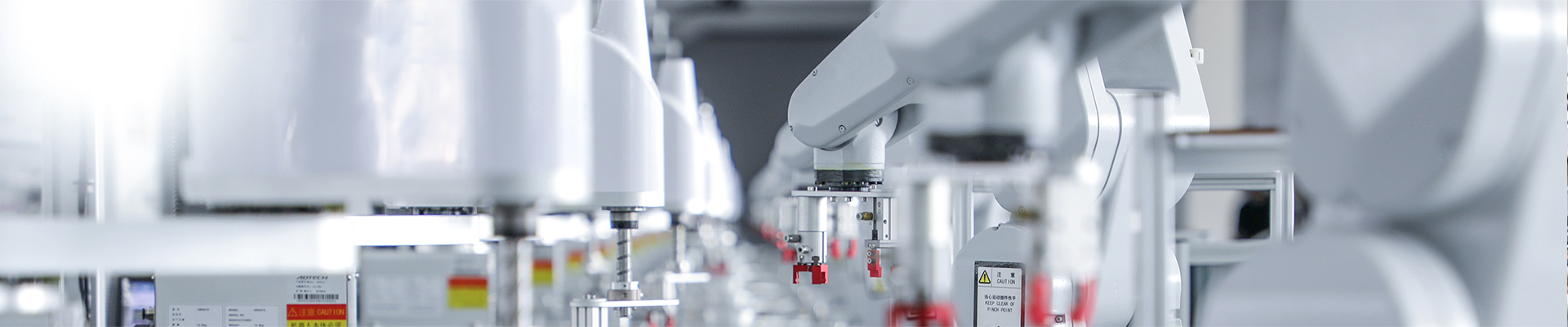
How does temperature (ambient and operational) affect underground cable pulling, and what measures are taken to mitigate thermal-related issues?
2025-07-19Temperature, both ambient during installation and projected operational temperature after energization, significantly impacts underground cable pulling. Managing these thermal factors is crucial for the cable's integrity during the pull and its long-term performance.
I. Impact of Ambient Temperature on Pulling:
-
1. Cable Jacket Rigidity/Softness:
-
Cold Temperatures: At very low ambient temperatures, many cable jacket materials (especially PVC) can become stiff and brittle. This increases the risk of cracking, scuffing, or permanent deformation if the cable is pulled around tight bends or handled improperly.
-
Hot Temperatures: In extremely hot weather, some cable jackets can become softer and tackier. This can increase the coefficient of friction, leading to higher pulling tensions and potential sticking.
-
-
2. Lubricant Viscosity:
-
Cold Temperatures: Lubricants can become more viscous (thicker) in cold weather, reducing their effectiveness in lowering friction.
-
Hot Temperatures: Lubricants can become less viscous (thinner) in hot weather, potentially affecting their ability to maintain a consistent film.
-
-
3. Pulling Tension and Sidewall Pressure: Both extreme cold (due to rigidity) and extreme heat (due to tackiness/softness) can lead to higher-than-predicted pulling tensions and sidewall pressures, increasing the risk of exceeding the cable's Maximum Allowable Pulling Tension (MAPT) or minimum bend radius.
II. Mitigation Measures During Pulling (Ambient Temperature):
-
1. Cable Conditioning: If possible, store cables in a temperature-controlled environment before pulling, especially in extreme cold, to improve flexibility.
-
2. Modified Pulling Speeds: Pulling slower in very cold weather to reduce stress, and potentially slower in very hot weather to prevent excessive heat buildup from friction.
-
3. Lubricant Selection & Application: Choose lubricants designed to perform effectively across the anticipated temperature range. In hot weather, generous and continuous application is even more critical. In cold weather, ensure the lubricant's viscosity doesn't hinder its spread.
-
4. Larger Bend Radii & Sheaves: Using larger diameter rollers and sheaves, especially in cold weather, to ensure the cable is never bent too sharply.
-
5. Scheduling: If feasible, schedule pulls during cooler parts of the day in hot climates, or warmer parts of the day in cold climates.
-
6. Cable Heaters/Coolers (Rare): In extreme cases for very critical or sensitive cables, temporary heating or cooling systems might be employed at the feeder end to maintain optimal cable temperature during the pull.
III. Impact of Operational Temperature (Post-Energization) on Cable Pulling Planning:
While not directly impacting the act of pulling, the projected operational temperature of the cable after it's energized significantly influences decisions made during the planning and installation phases, especially concerning backfill and conduit:
-
1. Thermal Dissipation: Underground power cables generate heat when energized. This heat must dissipate into the surrounding soil to prevent the cable's insulation from overheating and degrading.
-
2. Ampacity Derating: If heat cannot escape efficiently (due to poor thermal resistivity of surrounding soil/backfill or insufficient spacing), the cable's current carrying capacity (ampacity) must be "derated" or reduced, meaning it cannot carry its full design load.
-
3. Lifespan Reduction: Prolonged operation above the cable's rated temperature drastically shortens its lifespan, leading to premature failure.
IV. Mitigation Measures for Operational Temperature (Planning & Installation):
-
1. Thermal Resistivity Studies: Conduct thorough soil thermal resistivity studies along the proposed cable route.
-
2. Engineered Thermal Backfill: For critical power cable installations, our expertise extends to recommending and utilizing engineered thermal backfill materials (e.g., fluid thermal grout, selected granular materials with low resistivity). These are specially blended materials placed directly around the cable in the trench to enhance heat transfer away from the cable.
-
3. Proper Cable Spacing: For multiple cables in a trench, ensuring adequate spacing between them allows each cable to dissipate heat effectively.
-
4. Conduit Selection: While conduits provide mechanical protection, they can also trap heat. Careful thermal analysis dictates appropriate conduit sizing and material, and sometimes direct burial is preferred for thermal reasons if mechanical protection is otherwise sufficient.
-
5. Burial Depth: Ensure sufficient burial depth to utilize the stable ground temperature below the frost line and allow for effective heat dissipation into the surrounding soil mass.
-
6. Temperature Monitoring Systems: For very high voltage or critical underground lines, Distributed Temperature Sensing (DTS) fiber optic cables can be installed alongside the power cable to provide continuous, real-time temperature monitoring, allowing for dynamic load management to prevent overheating.
Our comprehensive approach to underground cable pulling extends beyond just the equipment. We offer solutions and expertise that consider the full thermal lifecycle of the cable, ensuring not only a successful pull but also optimal long-term operational performance and reliability.