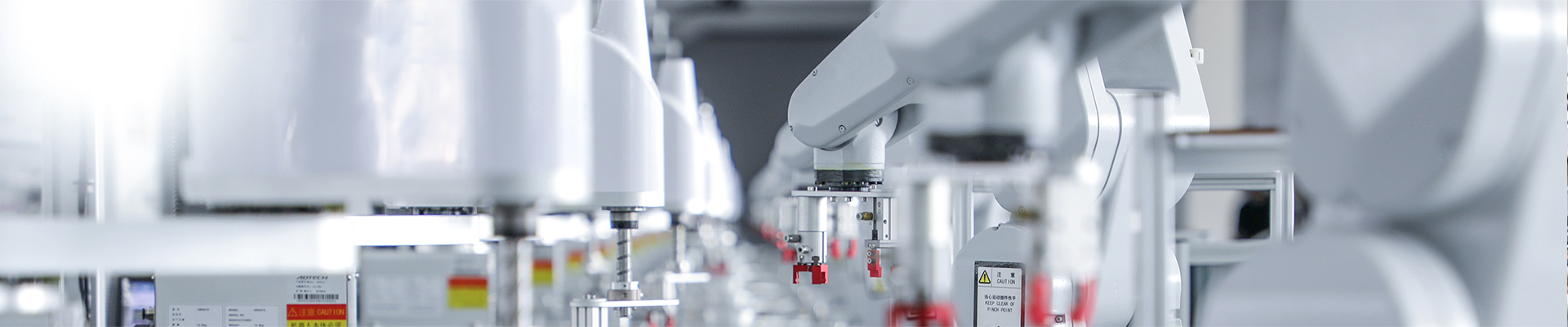
FAQ
The dual electrical and optical nature of OPGW (Optical Ground Wire) necessitates specialized tools and equipment for its safe and efficient stringing. This ensures the mechanical integrity of the metallic components and the delicate optical fibers are preserved. Our comprehensive one-stop supply includes all essential equipment for OPGW installation:
I. Core Stringing Equipment (Adapted for OPGW):
-
1. Hydraulic Tensioners:
-
Key Features: Must be capable of providing precise, continuous, and adjustable tension to prevent the OPGW from touching the ground or encountering obstacles during stringing. They often feature multiple bullwheels with appropriate groove linings (e.g., neoprene or specialized plastic) to protect the OPGW's outer metallic strands and prevent damage to the optical core.
-
Our Offering: Our range of hydraulic tensioners is designed with advanced control systems and non-abrasive bullwheel materials, optimized for the unique characteristics of OPGW, ensuring minimal stress on the cable.
-
-
2. Hydraulic Pullers:
-
Key Features: Equipped with accurate tension readouts (dynamometers) and often automatic shut-off mechanisms. They need sufficient pulling capacity for the weight and length of the OPGW span.
-
Our Offering: Our pullers feature robust designs and precision controls to maintain the Maximum Allowable Pulling Tension (MAPT) for OPGW, safeguarding the optical fibers within.
-
-
3. Puller-Tensioner Machines:
-
Key Features: Combined units offering both pulling and tensioning capabilities, providing greater operational flexibility and efficiency, especially for complex or multi-circuit installations.
-
II. Specialized OPGW-Specific Accessories:
-
1. OPGW Stringing Blocks (Pulleys):
-
Key Features: Critical for guiding the OPGW along the span and around tower structures. They must have large diameter sheaves (typically much larger than for conventional conductors, often 20-30 times the OPGW diameter) to maintain the minimum bending radius of the optical fibers. The grooves must be wide, smooth, and often lined with highly protective, non-abrasive materials (e.g., polyurethane, neoprene) to prevent crushing or abrasion of the OPGW's outer strands.
-
Our Offering: We provide a variety of OPGW-specific stringing blocks and rollers, meticulously designed to protect the cable's delicate optical core during installation.
-
-
2. Non-Rotating Pulling Ropes:
-
Key Features: Essential to prevent torque and twisting from being transferred to the OPGW cable, which could damage the optical fibers. Typically braided ropes are preferred.
-
-
3. Anti-Twisting Devices (Swivels):
-
Key Features: Heavy-duty swivels must be inserted between the pulling grip and the pulling rope to absorb any torsional forces, preventing the OPGW from twisting during the pull.
-
-
4. OPGW Pulling Grips (Stockings/Socks):
-
Key Features: Specifically designed to apply uniform gripping pressure over a larger surface area of the OPGW, minimizing stress concentration on the delicate optical core. They often have internal liners or special weaves.
-
-
5. Running Boards (for Multiple Wires): If installing multiple wires simultaneously, specialized running boards ensure even tension distribution and prevent wire contact.
III. Safety and Support Equipment:
-
1. Cable Reel Stands/Trailers: Robust, high-capacity stands capable of safely unwinding large and heavy OPGW reels while maintaining controlled back tension.
-
2. Hydraulic Crimping Tools: For securing OPGW dead-end and suspension clamps. These require specific dies matched to the OPGW type.
-
3. Fall Protection Equipment: For personnel working at height on towers.
-
4. Communication Systems: Reliable two-way communication (radios, headsets) between puller/tensioner operators and tower crews.
-
5. Grounding Equipment: Essential for electrical safety, as OPGW is installed on energized or potentially energized structures.
By providing a full spectrum of specialized OPGW installation tools and equipment, from high-precision tensioners and pullers to protective stringing blocks and anti-twisting devices, we ensure that our clients can achieve safe, efficient, and damage-free OPGW deployments worldwide.
Splicing and terminating OPGW (Optical Ground Wire) cables are highly critical processes that directly impact the long-term optical performance, mechanical integrity, and electrical continuity of the installed system. Precision, environmental protection, and specialized expertise are paramount.
I. Critical Considerations for Splicing OPGW:
-
1. Specialized Splice Enclosures (Joint Boxes):
-
Purpose: These enclosures are designed to house and protect the delicate optical fiber splices from environmental factors (moisture, dust, extreme temperatures), mechanical stress, and vibration. They also provide strain relief for the OPGW cable.
-
Key Features: Must be robust, hermetically sealed, UV-resistant, and corrosion-resistant. They must also accommodate the specific OPGW cable diameter and fiber count, and often include grounding provisions.
