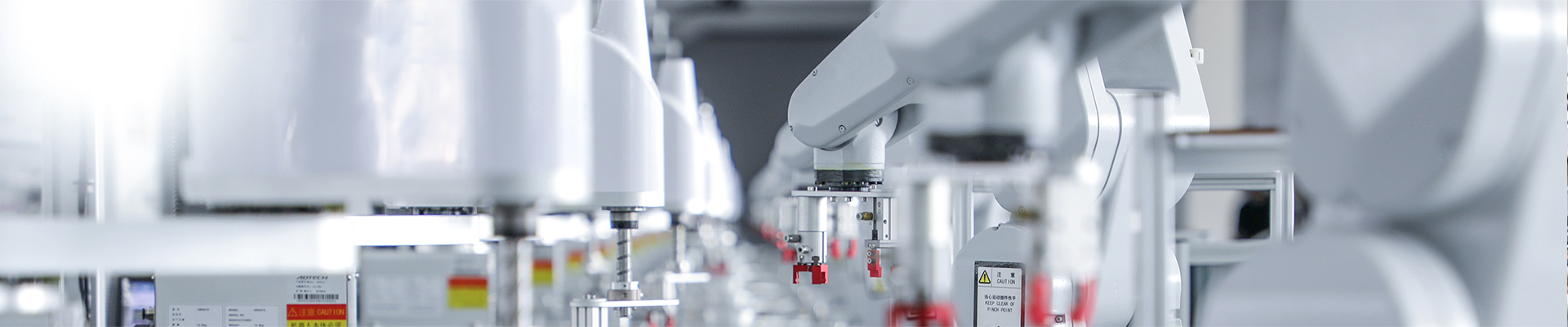
FAQ
While both overhead conductor pulling and underground cable pulling involve moving conductors, the environments and methodologies are fundamentally distinct, requiring specialized equipment and techniques:
Overhead Conductor Pulling (OHTL):
-
Environment: Conductors are pulled in the open air, supported by towers or poles, often over long spans and challenging terrain.
-
Primary Goal: To string conductors to precise sag and tension specifications, ensuring proper clearances and preventing ground contact.
-
Key Equipment:
-
Hydraulic Pullers: Generate the pulling force, typically connected to a pulling rope that is then attached to the conductor.
-
Hydraulic Tensioners: Apply back-tension to the conductor reel, keeping the conductor elevated and under controlled tension throughout the pull.
-
Stringing Blocks (Sheaves): Suspended from towers, these rollers guide the conductor smoothly along the path, minimizing friction and preventing damage.
-
Pulling Grips & Running Boards: Specialized devices to connect the pulling rope to the conductor(s) without damaging them.
-
-
Challenges: Managing sag, avoiding obstacles like trees and existing power lines, navigating difficult terrain, and dealing with weather conditions.
Underground Cable Pulling:
-
Environment: Cables are pulled through pre-installed conduits, ducts, or directly into trenches, often in confined spaces like manholes, vaults, or narrow urban trenches.
-
Primary Goal: To safely install cables without exceeding their maximum pulling tension or bending radius, protecting the cable jacket and insulation from abrasion or damage.
-
Key Equipment:
-
Cable Pullers (Winches): Often compact, designed for high pulling force over shorter distances, adapted for conduit pulling. They may be hydraulic, electric, or even manual.
-
Cable Lubricants: Applied generously to the cable and/or inside the conduit to drastically reduce friction during the pull.
-
Duct Rodders/Fish Tapes: Used to pre-string a pilot line through the conduit or duct.
-
Cable Rollers/Guides: Used in open trenches or manholes to support the cable and guide it into the conduit/trench without dragging on abrasive surfaces.
-
Specialized Pulling Eyes/Grips: Designed to attach securely to the cable, often to its central conductor or strength member, and capable of withstanding significant tension without damaging the outer sheath.
-
-
Challenges: High friction within conduits, navigating tight bends, potential conduit blockages, limited working space in vaults, precise route planning to avoid existing underground utilities, and managing heat generated during long pulls.
Our company provides comprehensive, one-stop solutions for both these critical areas, offering state-of-the-art equipment and tools specifically designed for the unique demands of overhead tension stringing and efficient underground cable laying.
Reconductoring, the process of replacing existing overhead conductors with new ones (often higher capacity HTLS or ACCC), presents unique challenges, especially when maintaining partial or full service. This requires highly specialized techniques and equipment:
-
Live-Line Reconductoring (Maintaining Service): This highly complex and dangerous method requires specialized equipment and rigorously trained personnel to work on or near energized lines.
-
Insulated Equipment: All stringing equipment, tools, and platforms must be highly insulated and rated for the specific voltage of the energized line.
-
Barehand or Hot Stick Techniques: Personnel work from insulated buckets or with insulated tools (hot sticks) to manipulate the conductors while the line remains energized.
-
Conductor Transfer Devices: Specialized clamps, rollers, and temporary supports are used to safely transfer the energized conductors from old insulators to new ones without creating electrical faults.
-
Strict Grounding and Bonding: Meticulous grounding and bonding procedures are followed to ensure equipotential zones and prevent accidental energization or induced voltages.
-
Specialized Tension Stringing: The new conductor is pulled in alongside the old, or the old conductor is simultaneously pulled out as the new one is pulled in, all while maintaining precise tension to prevent contact with energized lines or structures.
-
-
De-energized Reconductoring (Safer, More Common): The line section is de-energized, grounded, and isolated before work begins.
-
Pulling Old and Pulling New Simultaneously: Often, the old conductor acts as the pulling rope for the new conductor. Specialized splicing grips or conductor connectors are used to connect the old conductor to the new one. As the old conductor is pulled out on one side by a tensioner, the new conductor is simultaneously pulled in by a puller on the other side.
-
Conductor Replacement Rollers (CRR): Innovative systems allow the new conductor to be threaded through the existing insulators, or specialized rollers are temporarily attached to the existing line to guide the new conductor, minimizing the need for extensive rigging changes.
-
High-Capacity Pullers & Tensioners: Reconductoring often involves pulling long sections and/or heavy new conductors, requiring robust equipment capable of handling high loads and maintaining precise tension control.
-
-
OPGW Stringing during Reconductoring: When replacing an old ground wire with OPGW, extreme care is taken to protect the optical fibers, necessitating specific OPGW-compatible stringing blocks and precise tension control.
Our comprehensive range of overhead conductor pulling equipment, including high-capacity hydraulic pullers and tensioners, specialized reconductoring tools, and sensitive conductor-friendly accessories, provides the essential solutions for safe, efficient, and reliable reconductoring projects, whether de-energized or, with the necessary safety protocols, in live-line environments.
