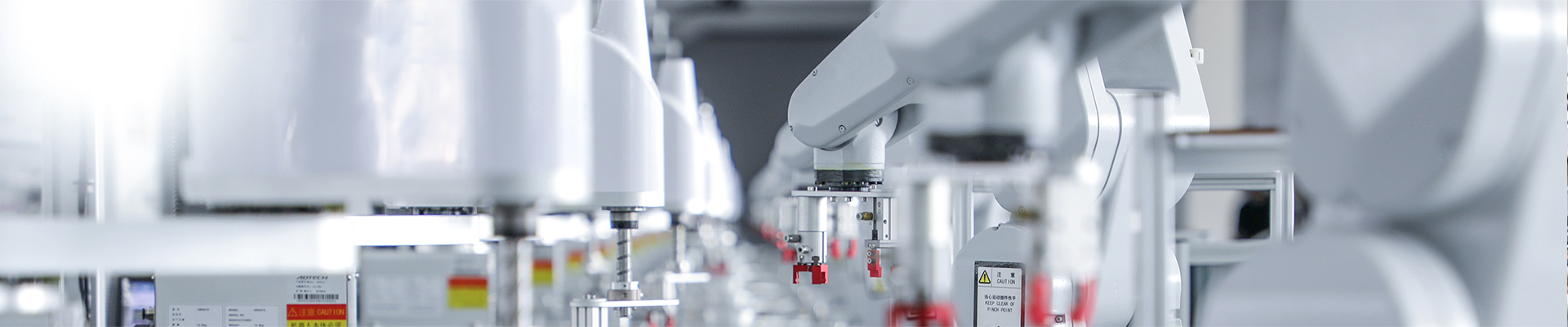
What are the latest technological advancements in "Cable Stringing Equipment" enhancing efficiency and safety?
2025-07-20The "Cable Stringing Equipment" industry is undergoing significant technological advancements, integrating smart features and automation to revolutionize efficiency and safety:
-
Advanced Automation and Control Systems:
-
Constant Tension & Speed Control (Closed-Loop Systems): Modern pullers and tensioners use sophisticated electronic and hydraulic systems to automatically maintain a pre-set constant tension and speed, regardless of terrain changes or friction variations. This prevents over-tensioning (which can damage conductors) and ensures uniform sag.
-
Automated Synchonization: For puller-tensioner setups, automated synchronization ensures both machines work in perfect harmony, maintaining precise tension and speed across the entire span, crucial for complex bundled conductor stringing.
-
-
Real-time Data Acquisition & Telemetry (IoT Integration): Equipment is outfitted with numerous sensors that continuously monitor critical parameters such as pulling force, conductor length, speed, engine diagnostics, and hydraulic pressures. This data is displayed on intuitive digital operator interfaces and transmitted wirelessly via IoT (Internet of Things) to remote monitoring platforms for real-time supervision, analysis, and record-keeping.
-
High-Precision GPS/GNSS Integration: Integrated Global Navigation Satellite Systems (GNSS) with RTK (Real-Time Kinematic) accuracy allow for precise pre-mapping of the stringing route and monitor the exact position and progress of the operation. This is invaluable for accurate "as-built" mapping, ensuring adherence to design specifications, and optimizing logistics.
-
Remote Monitoring & Diagnostics: Operators and project managers can monitor machine performance, track progress, and receive alerts from a central location. This capability allows for proactive maintenance planning, rapid response to operational challenges, and enhanced safety oversight.
-
Predictive Maintenance & AI Analytics: Leveraging real-time and historical operational data, onboard AI and machine learning algorithms can predict potential mechanical failures or maintenance needs (e.g., component wear, fluid degradation). This enables proactive scheduling of maintenance, significantly reducing unplanned downtime, costly emergency repairs, and extending equipment lifespan.
-
Enhanced Safety Features: This includes advanced electronic overload protection with automatic shutdown, multiple emergency stop buttons, robust guarding of moving parts, fail-safe braking systems, and comprehensive alarm systems (audible and visual) to alert personnel to hazardous conditions.
-
Hybrid and Electric Drive Systems: Increasingly, manufacturers are offering hybrid or fully electric stringing equipment, significantly reducing fuel consumption, emissions, and noise pollution, aligning with global sustainability goals.
These advancements collectively lead to significantly higher productivity, reduced operational risks, improved precision in conductor placement, and a safer working environment.