential damage to pulling equipment (winches, drones) if the pilot line becomes energized.
Key Characteristics of Non-Conductive Pilot Wires:
Dielectric Strength: The ability to withstand high voltage without conducting electricity. This is the defining characteristic and is tested rigorously.
High-Strength, Low-Elongation Fibers: Typically made from UHMWPE/HMPE (Dyneema®, Spectra®) or sometimes Aramid (Kevlar®) fibers. These materials inherently possess excellent dielectric properties in their dry state.
Hydrophobic (Water-Repelling): The fibers are designed to repel water, preventing moisture absorption that could compromise dielectric performance. Some ropes may have additional coatings or treatments to enhance water resistance.
UV Resistance: For outdoor exposure.
Abrasion Resistance: To withstand friction as they run through blocks.
Lightweight: Crucial for ease of handling, especially for drone or helicopter deployment.
Non-Twisting Construction: Often braided in constructions (e.g., 12-strand) that prevent rotation under load, similar to anti-twist steel ropes.
How They are Used in Practice:
The non-conductive pilot wire is the very first line strung. Once this non-conductive pilot wire is across the span, it can then be used to pull a heavier, potentially conductive pulling rope (like an anti-twist steel wire rope) into place. This allows the safe establishment of the pulling path before introducing any conductive elements. For live-line work, specific "dielectric work ropes" and "dielectric rescue ropes" are used, which are even more strictly tested for their insulating properties.