Selecting the correct pulling lubricant is a critical, yet often overlooked, factor in successful underground cable pulling. It directly impacts pulling tension, cable integrity, and installation efficiency. Key factors to consider include:
-
Cable Jacket Material: Lubricants must be chemically compatible with the cable's outer jacket (e.g., PVC, polyethylene, LLDPE, LSZH - Low Smoke Zero Halogen). Incompatible lubricants can cause swelling, cracking, or degradation of the jacket over time, leading to premature cable failure. Always consult the cable manufacturer's recommendations.
-
Conduit Material: Similarly, the lubricant must be compatible with the conduit material (e.g., PVC, HDPE, steel).
-
Friction Reduction Coefficient: The primary purpose of a lubricant is to reduce friction between the cable and the conduit wall. Look for lubricants with a high coefficient of friction reduction to minimize pulling tension.
-
Temperature Range: The lubricant must maintain its properties and effectiveness across the expected ambient and pulling temperatures. Some lubricants can become too viscous in cold weather or break down in high heat.
-
Residue and Clean-up: Consider whether the lubricant leaves a messy, sticky residue that needs extensive cleanup, or if it dries clean and won't attract dirt or obstruct future cable additions. Water-based, non-toxic, and biodegradable lubricants are often preferred for environmental reasons.
-
Ease of Application: The lubricant should be easy to apply uniformly throughout the conduit run, whether manually, with a pump, or through pre-lubricated conduits.
-
Shear Stability: The lubricant needs to maintain its lubricating properties even under the high shear forces experienced during a long, tight pull.
-
Impact on Operation:
-
Reduced Pulling Tension: The most significant benefit. Lower tension means less strain on the cable, puller, and crew, reducing the risk of cable damage (stretching, jacket abrasion, conductor deformation).
-
Prevention of Cable Damage: Minimizes friction burns, jacket scoring, and insulation damage caused by dragging against rough conduit surfaces or tight bends.
-
Longer Pulls: Enables longer continuous pulls, reducing the need for intermediate pull points (manholes/vaults), which saves time and cost.
-
Improved Efficiency: Smoother pulls mean faster installation times and less effort for the crew.
-
While our company provides the robust cable pulling equipment, we strongly advise our clients on the importance of selecting the correct, high-quality cable lubricant as an integral part of ensuring the success and longevity of their underground cable installations.
Modern underground cable pullers are far more sophisticated than traditional winches, integrating advanced features like automatic tension control and data logging to revolutionize safety, precision, and efficiency:
-
Automatic Tension Control:
-
Purpose: Ensures the cable is pulled at or below its maximum allowable pulling tension, preventing overstressing and potential damage to the cable's conductors, insulation, or jacket.
-
How it Works: Our advanced hydraulic or electric cable pullers are equipped with integrated load cells that continuously monitor the actual pulling force. Operators can pre-set a maximum tension limit. If this limit is approached, the puller's control system automatically reduces speed or even temporarily stops the pull to prevent exceeding the set threshold. This "smart" control minimizes human error and protects valuable cables.
-
-
Real-time Data Logging:
-
Purpose: Provides a comprehensive, verifiable record of the entire pulling operation for quality assurance, compliance, troubleshooting, and future reference.
-
Data Captured: Typically includes:
-
Pulling Tension (Force): Continuous graph and peak tension values.
-
Pulling Speed: Instantaneous and average speed.
-
Distance Pulled: Accurate footage.
-
Time & Date Stamps: For the entire operation.
-
Temperature (sometimes): Ambient and/or cable temperature.
-
-
Benefits:
-
Proof of Quality: Demonstrates that the cable was installed within manufacturer specifications, crucial for warranty and liability.
-
Troubleshooting: Helps diagnose problems during or after a pull (e.g., identifying points of high friction).
-
Optimization: Provides data to analyze and improve future pulling plans and techniques.
-
Compliance: Meets stringent industry standards and client requirements.
-
-
-
User Interface & Connectivity: Modern pullers feature intuitive digital displays for real-time monitoring and data review. Many also offer USB ports, Wi-Fi, or Bluetooth connectivity for easy data download and integration with project management software.
Our range of underground cable laying equipment includes robust cable pullers with these advanced features, providing unparalleled control, reliability, and documentation for your critical infrastructure projects.
Pulling heavy or large-diameter bundled conductors in complex overhead transmission line projects presents amplified challenges that require highly specialized equipment and meticulous execution:
-
Immense Weight & Tension: Bundled conductors (e.g., 4, 6, or even 8 sub-conductors per phase) can be extremely heavy. This translates to enormous pulling forces and back-tensions, demanding:
-
High-Capacity Pullers & Tensioners: Our equipment is designed with the robust power, durable components, and high pulling/tensioning capacities (e.g., 20 tons or more) required to handle these loads safely.
-
Reinforced Structures: Towers and temporary supports must withstand the increased dynamic loads during the pull.
-
-
Maintaining Bundle Geometry: The sub-conductors within a bundle must maintain their precise spacing and orientation to control corona effects, impedance, and wind loading. This requires:
-
Specialized Running Boards: Designed to connect all sub-conductors simultaneously, preventing twisting and ensuring even tension distribution. Integrated, high-capacity swivels are crucial to prevent rotational forces from transmitting to the bundle.
-
Bundle Spacers/Dampers: Installed after pulling, but the stringing process must accommodate their future placement.
-
-
Increased Friction: The greater surface area and weight of bundled conductors increase friction within stringing blocks and at angle structures. This necessitates:
-
Large-Diameter, Multi-Groove Stringing Blocks: With exceptionally smooth, durable, and often non-metallic liners (for sensitive conductors) to minimize friction and protect each sub-conductor individually.
-
Strategic Block Placement: More careful placement to reduce severe bending angles.
-
-
Longer Pull Sections: To maximize efficiency, bundled conductor pulls often span many kilometers, requiring pullers and tensioners with high rope storage capacity and extended operational endurance.
-
Communication & Coordination: With greater distances and multiple crews involved, flawless, real-time communication between the puller operator, tensioner operator, and all intermediate ground crews is absolutely critical for safety and precision.
-
Navigating Obstacles: Pulling multiple, heavy conductors over obstacles like rivers or highways adds layers of complexity, requiring enhanced overhead protection and highly coordinated traffic management.
Our company specializes in providing the heavy-duty, high-precision tension stringing equipment and bespoke accessories specifically engineered to meet the rigorous demands of complex bundled conductor pulling operations, ensuring safety, efficiency, and the long-term integrity of vital transmission lines.
Safety is paramount in all conductor pulling operations, and the industry is continuously adopting new technologies and best practices to minimize risks:
-
Advanced Remote Control Systems: Allowing operators to control pullers and tensioners from a safe distance, away from the immediate hazards of moving machinery, high-tension ropes, and conductors. This significantly reduces "line-of-fire" risks.
-
Automated Overload Protection & Emergency Stops: Our modern pulling equipment is equipped with intelligent systems that automatically detect if pre-set tension or pulling force limits are exceeded, initiating a controlled slowdown or emergency stop. Readily accessible emergency stop buttons are also standard.
