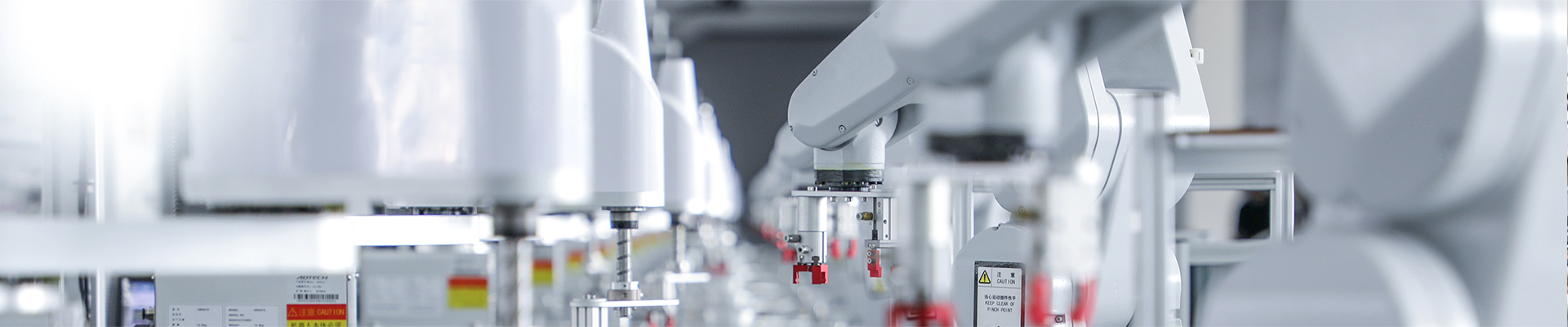
Hydraulic Compressors for Jointing & Dead-Ending
Hydraulic compressors (more commonly called hydraulic crimpers or hydraulic compression tools) are indispensable for ensuring strong, reliable, and electrically conductive connections when jointing (splicing) power line conductors or attaching dead-end fittings. These tools exert immense force to cold-weld the conductor and the connector/fitting together, creating a connection that can withstand significant mechanical tension and carry high electrical current without excessive resistance or heating.
How Hydraulic Compressors Work for Power Lines:
The basic principle involves using hydraulic pressure to force a set of dies to compress a metal sleeve or connector onto a conductor.
Conductor Preparation: The ends of the conductors to be joined or the conductor end to be dead-ended are carefully cleaned and brushed to ensure good electrical contact.
Sleeve/Connector Placement: An aluminum, copper, or bimetallic (e.g., aluminum barrel with a copper tongue) compression sleeve (splice connector) or dead-end fitting is slipped over the conductor(s). These connectors are precisely engineered to match specific conductor types and sizes.
Die Selection: The correct dies (molds) for the specific conductor and connector size are selected and inserted into the crimping head of the hydraulic compressor. Dies are crucial; using the wrong die can result in a faulty connection that can overheat or fail mechanically.
Compression: The operator positions the tool around the sleeve/connector. Hydraulic fluid is then pumped to a cylinder within the tool, extending a ram that forces the dies together. This extreme pressure permanently deforms the sleeve onto the conductor, creating a solid, low-resistance connection.
Hexagonal or Circular Compression: Most compression for overhead lines uses either a hexagonal crimp (common for many standard conductors and connectors) or a circular/indent crimp for specific applications.
Inspection: After crimping, the joint is inspected to ensure the correct number of crimps have been made in the specified locations, and that the crimps are uniform and complete.
Types of Hydraulic Compressors for Power Line Work:
These tools vary by the amount of force they can generate, their power source, and their portability.
Manual Hydraulic Crimpers (Hand-Operated):
Description: Self-contained tools where the operator manually pumps a handle to build hydraulic pressure and perform the crimp.
Force: Typically generate up to 12-15 tons (100-150 kN) of force.
Application: Suitable for smaller to medium-sized conductors (e.g., up to 400-500 mm² ACSR) and for distribution line work or smaller transmission conductors where portability is key and the number of crimps is limited.
Advantages: Portable, no external power source needed, relatively inexpensive.
Disadvantages: Labor-intensive for multiple crimps, limited force for very large conductors.
Battery-Powered Hydraulic Crimpers:
Description: These tools integrate a small electric motor and hydraulic pump, powered by a rechargeable battery (e.g., 18V or 21V Lithium-ion). The operator presses a button to initiate the crimping cycle.
Force: Range from 5-ton handheld units up to 12-ton or 15-ton models, sometimes even higher.
Application: Ideal for frequent crimping on distribution lines and smaller transmission conductors, offering convenience and speed.
Advantages: Portable, fast, less operator fatigue, no external power source needed during operation.
Disadvantages: Battery life management, higher initial cost than manual tools. (Cembre, Marlow are prominent in this category).
Remote Head Hydraulic Crimpers with External Power Source:
Description: These consist of a separate crimping head (which holds the dies) connected by high-pressure hydraulic hoses to an external hydraulic power unit.
Power Units: Can be:
Manual Foot/Hand Pumps: Simple, portable, but require operator effort.
Electric Hydraulic Pumps: Powered by an electrical outlet or generator.
Gasoline/Diesel Engine-Driven Hydraulic Pumps: Self-contained, powerful units for remote locations without electricity.
Force: Can generate very high forces, from 20 tons (200 kN) up to 100 tons (1000 kN) or even 300 tons (3000 kN) for large transmission line conductors.
Application: Essential for large ACSR/AAAC conductors on high-voltage transmission lines (110kV and above, as noted in search results), where significant force is required for mid-span joints and heavy-duty dead-ends.
Advantages: Extremely high force capability, faster crimping cycle for large joints, versatile (one power unit can operate different heads), suitable for continuous operation.
Disadvantages: Less portable (separate head and pump), require a power source for the pump (unless it's engine-driven), higher cost. (Dongfang Power Transmission Equipment, Ningbo Marshine Power Technology, and Tesmec offer these types of systems).
Key Features and Considerations:
Compression Force: The most critical specification, measured in kN or tons. Must match the requirements of the conductor and connector being used.
Die Sets: Essential accessories. Each conductor/connector combination requires a specific die. Tools often come with a selection of dies, or dies can be purchased separately. Hexagonal dies are very common.
Opening/Jaw Size: Determines the maximum diameter of connector the tool can accommodate.
Stroke Length: The distance the ram travels to complete the crimp.
Durability: Robust construction to withstand heavy use in field conditions.
Safety Features: Pressure relief valves, automatic retraction (for battery tools), ergonomic design, and secure handling.
Standards: Tools and connectors should comply with relevant industry standards (e.g., ANSI C119.4, IEC).
Leading International Manufacturers: