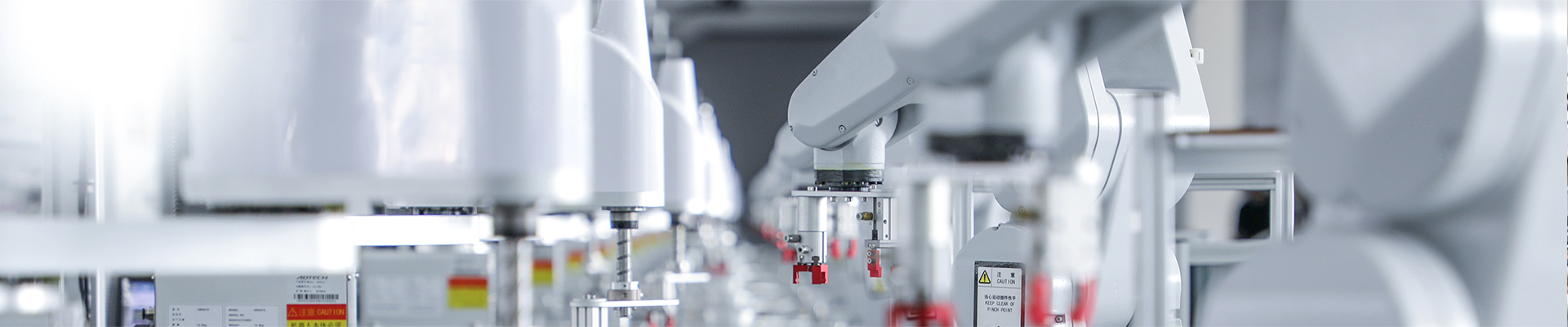
Conductor Grips & Clamps
"Conductor grips" and "conductor clamps" are broad terms used for devices that securely grasp or hold electrical conductors. In the context of overhead power line stringing, they refer to specialized tools and hardware critical for various stages of the installation process.
It's important to distinguish between:
Temporary Grips (Pulling Grips/Come-Alongs): Used during the stringing process to temporarily hold, pull, tension, or sag the conductor.
Permanent Clamps (Suspension, Dead-End, Strain Clamps): Used as final hardware to secure the conductor to the pole/tower for its operational life.
1. Conductor Grips (Pulling Grips / Come-Alongs)
These are temporary tools used during the dynamic stringing and sagging phases of conductor installation. Their primary function is to securely grasp the conductor without damaging it, allowing tension to be applied.
Key Features:
Non-Slip Grip: Designed to hold firmly under high tension without slipping.
Conductor Protection: Jaws are specifically shaped and sometimes lined to minimize deformation, scoring, or damage to the conductor's outer strands.
High Strength: Rated for the substantial pulling forces required for stringing and sagging.
Ease of Use: Designed for quick attachment and release by linemen.
Material: Usually made from high-strength forged steel or aluminum alloy (for lighter applications or specific conductor types like ACSR).
Common Types:
Automatic Grips / Self-Gripping Clamps (Come-Alongs): These are the most common. They have a spring-loaded or cam-action jaw mechanism that automatically tightens its grip on the conductor as tension is applied.
Parallel Jaw Grips: Have jaws that maintain a parallel relationship as they close, distributing the gripping force evenly. Often used for a wide range of bare or insulated cables. Some have smooth jaws for bare conductors to minimize damage, while others have serrated or "V"-grooves for better grip on insulated or high-strength cables.
Chicago Grips (Lever Type Grips): A classic design with a lever arm that, when actuated, closes the jaws onto the conductor. Available with various jaw contours (round, single-V, double-V, serpentine) for different cable types (ACSR, copper, insulated). Many have a locking feature to hold the jaws open for easy placement.
Haven's Grips: A lighter, more compact grip, often used for smaller wires, messenger wire, or guy strand where conductor deformation is less of a concern.
Mesh Grips / Cable Socks:
Description: A woven mesh "sock" (made of galvanized steel wire or high-strength synthetic fiber like Aramid/Kevlar) that slips over the end of the conductor. As tension is applied, the mesh tightens down on the conductor, providing a secure grip.
Applications: Ideal for pulling long lengths of conductor, especially when connecting the pulling rope to the conductor. They distribute the pulling force over a longer section of the conductor, minimizing stress concentrations. Also used for fiber optic cables (OPGW/ADSS) due to their gentle, distributed grip.
Types: Single eye, double eye, open-ended, and multi-cable versions for bundled conductors.
Hot-Line Grips: Designed to be operated remotely using hot sticks for safety when working near energized lines. They often have special latches or designs for this purpose.
Applications:
Connecting the pulling rope to the conductor.
Applying tension during the sagging process to achieve the correct conductor tension and sag.
Holding conductors in place while making splices or attaching permanent hardware.
Temporary support during maintenance or repair.
2. Conductor Clamps (Permanent Hardware)
These are fittings used for the permanent attachment of conductors to towers or poles once stringing and sagging are complete. They are designed to support the conductor for its entire operational life and withstand environmental forces (wind, ice, vibration).
Common Types:
Suspension Clamps:
Purpose: To "hang" or suspend the conductor from an insulator string on a suspension tower. They allow the conductor to swing freely in response to wind or temperature changes, preventing excessive stress at the attachment point.
Design: Typically comprise a clamp body that securely holds the conductor, a keeper, and hardware for connection to the insulator. Often made of galvanized steel or aluminum alloy. For bundled conductors, specialized multi-conductor suspension clamps or yokes are used.
Protection: May include armor rods or vibration dampers (like Stockbridge dampers) to protect the conductor from fatigue at the clamp point.
Dead-End Clamps / Strain Clamps (Tension Clamps):
Purpose: To terminate a conductor at a dead-end tower or at a strain tower where the line changes direction significantly or ends. They are designed to withstand the full tensile load (tension) of the conductor.
Types:
Bolted Type: Heavy-duty clamps that use bolts to compress jaws onto the conductor.
Compression Type: Requires specialized hydraulic compression tools to permanently crimp the clamp onto the conductor. Offers a very strong, low-resistance connection.
Preformed Helical Grips (Preforms): Made of individual helical wires that wrap around the conductor, providing a long, uniform grip. Very popular for dead-ending conductors (especially ACSR) as they distribute stress over a long length, minimizing localized damage.
Wedge Clamps: Simple, reusable clamps that use a wedge mechanism to grip the conductor. Common in distribution lines.
Mid-Span Clamps / Repair Sleeves: Used for making permanent electrical and mechanical connections (splices) between two conductor sections in the middle of a span. They can be compression type or bolted.
Jumper Clamps: Used to connect a jumper loop (flexible conductor) around a suspension insulator string or a dead-end assembly.
Key Considerations for All Grips & Clamps:
Conductor Type & Size: Must match the specific conductor (e.g., ACSR, AAC, AAAC, steel, insulated, OPGW, ADSS) and its diameter (AWG/MCM or mm). Improper matching can lead to damage or slippage.
Rated Load (WLL / MBS): Must be sufficient for the intended application (pulling tension, dead-end tension).
Material Compatibility: For permanent clamps, material must be compatible with the conductor to prevent galvanic corrosion.
Standards: Adherence to relevant industry standards (e.g., IEEE, ASTM, IEC).