-
Real-time Load Monitoring & Alerts: Digital displays and integrated load cells provide continuous, real-time feedback on pulling tension. Operators receive audible and visual alerts if tensions approach dangerous levels, allowing for immediate corrective action.
-
GPS Tracking & GIS Integration: For large projects, GPS tracking of equipment and personnel, integrated with GIS mapping, provides a live overview of the work zone, helping identify potential conflicts and ensure crews are in safe positions.
-
Enhanced Communication Systems: Robust, hands-free two-way radio systems (often integrated into hard hats) ensure continuous and clear communication between all team members, regardless of their location on the stringing path.
-
High-Visibility Equipment & Clothing: Ensuring all equipment, ropes, and personnel are highly visible, especially in low-light conditions or busy work zones.
-
Rigorous Grounding and Bonding Procedures: Meticulous application of equipotential grounding and bonding on all equipment, structures, and conductors, particularly when working near energized lines, to mitigate hazards from induced voltage or accidental energization.
-
Regular Equipment Inspection & Maintenance: A proactive approach to equipment maintenance, including daily pre-operation checks, regular servicing, and timely replacement of worn components, to prevent mechanical failures.
-
Comprehensive Training & Certification: Ensuring all personnel involved in conductor pulling operations are thoroughly trained, certified, and regularly retrained on equipment operation, safety protocols, and emergency procedures.
-
Pre-Job Hazard Analysis (JHA): Conducting detailed Job Hazard Analyses before every pulling operation to identify potential risks, implement control measures, and brief the entire crew.
Our commitment to safety is reflected in the design and capabilities of our conductor pulling equipment. We prioritize features that empower safe practices, contributing to a significantly safer working environment for power line and cable installation professionals worldwide.
Meticulous planning is the bedrock of any successful conductor stringing project, minimizing risks, optimizing efficiency, and ensuring compliance. Key planning stages and critical data points include:
I. Pre-Project Assessment & Feasibility:
-
Route Survey & Mapping: Comprehensive LiDAR, drone, or ground surveys to create accurate 3D terrain models for overhead lines, or precise underground utility maps for cable laying.
-
Geotechnical & Soil Analysis: Especially critical for underground projects to assess soil stability, rock presence, and water table.
-
Environmental Impact Assessment (EIA): Identifying sensitive ecological areas, waterways, and protected zones to plan low-impact stringing methods.
-
Permitting & Right-of-Way (ROW) Acquisition: Securing all necessary permits and easements, addressing any community concerns.
II. Engineering & Design Phase:
-
Conductor/Cable Specifications:
-
Type: ACSR, HTLS, ACCC (overhead); XLPE, EPR (underground).
-
Size & Weight: Diameter, cross-sectional area, weight per unit length.
-
Maximum Allowable Tension (MAT) / Maximum Pulling Tension (MPT): Critical limits that must not be exceeded during stringing.
-
Minimum Bending Radius: Especially crucial for underground cables to prevent damage.
-
-
Sag & Tension Charts (Overhead): Detailed calculations for various temperatures, wind, and ice loading to ensure correct clearances and line performance.
-
Structure Loading Analysis (Overhead): Ensuring towers/poles can withstand stringing loads.
-
Conduit/Duct System Design (Underground): Number, size, and routing of conduits, including bend radii and manhole/vault locations.
-
Jointing and Splicing Requirements: Planning for conductor splices or cable joints, including locations and specialized equipment.
III. Operational Planning & Resource Allocation:
-
Equipment Sizing & Selection: Based on conductor/cable type, length, tension, and site conditions (e.g., pulling/tensioning capacity, stringing block size, reel stand capacity, cable puller size, roller type). Our comprehensive product range allows us to advise on the most suitable equipment.
-
Crew Resourcing & Training: Number of personnel, required certifications (e.g., hot stick, live-line, confined space), and specific training for the chosen equipment and stringing method.
-
Logistics & Material Handling Plan: Transportation of conductors/cables, reels, equipment, and access to job sites.
-
Safety Plan & Emergency Response: Detailed Job Hazard Analysis (JHA), emergency contact information, medical response, and rescue plans.
-
Traffic Management Plan: For both overhead and underground work in populated areas.
-
Communication Plan: Ensuring seamless, real-time communication among all team members and external stakeholders.
By addressing these critical points in the planning phase, projects can anticipate challenges, mitigate risks, and execute conductor stringing operations efficiently and safely.
Minimizing friction and preventing conductor damage is paramount for the longevity and performance of both overhead and underground power lines. Current best practices involve a combination of high-quality equipment, meticulous planning, and skilled execution:
For Overhead Conductor Stringing (Tension Stringing):
-
Properly Sized & Lined Stringing Blocks:
-
Large Sheave Diameter: Ensures the conductor maintains its natural bending radius, reducing localized stress.
-
Non-Metallic Liners: Critical for sensitive conductors (HTLS, ACCC, OPGW). Our blocks feature durable polyurethane or nylon liners to prevent scratching, denting, or crushing of the conductor's surface or sensitive core.
-
Smooth, Sealed Bearings: High-quality, sealed bearings minimize rolling friction and ensure the sheave spins freely, reducing the required pulling force.
-
-
Precision Hydraulic Pullers & Tensioners:
-
Closed-Loop Systems: Provide infinitely variable and consistent tension control, preventing sudden jerks or uncontrolled conductor movement.
-
Real-time Tension Monitoring: Operators can continuously monitor pulling force and back-tension, ensuring limits are not exceeded.
-
-
Specialized Pulling Grips & Running Boards:
-
Even Force Distribution: Grips designed to distribute force uniformly along the conductor to prevent localized stress or crushing.
-
Integrated Swivels: Critical for bundled conductors and OPGW to prevent twisting and transfer of torsional forces.
-
-
Optimized Stringing Path: Planning the route to minimize severe angle structures, as bends significantly increase friction on stringing blocks.
-
Controlled Pulling Speed: Maintaining a smooth, consistent pulling speed to avoid dynamic loading and excessive friction.
For Underground Cable Stringing (Pulling):
-
High-Quality Cable Lubricants:
-
Chemical Compatibility: Crucial to select lubricants chemically compatible with both the cable jacket and conduit material to prevent degradation.
-
High Friction Reduction: Using lubricants specifically designed for electrical cables that drastically reduce pulling tension.
-
Proper Application: Ensuring uniform and sufficient application of lubricant along the entire length of the cable and/or inside the conduit.
-
-
Cable Rollers & Guides:
-
Appropriate Size & Material: Using rollers and guides that support the cable adequately and have smooth, non-abrasive surfaces to prevent dragging or abrasion in manholes, vaults, or open trenches.
-
Radius Control: Ensuring rollers guide the cable around bends without exceeding its minimum bending radius.
-
-
Properly Sized Conduits/Ducts: Selecting conduit sizes that provide sufficient clearance for the cable, minimizing friction.
-
Automated Cable Pullers with Tension Monitoring: Modern pullers with automatic tension control prevent exceeding the cable's maximum allowable pulling tension.
