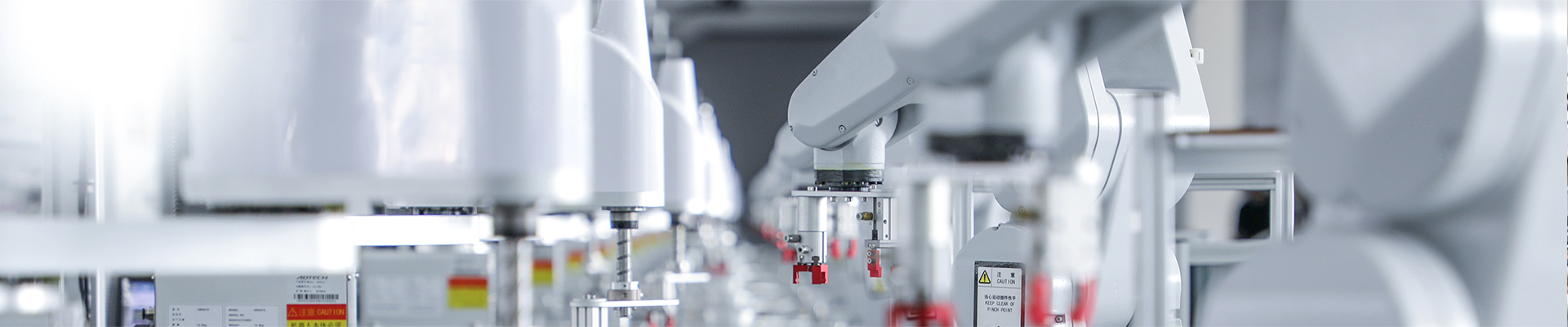
Helicopter & Drone Compatible Stringing Blocks
The increasing use of helicopters and drones for power line stringing, particularly in challenging terrains or environmentally sensitive areas, has driven the development of specialized stringing blocks. These "air-compatible" blocks prioritize light weight, quick attachment, and robust design to withstand aerial deployment and retrieval.
Why Helicopter & Drone Compatibility Matters for Stringing Blocks:
Traditional stringing blocks are often heavy and require significant human effort or ground-based machinery for installation on towers. When using aerial methods:
Weight is Critical: Helicopters and drones have payload limitations. Every kilogram saved on the block means more payload for other equipment, longer flight times, or reduced fuel consumption.
Rapid Deployment: Blocks need to be quickly and securely attached by aerial crews (often from a hovering helicopter) or autonomously by drones. This requires specialized attachment mechanisms.
Durability for Aerial Handling: Blocks may be subjected to rougher handling during aerial transport and placement.
Operator Safety: Designs often incorporate features that simplify remote handling and minimize risks to ground crews.
Key Characteristics of Helicopter & Drone Compatible Stringing Blocks:
Ultra-Lightweight Construction:
Frame Material: High-strength aluminum alloys are almost exclusively used for the frame to minimize weight while maintaining structural integrity.
Sheave Material: Often Nylon (MC Nylon) or lightweight composite materials are preferred for sheaves over heavier aluminum, especially for smaller blocks. For larger blocks, lightweight aluminum sheaves (sometimes with a very thin lining) are still used.
Optimized Design: Engineers strip away any unnecessary material, using advanced CAD and FEA (Finite Element Analysis) to optimize the design for strength-to-weight ratio.
Specialized Attachment Mechanisms:
Integrated Helicopter Arm / Eye: Many helicopter blocks have a dedicated, robust attachment point (often a large eye or a short arm) designed for quick connection to a helicopter's hook or sling.
Spring-Loaded Side Gates: A common feature to allow easy, one-handed insertion of the pilot rope or conductor. The spring ensures the gate automatically closes and latches securely once the line is in place.
Hot-Stick Compatible: Often designed so that components (like the gate or attachment pins) can be manipulated using hot sticks, allowing for safer installation near energized lines.
Remote Release/Locking: For drone applications, some advanced blocks might incorporate mechanisms for remote locking or release, though this is still an emerging area.
Large Diameter Sheaves (Still Important): While lightweight, these blocks still prioritize conductor integrity. Therefore, even for aerial deployment, they maintain appropriately large sheave diameters (e.g., 500mm, 660mm, 822mm, up to 1040mm for larger conductors) to minimize bending stress on the conductor, especially for OPGW and ADSS.
Smooth, Low-Friction Operation:
High-Quality Bearings: Precision, sealed, anti-friction bearings are critical for smooth sheave rotation, reducing drag and making the pulling process more efficient.
Sheave Lining: Urethane or neoprene linings are still often applied to protect the conductor, especially for sensitive cables like OPGW/ADSS.
Specific Use Cases:
Primarily used for pilot wire stringing (often non-conductive, high-strength synthetic ropes like Dyneema) as this is the lightest line to pull first.
Also used for OPGW and ADSS cable stringing, where light weight and delicate handling are crucial.
Can be used for single conductor distribution or lighter transmission reconductoring.