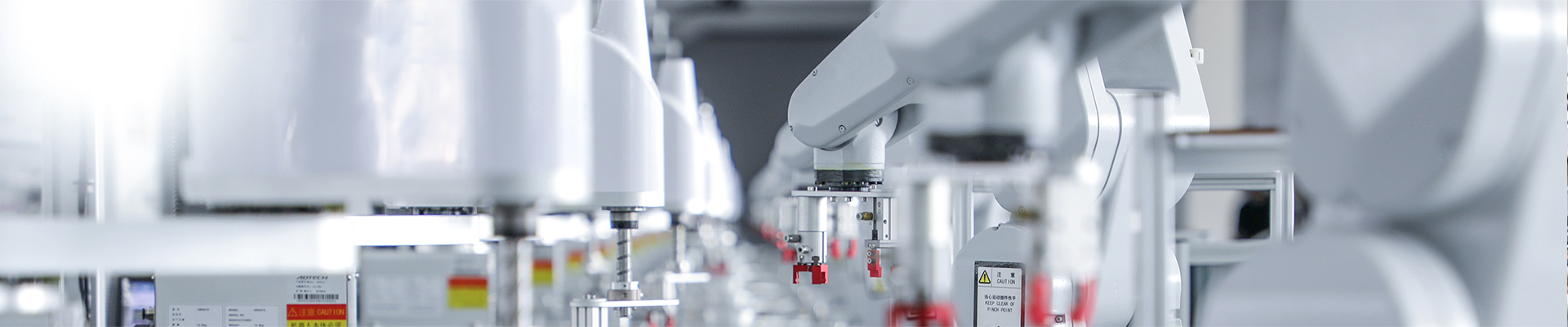
FAQ
Large-scale cable laying projects, whether installing overhead transmission lines or extensive underground cable networks, necessitate thorough environmental impact assessments (EIAs) and robust mitigation strategies to minimize ecological disruption and ensure regulatory compliance.
I. Key Considerations for Environmental Impact Assessments (EIAs):
-
Terrestrial Ecosystems:
-
Habitat Fragmentation: Impact of ROW clearing on forests, wetlands, and animal migration corridors.
-
Vegetation Loss: Removal of trees and plants.
-
Soil Disturbance: Erosion, compaction, and alteration of soil structure, especially during trenching.
-
Species Protection: Presence of endangered or protected flora and fauna, requiring specific avoidance measures or relocation plans.
-
-
Aquatic Ecosystems:
-
Water Quality: Sedimentation, runoff from disturbed areas, potential spills of lubricants or fuels impacting rivers, lakes, and wetlands.
-
Aquatic Habitat Disruption: Impact on fish spawning grounds or aquatic plant life during water crossings (rivers, coastal areas).
-
-
Noise and Air Quality:
-
Construction Noise: Impact on wildlife and nearby communities from heavy machinery.
-
Air Emissions: From diesel engines and dust generated during excavation.
-
-
Cultural and Historical Resources:
-
Archaeological Sites: Potential disturbance of undiscovered historical artifacts.
-
Sacred Sites: Impact on areas of cultural significance.
-
-
Visual Impact (Overhead): Aesthetic impact of new transmission towers on landscapes.
-
Waste Management: Proper disposal of excavated spoil, construction debris, and hazardous materials.
II. Mitigation Strategies:
-
A. Route Optimization and Siting:
-
Avoidance: Prioritizing routes that bypass sensitive ecosystems, critical habitats, historical sites, and dense population centers.
-
Co-location: Utilizing existing utility corridors or road easements to minimize new disturbances.
-
Micro-siting: Fine-tuning tower/pole locations (overhead) or trench paths (underground) to avoid specific sensitive features.
-
-
B. Low-Impact Construction Methods:
-
Tension Stringing (Overhead): Our core method for overhead lines keeps conductors elevated, preventing ground disturbance and damage to underlying vegetation and soil, thus minimizing environmental impact compared to older methods.
-
Trenchless Technologies (Underground): Employing HDD for water/road crossings, or micro-trenching in urban areas to minimize surface excavation, soil disruption, and habitat fragmentation.
-
Temporary Matting/Bridges: Protecting sensitive wetlands, stream banks, or agricultural fields from heavy equipment.
-
Drones for Pilot Line Installation: Significantly reduces the need for ground clearing and access in remote or difficult terrain.
-
-
C. Erosion and Sediment Control:
-
Best Management Practices (BMPs): Implementing silt fences, sediment basins, erosion control blankets, and timely revegetation to prevent soil runoff into water bodies.
-
-
D. Waste and Spill Management:
-
Reduced Waste: Optimizing material usage, recycling old cables/conductors and packaging.
-
Biodegradable Lubricants: Using environmentally friendly cable lubricants for underground pulls.
-
Spill Prevention Plans: Strict protocols for handling, storing, and disposing of fuels, oils, and other chemicals to prevent contamination.
-
-
E. Wildlife Protection:
-
Pre-construction Surveys: Identifying and locating wildlife and their habitats.
-
Seasonal Restrictions: Scheduling work to avoid critical breeding or nesting periods.
-
Bird Flight Diverters (Overhead): Installation of visual markers to reduce avian collisions with conductors.
-
-
F. Restoration and Monitoring:
-
Prompt Reclamation: Rapidly restoring disturbed areas to their natural state or an equivalent functional condition, including native species planting.
-
Post-Construction Monitoring: Ongoing monitoring to ensure the effectiveness of mitigation measures and address any unforeseen impacts.
-
Our company is dedicated to supporting responsible infrastructure development. We provide advanced cable laying and tension stringing equipment designed to enable these mitigation strategies, helping our global clients meet stringent environmental regulations and achieve their sustainability goals.
Regardless of whether it's a high-voltage power cable or a delicate fiber optic line, every successful cable installation project follows a series of fundamental, interconnected steps, ensuring efficiency, safety, and long-term reliability:
-
1. Project Planning & Site Survey:
-
Detailed Assessment: This initial stage involves thoroughly evaluating the project's scope, requirements, and site conditions. For overhead lines, this includes terrain, existing infrastructure, and environmental factors. For underground cables, it's about soil analysis, existing utility mapping, and potential obstacles.
-
Route Selection: Determining the optimal path for the cable run, considering factors like length, accessibility, environmental impact, and avoiding known hazards or future development areas.
-
Permitting & Right-of-Way (ROW) Acquisition: Securing all necessary legal permissions and easements from landowners and authorities.
-
Equipment & Material Specification: Identifying the precise cable type, size, and quantity, along with all necessary installation equipment (pullers, tensioners, stringing blocks, rollers, conduits, splicing tools) from our comprehensive range.
-
-
2. Design & Engineering:
-
Load Calculations: For overhead, this involves sag-tension calculations, structure loading analysis, and clearance requirements. For underground, it's about maximum pulling tension calculations, thermal resistivity of backfill, and conduit sizing.
-
Detailed Drawings: Creating precise plans, profiles, and schematics for the entire installation, including splice points, manhole/vault locations, and grounding details.
-
-
3. Site Preparation:
-
Clearing & Grading: Preparing the installation corridor, including vegetation removal (for overhead) or trench excavation/duct path preparation (for underground).
-
Traffic Management: Implementing plans to ensure public and worker safety around the work zone, especially in urban areas.
-
Utility Locating: For underground projects, meticulous identification and marking of all existing utilities to prevent accidental strikes.
-
-
4. Cable/Conductor Installation (Pulling/Stringing):
-
Equipment Setup: Deploying and calibrating specialized equipment such as hydraulic pullers, tensioners, cable winches, reel stands, and stringing blocks.
-
Controlled Pulling/Stringing: Using precise tension and speed control to lay the cable without exceeding its maximum allowable pulling tension (MAPT) or minimum bend radius. Our equipment ensures this critical step is performed with utmost precision.
-
Lubrication: For underground pulls, applying appropriate lubricants to minimize friction and reduce pulling forces.
-
-
5. Jointing, Splicing & Termination:
-
Precision Work: Connecting cable sections (splices) or connecting the cable to equipment (terminations) using specialized tools and highly trained technicians. This is a critical point for long-term reliability.
-
Environmental Protection: Ensuring joints and terminations are properly sealed and protected from moisture and environmental degradation.
-
-
6. Testing & Commissioning:
-
Post-Installation Testing: Performing comprehensive electrical and/or optical tests (e.g., insulation resistance, continuity, OTDR for fiber) to verify the integrity and performance of the installed cable.
-
Documentation: Compiling all "as-built" drawings, test reports, and operational data for future reference and maintenance.
-
Energization/Activation: Bringing the cable into service after successful testing.
-
-
7. Restoration & Clean-up:
-
Site Remediation: Restoring the disturbed areas to their original condition, including backfilling, compaction, and landscaping.
-
Waste Disposal: Proper management and disposal of all construction waste.
-
Our company provides the complete suite of high-quality tools and equipment, from the initial planning stages through final testing, supporting every step of this critical process for both overhead and underground cable installations worldwide.
Trenchless technologies have revolutionized underground cable laying by minimizing surface disruption, and recent advancements continue to enhance their efficiency, precision, and cost-effectiveness.