-
-
2. Fusion Splicing Technology:
-
Purpose: The standard method for joining optical fibers in OPGW. Fusion splicers precisely align and fuse the fiber ends using an electric arc, creating a low-loss, high-strength connection.
-
Equipment: High-precision fusion splicers specifically designed for single-mode fibers. Requires clean environment, power source, and skilled technicians.
-
-
3. Fiber Preparation Tools:
-
Purpose: Essential for stripping the fiber coating, cleaning the bare fiber, and cleaving (cutting) the fiber end to a precise angle, all critical for low-loss splices.
-
Equipment: Fiber strippers, cleavers, alcohol wipes, lint-free tissues.
-
-
4. Optical Loss Budget:
-
Consideration: Each splice introduces a small amount of optical loss. The total cumulative loss of all splices and the cable's attenuation must remain within the optical power budget of the communication system to ensure signal quality.
-
-
5. Protection of Splices:
-
Purpose: After fusion, the bare fiber splice must be protected.
-
Method: Typically achieved using heat-shrink splice protectors or mechanical protectors, which are then organized within splice trays inside the enclosure.
-
-
6. Grounding and Shielding:
-
Purpose: Maintaining the electrical continuity of the OPGW's metallic components across the splice point, providing grounding and lightning protection.
-
Method: Splice enclosures often incorporate electrical continuity clamps or bonding braids to connect the metallic components of the OPGW across the joint.
-
II. Critical Considerations for Terminating OPGW:
-
1. Specialized Termination Hardware:
-
Purpose: To securely anchor the OPGW cable at the tower or substation, transfer mechanical tension, and transition the optical fibers to indoor or outdoor communication equipment.
-
Types: Preformed dead-ends (helical grips), suspension clamps, down-lead clamps, and specific hardware for guiding the OPGW from the top of the tower to the splice enclosure or entry point.
-
-
2. Mechanical Strength:
-
Consideration: Termination hardware must be rated to withstand the full design tension and potential environmental loads (wind, ice) on the OPGW cable, ensuring it remains securely attached to the structure.
-
-
3. Fiber Management:
-
Purpose: At the termination point, the optical fibers are carefully separated from the metallic components of the OPGW and routed into a Fiber Optic Distribution Panel (FODP) or other communication enclosure.
-
Method: Requires careful breakout kits, protective tubes, and proper slack management to prevent tight bends or stress on the fibers.
-
-
4. Electrical Grounding:
-
Purpose: Ensure the metallic components of the OPGW are effectively grounded to the tower structure and ultimately to earth, providing critical lightning protection.
-
Method: Proper bonding and grounding connections at every tower and substation entry point.
-
-
5. Environmental Protection:
-
Consideration: Outdoor termination points and fiber optic patch panels must be robust, weatherproof, and designed to protect the optical connections from moisture, UV radiation, and physical damage.
-
III. Overall Importance:
The quality of splicing and termination directly impacts the overall performance and longevity of the OPGW system. Poorly executed splices can lead to high optical losses, while inadequate terminations can compromise both mechanical integrity and electrical grounding. Our company not only supplies the specialized OPGW installation tools but also provides guidance on best practices for splicing and termination, ensuring seamless integration and optimal performance of your OPGW network.
Comprehensive testing and commissioning procedures are paramount for OPGW (Optical Ground Wire) after installation. These procedures verify both its crucial electrical grounding function and its high-performance optical communication capabilities, ensuring system integrity and reliability before being put into service.
I. Electrical Testing and Commissioning:
-
1. Visual Inspection:
-
Purpose: To check for any visible mechanical damage to the OPGW cable, termination hardware, clamps, and grounding connections on towers and at substations.
-
Procedure: A thorough visual inspection by trained personnel, often using binoculars or drones for elevated sections.
-
-
2. Electrical Continuity and Resistance Testing:
-
Purpose: To confirm the continuous electrical path of the OPGW's metallic components from tower to tower and to ground. Verifies the integrity of splices and terminations.
-
Procedure: Using a low-resistance ohmmeter or multimeter to measure resistance along the OPGW path and to ground. Compare readings against design specifications.
-
-
3. Grounding System Resistance Testing:
-
Purpose: To verify that the OPGW is effectively grounded to the tower structures and the overall substation ground grid, ensuring proper lightning protection.
-
Procedure: Earth resistance (ground impedance) tests (e.g., fall-of-potential method) are performed on tower footings and substation ground grids to ensure they meet specified resistance values.
-
-
4. Corona and RIV (Radio Interference Voltage) Tests (for EHV/UHV applications):
-
Purpose: To detect any sources of corona discharge or radio interference that could affect the performance of the power line or communication signals.
-
Procedure: Specialized tests conducted under energized conditions to measure RIV levels.
-
-
5. Short-Circuit withstand verification (Design Review):
-
Purpose: Though not a field test, review of documentation and calculations to confirm the OPGW's metallic cross-section is adequate to safely carry and dissipate maximum fault currents without damage.
-
II. Optical Testing and Commissioning:
-
1. Optical Time Domain Reflectometer (OTDR) Testing:
-
Purpose: The most critical optical test. It provides a "fingerprint" of the fiber, measuring optical loss, locating splices, connectors, and any anomalies (bends, breaks, high-loss events) along the entire fiber length. It also measures the overall length of the fiber.
-
Procedure: Bi-directional OTDR tests (from both ends of each fiber) are performed at multiple wavelengths (e.g., 1310 nm and 1550 nm) for each individual fiber. Results are saved as baseline data.
-
-
2. Optical Power Meter (OPM) and Light Source Testing (Insertion Loss Test):
-
Purpose: To measure the total end-to-end attenuation (loss) of each fiber link, including all splices and connectors. This confirms the link meets the design's optical loss budget.
-
Procedure: A calibrated light source injects light at one end, and an OPM measures the received power at the other end. Loss is calculated in dB. Performed bi-directionally.
-
-
3. Visual Fault Locator (VFL) (Preliminary/Troubleshooting):
-
Purpose: A simple tool that injects visible red laser light into the fiber. Useful for quick continuity checks, identifying breaks in short distances, or locating misaligned connections.