-
Pulling Eyes vs. Grips: Using manufacturer-recommended pulling eyes for direct connection to the cable's strength member whenever possible, or specialized grips designed for minimal jacket damage.
-
Clean Conduits: Ensuring conduits are free from debris, water, or kinks before pulling.
Our company provides a full range of equipment and tools designed to implement these best practices, ensuring the safe, efficient, and damage-free installation of conductors and cables, maximizing their operational lifespan.
Environmental sustainability is increasingly integrated into conductor stringing projects worldwide, driven by stricter regulations, corporate responsibility, and public demand. Emerging trends include:
-
Minimized Right-of-Way (ROW) Disturbance:
-
Tension Stringing: The fundamental practice that keeps conductors elevated, preventing ground disturbance, soil erosion, and damage to vegetation.
-
Compact Line Designs: Using advanced conductors (HTLS, ACCC) that allow for higher capacity on existing or narrower ROWs, reducing the need for new corridors.
-
Vertical Stringing Techniques: Especially in urban or sensitive areas, to minimize lateral ground disturbance.
-
-
Low-Impact Access & Equipment:
-
Drones for Pilot Line Installation: Significantly reduces the need for heavy ground equipment and extensive access roads in remote or fragile environments.
-
All-Terrain, Smaller Footprint Equipment: Utilizing track-mounted or highly maneuverable pullers and tensioners that can navigate challenging terrain with minimal environmental disruption.
-
Temporary Matting & Bridges: Deploying non-permanent solutions over wetlands, sensitive soils, or small waterways to protect the ground and aquatic ecosystems.
-
-
Biodiversity Protection:
-
Pre-Construction Wildlife Surveys: Identifying and protecting endangered species or critical habitats.
-
Seasonal Restrictions: Adhering to specific construction windows to avoid critical wildlife breeding or migration periods.
-
Bird Flight Diverters: Installation of visual markers on conductors to reduce avian collisions.
-
-
Waste Reduction & Recycling:
-
Recycling Old Conductors: Implementing processes for recycling retired conductors and other construction waste.
-
Minimizing Packaging Waste: Working with suppliers to reduce and recycle packaging for equipment and materials.
-
-
Noise & Emissions Control:
-
Quieter Equipment: Preference for pullers and tensioners with lower noise emissions.
-
Alternative Fuels/Electric Equipment: Exploring electric or hybrid-powered stringing equipment to reduce greenhouse gas emissions and noise, especially in urban or sensitive areas.
-
-
Water Resource Protection:
-
Erosion and Sediment Control: Implementing robust measures (silt fences, sediment traps) to prevent soil runoff into water bodies.
-
Spill Prevention Plans: Strict protocols for handling fuels, lubricants, and other chemicals to prevent contamination of soil and water.
-
As a global manufacturer, we are committed to providing conductor stringing equipment that aligns with these evolving environmental standards, enabling our clients to achieve their project goals while demonstrating strong environmental stewardship.
Safety around high-tension conductor stringing operations is non-negotiable, and the industry is continuously adopting new innovations and protocols to protect personnel:
-
Real-time Data Monitoring & Control:
-
Automated Overload Protection: Our hydraulic pullers and tensioners feature systems that automatically slow down or stop if pre-set pulling force or tension limits are exceeded, preventing conductor breakage, equipment damage, and dangerous snap-backs.
-
Digital Displays & Alarms: Operators receive instant, accurate readings of tension, speed, and distance, with audible and visual alerts for any deviations from safe parameters.
-
-
Enhanced Communication Systems:
-
Integrated Two-Way Radios: Hands-free, clear communication systems (often integrated into hard hats) are mandatory for all crew members, ensuring immediate coordination and emergency response, especially over long spans.
-
"All-Stop" Protocols: Clear, universally understood signals and emergency stop buttons on all key equipment (pullers, tensioners, auxiliary devices) that can immediately halt operations.
-
-
Rigorous Grounding and Bonding:
-
Equipotential Grounding: Implementing systems that ensure all conductive parts within the work zone, including equipment, structures, and the conductor being strung, are at the same electrical potential. This is crucial for protecting against induced voltages, especially when working near energized lines.
-
Traveling Grounds: Employing specialized grounding devices that move along with the conductor during stringing, continuously providing a path to ground.
-
-
Remote Control Capabilities: Allowing operators to control pulling and tensioning machines from a safe distance, away from the immediate hazards of moving conductors and high-tension ropes.
-
Specialized Personal Protective Equipment (PPE):
-
Arc-Rated Clothing: Essential for workers near potential arc flash hazards.
-
Insulated Tools & Gloves: For any work near or on energized lines (in live-line reconductoring scenarios).
-
High-Visibility Clothing: To ensure personnel are easily seen in all conditions.
-
-
Comprehensive Training & Certification:
-
Job Hazard Analysis (JHA): Mandatory pre-job briefings for every task to identify specific risks and mitigation strategies.
-
Equipment-Specific Training: Thorough training on the safe operation and maintenance of all stringing equipment.
-
Emergency Response Drills: Regular practice of emergency procedures, including rescue from heights or confined spaces.
-
-
Drone Inspections for Pre-Stringing & Post-Stringing: Used to identify potential hazards or conductor damage without putting personnel at risk.
Our equipment is designed with cutting-edge safety features, and we are committed to supporting our clients with the knowledge and tools necessary to implement the most stringent safety protocols, ensuring the well-being of every professional involved in conductor stringing.
While full automation of conductor stringing with AI is still emerging, AI and machine learning are already beginning to, or are expected to, profoundly influence various aspects of conductor stringing operations, primarily by enhancing planning, monitoring, and safety:
-
Optimized Route Planning & Design:
-
AI-powered GIS Analysis: AI can analyze vast datasets (LiDAR, drone imagery, terrain data, environmental restrictions, population density, existing infrastructure) to suggest optimal stringing routes for both overhead and underground, minimizing environmental impact, construction complexity, and cost.
-
Predictive Modeling for Sag/Tension: AI algorithms can process real-time environmental data (temperature, wind) to predict precise conductor sag and tension variations, allowing for dynamic adjustments during stringing for optimal performance and less rework.
-
-
Enhanced Equipment Monitoring & Predictive Maintenance:
-
Sensor Data Analysis: AI can analyze real-time data from sensors on pulling machines, tensioners, and stringing blocks (e.g., load, speed, temperature, vibration). This allows for predictive maintenance, identifying potential equipment failures before they occur, reducing downtime and costly repairs.
-
Performance Optimization: AI can learn optimal operating parameters for specific conductor types and environmental conditions, suggesting fine-tuning of equipment settings for maximum efficiency and conductor protection.
-
-
Automated Quality Control & Anomaly Detection:
-
Drone-Based Inspection with AI: Drones equipped with high-resolution cameras can capture imagery of the strung conductor. AI image recognition algorithms can then automatically detect subtle defects, damage, or deviations in sag, which might be missed by human inspection.