I. Advancements in Horizontal Directional Drilling (HDD):
-
1. Enhanced Steering & Guidance Systems:
-
Advancement: More sophisticated real-time tracking (magnetic, wireline, GPS-assisted) allows for incredibly precise bore paths, even over long distances and around existing underground utilities. This significantly reduces the risk of costly utility strikes.
-
Impact: Higher accuracy leads to fewer re-drills, faster completion, and reduced damage claims, improving overall project efficiency and lowering indirect costs.
-
-
2. More Powerful & Compact Rigs:
-
Advancement: Modern HDD rigs offer increased thrust and pullback capabilities in smaller footprints, enabling them to tackle harder ground conditions and larger conduit diameters, even in confined urban spaces.
-
Impact: Expands the applicability of HDD to more challenging sites, making it viable for projects that previously required extensive open trenching. Increased power also means faster drilling.
-
-
3. Improved Drilling Fluids & Solids Control:
-
Advancement: Development of more environmentally friendly and efficient drilling muds, coupled with advanced recycling and separation systems.
-
Impact: Reduces water consumption, minimizes waste disposal volumes, and lowers the environmental footprint and associated costs.
-
II. Advancements in Micro-trenching:
-
1. Narrower & More Precise Cuts:
-
Advancement: Specialized cutting wheels can now create extremely narrow (as little as 0.5-1 inch wide) and shallow trenches (typically 8-16 inches deep) in various pavement types.
-
Impact: Minimal surface disturbance, greatly reduced excavation spoil, faster installation, and lower restoration costs. Ideal for "fiber to the home" (FTTH) deployments in urban/suburban areas.
-
-
2. Integrated Installation & Backfill:
-
Advancement: Some micro-trenching machines can simultaneously cut the trench, vacuum out debris, lay the small-diameter cable or micro-duct, and apply rapid-curing backfill material.
-
Impact: Streamlines the entire process, drastically reducing project timelines and labor costs.
-
-
3. Durable Reinstatement Materials:
-
Advancement: Development of specialized, fast-setting, and highly durable polymer-modified grouts or cold asphalt mixes for sealing the micro-trench.
-
Impact: Ensures long-term pavement integrity and minimizes future maintenance, allowing for quick return to service for roads and sidewalks.
-
III. Overall Impact on Efficiency and Cost:
-
Reduced Restoration Costs: This is often the largest cost-saving for trenchless methods. Avoiding extensive surface disruption means significantly lower expenses for road/sidewalk repair, landscaping, and traffic management.
-
Faster Project Completion: Trenchless methods, particularly micro-trenching, can be dramatically faster than traditional trenching, leading to reduced labor costs and earlier service activation.
-
Minimized Traffic/Public Disruption: Less disruption to daily life and commerce, which can translate into significant indirect savings (e.g., avoiding fines, maintaining public goodwill).
-
Lower Environmental Impact: Reduced soil disturbance, less waste, and fewer emissions contribute to lower environmental compliance costs and enhanced corporate social responsibility.
-
Increased Safety: Less open excavation reduces worker exposure to hazards like trench collapse and traffic.
Our comprehensive range of underground cable laying equipment includes the latest in HDD and micro-trenching support tools, alongside powerful cable pullers and winches, ensuring our clients can capitalize on these advancements for efficient, cost-effective, and minimally disruptive installations.
Ensuring optimal cable protection is paramount for maximizing the lifespan and reliability of any installed cable or conductor. Our approach integrates robust equipment, meticulous procedures, and quality materials for both overhead and underground systems:
I. During Installation:
-
A. For Overhead Transmission Line (OHTL) Tension Stringing:
-
Precision Hydraulic Pullers & Tensioners: Our equipment features automated tension control systems that maintain constant tension and speed, preventing sudden jerks or overstressing the conductor. This is crucial to avoid stretching, nicks, or breaks in the delicate strands.
-
Properly Sized Stringing Blocks: Utilizing blocks with large sheave diameters ensures the conductor maintains its natural bend radius. Blocks with non-metallic, high-resistance liners (e.g., polyurethane, nylon) prevent scratching, denting, or crushing of sensitive conductors like ACCC or OPGW.
-
Integrated Swivels & Running Boards: These accessories prevent twisting of the conductor (especially for bundled conductors) and ensure uniform load distribution, minimizing stress on the outer strands.
-
Controlled Sag & Tension: Adhering to engineered sag-tension charts to ensure proper line performance and minimize dynamic loads during stringing.
-
-
B. For Underground Cable Laying:
-
Automated Cable Pullers with Real-time Monitoring: Our pullers provide precise tension and speed control, preventing the cable's Maximum Allowable Pulling Tension (MAPT) from being exceeded, which could damage insulation or conductors.
-
High-Performance Cable Lubricants: Using chemically compatible, low-friction lubricants specifically designed for electrical cables. Proper and sufficient application significantly reduces pulling force and minimizes jacket abrasion.
-
Appropriate Cable Rollers & Guides: Deploying robust rollers with smooth, non-abrasive surfaces in manholes, vaults, and trenches to support the cable and guide it around bends without exceeding its minimum bending radius.
-
Clean & Properly Sized Conduits: Ensuring conduits are free of debris, sharp edges, or kinks before pulling to prevent abrasion or snags. Selecting conduits with adequate internal diameter.
-
Specialized Pulling Eyes: Using manufacturer-approved pulling eyes that attach to the cable's strength member, distributing tension evenly.
-
II. After Installation (Long-term Protection):
-
A. For Overhead Transmission Lines:
-
Proper Sag & Tension: Correct sag prevents excessive mechanical stress, especially under extreme weather conditions (wind, ice), and ensures adequate ground clearance.
-
Vibration Dampers & Spacers: Installing devices like Stockbridge dampers or spacer-dampers to mitigate Aeolian vibration or galloping, which can cause conductor fatigue and damage.
-
Bird Flight Diverters: Visual markers to prevent avian collisions.
-
Regular Inspections: Visual and drone-based inspections to identify any wear, corrosion, or external damage.
-
-
B. For Underground Cables:
-
Robust Conduits/Duct Banks: Encasing cables in durable PVC, HDPE, or concrete conduits provides a primary physical barrier against mechanical damage from excavation, rodents, or ground movement.
-
Proper Backfill Materials: Utilizing thermally stable and well-compacted backfill (often engineered thermal backfill) to ensure efficient heat dissipation away from the cable, preventing overheating and insulation degradation. This is crucial for long-term ampacity and lifespan.
-
Warning Tapes & Markers: Burying detectable warning tapes or mesh above the cable indicates its presence to future excavators, significantly reducing accidental strikes ("dig-ins").
-
Duct Seals & End Caps: Sealing conduit ends in manholes/vaults prevents moisture, gases, and pests from entering and damaging the cable.
-
Controlled Burial Depth: Ensuring cables are buried at the industry-standard depth to protect them from surface loads and frost heaving.
-
Our "one-stop supply" philosophy means we offer not just the cutting-edge installation equipment, but also provide guidance on best practices and accessories crucial for maximizing cable protection and ensuring the lasting performance of your electrical infrastructure.
Sustainability and environmental responsibility are becoming core tenets of global cable installation projects, driven by regulatory demands, corporate responsibility, and a growing awareness of ecological impact. The latest practices include:
-
1. Reduced Environmental Footprint through Technology:
-
Tension Stringing (Overhead): A fundamental practice we champion, keeping conductors elevated off the ground prevents soil erosion, minimizes damage to vegetation, and reduces the need for extensive ground clearing, especially in sensitive habitats.
-
Trenchless Technologies (Underground):
-
Horizontal Directional Drilling (HDD): Installing cables under rivers, roads, railways, and environmentally sensitive areas (wetlands, forests) without surface disruption, preserving ecosystems and reducing restoration costs.
-
Micro-trenching: Creating narrow, shallow cuts in urban pavements for fiber optic cables, significantly reducing excavation volume, soil spoil, and traffic impact.
-
Vibratory Plowing: For direct burial in open terrain, plowing creates minimal disturbance compared to traditional trenching, quickly restoring the landscape.
-
-
Drones for Pilot Line Installation & Inspection: Minimizing the need for ground vehicles and personnel in remote or challenging terrain, reducing disturbance and enhancing safety. Drones also reduce the environmental impact of traditional survey methods.
-
-
2. Eco-Friendly Materials and Lubricants:
-
Biodegradable Cable Lubricants: Utilizing lubricants for underground pulls that are non-toxic and biodegrade, minimizing soil and water contamination.
-
Halogen-Free & Low-Smoke Cables: Increasingly specified for indoor applications, these cables emit fewer toxic fumes and less smoke in case of fire, enhancing safety and reducing environmental pollution.
-
Recycled/Sustainable Materials in Equipment: Manufacturing equipment with a focus on using recyclable components and reducing material waste in our own production processes.
-
-
3. Emission and Noise Reduction:
-
Fuel-Efficient Equipment: Our modern pullers, tensioners, and other machinery are designed with optimized engines to reduce fuel consumption and greenhouse gas emissions.
-
Electric or Hybrid Equipment: Growing adoption of electric or hybrid-powered cable installation equipment, particularly for urban or noise-sensitive areas, to reduce noise pollution and localized emissions.
-
-
4. Responsible Waste Management:
-
Recycling Programs: Implementing processes for recycling retired conductors/cables (copper, aluminum) and other construction waste materials.
-
Minimized Packaging: Working with suppliers to reduce and recycle packaging for equipment and materials.