-
Procedure: Light leakage indicates a problem.
-
-
4. Fiber End-Face Inspection:
-
Purpose: To ensure that fiber optic connector end-faces are clean and free from scratches or defects, which can cause significant optical loss.
-
Procedure: Using a fiber inspection microscope or probe. Cleaning is performed if necessary.
-
-
5. Chromatic Dispersion (CD) and Polarization Mode Dispersion (PMD) Testing (for high-speed, long-haul networks):
-
Purpose: For very high-speed (e.g., 10 Gbps and above) or very long-distance applications, these tests measure signal distortion that can limit bandwidth.
-
Procedure: Specialized equipment measures dispersion characteristics.
-
III. Documentation and Reporting:
-
All test results (electrical and optical) are meticulously documented, compared against design specifications, and retained as critical "as-built" records. This data is invaluable for future maintenance, troubleshooting, and network management.
Our company provides not only the robust OPGW installation equipment but also comprehensive testing solutions and expertise, including advanced fiber optic test equipment and electrical measurement tools, ensuring that every OPGW installation meets the highest standards of performance and reliability.
The OPGW market is experiencing dynamic growth, driven by the global expansion of power grids, the demand for smart grid functionalities, and the continuous need for robust telecommunication infrastructure. Latest trends and innovations are making OPGW even more versatile and efficient.
I. Latest Trends in OPGW Cable Technology:
-
1. Higher Fiber Counts:
-
Trend: Traditional OPGW cables might have had 24-48 fibers. Modern OPGW designs now frequently incorporate 96, 144, or even 288+ optical fibers.
-
Implication: This caters to the exponential growth in data demand, provides ample capacity for future expansions (e.g., 5G backhaul, IoT sensor networks), and allows for dark fiber leasing, creating new revenue streams for utilities.
-
-
2. Optimized Cable Designs for Specific Applications:
-
Trend: Beyond the classic central tube and multi-layer designs, there's a focus on specialized OPGW for:
-
Retrofit Applications: Lighter, smaller diameter OPGW (e.g., with aluminum-clad steel wires) to replace existing shield wires on older towers with limited load capacity, often without requiring costly tower modifications.
-
High Short-Circuit Current Capacity: OPGW designs with larger aluminum cross-sections or specialized conductors to handle very high fault currents in critical transmission lines.
-
Extreme Environmental Conditions: Enhanced corrosion resistance for coastal areas, or specific designs for high ice/wind loading regions.
-
-
-
3. Integration of Advanced Materials:
-
Trend: Use of advanced alloys for the metallic strands that offer superior strength-to-weight ratios or improved electrical conductivity, while maintaining corrosion resistance.
-
Implication: Lighter cables reduce tower loading, while improved conductivity enhances electrical performance.
-
-
4. Enhanced Protection for Optical Fibers:
-
Trend: Improvements in gel-filled stainless steel tubes or PBT tubes for the optical core to provide even greater protection against moisture, hydrogen ingress, and mechanical stress.
-
Implication: Increased longevity and reliability of the optical component, especially in harsh environments.
-
II. Innovations in OPGW Installation Methods and Equipment:
-
1. Real-time Tension Monitoring and Data Logging:
-
Innovation: Our advanced hydraulic pullers and tensioners feature integrated digital load cells and GPS, providing real-time tension, speed, and distance data. This data is logged and can be wirelessly transmitted.
-
Implication: Ensures strict adherence to OPGW's Maximum Allowable Pulling Tension (MAPT), prevents damage to optical fibers, provides verifiable "as-built" records, and optimizes stringing operations for efficiency and safety.
-
-
2. Drone Technology for Pre-Installation Surveys and Inspections:
-
Innovation: Drones equipped with high-resolution cameras, LiDAR, and thermal imaging are used for detailed route surveys, obstacle identification, tower inspections, and post-installation visual checks.
-
Implication: Enhances safety by reducing manual tower climbing, improves accuracy of survey data, and speeds up the planning and inspection phases.
-
-
3. Improved Stringing Blocks and Accessories:
-
Innovation: Development of lighter, more durable stringing blocks with optimized groove designs and advanced polymer linings that further minimize friction and protect the OPGW's outer strands and optical core.
-
Implication: Reduced cable damage, smoother pulls, and extended equipment lifespan.
-
-
4. Optimized Splicing and Testing Equipment:
-
Innovation: Faster and more automated fusion splicers, handheld OTDRs with cloud connectivity, and integrated fiber cleaning and inspection tools.
-
Implication: Quicker, more accurate, and reliable fiber optic connections, streamlining the commissioning process.
-
-
5. Live-Line Installation Techniques (where applicable):
-
Innovation: While challenging, advancements in live-line tools and techniques allow for the replacement of existing ground wire with OPGW without de-energizing the transmission line, minimizing service disruption.
-
Implication: Significant economic benefits by avoiding costly outages. Requires highly specialized equipment and highly trained personnel.
-
These trends and innovations underscore the growing importance of OPGW in building the resilient, intelligent, and interconnected power and communication networks of tomorrow. As a prominent manufacturer and exporter, our company is dedicated to providing cutting-edge OPGW installation equipment that supports these advancements, helping our global clients achieve superior performance and efficiency in their projects.
Preventing damage to the sensitive optical fibers within OPGW during stringing is paramount. Unlike conventional conductors, OPGW's primary vulnerability is its optical core. The most critical factors to control are:
-
1. Pulling Tension (Tensile Stress):
-
Control: The pulling tension applied to the OPGW must never exceed its Maximum Allowable Pulling Tension (MAPT). Exceeding MAPT can stretch the metallic strands, which in turn can induce micro-bends or macro-bends in the optical fibers, leading to increased optical attenuation (signal loss) or even fiber breakage.
-
Solution: Our hydraulic pullers and tensioners are equipped with precision digital dynamometers (load cells) and automatic tension control systems. These systems provide real-time tension readouts and can be pre-set to automatically slow down or stop the operation if tension approaches or exceeds the OPGW's MAPT. This ensures the fibers remain unstressed.
-
-
2. Minimum Bending Radius (Bending Stress):
-
Control: OPGW cables have a strict minimum bending radius (MBR) for both static (installed) and dynamic (during stringing) conditions. Bending the cable too sharply will cause severe macro-bending losses or permanent damage to the fibers. Dynamic MBR during stringing is typically much larger than the static MBR.