-
Cable Integrity Monitoring (Underground): AI can analyze data from smart pulling eyes or internal sensors during underground pulls to detect potential cable damage or excessive stress points in real-time.
-
-
Improved Safety & Risk Management:
-
Hazard Identification: AI can analyze drone footage or site data to identify potential safety hazards (e.g., unstable ground, proximity to energized lines, obstacle clashes) and alert crews.
-
Real-time Risk Assessment: AI can combine real-time operational data with weather forecasts and historical incident data to provide dynamic risk assessments to the crew, allowing for proactive safety measures.
-
-
Training & Simulation: AI-powered simulations and virtual reality (VR) training environments can provide highly realistic scenarios for operators and crews to practice complex stringing operations, improving skill and readiness without real-world risks.
While the human element remains central, our company is actively following and integrating these advancements into our equipment design and operational recommendations, ensuring our clients benefit from the cutting edge of stringing technology.
Cable pulling operations, whether overhead or underground, inherently involve significant safety hazards that demand rigorous mitigation strategies and advanced technologies. Key hazards and their solutions include:
I. Common Hazards:
-
High-Tension Release / Snap-back: Sudden release of tension (e.g., rope or cable breakage) can result in severe injuries from whipping lines or flying debris.
-
Entanglement / Pinch Points: Loose clothing, hair, or body parts getting caught in moving machinery (capstans, sheaves, winches) or between the cable and conduit/structure.
-
Electrical Hazards: Contact with energized lines (overhead), induced voltages, or improper grounding/bonding.
-
Falls from Height (Overhead): Working on poles or towers.
-
Confined Space Hazards (Underground): Oxygen deficiency, toxic gases, engulfment in manholes/vaults.
-
Struck-by Hazards: Moving vehicles, falling tools, or uncontrolled cable/conductor movement.
-
Ergonomic Strain: Manual pulling, repetitive motions, or awkward postures leading to musculoskeletal injuries.
II. Mitigation Strategies & Technologies:
-
Pre-Job Hazard Analysis (JHA) & Planning:
-
Detailed Risk Assessments: Identifying all potential hazards specific to the site and task.
-
Emergency Response Plans: Including communication protocols, rescue plans (especially for confined spaces or heights), and first aid.
-
"All-Stop" Protocols: Clear, universally understood signals and readily accessible emergency stop buttons on all key equipment, empowering any crew member to halt operations instantly.
-
-
Advanced Equipment Safety Features:
-
Automated Overload Protection: Our pullers and tensioners incorporate intelligent systems that automatically reduce speed or stop if pre-set pulling tension limits are exceeded, preventing equipment failure and dangerous snap-backs.
-
Remote Control Systems: Allow operators to control machines from a safe distance, away from direct pinch points and high-tension areas.
-
Guarding & Emergency Stops: All moving parts on our machinery are robustly guarded, and emergency stop buttons are strategically placed.
-
-
Rigorous Grounding and Bonding:
-
Equipotential Grounding: Mandatory for all conductive elements in the work zone (equipment, structures, cables) to prevent electrical shock from induced voltages or accidental energization, particularly near existing power lines.
-
Traveling Grounds (Overhead): Devices that continuously ground the conductor as it's being strung.
-
-
Personal Protective Equipment (PPE):
-
Hard Hats, Safety Glasses, Gloves: Standard for all personnel.
-
Arc-Rated Clothing: For workers near potential electrical hazards.
-
Fall Protection: Harnesses, lanyards, and anchor points for all work at height.
-
Respiratory Protection/Gas Monitors (Underground): For confined spaces.
-
-
Enhanced Communication:
-
Two-Way Radios: Clear, reliable communication between all crew members, especially puller/tensioner operators and ground personnel over long distances.
-
Pre-set Hand Signals: For visual communication when radios are not feasible.
-
-
Site Management & Traffic Control:
-
Barricades & Signage: Clearly demarcating work zones to protect both workers and the public.
-
Flaggers & Traffic Plans: Managing vehicle and pedestrian flow safely.
-
Overhead Protection (Overhead): Guard structures or netting when pulling over roads, railways, or energized lines.
-
-
Comprehensive Training: Thorough training and certification for all personnel on equipment operation, safety protocols, rescue procedures, and hazard recognition.
Our commitment to safety is engineered into every piece of equipment we manufacture, providing robust, intuitive, and feature-rich solutions that empower safer cable pulling operations across all environments.
Controlling pulling tension is critical to prevent damage and ensure the longevity of cables and conductors, whether overhead or underground. The primary methods for calculating and controlling this tension are:
I. Calculation of Pulling Tension:
-
Engineering Formulas: For both overhead and underground, theoretical pulling tension is calculated using engineering formulas that account for:
-
Cable/Conductor Weight: The inherent weight of the material.
-
Coefficient of Friction (μ): Between the cable/conductor and its support (stringing blocks for overhead, conduit for underground). This is a critical factor, often determined by material compatibility and the use of lubricants (underground).
-
Length of Pull: Longer pulls accumulate more friction.
-
Number and Severity of Bends: Each bend significantly increases tension due to sidewall pressure.
-
Temperature & Environment: Affects conductor sag (overhead) and lubricant performance (underground).
-
-
Manufacturer Specifications: Cable and conductor manufacturers provide Maximum Allowable Pulling Tension (MAPT) or Maximum Allowable Tension (MAT) specifications. These are absolute limits that must never be exceeded to avoid internal damage to conductors, insulation, or the outer jacket/sheath.
-
Computer Software: Specialized software is often used for complex pulls (especially underground with multiple bends or long runs) to accurately model and predict tension profiles, optimizing pulling points and lubrication strategies.
II. Control of Pulling Tension:
-
Real-time Load Cells & Digital Displays: Our modern pulling equipment (both hydraulic pullers for overhead and powerful winches for underground) are equipped with integrated load cells that provide continuous, real-time feedback on the actual pulling force. This data is displayed digitally, allowing operators to monitor tension instantly.
-
Automatic Tension Control: Advanced pullers feature closed-loop hydraulic or electric systems that allow operators to pre-set a maximum tension limit. If the actual pulling force approaches this limit, the system automatically slows down, or even stops, the pull until the tension is within safe parameters. This prevents overstressing the cable/conductor.
-
Consistent Speed Control: Maintaining a smooth, consistent pulling speed (without jerks or sudden accelerations) minimizes dynamic tension spikes and helps maintain stable friction.
-
Proper Equipment Selection:
-
Overhead: Using correctly sized stringing blocks with smooth, well-lubricated bearings and appropriate liners (non-metallic for sensitive conductors) to minimize friction. Precision hydraulic tensioners apply controlled back-tension.
-
Underground: Utilizing effective cable lubricants, adequate conduit sizing, and appropriate cable rollers/guides in manholes/vaults to reduce friction.