-
Proper Spoil Disposal: Managing excavated soil and rock responsibly, often repurposing it for other projects or ensuring it is disposed of in an environmentally sound manner.
-
-
5. Biodiversity Protection & Mitigation:
-
Pre-Construction Surveys: Conducting thorough ecological surveys to identify and protect endangered species, critical habitats, and breeding grounds.
-
Seasonal Restrictions: Scheduling work to avoid sensitive periods for wildlife (e.g., nesting seasons).
-
Habitat Restoration: Prompt and effective restoration of disturbed areas using native vegetation to promote ecological recovery.
-
Bird Flight Diverters (Overhead): Installation of visible markers on conductors to reduce avian collisions.
-
Our commitment to sustainability is woven into our product design and our recommendations for installation practices, helping our clients not only meet regulatory requirements but also contribute positively to global environmental stewardship.
The future of cable installation is inextricably linked with the evolution of smart grids and the accelerating integration of renewable energy sources. Several exciting trends are shaping technologies and practices:
-
1. Ultra-High-Voltage (UHV) and HVDC Cable Systems:
-
Trend: The increasing need to transmit massive amounts of power over long distances from remote renewable energy hubs (e.g., offshore wind farms, large solar arrays) to consumption centers. HVDC (High Voltage Direct Current) is increasingly preferred for its lower losses over long distances and ability to integrate asynchronous grids.
-
Installation Impact: Requires more robust, larger, and heavier cables. Demands even greater precision in tension control, specialized handling equipment, and advanced thermal management during installation and operation.
-
-
2. Submarine Cable Expansion:
-
Trend: The proliferation of offshore wind farms necessitates vast networks of inter-array and export cables. Also, the increasing demand for global data connectivity continues to drive new transoceanic fiber optic cable installations.
-
Installation Impact: Development of highly specialized cable laying vessels (CLVs) with dynamic positioning, advanced ROVs (Remotely Operated Vehicles) for precise seabed trenching and burial, and sophisticated cable handling systems capable of managing immense cable weights and lengths in challenging marine environments.
-
-
3. Integrated Smart Grid Functionality:
-
Trend: Cables are no longer just passive conduits. They are becoming integral components of smart grids, requiring real-time monitoring and communication capabilities.
-
Installation Impact: Increasing integration of fiber optic cables within power cables (e.g., OPGW for overhead, or fiber in the core of underground power cables) for real-time sensing of temperature, strain, and fault location. This requires precision handling to protect the embedded fiber during installation.
-
-
4. Robotics and Automation:
-
Trend: Automation of repetitive or hazardous tasks to improve safety, efficiency, and consistency.
-
Installation Impact: Development of autonomous trenching and plowing machines, robotic inspection systems (drones, ROVs), and semi-automated cable handling on job sites. This reduces human exposure to risk and accelerates installation times.
-
-
5. Digital Twins and Predictive Analytics:
-
Trend: Creation of virtual replicas of entire cable infrastructure, enabling advanced simulations and data-driven decision-making.
-
Installation Impact: During planning, digital twins optimize routes, predict pulling tensions, and simulate thermal performance. During installation, real-time data from our smart equipment feeds the twin, allowing for immediate adjustments and "as-built" documentation. Post-installation, predictive analytics forecast maintenance needs and extend asset lifespan.
-
-
6. Advanced Materials and Cable Design:
-
Trend: Innovation in insulation (e.g., XLPE for higher temperatures, new polymeric materials for HVDC), conductor materials (e.g., HTLS, ACCC for increased capacity on existing towers), and lighter, more durable protective jacketing.
-
Installation Impact: Requires specialized stringing and pulling equipment designed to handle the unique mechanical properties and sensitivities of these advanced cables.
-
-
7. Focus on Resilience and Hardening:
-
Trend: Increasing demand for infrastructure that can withstand extreme weather events and natural disasters.
-
Installation Impact: Greater emphasis on undergrounding cables where feasible, and using highly robust, protected overhead conductors (like Aerial Bundled Cables - ABC) in vulnerable areas. Installation methods will prioritize minimizing environmental vulnerabilities.
-
As a leading manufacturer and exporter, our company is at the forefront of these trends, continuously innovating our cable installation tools and equipment to support the complex and evolving demands of global power and communication infrastructure, ensuring a reliable and sustainable future.
Selecting the most appropriate underground cable laying method is a complex decision, driven by a combination of technical, environmental, economic, and logistical factors unique to each project. Critical factors include:
-
1. Soil and Geological Conditions:
-
Soft/Cohesive Soils: Direct burial (plowing) or traditional open trenching are often efficient and cost-effective.
-
Rocky Terrain/Hard Ground: Requires specialized equipment like rock trenchers or horizontal directional drilling (HDD). This significantly impacts cost and complexity.
-
High Water Table/Wetlands: Dictates the need for methods that minimize dewatering, such as HDD, or requires specific trenching and backfill techniques to manage water.
-
Thermal Resistivity: For power cables, the soil's ability to dissipate heat is crucial. Low thermal resistivity often allows for direct burial, while high resistivity may necessitate specialized thermal backfills or even conduits.
-
-
2. Existing Underground Infrastructure and Congestion:
-
Urban vs. Rural: Densely populated urban areas have a complex "spaghetti" of existing utilities (water, gas, sewer, other power, telecom). This strongly favors trenchless methods like HDD or micro-trenching to avoid costly and dangerous strikes. Rural areas with fewer obstructions may allow for more traditional trenching.
-
Accurate Mapping: The availability and reliability of existing utility maps (and the willingness to use GPR or vacuum excavation) is a major determinant.
-
-
3. Environmental and Regulatory Sensitivities:
-
Protected Areas: National parks, wildlife habitats, or environmentally sensitive wetlands often prohibit open excavation, making HDD the only viable option.
-
Water Bodies/Roads/Railways: Crossing these features almost always necessitates trenchless methods to avoid disruption and ecological damage.
-
Noise and Emissions: Local regulations may dictate the use of quieter, lower-emission equipment, which can influence method choice.
-
Restoration Requirements: The speed and quality of surface restoration needed after the project.
-
-
4. Cable Type and Size:
-
Small Diameter (Fiber Optic): Micro-trenching or blowing into existing ducts are highly efficient.
-
Medium/Large Power Cables: Open trenching (with or without conduits) or HDD are common. Very large cables may require multiple conduits or dedicated duct banks.
-
Delicacy: Fiber optic cables' strict bend radius and low pulling tension limits heavily influence the choice of pulling equipment and guides.
-
-
5. Project Length and Scale:
-
Short Runs: Open trenching or manual methods might be sufficient.
-
Long Runs: Plowing (for direct burial) or HDD become highly efficient due to speed.
-
Multiple Cables: Duct banks within trenches can consolidate multiple cables.
-
-
6. Cost and Schedule:
-
Initial Cost: Trenchless methods often have higher per-meter initial costs for equipment/specialists, but can be cheaper overall due to reduced restoration, traffic management, and project speed.
-
Maintenance & Future Access: Using conduits (often with traditional trenching or HDD) allows for easier future cable replacement or upgrades without re-excavation, reducing future costs.
-
Fault Location & Repair: Direct burial can make fault location and repair more challenging and costly.
-
Our company offers a comprehensive suite of underground cable laying equipment designed to support all these methods, from heavy-duty trenchers and plows to precision HDD support tools and advanced cable pullers, enabling our clients to select and execute the optimal solution for any project condition.
Laying underground cables in rocky terrains or areas with high water tables presents significant engineering and logistical challenges that require specialized equipment and refined techniques to ensure project success and long-term cable integrity.
I. Challenges in Rocky Terrain:
-
Difficulty in Excavation: Traditional trenching is slow, costly, and can damage equipment. Rock is often too hard for standard trenchers.
-
Cable Protection: Sharp rock fragments can damage cable jackets and insulation, both during installation and over time due to ground movement.
-
Backfill Quality: Achieving proper compaction and thermal performance with rocky spoil is difficult, leading to voids or hot spots.
-
Equipment Wear & Tear: High abrasion and impact stress on digging teeth, chains, and hydraulic components.
II. Specialized Equipment and Techniques for Rocky Terrain:
-
Rock Trenchers: Our specialized rock trenchers are equipped with heavy-duty cutting chains or wheels armed with carbide-tipped teeth. These powerful machines are designed to cut through solid rock, asphalt, and concrete.
-
Horizontal Directional Drilling (HDD): Often the preferred method for crossing solid rock formations or when surface disturbance is unacceptable. HDD rigs drill a bore under the rock, through which conduits are pulled, completely avoiding excavation.
-
Blasting: In extreme cases of very hard, solid rock, controlled blasting may be necessary to fracture the rock, followed by mechanical excavation. This requires strict safety protocols and environmental considerations.
-
Specialized Backfill: After excavation (or within conduits), a "bedding" of fine-grained, screened sand or engineered thermal backfill is placed around the cable to cushion it and provide optimal thermal dissipation, protecting it from sharp rock.
-
Heavy-Duty Conduits: Robust, thick-walled conduits (e.g., rigid PVC, steel, or heavily protected HDPE) are used to provide maximum mechanical protection against rock movement or future excavation.
III. Challenges in High Water Table Environments:
-
Trench Instability: Water-saturated soil can lead to trench collapse, making it dangerous and difficult to maintain trench dimensions.
-
Dewatering Requirements: Constant pumping may be necessary to keep trenches dry for cable laying and backfilling, increasing costs and requiring proper water discharge management.
-
Cable Buoyancy: Cables can float in water-filled trenches, making it difficult to maintain proper depth and alignment.
-
Backfill Compaction: Achieving proper compaction in wet conditions is challenging, leading to unstable ground and potential future settlement.
-
Moisture Ingress: Increased risk of water entering conduits or damaging cable joints/terminations if not properly sealed.
IV. Specialized Equipment and Techniques for High Water Table:
-
Dewatering Pumps & Well Points: High-capacity pumps and a network of well points are used to lower the water table in the immediate vicinity of the trench.
-
Trench Shoring/Sloping: Using trench boxes, shoring systems, or extensive sloping to prevent trench collapse in unstable, wet soils.
-
Horizontal Directional Drilling (HDD): The most effective solution, as it completely bypasses the need for open trenches in saturated ground, drilling a path beneath the water table.
-
Cable Weights/Anchoring: In water-filled trenches, weights or anchoring systems may be used to keep buoyant cables submerged and properly aligned.
-
Specialized Backfill: Using porous, free-draining backfill materials (like gravel) immediately around the cable, and ensuring proper compaction to minimize future settlement. Flowable thermal backfill (like CLSM) can also be effective as it displaces water and hardens.
-
Watertight Seals: Ensuring all conduits and cable entries into manholes/vaults are perfectly sealed to prevent water ingress.
Our company provides the robust and specialized underground cable laying equipment, including powerful trenchers, supporting tools for HDD, high-capacity winches, and all necessary accessories to tackle even the most challenging geological and hydrological conditions, ensuring successful and durable cable installations.
Addressing environmental concerns is paramount in modern underground cable laying projects. Proactive environmental impact assessments (EIAs) and robust mitigation strategies are crucial to protect soil, water resources, and sensitive habitats.
I. Soil Protection and Management:
-
A. Minimizing Disturbance:
-
Trenchless Technologies: Our equipment supports Horizontal Directional Drilling (HDD) and Micro-trenching which significantly reduce the amount of excavated soil compared to traditional trenching, thereby minimizing soil disturbance and compaction.
-
Reduced Footprint: Optimizing equipment routes and staging areas to limit the overall disturbed area.
-
-
B. Soil Handling:
-
Topsoil Segregation: Separating and storing nutrient-rich topsoil from subsoil during excavation. This allows for proper re-establishment of vegetation during restoration.
-
Controlled Compaction: Using appropriate compaction equipment and techniques to avoid over-compaction, which can impede water infiltration and root growth, while still ensuring stability.
-
-
C. Erosion Control:
-
Silt Fences & Sediment Basins: Installing barriers to prevent soil erosion and sediment runoff into waterways, especially on sloped terrain or near water bodies.
-
Prompt Restoration & Revegetation: Rapidly backfilling trenches and revegetating disturbed areas with native species to stabilize soil and prevent erosion.
-
II. Water Quality Protection:
-
A. Preventing Contamination:
-
Spill Prevention Plans: Strict protocols for handling, storing, and refueling equipment to prevent leaks or spills of fuels, lubricants, and hydraulic fluids that could contaminate groundwater or surface water.
-
Environmentally Friendly Lubricants: Using biodegradable, non-toxic cable pulling lubricants that minimize chemical impact if they enter the soil or water.
-
-
B. Managing Water Flow:
-
Dewatering Control: If dewatering is necessary in high-water-table areas, ensuring pumped water is filtered or treated to remove sediment before discharge into natural waterways.
-
HDD for Water Crossings: Installing cables under rivers, streams, and wetlands via HDD completely avoids disturbing the water body itself or its banks.
-
Avoiding Aquifers: Careful route planning to avoid sensitive aquifers or groundwater recharge zones.
-
III. Sensitive Habitats and Biodiversity Protection:
-
A. Pre-Construction Surveys:
-
Ecological Assessments: Conducting thorough surveys to identify protected flora and fauna, critical habitats, and migratory routes.
-
Archaeological/Cultural Surveys: Identifying historical sites or artifacts that need protection.
-
-
B. Route Selection & Avoidance:
-
Sensitive Area Bypass: Prioritizing routes that completely avoid wetlands, old-growth forests, designated nature reserves, and known endangered species habitats.
-
-
C. Timing Restrictions:
-
Seasonal Work Windows: Scheduling cable laying to avoid critical periods for wildlife (e.g., bird nesting seasons, fish spawning seasons).
-
-
D. Habitat Restoration:
-
Native Species Replanting: Using local, native plant species for revegetation to support local ecosystems and biodiversity.
-
Monitoring: Post-construction monitoring to ensure habitat recovery and the effectiveness of mitigation measures.
-
Our commitment to sustainable practices is reflected in our equipment design, which facilitates minimal-impact installation methods, and our advisory services that guide clients on integrating comprehensive environmental mitigation strategies into their underground cable laying projects worldwide.
Effective fault detection, efficient repair, and proactive future maintenance planning are crucial for maximizing the reliability, minimizing downtime, and extending the lifespan of underground cable networks. These considerations are often more complex than for overhead lines.
I. Fault Detection:
-
1. Common Fault Types: Underground cables are primarily susceptible to insulation breakdown (due to aging, overheating, or mechanical damage), partial discharge, and dig-ins (accidental damage during excavation).
-
2. Advanced Detection Technologies:
-
Time Domain Reflectometry (TDR) / Optical Time Domain Reflectometry (OTDR): Used for locating faults on metallic cables (TDR) and fiber optic cables (OTDR) by sending a signal and analyzing reflections. Can pinpoint faults with high accuracy.
-
Acoustic/Vibration Sensors: Increasingly deployed along cable routes or within manholes to detect abnormal sounds or vibrations indicative of partial discharge or physical stress.
-
Thermal Imaging/Distributed Temperature Sensing (DTS): Using infrared cameras or fiber optic cables embedded with the power cable to detect localized hot spots, which often precede insulation failure.
-
Partial Discharge (PD) Testing: Non-invasive tests that detect small electrical discharges that can occur in voids or defects within cable insulation, indicating impending failure.
-
Ground Penetrating Radar (GPR) & Electromagnetic Locators: Essential for accurately locating the buried cable itself before any repair excavation, preventing further damage.
-
II. Repair Strategies:
-
1. Fault Location Precision: Accurate fault location is paramount to minimize excavation, reduce repair time, and lower costs. Our equipment and services support precise fault location.
-
2. Excavation & Access: Careful excavation (often using vacuum excavation to avoid damaging adjacent utilities) to expose the damaged cable section. Providing safe working space for repair crews.
-
3. Specialized Splicing & Jointing: Repairing HV/EHV cables requires highly skilled and certified cable jointers. They use advanced, often pre-fabricated, splice kits designed for the specific cable type and voltage, ensuring a watertight and electrically robust connection. Cleanliness and environmental control (e.g., jointing shelters) are critical.
-
4. Re-testing: After repair, the repaired section (and often adjacent sections) must be thoroughly re-tested (e.g., insulation resistance, VLF testing) to verify the integrity of the new joint and the cable system.
-
5. Backfill & Restoration: Proper re-installation of thermal backfill and meticulous compaction are vital to ensure long-term thermal performance and structural integrity of the repaired section.
III. Future Maintenance Planning:
-
1. "As-Built" Documentation: Maintaining accurate and detailed "as-built" drawings and GIS records of cable routes, depths, splice locations, and conduit details. This data is invaluable for future maintenance and fault finding.
-
2. Preventative Maintenance (PM):
-
Routine Inspections: Periodic visual inspections of surface areas above cable routes for signs of subsidence or disturbance.
-
Thermographic Surveys: Infrared surveys to identify subtle temperature anomalies on the surface that may indicate hot spots below.
-
Targeted PD Testing: Regular partial discharge testing of critical joints and terminations.
-
-
3. Predictive Maintenance (PdM):
-
Digital Twins: Creating digital replicas of the underground network that integrate real-time operational data (load, temperature, environmental conditions) from embedded sensors.
-
Analytics & AI: Using predictive analytics and AI to analyze data patterns, forecast potential failures before they occur, and optimize maintenance schedules based on actual asset condition rather than fixed intervals. This allows for proactive repair or replacement, minimizing unplanned outages.
-
-
4. Spares Management: Ensuring an adequate stock of critical cable sections, splice kits, and specialized repair tools.
-
5. Training & Skill Development: Continuously training and certifying personnel in the latest fault detection, repair, and installation technologies and safety protocols.
Our commitment to a "one-stop supply" includes not just the initial underground cable laying equipment but also tools and expertise that support comprehensive fault detection, efficient repair, and intelligent long-term asset management, ensuring your network's enduring performance and reliability.
The Maximum Allowable Pulling Tension (MAPT) is a critical parameter in underground cable pulling, representing the maximum force that can be safely applied to a cable during installation without causing damage to its conductors, insulation, or jacket. Exceeding MAPT can lead to costly cable failure, reduced lifespan, and project delays.
I. Calculation of MAPT:
MAPT is primarily determined by the cable manufacturer and depends on several factors:
-
Conductor Material: Copper conductors typically have a higher tensile strength than aluminum conductors.