-
Solution: We provide large-diameter OPGW-specific stringing blocks (pulleys) and sheaves that ensure the OPGW is never bent beyond its dynamic MBR. These blocks feature wide, smooth grooves lined with protective materials (e.g., neoprene, polyurethane) to distribute pressure evenly and prevent kinking or crushing.
-
-
3. Torsional Forces (Twisting):
-
Control: Twisting the OPGW cable during stringing can cause the optical fibers inside to twist or even buckle, leading to significant signal loss or fiber damage. This is especially critical for OPGW with a central optical tube design.
-
Solution: The use of high-quality, non-rotating pulling ropes (e.g., braided steel or synthetic ropes) and robust anti-twisting swivels between the pulling grip and the pulling rope is essential. These devices prevent torque from being transferred from the pulling system to the OPGW itself.
-
-
4. Abrasion and Crushing (External Mechanical Damage):
-
Control: Any rubbing, scuffing, or crushing of the OPGW's outer metallic layers can compromise its structural integrity and potentially damage the internal optical unit. This includes contact with tower steel, ground, or other obstacles.
-
Solution: Beyond the specialized stringing blocks, proper site preparation, ensuring clear pathways, using line guards on cross-arms, and meticulous handling are crucial. Our equipment is designed to facilitate smooth, contact-free stringing.
-
-
5. Stringing Speed:
-
Control: While efficiency is important, excessively high stringing speeds can lead to dynamic over-tensioning, increased friction, and greater risk of accidental damage.
-
Solution: Our tensioners and pullers allow for precise control over stringing speed, enabling operators to maintain a slow, steady pace, especially around critical points like angle towers or mid-span obstructions.
-
-
6. Communication and Supervision:
-
Control: Clear, continuous communication between the puller operator, tensioner operator, and ground/tower crews is vital to respond immediately to any issues (e.g., snagging, abnormal tension spikes).
-
Solution: Implementing robust two-way radio or headset communication systems across the entire stringing span. Continuous supervision by experienced personnel.
-
By utilizing our precisely engineered OPGW stringing equipment and adhering to these critical control factors, our clients can ensure successful, damage-free, and high-performance OPGW installations.
The internal design of OPGW (Optical Ground Wire) cables, particularly whether it's a central tube or multi-loose tube (also known as stranded loose tube) construction, significantly influences the stringing process and the selection of specialized equipment. Understanding these differences is key to a successful installation.
I. Central Tube OPGW Design:
-
Description: In a central tube design, all the optical fibers are housed within a single, larger hermetically sealed stainless steel tube (or similar protective material) located at the core of the OPGW. The metallic strands (aluminum-clad steel, aluminum alloy) are then stranded around this central tube.
-
Impact on Stringing:
-
Torsional Sensitivity: Central tube designs are generally more sensitive to twisting (torsion) during stringing. Any significant twist can cause the central tube to rotate or buckle, stressing the fibers inside and leading to optical performance degradation or damage.
-
Minimum Bend Radius (Dynamic): While the static MBR might be similar, the dynamic MBR during stringing needs strict adherence due to the single, rigid central tube.
-
Crush Resistance: Can be slightly less crush-resistant than multi-tube designs as all fibers are concentrated in one area.
-
-
Equipment Implications:
-
Anti-Twisting Swivels: Absolutely critical. High-quality, robust anti-twisting swivels must be used between the pulling grip and the pulling rope to prevent any torque transfer.
-
Larger Diameter Stringing Blocks: Even more emphasis on using the largest possible diameter stringing blocks to ensure the cable is never bent too sharply, especially at angles.
-
Non-Rotating Pulling Ropes: Mandatory to avoid inducing twist.
-
Precise Tension Control: Essential to prevent over-tensioning which could indirectly induce torsion or micro-bends if the outer layers deform.
-
II. Multi-Loose Tube (Stranded Loose Tube) OPGW Design:
-
Description: In this design, optical fibers are grouped into several smaller, individual loose tubes. These tubes are then stranded around a central strength member (e.g., a steel wire) along with the metallic conductor strands. This stranding can be S-Z stranding or helical.
-
Impact on Stringing:
-
Torsional Tolerance: Generally more tolerant to twisting compared to central tube designs. The individual loose tubes can accommodate some degree of twisting without directly stressing the fibers, thanks to the "excess fiber length" within the tubes.
-
Flexibility: Often more flexible than central tube designs of comparable diameter due to the stranded nature of the tubes.
-
Crush Resistance: Can offer slightly better crush resistance due to the distributed protection of multiple tubes.
-
-
Equipment Implications:
-
Swivels are still recommended: While more tolerant, using a good quality anti-twisting swivel is still best practice to minimize any torsional stress.
-
Stringing Blocks: Standard OPGW-specific large-diameter blocks with protective linings are still required.
-
Pulling Grips: Standard OPGW pulling grips are suitable.
-
III. Overall Considerations for Both Designs:
Regardless of the OPGW design, certain principles of stringing remain universal and require specialized equipment:
-
Precise Tension Control: All OPGW requires vigilant tension monitoring to stay within the MAPT.
-
Adequate Sheave Diameters: Always adhere to the manufacturer's recommended dynamic bending radius by using appropriately sized stringing blocks.
-
Protective Linings: All stringing blocks must have non-abrasive, protective linings.
-
Skilled Operators: Proper training and experience are crucial for understanding the nuances of each OPGW type.
Our comprehensive range of OPGW stringing equipment, including adaptable pullers, tensioners, and a wide array of specialized stringing blocks and accessories, is designed to accommodate various OPGW cable constructions, ensuring optimal performance and protection for your specific project requirements.
OPGW stringing inherently involves working at height and often near existing energized power lines, making conductor clearance management and safety paramount. Adhering to strict best practices is essential to protect personnel, prevent damage to existing infrastructure, and avoid catastrophic incidents.
I. Critical Safety Protocols & Planning:
-
1. Comprehensive Pre-Stringing Survey and Risk Assessment (Job Hazard Analysis - JHA):
-
Best Practice: Conduct a detailed site survey to identify all existing utilities, crossing points (roads, railways, power lines, communication lines), and potential obstacles. Perform a thorough JHA to identify all hazards and develop specific mitigation strategies for each span.