-
-
Strategic Pulling Points: For very long or complex runs, intermediate pulling points may be established to break up the pull into shorter segments, keeping tension below the MAPT.
By combining accurate tension calculation with precise, real-time control mechanisms offered by our advanced pulling equipment, we empower our clients to execute safe, efficient, and damage-free cable and conductor installations, maximizing their lifespan and performance.
Pulling fiber optic cables, whether for overhead ADSS (All-Dielectric Self-Supporting) installations or underground duct runs, presents unique challenges due to their delicate nature. Precision and care are paramount to avoid damaging the optical fibers and compromising signal integrity:
I. Key Challenges:
-
Low Allowable Pulling Tension: Fiber optic cables (especially the delicate glass fibers within) have very low maximum allowable pulling tensions compared to copper conductors. Exceeding this limit, even momentarily, can cause micro-bends, elongation, or breakage of the fibers, leading to signal loss or complete failure.
-
Minimum Bend Radius: Fiber optic cables have a strict minimum bend radius that must not be violated during pulling or installation. Kinking or bending too sharply can cause permanent signal attenuation or fiber breaks.
-
Twisting: Twisting the cable during pulling can induce torsional stress on the fibers, leading to similar damage as exceeding tension limits.
-
Abrasion and Crushing: The outer jacket, while protective, is still vulnerable to abrasion or crushing if dragged over rough surfaces or improperly handled.
-
Long Pulls & Multiple Bends (Underground): Friction accumulates rapidly in long underground pulls with multiple bends, making it difficult to keep tension below the low MAPT for fiber.
II. Best Practices and Specialized Equipment:
-
Precision Tension Control:
-
Automated Cable Pullers: Our advanced cable pullers for underground installations and hydraulic tensioners for overhead ADSS stringing offer precise, automatic tension control, ensuring the pulling force never exceeds the fiber cable's MAPT.
-
In-line Tension Monitors: Essential for real-time verification of pulling tension throughout the entire pull.
-
-
Specialized Pulling Eyes/Grips:
-
Swivel Pulling Eyes: Crucial for fiber optic cables. These allow the pulling rope to rotate independently of the cable, preventing any torsional forces from being transmitted to the delicate fibers.
-
Factory-Attached Pulling Eyes: Often preferred, as they are securely attached to the cable's central strength member (not just the jacket) and tested to safely transfer pulling force.
-
-
Large Radius Stringing Blocks (Overhead) / Cable Rollers (Underground):
-
Overhead: Stringing blocks for ADSS must have very large sheave diameters and smooth, non-metallic liners (polyurethane, nylon) to ensure the cable is gently supported and maintains its minimum bend radius.
-
Underground: Large-radius cable rollers are used in manholes and vaults to guide the cable smoothly around bends without exceeding the minimum bend radius.
-
-
High-Performance Cable Lubricants (Underground): Use only high-quality, non-damaging, and low-friction lubricants specifically designed for fiber optic cables to minimize pulling tension.
-
Cable Pushers/Feeders: These devices are often used at intermediate points in underground runs to "push" the cable, reducing the pulling tension required from the main puller.
-
Duct Integrity: Ensuring conduits/ducts are clean, clear of obstructions, and free from sharp edges or kinks before pulling.
-
Experienced Crews: Proper training and experience are vital, as even minor mishandling can result in significant damage and costly rework.
Our company offers specialized cable pulling equipment, from precision hydraulic tensioners for overhead ADSS to sophisticated underground cable pullers with integrated tension control, along with the necessary accessories like swivel pulling eyes and large-diameter rollers, all engineered to ensure the safe and reliable installation of delicate fiber optic cables.
Environmental concerns and the drive for sustainability are increasingly influencing modern cable pulling techniques and equipment design, pushing the industry towards more eco-friendly and lower-impact operations:
-
Minimizing Ground Disturbance:
-
Tension Stringing (Overhead): By keeping conductors elevated off the ground, tension stringing (a core of our OHTL offering) significantly reduces soil erosion, damage to vegetation, and disturbance to sensitive ecosystems compared to traditional methods.
-
Trenchless Technologies (Underground): For underground cable laying, techniques like Horizontal Directional Drilling (HDD), trenchless plowing, and micro-trenching minimize excavation, reducing soil disturbance, disruption to surface features (roads, landscaping), and the need for extensive backfilling. Our equipment supports integration with these methods.
-
-
Reduced Emissions and Noise:
-
Fuel-Efficient Engines: Our modern hydraulic pullers and tensioners are designed with more efficient engines to reduce fuel consumption and emissions.
-
Electric/Hybrid Equipment: There's a growing trend towards electric or hybrid-powered cable pulling equipment, particularly for urban or noise-sensitive environments, to reduce air pollution and noise levels.
-
Quieter Operations: Equipment design focuses on reducing operational noise.
-
-
Preservation of Biodiversity:
-
Drones for Pilot Line Installation: Drones can carry pilot lines over challenging terrain (dense forests, wetlands) without requiring extensive access roads or ground-level crew intrusion, minimizing habitat fragmentation and disturbance.
-
Targeted Vegetation Management: Using precise techniques for clearing only what's necessary, rather than wide swaths, to maintain ecological integrity.
-
Bird Flight Diverters: Installation of visual markers on overhead lines to reduce bird collisions.
-
-
Waste Reduction and Recycling:
-
Material Selection: Using durable, long-lasting materials in equipment design to extend product lifespan and reduce waste.
-
Recycling Programs: Promoting the recycling of old conductors/cables and other construction waste generated during projects.
-
Minimizing Lubricant Residue (Underground): Using advanced cable lubricants that leave minimal, non-toxic residue in conduits, simplifying future maintenance and reducing environmental impact.
-
-
Water Quality Protection:
-
Erosion and Sediment Control: Implementing robust measures during ground-disturbing activities (underground) to prevent sediment runoff into waterways.
-
Spill Prevention: Strict protocols for handling and storing fuels, lubricants, and other chemicals to prevent soil and water contamination.
-
Our company is committed to integrating sustainable practices into both our manufacturing processes and the design of our cable pulling and stringing equipment, helping our global clients achieve their infrastructure goals responsibly.
Advancements in data logging and monitoring systems are transforming cable pulling operations into highly measurable and verifiable processes, offering significant benefits for project management and quality assurance:
-
Real-time Performance Monitoring:
-
Integrated Sensors: Our modern cable pullers (for both overhead and underground applications) are equipped with a suite of sensors that capture critical data in real time, including pulling tension (force), pulling speed, distance pulled, and sometimes ambient temperature.
-
Digital Displays: Operators and supervisors have immediate access to this data via clear digital displays on the equipment, allowing for instant adjustments to optimize the pull and prevent exceeding safe limits.
-
-
Comprehensive Data Logging:
-
Automatic Recording: All operational data is automatically logged and stored internally on the equipment or on removable media (e.g., USB drives).
-
Time-Stamped Records: Data points are precisely time-stamped, providing a detailed chronology of the entire pulling operation.