-
Conductor Size (kcmil/mm²): Larger conductors can withstand greater pulling forces.
-
Conductor Type: Solid, stranded, or compacted conductors have different tensile properties.
-
Cable Design: The presence of a central strength member (especially in fiber optic cables), armor, or specific jacket materials can influence MAPT.
The general formula for calculating MAPT for power cables is often based on the allowable stress on the conductor:
-
For Copper Conductors: MAPT (lbs) ≤ Conductor kcmil ×8 lbs/kcmil
-
For Aluminum Conductors: MAPT (lbs) ≤ Conductor kcmil ×6 lbs/kcmil
For multi-conductor cables, the MAPT is usually based on the sum of the MAPT of all individual conductors, assuming they are sharing the load equally. However, for practical pulls, derating factors (e.g., 75-80%) are often applied to provide a safety margin, especially for multi-conductor pulls.
For fiber optic cables, the MAPT is often much lower and is specifically tied to the tensile strength of the aramid yarns or central strength member, not the delicate optical fibers themselves. Manufacturers provide explicit MAPT values for their fiber optic cables.
II. Monitoring MAPT During Pulling:
Precise monitoring of pulling tension is paramount to stay within the MAPT and prevent cable damage.
-
1. Automated Hydraulic Pullers with Load Cells: Our state-of-the-art hydraulic cable pullers are equipped with integrated digital load cells (dynamometers) that provide real-time tension readouts. This is the most accurate and reliable method.
-
2. Data Logging: Advanced pullers feature data logging capabilities that record pulling tension, speed, distance, and time throughout the entire pull. This data can be downloaded and analyzed post-pull, serving as an "as-built" quality assurance record and for troubleshooting.
-
3. Pre-Set Tension Limits: Our intelligent pullers allow operators to pre-set the MAPT. If the pulling tension approaches or exceeds this pre-set limit, the machine will automatically slow down or stop, preventing overstressing of the cable.
-
4. Continuous Communication: Maintaining clear and continuous communication between the pulling end, the feeding end, and intermediate points ensures that any anomalies (e.g., snags, increased friction) are immediately addressed.
-
5. Pulling Software & Calculations: Prior to any pull, specialized software is used to calculate theoretical pulling tensions based on cable weight, duct configuration (lengths, bends), and estimated coefficients of friction. This calculation helps determine appropriate equipment sizing and potential points of high stress.
By utilizing our precision-engineered pulling equipment with advanced monitoring capabilities, you can ensure that your underground cable installations are performed safely, efficiently, and without compromising the integrity of your valuable cable assets.
Cable lubricants are absolutely essential for efficient and safe underground cable pulling. They play a critical role in reducing friction, lowering pulling tensions, and ultimately protecting the cable and conduit from damage.
I. The Role of Cable Lubricants:
-
1. Friction Reduction: The primary function is to create a slippery film between the cable jacket and the inner wall of the conduit. This significantly reduces the coefficient of friction (COF), which is the force resisting movement.
-
2. Lowering Pulling Tension: By reducing friction, lubricants drastically lower the required pulling force. This helps stay within the cable's Maximum Allowable Pulling Tension (MAPT), preventing stretching, scuffing, or internal damage to conductors and insulation. It also reduces stress on pulling equipment.
-
3. Preventing Cable Damage: Reduced friction minimizes abrasion, nicks, and scrapes on the cable jacket, which could compromise its protective layers and lead to premature failure. It also lowers sidewall pressure (the force exerted by the cable on the conduit wall at bends), reducing the risk of damage at these critical points.
-
4. Easier Installation: Facilitates smoother, faster pulls, especially for long runs, multiple cables in one conduit, or conduits with many bends.
-
5. Future Removal/Replacement: A well-lubricated cable is often easier to remove from the conduit decades later, simplifying future maintenance or upgrades.
II. Selecting the Correct Lubricant Type:
The selection of the correct lubricant is critical for compatibility and performance. Using the wrong lubricant can cause severe damage to the cable jacket and insulation. Key considerations include:
-
1. Cable Jacket Material: This is the most important factor. Common jacket materials include:
-
PVC (Polyvinyl Chloride): Generally compatible with most water-based or polymer-based lubricants.
-
PE (Polyethylene) / HDPE (High-Density Polyethylene): Good compatibility with most standard lubricants.
-
XLPE (Cross-Linked Polyethylene): Requires lubricants specifically tested for XLPE compatibility.
-
LSZH (Low Smoke Zero Halogen): These environmentally friendly jackets require specially formulated lubricants that won't compromise their fire-retardant properties or emit harmful substances.
-
Rubber/Neoprene: May react adversely with certain oil-based lubricants.
-
Fiber Optic Cables: Often have delicate jackets and require highly compatible, non-gelling, and easy-to-clean lubricants.
-
-
2. Conduit Material: Common conduit materials include:
-
PVC: Most lubricants are compatible.
-
HDPE: Most lubricants are compatible.
-
Steel/Aluminum: Compatibility is less of an issue, but the lubricant must be effective on metal surfaces.
-
Fiberglass: Requires lubricants that won't degrade the resin.
-
-
3. Lubricant Composition:
-
Water-Based (Polymer-Based): The most common and versatile type. They dry to a thin, non-conductive film and are generally compatible with a wide range of cable and conduit materials. They are easy to clean up. Our recommended lubricants are typically high-performance, water-based formulas.
-
Wax-Based / Oil-Based: Less common for general cable pulling due to potential incompatibility with certain jacket materials, tendency to leave sticky residues, and difficulty in cleaning. Should generally be avoided unless explicitly approved by the cable manufacturer.
-
Specialty Lubricants: For very specific applications (e.g., fiber blowing, high-temperature environments), specialized lubricants may be required.
-
-
4. Temperature Range: Some lubricants perform better in specific temperature ranges. Extremely hot or cold conditions can affect their viscosity and effectiveness.
-
5. Manufacturer Recommendations: Always consult both the cable manufacturer's recommendations and the lubricant manufacturer's compatibility data (e.g., IEEE 1210 testing) before selection.
III. Application Techniques:
Proper application is as important as selection. Lubricant should be applied continuously at the feeder end, and often at intermediate points (e.g., manholes, long pulls), to ensure a consistent film throughout the entire conduit length. Over-lubricating is rarely an issue; under-lubricating is a common cause of pulling problems.
Our comprehensive supply chain includes a range of high-performance, tested, and compatible cable lubricants designed to work seamlessly with our cable pulling equipment and various cable types, ensuring optimal installation performance and long-term cable integrity.
Underground cable pulling operations, by their very nature, involve significant risks to personnel and the integrity of the cable. Adhering to strict safety protocols and utilizing appropriate equipment are paramount to mitigate these risks.
I. Essential Safety Protocols:
-
1. Comprehensive Risk Assessment & Planning:
-
Job Hazard Analysis (JHA): Before starting, identify all potential hazards (e.g., electrical, trench collapse, confined space, traffic, pinch points, struck-by).
-
Utility Locating: Meticulous identification and marking of all existing underground utilities (gas, water, sewer, other power, telecom) using advanced methods (GPR, vacuum excavation) to prevent catastrophic dig-ins. "Call Before You Dig" services are mandatory.
-
Emergency Plan: Establish clear emergency procedures, including first aid, evacuation routes, and communication protocols.
-
-
2. Trench and Excavation Safety:
-
Shoring/Sloping/Shielding: Implement proper trench protective systems (shoring, sloping, trench boxes/shields) for any excavation deeper than 5 feet (1.5 meters) or in unstable soil, to prevent trench collapse.
-
Atmospheric Monitoring: For confined spaces (manholes, vaults), test for oxygen deficiency, flammable gases, and toxic gases before entry and continuously during work. Ensure proper ventilation.
-
Safe Access/Egress: Provide ladders or ramps for safe entry and exit from trenches and manholes.
-
-
3. Electrical Safety (for existing live cables):
-
De-energization & Lockout/Tagout (LOTO): For work near or on existing electrical infrastructure, ensure circuits are de-energized, isolated, and properly locked out and tagged out.
-
Minimum Approach Distances (MAD): Maintain safe working distances from any energized lines or equipment.
-
Grounding and Bonding: Proper grounding of equipment and bonding of metallic components to prevent electrical shock.
-
-
4. Personal Protective Equipment (PPE):
-
Mandatory PPE: Hard hats, safety glasses, high-visibility clothing, safety-toed boots.
-
Job-Specific PPE: Insulated gloves and boots (if working near live electrical systems), hearing protection (for noisy equipment), respirators (in dusty or confined spaces), fall protection (if working at height).
-
-
5. Communication:
-
Clear Communication Channels: Establish robust two-way communication (e.g., radios, headsets) between the pulling operator, feeder crew, and any intermediate personnel along the pull path. Hand signals should be pre-determined.
-
Stop Work Authority: Empower all team members with the authority to stop work immediately if an unsafe condition arises.
-
-
6. Equipment Operation:
-
Trained Operators: Only trained and certified personnel should operate cable pulling equipment and heavy machinery.
-
Pinch Point Awareness: Identify and guard all pinch points on equipment (e.g., capstans, rollers) and cable pathways.
-
II. Equipment Considerations for Safety:
-
1. Automated Cable Pullers with Tension Control: Our hydraulic pullers are equipped with load cells and automatic shut-off features. If pulling tension exceeds the pre-set Maximum Allowable Pulling Tension (MAPT), the machine automatically stops or slows, protecting both the cable and personnel.