-
Implication: Our expertise extends to advising on meticulous planning, including identifying suitable puller/tensioner sites and intermediate setup points.
-
-
2. De-energization (Preferred Method):
-
Best Practice: Whenever possible, and especially for work directly on or adjacent to conductors, de-energize and properly ground the existing power lines in the work area. Implement strict Lockout/Tagout (LOTO) procedures.
-
Implication: This is the safest approach and should be prioritized.
-
-
3. Minimum Approach Distances (MAD):
-
Best Practice: For work on or near energized lines, rigorously adhere to established Minimum Approach Distances (MAD) as defined by local regulations and utility standards. Only qualified and authorized personnel using approved insulated tools and equipment should approach within MAD.
-
Implication: Strict training and supervision are required.
-
-
4. Grounding and Bonding:
-
Best Practice: All stringing equipment (pullers, tensioners, reel stands), as well as tower structures and conductive parts of stringing blocks, must be properly grounded and bonded to the earth. This provides a safe path for any induced or fault currents.
-
Implication: Utilize high-quality grounding rods, clamps, and cables. Our equipment is designed with clear grounding points.
-
-
5. Warning Devices and Temporary Clearances:
-
Best Practice: At road crossings, railway crossings, or existing power line crossings, implement temporary warning devices such as:
-
Temporary Warning Structures/Nets: To prevent OPGW from sagging too low or contacting traffic.
-
Insulated Crossings Guards/Hoses: To protect existing energized conductors from accidental contact with the OPGW or pulling rope.
-
Flagmen/Traffic Control: To manage traffic flow and ensure public safety.
-
-
Implication: Requires careful coordination with local authorities (e.g., road, rail, other utilities).
-
-
6. Personal Protective Equipment (PPE):
-
Best Practice: Mandatory use of appropriate PPE for all personnel, including hard hats, safety glasses, high-visibility clothing, safety-toed boots, and insulated gloves/sleeves when working near energized parts.
-
-
7. Emergency Response Plan:
-
Best Practice: Develop and communicate a clear emergency response plan for potential incidents (e.g., accidental contact, equipment failure, injury).
-
II. Equipment and Methodological Considerations:
-
1. Pilot Rope and Running Boards:
-
Best Practice: Often, a non-conductive pilot rope is strung first, then a stronger pulling rope, and finally the OPGW. Running boards can be used for multi-line stringing to maintain separation.
-
-
2. Controlled Sag and Tension:
-
Best Practice: Maintain controlled sag and tension throughout the stringing process using precise pullers and tensioners to prevent unexpected contact with obstacles or existing lines.
-
-
3. Continuous Communication:
-
Best Practice: Maintain constant, clear two-way communication (e.g., radios, headsets) between all personnel involved in the stringing operation – puller operator, tensioner operator, tower crews, and safety officers.
-
-
4. Spotters and Safety Observers:
-
Best Practice: Designate dedicated spotters at critical points (crossings, close proximity to other lines) to continuously monitor clearances and provide immediate warnings.
-
-
5. Weather Monitoring:
-
Best Practice: Monitor weather conditions closely (wind speed, lightning risk). High winds can make controlled stringing impossible and increase the risk of conductor swing. Suspend operations during adverse weather.
-
Our comprehensive OPGW stringing solutions include not only the highly controllable stringing equipment but also guidance on best safety practices and a range of safety accessories, helping our clients execute challenging OPGW installations with the utmost safety and precision.
Terrain and span length are fundamental factors that significantly influence the OPGW cable stringing strategy and directly dictate the type and capacity of stringing equipment required. Proper consideration of these elements ensures a smooth, safe, and efficient installation.
I. Influence of Terrain:
-
1. Flat/Open Terrain:
-
Impact: Simplest stringing conditions. Minimal obstructions, easy access for equipment.
-
Strategy: Long continuous pulls are often feasible.
-
Equipment: Standard hydraulic pullers and tensioners are well-suited. Reel stands and trailers can be positioned easily.
-
-
2. Hilly/Mountainous Terrain:
-
Impact: Challenging access for equipment, steep inclines/declines, potential for severe vertical angles, increased risk of OPGW touching ground or obstacles.
-
Strategy: May require more frequent intermediate setup points, potentially using helicopters for initial pilot rope installation in inaccessible areas. Careful calculation of sag and tension to avoid ground contact on undulations.
-
Equipment: More powerful pullers with greater line pull capacity for steep inclines. Specialized stringing blocks designed for high vertical angles. Remote-controlled equipment or advanced communication systems for operations across varied elevations. May necessitate smaller, more agile equipment that can be transported more easily.
-
-
3. Urban/Congested Areas:
-
Impact: Limited space for equipment setup, numerous existing structures, roads, railways, and other utility crossings. High public safety risk.
-
Strategy: Short spans, often requiring specialized tension stringing methods (live-line or de-energized with strict clearances). Extensive use of temporary warning structures (e.g., nets, insulated crossing guards). Meticulous traffic management.
-
Equipment: Compact, highly maneuverable pullers and tensioners. A wider array of specialized stringing accessories like insulated rollers, ground mats, and overhead crossing structures. Emphasis on real-time tension monitoring to avoid sag violations.
-
-
4. Wetlands/Swamps/Water Crossings:
-
Impact: Difficult access, unstable ground, environmental sensitivity.
-
Strategy: May require specialized access equipment (e.g., amphibious vehicles, barges). Helicopters for pilot wire installation over water. Very long spans across water bodies are common.
-
Equipment: High-capacity pullers and tensioners for exceptionally long spans. Specialized floating stringing blocks or roller systems for water crossings. Environmental protection equipment.
-
II. Influence of Span Length:
-
1. Short Spans (e.g., less than 300m):
-
Impact: Relatively lower pulling tensions. Less prone to sag issues.
-
Strategy: Can often be strung relatively quickly.
-
Equipment: Standard-capacity pullers and tensioners are typically sufficient.
-
-
2. Medium Spans (e.g., 300m - 600m):
-
Impact: Moderate pulling tensions. Sag management becomes more critical.