-
Graphing Capabilities: Many systems can generate graphs of tension over distance or time, providing a visual representation of the pull's profile.
-
-
Benefits for Project Management:
-
Progress Tracking: Managers can accurately track real-time progress against project schedules and budgets.
-
Resource Optimization: Data helps identify optimal pulling speeds and tension requirements, leading to more efficient use of equipment and personnel.
-
Reduced Rework: By monitoring tension and speed, potential issues can be identified and addressed before they lead to cable damage, preventing costly rework and delays.
-
Performance Benchmarking: Historical data can be used to benchmark performance, identify areas for improvement in future projects, and refine planning.
-
-
Benefits for Quality Assurance (QA):
-
Verifiable Installation Quality: The logged data provides irrefutable proof that the cable/conductor was installed within manufacturer specifications (e.g., maximum allowable pulling tension was not exceeded, minimum bending radius was adhered to if monitored). This is crucial for warranty claims and liability.
-
Troubleshooting: If issues arise after installation (e.g., cable failure), the detailed pulling data can be analyzed to determine if installation practices contributed to the problem.
-
Compliance Documentation: The comprehensive records serve as vital documentation for regulatory compliance and client requirements.
-
Training & Best Practices: Data can highlight successful techniques or areas where training might be needed, fostering continuous improvement in installation practices.
-
Our state-of-the-art cable pulling and stringing equipment incorporates these advanced data logging and monitoring capabilities, empowering our clients with the tools to manage projects with unparalleled precision, assure quality, and enhance overall operational efficiency.
Underground cable laying involves several distinct methods, each chosen based on factors like soil conditions, presence of existing utilities, environmental concerns, project scale, and cost-effectiveness:
-
1. Open Trenching (Cut and Cover):
-
Description: This is the traditional and most common method. A trench is excavated using excavators or trenching machines, the cable (often within conduits) is laid in the trench, and then the trench is backfilled and compacted.
-
Suitability:
-
Rural/Suburban Areas: Where surface disruption is less critical and there's ample space.
-
New Developments: Where the ground is undeveloped and there's no complex existing underground infrastructure.
-
Large Diameter Cables: When conduits or cables are too large for other methods.
-
-
Advantages: Relatively straightforward, good for multiple cables/conduits, easy access for inspection.
-
Disadvantages: Significant surface disruption, slower, higher environmental impact, potential traffic disruption.
-
-
2. Direct Burial (Plowing/Ripping):
-
Description: A specialized vibratory plow or ripper attaches to a tractor, creating a slot in the ground and simultaneously laying the cable (or conduit) into it. No open trench is created.
-
Suitability:
-
Agricultural or Rural Areas: Open fields with minimal existing infrastructure.
-
Long Distances: Very efficient for rapid deployment over long, unobstructed runs.
-
Smaller Diameter Cables: Typically used for communication or distribution cables.
-
-
Advantages: Very fast, minimal surface disruption, highly cost-effective for suitable terrain.
-
Disadvantages: Less protection for cables, not suitable for rocky soil, difficult to add future cables, requires clear rights-of-way.
-
-
3. Horizontal Directional Drilling (HDD):
-
Description: A steerable drilling rig drills a pilot bore along a pre-determined path, then reams the bore to the required diameter, and finally pulls the conduit(s) or cable through the enlarged bore.
-
Suitability:
-
Crossing Obstacles: Ideal for crossing rivers, roads, railways, sensitive environmental areas, or dense urban areas without surface disruption.
-
High-Value Areas: Where open trenching is impractical or prohibited.
-
-
Advantages: Minimal surface disruption, avoids traffic disruption, environmentally friendly, can avoid existing utilities.
-
Disadvantages: More complex, higher initial cost, requires specialized equipment and skilled operators, precise utility mapping is critical.
-
-
4. Micro-trenching:
-
Description: A specialized cutting wheel creates a narrow (1-2 inch) and shallow (8-12 inch) trench in pavements (roads, sidewalks), into which small-diameter cables (typically fiber optic) are laid, and then sealed.
-
Suitability:
-
Urban/Suburban Areas: Highly effective for deploying fiber optic networks in densely populated areas with minimal disruption.
-
Last-Mile Connectivity: Ideal for connecting homes and businesses.
-
-
Advantages: Very fast, extremely minimal surface disruption, lower cost than traditional trenching in urban settings, less traffic impact.
-
Disadvantages: Limited to small diameter cables, shallow depth offers less protection, specific pavement types required, potential long-term pavement issues.
-
Our company provides the robust cable pulling equipment, rollers, and accessories necessary to support all these methods, from heavy-duty winches for large-scale trenching operations to precision tools for the most delicate micro-trenching and HDD projects.
Trenchless cable laying technologies represent a significant leap forward in minimizing surface disruption, making them increasingly popular, especially in urban or environmentally sensitive areas. Key advancements and economic viability factors include:
I. Advancements:
-
Horizontal Directional Drilling (HDD):
-
Improved Steering & Guidance Systems: More precise GPS and magnetic guidance systems allow for highly accurate boring, even over long distances and around existing utilities, reducing the risk of costly strikes.
-
Faster Drill Rigs: More powerful and efficient rigs with enhanced mud mixing and recycling systems, accelerating project timelines.
-
Larger Diameter Capabilities: HDD rigs are now capable of installing larger diameter conduits and multiple conduits in a single pull.
-
Real-time Data Feedback: Operators receive instant data on bore path, torque, and pressure, enabling dynamic adjustments.
-
-
Micro-trenching:
-
Specialized Cutting Wheels: Thinner, more durable cutting wheels can create precise, narrow (1-2 inch) and shallow (8-12 inch) trenches in various pavement types with minimal debris.
-
Integrated Cable Laying: Some micro-trenching machines can simultaneously cut the trench, vacuum out debris, and lay the small-diameter cable or micro-duct, streamlining the process.
-
Advanced Backfill Materials: Developed durable, rapid-curing reinstatement materials that effectively seal the narrow trench, allowing for quick return to service and long-term pavement integrity.
-
-
Plowing (Vibratory Plows):
-
Increased Depth & Force: Modern plows can handle tougher soil conditions and lay cables/conduits at greater depths.
-
GPS-Guided Systems: Enhanced accuracy for straight-line installation.
-
II. Economic Viability:
Trenchless methods, while often having a higher initial equipment or per-meter cost than basic open trenching, become economically viable and often more cost-effective when considering the total project cost and indirect benefits:
-
Reduced Restoration Costs: This is the biggest factor. Avoiding surface disruption means significantly lower costs for road repair, landscaping, and sidewalk replacement. For example, repairing a major roadway after trenching can be extremely expensive.
-
Minimized Traffic Disruption & Lost Productivity: Avoiding road closures and traffic delays saves businesses money and reduces public inconvenience, which can lead to hefty fines or political pressure.