-
2. Remote Control Capability: Allows operators to be positioned away from the immediate pulling area, enhancing safety during critical pulls.
-
3. Emergency Stop Buttons: Easily accessible emergency stop buttons on all pulling equipment and at strategic points along the pull.
-
4. Properly Sized Rollers & Sheaves: Designed to support the cable's weight and guide it smoothly through conduits and bends without causing damage or kinking.
-
5. Swivels and Running Boards: Used to prevent cable twisting and ensure even distribution of pulling force.
-
6. Cable Feeding Devices: Assist in controlled feeding of the cable into the conduit, reducing manual handling and potential injuries.
-
7. Lighting: Adequate lighting for all work areas, especially in manholes or during night operations.
By integrating these stringent safety protocols with our advanced, safety-focused underground cable pulling equipment, we ensure that every project is executed with the highest regard for worker safety and cable integrity.
Pulling very large diameter cables (e.g., HV/EHV power cables) or multiple cables simultaneously through underground conduits presents significant challenges due to immense weight, friction, and the critical need to prevent damage. Specialized techniques and robust equipment are essential.
I. Techniques for Large Diameter / Multiple Cable Pulls:
-
1. Meticulous Route Planning and Conduit Design:
-
Minimize Bends: Design routes with as few bends as possible, and ensure any necessary bends have the largest possible radius to reduce sidewall pressure and friction.
-
Conduit Sizing: Select conduits with ample internal diameter to comfortably accommodate the cable(s) and allow for a sufficient amount of lubricant. For multiple cables, ensure the sum of their diameters allows for sufficient space within the conduit.
-
Conduit Quality: Use high-quality, smooth-walled conduits (e.g., large diameter HDPE, concrete-encased duct banks) free of burrs or obstructions.
-
-
2. Intermediate Pulling & Setup:
-
Intermediate Manholes/Vaults: For very long runs or those with significant changes in direction, strategically placed intermediate manholes or vaults allow for "segmenting" the pull. This involves pulling the cable in sections, resetting the pulling equipment, or even using an intermediate puller-feeder.
-
"Figure-8" Method: For very long lengths pulled in segments, the cable can be "figure-8'd" on the surface at intermediate points, allowing it to be pulled from both ends of the segment into the conduit. This reduces handling stress on the cable.
-
-
3. Continuous and Controlled Lubrication:
-
High-Volume Lubricant Application: Much larger quantities of high-performance, compatible cable lubricant are required. It must be applied continuously and generously at the feeding end and often at intermediate points (e.g., manholes).
-
Lubricant Pumping Systems: Automated pumping systems can inject lubricant directly into the conduit ahead of the cable.
-
-
4. Pre-calculated Pulling Tensions:
-
Sophisticated Software: Using advanced pulling software to accurately model and predict maximum pulling tensions and sidewall pressures for the entire pull, considering cable weight, conduit type, bends, and lubrication. This determines the necessary equipment capacity.
-
-
5. Heat Management During Pull:
-
Controlled Speed: Maintaining a slower, consistent pulling speed helps manage heat generated by friction, especially for very large cables or long runs.
-
Monitoring Cable Temperature: In critical applications, monitoring the cable's surface temperature during the pull can provide valuable feedback.
-
II. Specialized Equipment:
-
1. High-Capacity Hydraulic Cable Pullers: Our robust hydraulic pullers are engineered for immense pulling forces (tens of thousands of pounds or kN). They feature:
-
Powerful Engines/Motors: To deliver consistent, high torque.
-
Automated Tension Control: Integrated load cells and intelligent controls prevent exceeding MAPT.
-
Large Capstans/Drums: Designed to handle large pulling ropes without slippage or damage.
-
-
2. Cable Feeding Equipment:
-
Powered Cable Feeders: Positioned at the entry point of the conduit, these units actively push the cable into the duct, significantly reducing the pulling force required from the other end. This is crucial for heavy, stiff cables and long pulls.
-
Large Reel Stands & Trailers: Robust stands capable of safely supporting and unwinding massive and heavy cable reels (often weighing many tons).
-
-
3. Specialized Cable Rollers and Guides:
-
Heavy-Duty Rollers: Larger, more robust rollers with smooth, wide sheaves designed to support the immense weight of large cables and maintain the minimum bend radius at all turns and entrances.
-
Manhole Sheaves/Guides: Specifically designed to guide the cable smoothly around corners within manholes and vaults, minimizing sidewall pressure.
-
-
4. Heavy-Duty Pulling Grips/Eyes:
-
Swivel Pulling Eyes: Robust, high-strength pulling eyes specifically designed for large cables, often integrated with a swivel to prevent cable twisting. They attach securely to the cable's strength member or conductors.
-
Basket Grips: Heavy-duty, woven mesh grips for multiple cables or armored cables, designed to distribute pulling force evenly along a larger section of the cable.
-
-
5. Bore Gels & High-Performance Lubricant Pumps: For HDD applications, specialized drilling fluids and high-volume pumps are used to lubricate the bore and facilitate the pull-back of large conduit bundles or cable.
Our company specializes in providing this comprehensive range of high-capacity and precision-engineered underground cable pulling equipment, ensuring that even the most demanding large-scale or multi-cable installations are performed safely, efficiently, and to the highest quality standards.
Temperature, both ambient during installation and projected operational temperature after energization, significantly impacts underground cable pulling. Managing these thermal factors is crucial for the cable's integrity during the pull and its long-term performance.
I. Impact of Ambient Temperature on Pulling:
-
1. Cable Jacket Rigidity/Softness:
-
Cold Temperatures: At very low ambient temperatures, many cable jacket materials (especially PVC) can become stiff and brittle. This increases the risk of cracking, scuffing, or permanent deformation if the cable is pulled around tight bends or handled improperly.
-
Hot Temperatures: In extremely hot weather, some cable jackets can become softer and tackier. This can increase the coefficient of friction, leading to higher pulling tensions and potential sticking.
-
-
2. Lubricant Viscosity:
-
Cold Temperatures: Lubricants can become more viscous (thicker) in cold weather, reducing their effectiveness in lowering friction.
-
Hot Temperatures: Lubricants can become less viscous (thinner) in hot weather, potentially affecting their ability to maintain a consistent film.
-
-
3. Pulling Tension and Sidewall Pressure: Both extreme cold (due to rigidity) and extreme heat (due to tackiness/softness) can lead to higher-than-predicted pulling tensions and sidewall pressures, increasing the risk of exceeding the cable's Maximum Allowable Pulling Tension (MAPT) or minimum bend radius.
II. Mitigation Measures During Pulling (Ambient Temperature):
-
1. Cable Conditioning: If possible, store cables in a temperature-controlled environment before pulling, especially in extreme cold, to improve flexibility.
-
2. Modified Pulling Speeds: Pulling slower in very cold weather to reduce stress, and potentially slower in very hot weather to prevent excessive heat buildup from friction.
-
3. Lubricant Selection & Application: Choose lubricants designed to perform effectively across the anticipated temperature range. In hot weather, generous and continuous application is even more critical. In cold weather, ensure the lubricant's viscosity doesn't hinder its spread.
-
4. Larger Bend Radii & Sheaves: Using larger diameter rollers and sheaves, especially in cold weather, to ensure the cable is never bent too sharply.
-
5. Scheduling: If feasible, schedule pulls during cooler parts of the day in hot climates, or warmer parts of the day in cold climates.
-
6. Cable Heaters/Coolers (Rare): In extreme cases for very critical or sensitive cables, temporary heating or cooling systems might be employed at the feeder end to maintain optimal cable temperature during the pull.
III. Impact of Operational Temperature (Post-Energization) on Cable Pulling Planning:
While not directly impacting the act of pulling, the projected operational temperature of the cable after it's energized significantly influences decisions made during the planning and installation phases, especially concerning backfill and conduit:
-
1. Thermal Dissipation: Underground power cables generate heat when energized. This heat must dissipate into the surrounding soil to prevent the cable's insulation from overheating and degrading.
-
2. Ampacity Derating: If heat cannot escape efficiently (due to poor thermal resistivity of surrounding soil/backfill or insufficient spacing), the cable's current carrying capacity (ampacity) must be "derated" or reduced, meaning it cannot carry its full design load.
-
3. Lifespan Reduction: Prolonged operation above the cable's rated temperature drastically shortens its lifespan, leading to premature failure.
IV. Mitigation Measures for Operational Temperature (Planning & Installation):
-
1. Thermal Resistivity Studies: Conduct thorough soil thermal resistivity studies along the proposed cable route.
-
2. Engineered Thermal Backfill: For critical power cable installations, our expertise extends to recommending and utilizing engineered thermal backfill materials (e.g., fluid thermal grout, selected granular materials with low resistivity). These are specially blended materials placed directly around the cable in the trench to enhance heat transfer away from the cable.
-
3. Proper Cable Spacing: For multiple cables in a trench, ensuring adequate spacing between them allows each cable to dissipate heat effectively.
-
4. Conduit Selection: While conduits provide mechanical protection, they can also trap heat. Careful thermal analysis dictates appropriate conduit sizing and material, and sometimes direct burial is preferred for thermal reasons if mechanical protection is otherwise sufficient.