-
Strategy: Standard tension stringing methods.
-
Equipment: Mid-range hydraulic pullers and tensioners are common.
-
-
3. Long Spans (e.g., over 600m, or extremely long river/valley crossings > 1000m):
-
Impact: Requires very high pulling forces to maintain clearances. Increased risk of OPGW damage due to cumulative friction and dynamic stresses.
-
Strategy:
-
Higher Capacity Equipment: Requires the most powerful pullers and tensioners.
-
Precise Tension Control: Absolute necessity to prevent exceeding MAPT.
-
Intermediate Suspension: In extremely long spans, temporary suspension of the OPGW at intermediate points can break down the pull into shorter segments, reducing overall tension.
-
Pilot Wire and "Tagging": Often involves pulling a pilot wire, then a larger pulling rope, then the OPGW.
-
Helicopter Stringing: For initial pilot wire installation, especially over inaccessible or sensitive areas.
-
-
Equipment: Our highest capacity pullers and tensioners with advanced control systems and data logging capabilities. Specialized stringing blocks designed for very long spans and high tensions. Heavy-duty anti-twisting swivels and pulling grips.
-
Our comprehensive product line offers a full range of OPGW stringing equipment, from standard units for typical spans to high-capacity, precision-controlled systems for the most challenging terrain and longest span installations. We partner with clients to provide the right tools and expertise for optimal stringing performance, regardless of geographical complexity.
OPGW cable stringing, typically conducted on overhead transmission lines, often takes place in diverse and sensitive environments. Environmental considerations are critical not only for regulatory compliance but also for minimizing ecological impact and ensuring community relations. Our approach encompasses best practices for mitigation.
I. Key Environmental Considerations:
-
1. Flora and Fauna Protection:
-
Consideration: Stringing operations can disturb vegetation, wildlife habitats, nesting birds, and sensitive ecosystems. Equipment movement, personnel activity, and potential OPGW sagging can impact these.
-
Mitigation:
-
Pre-Construction Surveys: Conduct environmental impact assessments to identify sensitive areas, protected species, and critical habitats.
-
Restricted Work Zones: Establish clear boundaries for work areas to minimize disturbance.
-
Timing: Schedule work outside of sensitive periods (e.g., bird nesting seasons, migration periods).
-
Erosion Control: Implement measures like silt fences and re-vegetation to prevent soil erosion, especially on slopes or near waterways.
-
Wildlife Exclusion: Where necessary, use temporary fencing to keep wildlife away from active work zones.
-
-
-
2. Soil Compaction and Disturbance:
-
Consideration: Heavy equipment (pullers, tensioners, reel trailers) can compact soil, damage root systems, and alter drainage patterns, leading to erosion or reduced soil fertility.
-
Mitigation:
-
Minimize Footprint: Plan equipment setup areas to reduce the overall disturbed footprint.
-
Matting: Use temporary access mats or specialized ground protection systems in sensitive or soft ground areas to distribute weight and reduce compaction.
-
Restoration: Re-contour and re-vegetate disturbed areas with native species post-installation.
-
-
-
3. Noise Pollution:
-
Consideration: Equipment noise (engines, generators, stringing operations) can disturb local communities, wildlife, and livestock, especially during extended operations or in quiet areas.
-
Mitigation:
-
Noise-Reducing Equipment: Utilize modern, quieter hydraulic pullers and tensioners.
-
Operating Hours: Restrict noisy operations to specific daytime hours in residential areas.
-
Distance: Position noisy equipment as far as practically possible from sensitive receptors.
-
-
-
4. Fuel and Chemical Spills:
-
Consideration: Spills of hydraulic fluid, diesel, or lubricants from equipment can contaminate soil and water, posing environmental and health risks.
-
Mitigation:
-
Maintenance: Ensure all equipment is well-maintained and free of leaks.
-
Spill Kits: Keep spill containment and cleanup kits readily available on site.
-
Refueling Protocols: Implement strict refueling procedures, including secondary containment, away from water bodies.
-
Proper Waste Disposal: Dispose of all waste materials (including used lubricants, filters, and debris) according to local regulations.
-
-
-
5. Visual Impact:
-
Consideration: While OPGW itself is integrated into existing infrastructure, the construction phase can have a temporary visual impact.
-
Mitigation:
-
Site Cleanliness: Maintain a tidy work site throughout the project.
-
Prompt Restoration: Rapid restoration of disturbed areas post-installation.
-
-
II. Our Company's Role in Mitigation:
-
Eco-Friendly Equipment: Our modern stringing equipment is designed with efficiency in mind, often featuring lower emissions and quieter operation compared to older models.
-
Comprehensive Project Planning Support: We can advise on equipment selection and methodologies that align with environmental best practices, including guidance on site access, equipment placement, and waste management.
-
Compliance Assistance: We emphasize the importance of adhering to local and international environmental regulations, and our equipment helps facilitate compliant operations.
By proactively addressing these environmental considerations and leveraging appropriate equipment and methodologies, OPGW stringing projects can minimize their ecological footprint while ensuring the reliable development of critical power and communication infrastructure.
Thorough planning is the bedrock of a successful and safe OPGW stringing operation. Given the dual nature of OPGW (electrical and optical) and the complexities of working on power lines, meticulous preparation is critical. Our comprehensive approach to OPGW stringing projects always begins with these essential planning steps:
-
1. Detailed Route Survey and Feasibility Study:
-
Purpose: To understand the specific terrain, identify existing infrastructure, potential obstacles, and environmental sensitivities along the entire transmission line route.
-
Activities: Topographical surveys (LiDAR, drone mapping), ground resistivity tests, identification of road/rail/river/power line crossings, and assessment of access roads for equipment.
-
Output: Comprehensive route maps, obstacle lists, and preliminary site assessments.
-
-
2. OPGW Cable Selection and Design Verification:
-
Purpose: To ensure the chosen OPGW cable is suitable for the specific electrical and mechanical requirements of the line (e.g., short-circuit current capacity, tensile strength, fiber count, diameter for existing towers) and meets environmental conditions.
-
Activities: Reviewing OPGW specifications (e.g., central tube vs. multi-loose tube design, short-circuit rating, tensile strength, fiber type), confirming compatibility with tower structures and existing hardware.