-
Faster Project Completion: In many scenarios, particularly urban fiber deployment, micro-trenching and HDD can be significantly faster than traditional trenching, leading to reduced labor costs and earlier revenue generation (e.g., for telecom providers).
-
Reduced Environmental Impact: Avoiding extensive excavation can lower costs associated with environmental remediation or fines, especially in sensitive areas.
-
Lower Permitting Costs & Easier Approval: Often, permits for trenchless methods are easier to obtain and less costly due to minimal disruption.
-
Safety Improvements: Less exposure of workers to open trenches and traffic can lead to fewer incidents and associated costs.
-
Avoiding Obstacles: The ability to bore under existing utilities, rivers, or roads eliminates the need for expensive detours or complex bridge-like structures.
Our comprehensive range of underground cable laying equipment includes solutions that complement and enhance these trenchless technologies, ensuring our clients can select the most efficient and economically sound method for their specific project challenges.
Laying cables in dense urban environments presents a unique set of complex challenges that demand meticulous planning, advanced technology, and skilled execution:
-
1. Existing Underground Utility Congestion:
-
Challenge: Urban areas are rife with a spaghetti-like network of existing utilities (water, sewer, gas, telecom, other power lines). Damage to these can lead to significant disruptions, safety hazards, and massive financial penalties.
-
Solution: Highly Accurate Utility Mapping & Location: Utilizing advanced ground penetrating radar (GPR), electromagnetic locators, and detailed GIS data is paramount. "Dig Safe" protocols (Call Before You Dig) are non-negotiable. Vacuum Excavation (Hydro-excavation): A non-destructive method for safely exposing existing utilities before traditional excavation.
-
-
2. Limited Space & Access:
-
Challenge: Narrow sidewalks, busy streets, and dense building structures limit working space for equipment and material staging. Manholes and vaults are often cramped.
-
Solution: Compact & Maneuverable Equipment: Utilizing smaller footprint cable pullers, compact trenchers, and specialized tools designed for confined spaces. Careful Logistics Planning: Phased material delivery and efficient site organization.
-
-
3. Traffic and Pedestrian Disruption:
-
Challenge: Cable laying often requires road closures, lane reductions, or sidewalk obstructions, leading to traffic congestion and inconvenience for pedestrians.
-
Solution: Off-Peak Work Hours: Performing work during nights or weekends. Micro-trenching & HDD: These trenchless technologies minimize surface disruption. Robust Traffic Management Plans: Clear signage, flaggers, and coordination with local authorities.
-
-
4. Noise and Environmental Concerns:
-
Challenge: Construction noise can disturb residents and businesses. Dust, emissions, and waste generation are also concerns.
-
Solution: Quieter Equipment: Utilizing modern, quieter machinery or exploring electric/hybrid options. Dust Suppression: Water spraying. Efficient Waste Management: Recycling, proper disposal. Low-Impact Methods: Micro-trenching, HDD.
-
-
5. Pavement Restoration:
-
Challenge: Restoring disturbed roads and sidewalks to their original condition (or better) is critical for public safety and aesthetics. Poor restoration can lead to trip hazards or rapid pavement deterioration.
-
Solution: High-Quality Backfill & Compaction: Ensuring proper materials and techniques are used. Specialized Reinstatement for Micro-trenches: Using durable, compatible materials.
-
-
6. Permitting and Stakeholder Coordination:
-
Challenge: Navigating complex local regulations and obtaining numerous permits can be time-consuming. Coordination with multiple city departments, utility owners, and property owners is essential.
-
Solution: Dedicated Permitting Teams: Specialists to manage the process. Proactive Stakeholder Engagement: Early communication and clear plans.
-
Our extensive range of underground cable laying equipment, coupled with our expertise in diverse installation methods, positions us as a valuable partner in navigating these complex urban cable laying projects, ensuring efficient execution with minimal disruption.
Specialized cable protection systems and carefully selected backfill materials are crucial for safeguarding buried cables against external damage, moisture ingress, and thermal stress, thereby significantly contributing to their longevity and reliability:
-
I. Cable Protection Systems:
-
Conduits/Ducts:
-
Description: PVC, HDPE (High-Density Polyethylene), or concrete conduits encase the cable, providing a primary physical barrier.
-
Benefit: Protects against direct impact, allows for future cable replacement/addition without re-excavation (pulling new cables through existing conduits), and prevents moisture ingress. HDPE is increasingly popular for its flexibility, durability, and long continuous lengths.
-
-
Cable Ties & Spacers:
-
Description: Used within conduits or trenches to maintain proper separation and alignment of multiple cables.
-
Benefit: Prevents cables from rubbing against each other, reduces heat buildup (by allowing airflow), and ensures uniform stress distribution.
-
-
Warning Tapes/Mesh:
-
Description: Brightly colored, detectable tapes or mesh laid above the cable at a specific depth.
-
Benefit: Serves as a visual warning during future excavation, indicating the presence of buried utilities and preventing accidental strikes.
-
-
Duct Seals/End Caps:
-
Description: Used to seal the ends of conduits in manholes, vaults, or at building entries.
-
Benefit: Prevents water, gas, rodents, and debris from entering the conduit, protecting the cable and connected equipment.
-
-
Armored Cables:
-
Description: Cables with an additional layer of steel tape or wire armor under the outer jacket.
-
Benefit: Provides robust protection against crushing, cutting, and rodent damage, especially in direct burial applications or areas with high mechanical stress.
-
-
-
II. Backfill Materials:
-
Thermal Conductivity:
-
Importance: Cables generate heat when energized. The surrounding backfill must efficiently dissipate this heat away from the cable. Poor thermal conductivity leads to overheating, which degrades insulation and reduces cable life.
-
Best Practice: Using "thermal backfill" or "flowable thermal grout" – engineered materials (e.g., sand-cement mixtures, crushed rock fines) with high thermal conductivity that compact well and provide consistent heat dissipation.
-
-
Compaction & Stability:
-
Importance: Proper compaction prevents voids (which can trap moisture or lead to ground settlement) and ensures the cable remains in its designed position. Unstable backfill can allow movement that stresses the cable.
-
Best Practice: Using granular, well-graded materials that compact uniformly, often laid in layers and mechanically compacted. Flowable fills provide excellent compaction around the cable.
-
-
Non-Corrosive Properties:
-
Importance: The backfill material should not be chemically reactive with the cable jacket or other protection systems to prevent long-term degradation.
-
Best Practice: Avoiding highly acidic or alkaline soils, or using neutral backfill materials around the cable zone.
-
-
Absence of Sharp Objects:
-
Importance: The backfill immediately surrounding the cable should be free of rocks, broken glass, or other sharp debris that could puncture or abrade the cable jacket during laying or due to ground movement.
-
Best Practice: Using screened, fine-grained sand or select fill directly around the cable.
-
-
Our company not only manufactures the essential cable pulling and laying equipment but also advises on the best practices for incorporating these vital protection systems and backfill materials, ensuring that your buried cables deliver reliable performance for decades.