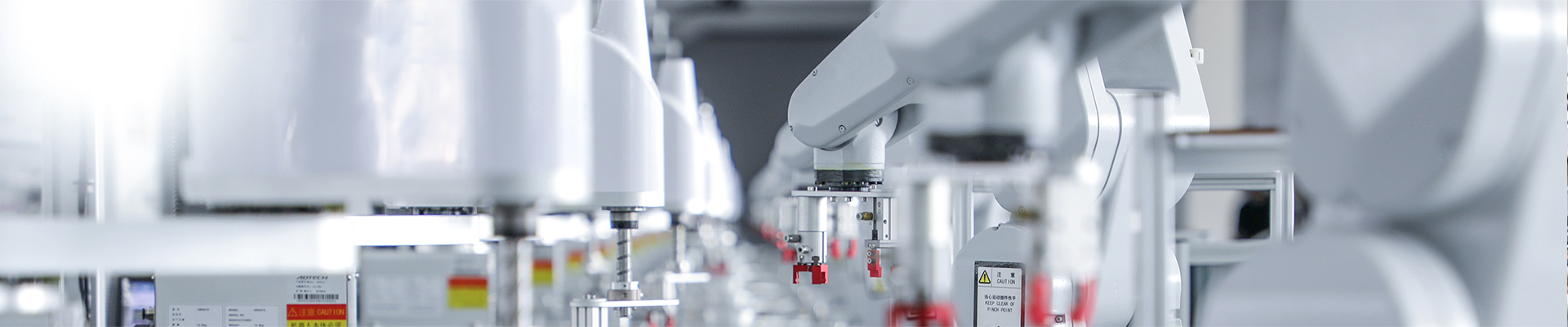
Remote Control & Automated Pullers
Remote control capabilities allow operators to manage the pulling operation from a safe distance, away from the immediate vicinity of the machine and the high-tension ropes/cables. This offers several key benefits:
Enhanced Safety: The primary advantage. Operators can position themselves in a location with optimal visibility of the entire pulling operation, including the conductor's movement, tension points, and potential obstructions, without being exposed to moving machinery or snap-back hazards.
Improved Visibility: Especially useful in challenging terrains or when pulling around bends, where direct line of sight to the machine might be limited.
Increased Efficiency: One operator can often manage the machine more effectively, sometimes even overseeing multiple machines in a synchronized stringing operation.
Reduced Labor: Minimizes the need for personnel directly at the machine's control panel.
Types of Remote Control:
Wired Remote Controls: Simple and robust, providing basic start/stop, speed, and tension adjustments.
Wireless Radio Remote Controls: Offer greater freedom of movement and range, often with more comprehensive control functions and emergency stop buttons.
Automated Pullers
Automated features take precision and efficiency a step further by integrating sensors, real-time data analysis, and programmable logic controllers (PLCs) to manage the pulling process with minimal human intervention.
Precision Tension/Pull Control (Automatic Tensioning Systems - ATS): This is a cornerstone of automation. Operators can pre-set a desired pulling force or tension, and the machine's hydraulic system automatically adjusts speed and power to maintain that constant tension, regardless of varying friction, terrain changes, or conductor weight. This is critical for preventing over-tensioning (which can damage conductors or structures) or under-tensioning (leading to sag issues).
Data Logging and Reporting: Automated pullers often include integrated data loggers that record critical parameters throughout the pull, such as:
Pulling force/tension over time.
Pulling speed.
Distance pulled.
GPS coordinates (on some advanced models).
This data can be downloaded (e.g., via USB) for quality control, project documentation, troubleshooting, and future planning.
Pre-programmable Pull Profiles: For complex pulls, operators can program specific pulling profiles that vary tension and speed at different stages of the pull (e.g., higher tension for initial setup, lower tension during mid-span, specific tension for sag setting).
Automatic Shut-off: The machine can be programmed to automatically stop if pre-set limits (maximum tension, maximum distance, etc.) are exceeded or if certain fault conditions are detected.
Synchronization for Bundled Conductors: For multi-conductor stringing, automated pullers can be electronically synchronized to ensure that each individual conductor in a bundle is pulled at the exact same speed and tension, preventing twisting or uneven loading.
Reduced Human Error: Automation minimizes the impact of operator fatigue or inconsistencies, leading to more reliable and consistent pulls.
Predictive Maintenance: Some advanced systems can monitor their own hydraulic health and performance, providing alerts for potential issues before they lead to breakdowns.
Integration of Remote Control and Automation:
Most high-end pullers for transmission and heavy cable applications now combine both remote control and automation. The remote control acts as the interface for the operator to monitor and command the automated functions, allowing for fine-tuning or emergency overrides from a safe vantage point.