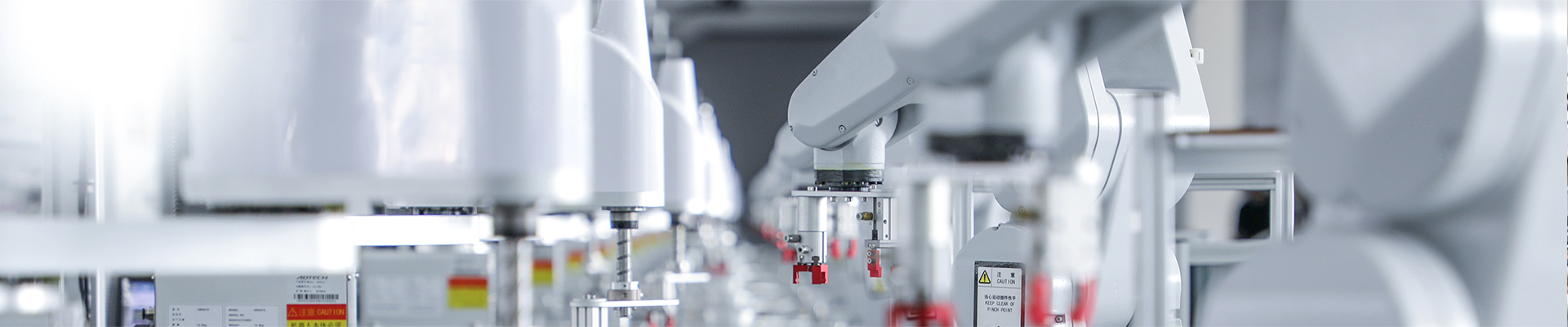
Motorized Take-up Reel Winders for Large Cable Drums
Motorized take-up reel winders for large cable drums are advanced machines designed for the controlled and efficient winding (or re-winding/retrieving) of heavy and large-diameter cables or conductors onto equally large drums. Unlike simple reel stands which primarily facilitate payout with braking, these units are actively driven to pull and spool the cable.
What are Motorized Take-up Reel Winders?
These are powerful machines equipped with a motor (electric or hydraulic) that drives the rotation of the cable drum. Their primary function is to retrieve cable onto a drum, or to transfer cable from one drum to another (often from a large shipping drum to a smaller, job-specific drum, or vice versa), or to spool newly manufactured cable onto drums.
Key Features and Operating Principles:
Motorized Drive System:
Electric Motor: Often combined with a gearbox for high torque at various speeds. Variable Frequency Drives (VFDs) are commonly used to provide precise speed and torque control, allowing for smooth acceleration/deceleration and constant tension winding.
Hydraulic Motor: Offers high power density and precise control, especially for very heavy loads. These are powered by a dedicated hydraulic power unit (HPU).
Engine-Driven (for mobile units): Some large field-based units are self-contained with a diesel engine powering a hydraulic pump for the winding motor.
Tension Control:
Crucial for quality winding. The system actively monitors and adjusts the winding torque to maintain a constant tension on the cable as it's wound. This prevents over-stretching, damage, or loose/uneven layering.
Load cells, dancer arms, or sophisticated control algorithms are used to achieve this.
Level-Winding (Traverse) Mechanism:
Automated Cable Laying: This is a hallmark feature. A traverse unit (often a lead screw or linear actuator) automatically guides the cable back and forth across the reel as it's being wound. This ensures a neat, even, and compact lay of the cable on the drum, preventing tangles, cross-overs, and maximizing the drum's capacity while protecting the cable.
Some advanced systems use sensors and PLC control for highly precise layering.
Reel Mounting & Lifting:
Shaftless Design: Many heavy-duty winders use a shaftless design where the reel is cradled or mounted on two independent side arms. This makes loading and unloading drums much easier and faster, as there's no heavy spindle to maneuver. Hydraulic arms lift the reel into position.
Through-Shaft Design: For some models, a heavy-duty shaft passes through the center of the reel, supported by bearings on either side.
Integrated Lifting Systems: Hydraulic lifting mechanisms are standard to safely raise and lower large, heavy cable drums.
Control System:
Modern winders feature intuitive control panels, often with touchscreens, allowing operators to set winding speed, tension, cable length (with integrated measuring systems), and control the traverse.
Emergency stop buttons and safety interlocks are standard.
Capacity:
Rated for the maximum weight of the cable drum they can handle (e.g., 5 tons, 10 tons, 20 tons, or even more for offshore/industrial applications).
Also specified by the maximum reel diameter and width.
Applications:
Retrieval/Recovery of Old Conductors: During reconductoring projects on transmission lines, these machines are used to pull down and neatly wind the old conductors onto drums for recycling or disposal.
Pilot Rope Recovery: After pulling in a new conductor, the pilot rope (steel wire rope) needs to be wound back onto its drum.
Cable Manufacturing Facilities: Used extensively in cable factories to spool finished cables onto shipping or storage drums.
Cable Distribution Centers: For cutting specific lengths of cable from large master reels and winding them onto smaller drums for customer orders.
Underground Cable Laying: Retrieving pulling ropes or old cables from conduits.
Offshore/Marine Applications: Used on vessels for laying and retrieving subsea cables, umbilicals, or even large ropes.
Mining & Industrial Plants: For managing large power cables for mobile equipment (e.g., cranes, excavators, conveyors).