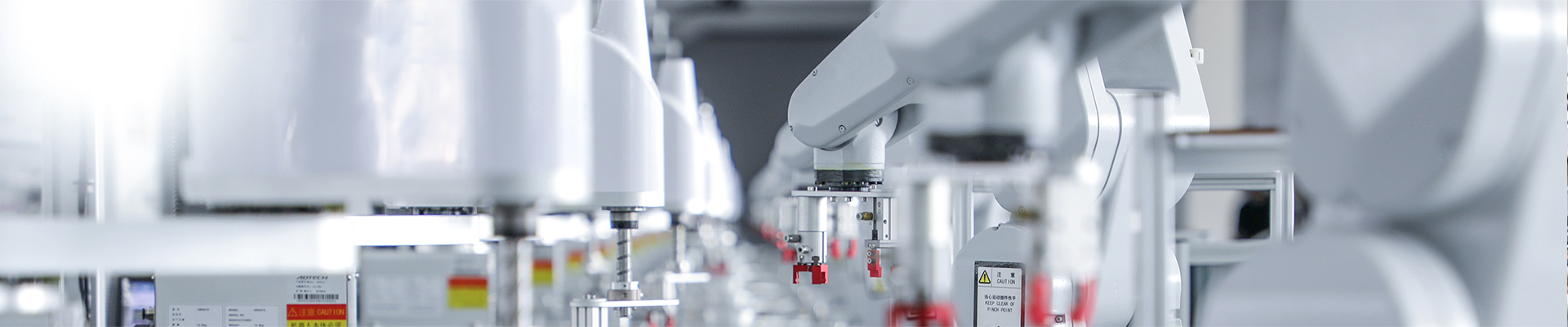
Stringing Blocks & Sheaves
Stringing blocks and sheaves (the wheels within the blocks) are indispensable tools in power line and cable installation. They are positioned along the stringing path, typically suspended from poles, towers, or temporary structures, to guide the pulling rope and conductor smoothly from the tensioner to the puller. They allow the conductor to be pulled over long distances and around obstacles with minimal friction and damage.
What are Stringing Blocks & Sheaves?
A stringing block is a frame that houses one or more sheaves (pulleys). The entire assembly is designed to attach securely to a support structure and allow the conductor or pulling rope to pass through it with minimal friction and without coming into contact with the structure itself.
Key Components:
Sheave(s) / Roller(s): The rotating wheel(s) that the conductor or rope runs over.
Material: Sheaves are commonly made from:
Aluminum Alloy: Lightweight, strong, and highly durable. Often polished to reduce friction.
Urethane Lined Aluminum: Aluminum sheaves with a premium polyurethane lining cast onto the groove. This provides a softer, non-abrasive surface that protects the conductor's outer strands, especially important for sensitive conductors like ACSR/AW, OPGW, or insulated cables. It also offers good resistance to oils, ozone, and compression set.
Neoprene Lined Aluminum: Similar to urethane, neoprene provides a protective and cushioned surface. Some neoprene linings can be semi-conductive, designed to help conduct induced voltages to ground during stringing.
Nylon/Polyamide: Used for lighter duty blocks, especially for fiber optic cables or smaller distribution lines. Offers good dielectric properties (non-conductive) and is gentle on sensitive cable jackets.
Bearings: High-quality stringing blocks use sealed, anti-friction ball bearings or bronze bushings. These are crucial for smooth rotation, minimizing friction, and reducing the load on the pulling equipment and the conductor. They are often packed with synthetic aviation grease for long-term lubrication and resistance to extreme conditions.
Groove Profile: The shape of the groove on the sheave is designed to cradle the specific diameter and type of conductor being strung, ensuring proper seating and preventing damage.
Frame: The rigid structure that holds the sheave(s) and provides attachment points.
Material: Typically high-strength aluminum alloy (for lightweight and durability) or galvanized steel (for heavier duty or specific applications).
Design: Varies widely depending on the type of block (e.g., full frame, half frame, universal, specialized).
Attachment Hardware: Mechanisms for securely attaching the block to the tower, pole, or crossarm.
Hooks/Clevises: Various types like snap hooks, ball clevises, Y-ball clevises, or crossarm brackets. These are designed for quick and secure installation and removal.
Safety Latches: Essential to prevent accidental disengagement.
Throat Opening / Gate: A design feature that allows for easy insertion and removal of the conductor or pulling rope, especially after splices or connectors have passed. Many blocks have a "gate" that can be opened for this purpose and then securely latched.
Grounding Attachments (Optional but important): Some blocks, especially for transmission lines, may include a grounding roller or attachment that helps dissipate induced currents from the conductor to ground as it passes through the block, enhancing safety.
Types of Stringing Blocks:
Single Sheave Blocks: The most common type, used for stringing single conductors, pilot ropes, OPGW, or ADSS cables. Sheave diameters vary widely (e.g., 7" for distribution, up to 53" or more for large transmission conductors).
Bundle Blocks (Multi-Sheave Blocks): Designed for stringing bundled conductors (2, 3, 4, or 6 conductors per phase). These blocks contain multiple sheaves, each precisely aligned to carry one sub-conductor of the bundle, maintaining their relative spacing.
Two-Sheave Blocks: For double bundles.
Three-Sheave Blocks: For triple bundles.
Four-Sheave Blocks: For quad (four) bundles.
Five or Six-Sheave Blocks: For very large bundles.
Corner / Angle Blocks: Specialized blocks designed to handle the increased side loads and angles when a line changes direction. They often have multiple sheaves arranged to guide the conductor smoothly around a bend.
Helicopter Stringing Blocks: Lightweight blocks designed for rapid deployment by helicopters.
Uplift / Hold-Down Blocks: Used in areas where the conductor might lift off the block (e.g., sag sections, high winds) or needs to be held down.
Underground / Fiber Optic Quadrant Blocks: Used for guiding cables around bends in underground ducts or trenches. Often have a series of rollers within a frame.
Importance of Proper Selection and Maintenance:
Conductor Protection: The right sheave material and diameter are critical to prevent damage to the conductor, which can compromise its long-term integrity and performance.
Minimizing Friction: Well-maintained blocks with high-quality bearings reduce friction, which means less pulling force is required from the puller, extending equipment life and potentially allowing longer stringing sections.
Safety: Properly rated blocks prevent failures that could lead to dropped conductors, equipment damage, or injury. Regular inspection (for cracks, bearing wear, sheave lining damage, and proper latching mechanisms) is paramount.
Load Capacity: Blocks have a Working Load Limit (WLL) and Breaking Load (BL). It's critical never to exceed the WLL and to account for factors like the angle of wrap, which significantly increases the actual load on the block compared to the conductor tension itself.