-
Output: Final OPGW cable specifications, sag-tension charts.
-
-
3. Stringing Method Selection and Span-by-Span Planning:
-
Purpose: To determine the most appropriate stringing method (e.g., tension stringing, conventional stringing with specific ground clearance requirements) for each section, considering terrain, span length, and existing line status (energized or de-energized).
-
Activities: Identifying puller and tensioner sites, intermediate setup points, anchor points, and planning for conductor drum locations. Detailed span-by-span sag and tension calculations.
-
Output: Stringing plan with equipment locations, sag charts, and tension limits per span.
-
-
4. Equipment Selection and Mobilization Plan:
-
Purpose: To select the correct type and capacity of OPGW stringing equipment and plan its transportation and setup.
-
Activities: Specifying hydraulic pullers and tensioners (matching capacity to line length/weight), OPGW-specific stringing blocks (correct diameter and lining), anti-twisting swivels, pulling grips, pilot ropes, and communication systems. Planning logistics for equipment delivery to remote sites.
-
Output: Equipment list, mobilization schedule, and site layout plans for puller/tensioner setups. Our one-stop supply capability ensures all necessary equipment is sourced efficiently.
-
-
5. Safety and Environmental Management Plan:
-
Purpose: To identify all potential hazards and develop robust mitigation strategies, ensuring the safety of personnel, public, and the environment.
-
Activities: Detailed Job Hazard Analysis (JHA), development of minimum approach distance (MAD) protocols, grounding and bonding plans, traffic management plans for crossings, emergency response procedures, and environmental protection measures (e.g., spill prevention, wildlife protection).
-
Output: Comprehensive Safety Plan, Environmental Management Plan, and permit acquisition.
-
-
6. Personnel Training and Certification:
-
Purpose: To ensure all personnel involved in the OPGW stringing operation are adequately trained, certified, and aware of specific procedures for OPGW handling and safety protocols.
-
Activities: Training on equipment operation, OPGW handling, splicing, safety procedures, and emergency response.
-
Output: Certified crew list and training records.
-
-
7. Communication Plan:
-
Purpose: To establish clear and reliable communication channels among all team members across the entire stringing section.
-
Activities: Determining communication methods (radios, headsets), establishing communication protocols, and ensuring signal coverage.
-
By meticulously executing these planning steps, particularly with the specialized requirements of OPGW in mind, we empower our clients to undertake stringing operations with maximum safety, efficiency, and adherence to project specifications.
While both scenarios involve stringing OPGW, installing on a brand-new transmission line and retrofitting an existing ground wire present distinct methodological differences, primarily due to the presence (or absence) of an existing energized power system and infrastructure.
I. Stringing OPGW on a Brand-New Transmission Line:
-
Context: This scenario involves stringing OPGW alongside new phase conductors on newly erected towers, where the line is not yet energized.
-
Methodology:
-
Conventional Tension Stringing: This is the most common method. After towers are erected, pilot ropes are strung (often by drone or manually), followed by pulling ropes, and then the OPGW. Phase conductors are typically strung either before or after the OPGW, depending on the sequence defined by the project.
-
No Live-Line Constraints: Since the line is de-energized, minimum approach distances (MAD) to existing energized conductors are not a concern (unless there are nearby existing active lines in the corridor). This simplifies safety protocols related to electrical hazards.
-
Clearer Right-of-Way: The right-of-way is usually clear of existing conductors, allowing for more straightforward equipment placement and less risk of accidental contact with other live components.
-
Parallel Stringing: Sometimes, multiple conductors and OPGW can be strung in parallel using specialized running boards and multiple pulling/tensioning machines, increasing efficiency.
-
-
Equipment Implications:
-
Our full range of hydraulic pullers and tensioners, conductor stringing blocks, reel stands, and pulling ropes are utilized. The equipment capacity is determined by the span lengths and OPGW weight/tension requirements.
-
II. Replacing an Existing Ground Wire with OPGW (Retrofit/Reconductoring):
-
Context: This involves removing an old, de-energized or, more commonly, energized overhead ground wire and replacing it with OPGW, often while the phase conductors below remain energized. This is a more complex and high-risk operation.
-
Methodology:
-
"Live-Line" or "Hot Stringing" Techniques (Most Common):
-
Carrier Method: A self-propelled carrier or robot travels along the existing ground wire, pulling a pilot rope and positioning specialized double pulleys. The old ground wire is then used as a pulling rope to pull in the new OPGW, simultaneously removing the old wire from the other end. This method significantly reduces outage requirements.
-
Direct Replacement Method: Involves pulling the new OPGW directly in place of the old ground wire, often using specialized clamps that grip both the old and new wires.
-
Insulated Tools and Equipment: All equipment and ropes must be designed for live-line work, featuring high dielectric strength and proper insulation.
-
Strict MAD Adherence: Maintaining minimum approach distances to the energized phase conductors below is absolutely critical. All personnel must be highly trained in live-line safety.
-
Temporary Grounding: Careful grounding and bonding procedures are implemented at each structure where work is being performed.
-
-
De-energized Replacement: If an outage is granted, the existing ground wire and potentially the phase conductors are de-energized and grounded. This simplifies safety, but outages are costly.
-
-
Equipment Implications:
-
Specialized "Live-Line" OPGW Stringing Equipment: This includes insulated puller-tensioners or standard units with strict grounding protocols, insulated stringing blocks, self-moving traction machines (robots) that travel on the existing ground wire, and insulated pulling ropes.
-
Anti-Twisting Devices: Even more critical to prevent torsional transfer during the simultaneous removal/installation process.
-
Enhanced Communication Systems: Robust, clear communication among all crews is paramount due to the higher risk.
-
Precision Control: Pullers and tensioners with advanced feedback and automatic control are vital to manage tensions within strict limits, especially when pulling against the resistance of the old wire.
-
Our company specializes in providing the full range of both conventional and advanced "live-line" OPGW stringing equipment and tools, enabling our clients to execute new line installations or complex retrofit projects safely and efficiently, regardless of whether the line is energized or de-energized.