-
5. Burial Depth: Ensure sufficient burial depth to utilize the stable ground temperature below the frost line and allow for effective heat dissipation into the surrounding soil mass.
-
6. Temperature Monitoring Systems: For very high voltage or critical underground lines, Distributed Temperature Sensing (DTS) fiber optic cables can be installed alongside the power cable to provide continuous, real-time temperature monitoring, allowing for dynamic load management to prevent overheating.
Our comprehensive approach to underground cable pulling extends beyond just the equipment. We offer solutions and expertise that consider the full thermal lifecycle of the cable, ensuring not only a successful pull but also optimal long-term operational performance and reliability.
Selecting the optimal underground cable installation method is crucial for project success, efficiency, and cost-effectiveness. The choice depends on a detailed assessment of site conditions, cable type, environmental considerations, and budget. The primary methods include:
-
1. Direct Burial (Plowing/Trenching):
-
Description: This involves placing cables directly into the ground without conduits.
-
Plowing: A vibratory plow uses a vibrating blade to create a narrow slit in the earth and simultaneously lay the cable. It's fast and minimally disruptive.
-
Trenching: An excavator or trencher digs an open trench, the cable is laid, and then the trench is backfilled.
-
-
Pros: Generally the lowest initial cost, faster installation in open, rural areas with suitable soil.
-
Cons: Less protection for the cable from future excavation or ground movement. Fault location and repair can be more challenging and disruptive.
-
Best Suited For: Rural areas, long runs, direct burial rated cables (e.g., UF cable, armored power cables, direct-burial fiber optic cables), and projects where future replacement is not a primary concern.
-
-
2. Conduit/Duct Bank Installation:
-
Description: Cables are pulled through pre-installed conduits (single pipes) or duct banks (multiple pipes encased in concrete or buried in a common trench).
-
Pros: Provides excellent mechanical protection for the cable, allows for easier future replacement, upgrades, or addition of new cables without re-excavation. Facilitates fault location and repair.
-
Cons: Higher initial cost due to conduit/duct bank materials and installation labor.
-
Best Suited For: Urban areas, critical infrastructure (e.g., substations, data centers), locations with frequent ground disturbance, and situations where future expansion or maintenance is anticipated.
-
-
3. Trenchless Technologies (Horizontal Directional Drilling - HDD, Micro-trenching, Pipe Bursting):
-
Description: These methods install cables or conduits without traditional open excavation.
-
Horizontal Directional Drilling (HDD): A steerable drilling rig creates a bore path under obstacles (roads, rivers, buildings) and then pulls a conduit or cable bundle back through the bore.
-
Micro-trenching: A specialized machine cuts a narrow, shallow trench in paved surfaces, lays small-diameter cables (often fiber optics), and immediately backfills.
-
Pipe Bursting: Used for replacing existing underground pipes; a bursting head breaks the old pipe while pulling a new, larger one into its place.
-
-
Pros: Minimizes surface disruption, ideal for congested urban areas or environmentally sensitive sites, reduces traffic impact, often faster overall project completion.
-
Cons: Higher equipment and specialized labor costs, limited by certain soil conditions (e.g., very rocky ground for micro-trenching), requires precise utility mapping.
-
Best Suited For: Urban environments, crossing natural barriers (rivers, wetlands), densely populated areas where minimizing disruption is paramount, fiber optic deployments.
-
Our company offers a comprehensive range of tools and equipment to support all these underground cable installation methods, including powerful trenchers, plows, advanced cable pullers, conduit handling equipment, and specialized tools for HDD, ensuring you have the right solution for any project requirement globally.
A successful underground cable installation is a sophisticated process that requires a diverse array of essential components and accessories, extending far beyond just the cable. Our "one-stop supply" ensures you have access to everything needed for a robust and reliable installation:
-
1. Conduits and Ducting:
-
Purpose: Provide physical protection for the cable from mechanical damage, moisture, and chemical exposure. They also allow for future cable replacement or additions.
-
Types: High-Density Polyethylene (HDPE), PVC (Polyvinyl Chloride), Fiberglass Reinforced Plastic (FRP), steel, concrete duct banks.
-
Selection Factors: Cable size, soil conditions, burial depth, mechanical strength requirements, chemical resistance, and budget.
-
-
2. Cable Pulling Equipment:
-
Purpose: To safely and efficiently pull cables through conduits or into trenches without exceeding the cable's Maximum Allowable Pulling Tension (MAPT) or minimum bend radius.
-
Our Offerings:
-
Hydraulic Cable Pullers/Winches: High-capacity machines with precise tension control and data logging.
-
Cable Feeders/Pushers: Devices that actively push the cable into the conduit, reducing friction and tension from the pulling end.
-
Cable Stands/Reel Trailers: Robust equipment to safely support and unwind large, heavy cable reels.
-
-
-
3. Cable Pulling Accessories:
-
Pulling Grips/Eyes: Securely attach the pulling rope to the cable, distributing tension evenly.
-
Swivels: Prevent cable twisting during the pull, especially important for multi-conductor or bundled cables.
-
Pulling Ropes/Tapes: High-strength, low-stretch ropes or tapes designed for cable pulling.
-
Conduit Mandrels: Used to prove the integrity and clear the internal diameter of conduits before pulling.
-
Duct Cleaners/Brushes/Sponges: For cleaning conduits of debris before pulling.
-
-
4. Cable Lubricants:
-
Purpose: Reduce friction between the cable jacket and conduit, lowering pulling tensions and preventing cable damage.
-
Types: Water-based polymer lubricants are most common due to compatibility with various cable jackets. Selection is critical for cable jacket material compatibility.
-
-
5. Rollers and Guides:
-
Purpose: Support the cable and guide it smoothly through trenches, manholes, and conduit entries/exits, preventing kinking or damage.
-
Types: Trench rollers, corner rollers, manhole sheaves, bellmouths/conduit entry guides.
-
-
6. Splicing and Termination Materials:
-
Purpose: To connect cable sections (splicing) or connect the cable to equipment (termination) reliably.
-
Types: Heat shrink, cold shrink, push-on, or tape-based splice kits and termination kits, specific to cable voltage and type. Requires specialized tools for preparation.
-
-
7. Backfill Materials:
-
Purpose: To surround and protect the cable/conduit in the trench, provide thermal dissipation (for power cables), and support the surrounding soil.
-
Types: Native soil (if suitable), sand, flowable thermal grout (for power cables), engineered thermal backfill.
-
-
8. Warning and Protection Systems:
-
Purpose: To indicate the presence of buried cables to prevent accidental dig-ins in the future.
-
Types: Detectable warning tapes (buried above the cable), concrete slabs, buried marker balls/locators, and accurate "as-built" documentation.
-
-
9. Safety and Testing Equipment:
-
Purpose: To ensure worker safety during installation and verify cable integrity after installation.
-
Types: PPE, trench shoring, confined space entry equipment, cable fault locators, insulation resistance testers, VLF (Very Low Frequency) test sets, continuity testers.
-
Our expertise extends beyond merely supplying equipment; we offer comprehensive solutions, from advising on the right materials to providing the high-quality tools needed for every stage of your underground cable installation project.
Optimal trench design and proper backfilling are foundational to the long-term longevity, thermal performance, and mechanical protection of underground cables. Neglecting these aspects can lead to premature cable failure and costly repairs.
I. Key Considerations for Trench Design:
-
1. Depth of Burial:
-
Importance: Provides protection from mechanical damage (surface loads, future excavation), maintains stable ground temperature, and often dictated by local codes/standards (e.g., NEC, IEEE).
-
Considerations: Type of cable (power vs. communication), voltage level, soil conditions, frost line depth (in cold climates), and anticipated surface loads (e.g., under roads, driveways).
-
-
2. Trench Width:
-
Importance: Sufficient width allows for safe working space, proper cable placement, adequate backfill around conduits/cables, and efficient heat dissipation (for power cables).
-
Considerations: Number of cables/conduits, cable diameter, minimum spacing requirements between cables for thermal and electrical reasons, and the type of installation (direct burial vs. conduit).
-
-
3. Clearance from Other Utilities:
-
Importance: Prevents interference, damage, or safety hazards with existing water, gas, sewer, and other electrical/telecom lines.
-
Considerations: Adherence to regulatory minimum separation distances. Requires meticulous pre-excavation utility locating and mapping.
-
-
4. Routing and Bending Radii:
-
Importance: Minimize sharp bends which can stress cables during pulling and potentially lead to long-term damage.
-
Considerations: Cables have a minimum bend radius. Trench design should incorporate sweeping curves where direction changes are necessary.
-
-
5. Drainage:
-
Importance: Prevents water pooling in the trench, which can affect backfill compaction, accelerate cable jacket degradation, and impact thermal performance.
-
Considerations: Trench bottom may need to be sloped to facilitate drainage, or a layer of gravel might be used.
-
II. Key Considerations for Backfilling:
-
1. Bedding Material (First Layer):
-
Importance: Provides a uniform, protective cushion around the cable or conduit, preventing damage from sharp objects (rocks) in the native soil.
-
Material: Typically clean, screened sand, fine-grained soil, or flowable thermal grout. Must be free of rocks, debris, or organic matter.
-
Application: Applied directly beneath and around the cable/conduit, typically 3-6 inches thick.
-
-
2. Thermal Backfill (for Power Cables):
-
Importance: Crucial for heat dissipation from energized power cables. Native soil's thermal resistivity can vary greatly; engineered backfill ensures efficient heat transfer.
-
Material: Specialized thermal backfill compounds (often a blend of sand, aggregates, and binders) or fluid thermal grouts (Controlled Low Strength Material - CLSM) with known, low thermal resistivity.
-
Application: Completely encases the cable/conduit within the trench, ensuring full contact for optimal heat transfer.
-
-
3. Compaction:
-
Importance: Prevents future ground settlement (which can damage cables or surface infrastructure), provides mechanical stability, and ensures consistent thermal contact.
-
Technique: Backfill in layers (e.g., 6-12 inch lifts) and compact each layer thoroughly using appropriate compaction equipment (vibratory plates, tampers). Avoid over-compaction which can damage conduits.
-
-
4. Warning Tape/Markers:
-
Importance: Critical for future safety; warns subsequent excavators of buried utilities.
-
Application: Non-metallic, detectable warning tape (often colored and printed with "CAUTION: BURIED ELECTRIC CABLE") is typically buried 12-18 inches above the cable/conduit. Marker posts or RFID/GPS markers can also be used.
-
-
5. Surface Restoration:
-
Importance: Restore the site to its original condition or better, including landscaping, paving, or re-seeding.
-
Our comprehensive range of equipment includes trenchers, plows, and compaction tools, and we provide guidance on best practices for trench design and backfilling, ensuring your underground cable installations are built for maximum durability, reliability, and long-term performance.
Modern underground power cables are continuously evolving, driven by the need for higher performance, greater durability, and enhanced reliability in an increasingly demanding electrical grid. Advancements in materials and cable designs are at the forefront of this evolution:
-
1. Advanced Insulation Materials:
-
Cross-Linked Polyethylene (XLPE): Remains the dominant insulation for medium and high voltage underground cables globally. Advancements focus on cleaner XLPE compounds with fewer impurities, leading to improved dielectric strength, reduced partial discharge activity, and extended lifespan.
-
Tree-Retardant XLPE (TR-XLPE): Specifically designed with additives that inhibit the formation of "water trees" – microscopic channels that can grow in the presence of moisture and an electric field, leading to insulation breakdown. This significantly enhances long-term reliability in wet environments.
-
Ethylene Propylene Rubber (EPR): Increasingly used for its superior flexibility, resistance to corona, and excellent performance in wet and contaminated environments, particularly in harsh industrial applications.
-
High Performance Polypropylene (HPTE/HPPR): Emerging as a potential successor to XLPE for some applications due to its higher operating temperature, improved thermal characteristics, and potentially easier recyclability.
-
-
2. Conductor Materials and Design:
-
Compacted Stranded Conductors: More tightly compacted conductor strands reduce overall cable diameter, improve thermal performance (less air gaps), and lower AC resistance, leading to greater ampacity for a given size.
-
Segmental Conductors: For very large cross-sections in high voltage cables, conductors are often made of insulated segments (Milliken conductors) to reduce skin effect losses and improve current distribution.
-
Aluminum Conductor Composite Core (ACCC) / High-Temperature Low-Sag (HTLS) variants: While primarily for overhead, principles of advanced core materials are being explored for specialized underground applications where thermal and mechanical strength are critical.
-
-
3. Enhanced Jacket and Sheath Materials:
-
Improved Polyethylene (PE) Compounds: Outer jackets are engineered for superior abrasion resistance, UV stability, and chemical resistance, protecting the internal components from external environmental factors.
-
Low Smoke Zero Halogen (LSZH): Increasingly specified, especially for indoor or confined space applications, these jackets do not emit toxic or corrosive gases when exposed to fire, enhancing safety and reducing environmental impact.
-
Integrated Moisture Barriers: Layers within the cable construction (e.g., aluminum foil laminate, lead sheath) provide a robust barrier against water ingress, critical for preventing insulation degradation.
-
-
4. Integrated Monitoring and Sensing Technologies:
-
Fiber Optic Distributed Temperature Sensing (DTS): Fiber optic cables are integrated within the power cable design (or laid alongside) to provide continuous, real-time temperature monitoring along the entire cable length. This allows for dynamic load management, predictive maintenance, and rapid fault location.
-
Partial Discharge (PD) Sensors: Miniaturized sensors can be embedded to monitor for partial discharge activity, an early indicator of insulation degradation.
-
-
5. HVDC (High Voltage Direct Current) Cables:
-
Advancements: Significant progress in DC-specific insulation materials and cable designs (e.g., mass impregnated (MI) and extruded (XLPE-DC) cables) enables efficient long-distance power transmission with lower losses, particularly for connecting remote renewable energy sources (like offshore wind farms) to the grid.
-
Installation Impact: These cables are often very large and require specialized, high-capacity pulling and handling equipment designed for their unique characteristics.
-
These material and design innovations are extending the lifespan of underground cables, increasing their power carrying capacity, improving their resilience to environmental stresses, and enabling smarter, more reliable grid operations. As a leading manufacturer and exporter, we are constantly updating our equipment offerings to be compatible with and facilitate the installation of these cutting-edge cable technologies.
The rapid integration of smart grid technologies is profoundly transforming underground cable installation, moving beyond simply laying power lines to establishing a highly interconnected, intelligent, and resilient energy network. This has significant implications for future projects, equipment, and planning.
I. Implications for Future Underground Cable Installation Projects:
-
1. Increased Use of Integrated Sensing and Communication Cables:
-
Trend: Smart grids rely on real-time data. This means a greater demand for power cables with integrated fiber optic cables (e.g., Fiber-in-Cable or DTS) for temperature, strain, and fault monitoring, or separate communication cables laid alongside power lines.
-
Impact: Installation projects will require more precise handling to protect these integrated sensing elements, and the ability to splice and terminate both power and fiber components in the field.
-
-
2. Emphasis on Reliability and Redundancy:
-
Trend: Smart grids aim for self-healing capabilities and minimized outages. This drives a need for highly reliable underground infrastructure and potentially redundant cable routes.
-
Impact: Greater demand for robust conduit systems, high-quality backfill, and thorough post-installation testing. More focus on minimizing fault occurrence through best practices during installation.
-
-
3. Distributed Energy Resources (DERs) Integration:
-
Trend: The proliferation of solar, wind, and battery storage at the local level (e.g., rooftop solar, community microgrids) requires new, often bidirectional, underground connections within distribution networks.
-
Impact: More frequent, smaller-scale underground cable installations within urban and suburban areas, often requiring compact, agile installation equipment (e.g., mini-HDD rigs, micro-trenchers) to minimize disruption.
-
-
4. Demand for "Undergrounding" for Resilience and Aesthetics:
-
Trend: Driven by storm hardening, wildfire mitigation, and aesthetic preferences, there's a growing push to move overhead lines underground, especially in vulnerable or populated areas.
-
Impact: A significant increase in the volume of underground installation projects, necessitating efficient, high-speed trenchless technologies and robust traditional trenching solutions.
-
-
5. Data-Driven Planning and Execution:
-
Trend: The use of "digital twins" and advanced analytics to simulate installations, predict performance, and optimize maintenance.
-
Impact: Integration of real-time data from our smart pulling equipment (tension, speed, distance) into project management systems, allowing for "as-built" documentation that feeds the digital twin for long-term asset management.
-
II. Impact on Equipment and Planning:
-
1. Smarter, Connected Equipment:
-
Equipment: Cable pullers, tensioners, and trenchers will increasingly feature integrated sensors, GPS, and communication modules for real-time data collection and remote monitoring.
-
Planning: Project managers will use this data for dynamic optimization of pulling operations, ensuring adherence to specifications, and for creating comprehensive post-installation reports.
-
-
2. Miniaturization and Precision:
-
Equipment: Smaller, more precise trenchless tools (e.g., micro-HDD for fiber/smaller power cables) for navigating congested urban undergrounds with minimal disruption.
-
Planning: Detailed underground utility mapping (with GPR, vacuum excavation) becomes even more critical to plan precise bore paths and avoid existing infrastructure.
-
-
3. Automation and Robotics:
-
Equipment: Development of semi-autonomous trenching and laying machines, robotic conduit inspection, and automated cable feeding systems to improve efficiency, safety, and consistency.
-
Planning: Incorporating robotic workflows into project plans, optimizing resource allocation, and leveraging automation for faster project delivery.
-
-
4. Enhanced Training and Skill Sets:
-
Workforce: Demand for technicians skilled in both traditional cable installation and new technologies like fiber splicing, data analysis from smart equipment, and operating advanced machinery.
-
Planning: Comprehensive training programs will be essential to ensure the workforce is equipped for the complexities of smart grid-compatible installations.
-
-
5. Focus on Lifecycle Management:
-
Equipment: Tools that support not just installation but also precise fault location, repair, and diagnostic testing (e.g., VLF test sets, PD locators) become even more vital for maintaining smart grid reliability.
-
Planning: Shifting towards a holistic lifecycle approach, where installation quality directly contributes to reduced operational costs and enhanced grid resilience over decades.
-
Our company is at the forefront of supplying the advanced, smart equipment and tools necessary to meet these evolving demands of underground cable installation, empowering our clients to build the intelligent, resilient power and communication networks of the future.