OPGW stringing, while generally standardized, presents several common challenges that can impact project efficiency, safety, and the integrity of the cable. Our expertise and specialized equipment are designed to help overcome these hurdles:
-
1. Maintaining Correct Tension and Sag:
-
Challenge: OPGW must be strung within a very narrow tension window to prevent exceeding its Maximum Allowable Pulling Tension (MAPT) (which can damage optical fibers) or having insufficient tension (leading to excessive sag and potential ground contact). Factors like friction in stringing blocks, variations in terrain, and temperature changes can affect tension.
-
Overcoming:
-
Precision Hydraulic Pullers & Tensioners: Our equipment features closed-loop hydraulic systems with digital tension readout and automatic tension control, ensuring the set tension is maintained precisely throughout the pull.
-
Low-Friction Stringing Blocks: Use large-diameter, highly lubricated stringing blocks with non-abrasive liners to minimize friction.
-
Real-time Monitoring: Constant communication between puller/tensioner operators and tension monitoring at critical points, combined with real-time data logging, allows for immediate adjustments.
-
-
-
2. Preventing OPGW Twisting/Torsion:
-
Challenge: Twisting the OPGW can severely damage the internal optical fibers, especially in central-tube designs. This can occur due to puller/tensioner misalignment, rope lay, or unaddressed torsional forces during the pull.
-
Overcoming:
-
Anti-Twisting Swivels: Always employ high-quality, free-running anti-twisting swivels between the pulling grip and the pulling rope.
-
Non-Rotating Pulling Ropes: Use specifically designed non-rotating or low-rotation pulling ropes (e.g., braided synthetic or steel).
-
Proper Equipment Alignment: Ensure puller, tensioner, and first/last stringing blocks are perfectly aligned with the line angle.
-
-
-
3. Managing Clearances at Crossings (Roads, Railways, Power Lines):
-
Challenge: Ensuring safe clearances for OPGW over roads, railways, or other energized lines is critical to prevent accidents and property damage.
-
Overcoming:
-
Pre-Planning: Meticulous pre-stringing surveys and detailed crossing plans are essential.
-
Temporary Warning Structures: Install temporary warning structures, safety nets, or elevated gantries to ensure minimum clearances are maintained.
-
Traffic Management: Implement strict traffic control (flagmen, detours) at road/rail crossings.
-
Insulated Guards: Use insulated sleeves or guards over existing energized lines that are being crossed.
-
Communication: Maintain constant communication with crossing authorities and nearby utility operators.
-
-
-
4. Difficult Terrain and Access:
-
Challenge: Remote, hilly, swampy, or densely vegetated terrain can make equipment mobilization, setup, and cable handling extremely difficult.
-
Overcoming:
-
Specialized Access Equipment: Utilize tracked vehicles, all-terrain cranes, or even helicopters for pilot wire installation in inaccessible areas.
-
Modular/Compact Equipment: Deploy more compact and easily transportable stringing equipment where access is limited.
-
Intermediate Puller/Tensioner Setups: Break long spans into shorter, more manageable sections using intermediate pulling and tensioning points.
-
-
-
5. Damage to OPGW Outer Strands/Jacket:
-
Challenge: Abrasions, nicks, or crushing of the OPGW's outer metallic layers can compromise its long-term mechanical and electrical integrity, potentially exposing the optical fibers.
-
Overcoming:
-
Protective Stringing Blocks: Use only OPGW-specific stringing blocks with large, smooth, and properly lined sheaves.
-
Proper Handling: Avoid dragging the OPGW on the ground or against sharp objects. Use proper reel handling equipment.
-
Regular Equipment Inspection: Routinely inspect all stringing equipment (especially blocks and rollers) for wear, damage, or foreign material that could abrade the cable.
-
-
Our extensive range of OPGW stringing equipment, coupled with our deep industry knowledge and technical support, provides our clients with the tools and strategies needed to successfully navigate and overcome these common challenges, ensuring robust and reliable OPGW installations worldwide.
Weather conditions are critical variables in OPGW stringing, capable of significantly impacting safety, efficiency, and the final quality of the installation. Understanding and mitigating these impacts is essential.
I. Influence of Weather Conditions:
-
1. Wind:
-
Impact: High winds can cause uncontrolled swinging of the OPGW cable, making it difficult to control sag and tension. It increases the risk of the OPGW touching other conductors, ground, or obstacles. It also poses a safety hazard for personnel working at height.
-
Stringing Challenge: Makes it challenging to maintain accurate sag and can induce dynamic over-tensioning.
-
Precaution:
-
Wind Speed Limits: Establish strict maximum permissible wind speed limits for stringing operations (e.g., suspend operations if wind speeds exceed 25-30 km/h or as per local regulations/project specifications).
-
Wind Meters: Utilize wind speed monitoring devices at multiple points along the span.
-
Guying: Use temporary guys on towers to increase stability in windy conditions.
-
Slower Speeds: Reduce stringing speed during moderate winds.
-
-
-
2. Temperature:
-
Impact: Temperature directly affects the sag and tension of the OPGW cable. Cables contract in cold weather (increasing tension) and expand in hot weather (decreasing tension, increasing sag).
-
Stringing Challenge: Ensuring the final sag and tension match design specifications, especially when stringing occurs at temperatures different from the target sagging temperature.
-
Precaution:
-
Temperature Compensation: Sag charts provided by OPGW manufacturers will account for temperature variations. Stringing crews must use the appropriate sag values for the ambient temperature during the operation.
-
Real-time Sag Measurement: Use optical or laser sag measurement tools to verify sag in real-time.
-
Re-sagging: For critical installations, re-sagging may be required after the OPGW has acclimatized to the ambient temperature.
-
Material Handling: Extreme cold can make some materials (e.g., plastic linings in blocks) more brittle, while extreme heat can soften them.
-
-
-
3. Ice and Snow:
-
Impact: Ice and heavy snow loads can significantly increase the weight of the OPGW, causing excessive sag and stress on the cable and towers. Fresh snow can also make ground access extremely difficult.
-
Stringing Challenge: Impractical to string during active icing conditions. Existing ice on structures can pose a hazard.
-
Precaution:
-
Avoid Stringing: OPGW stringing should generally not be performed during periods of active ice or heavy snowfall.
-
Ice Removal: If ice has formed, it must be removed from towers and existing conductors before stringing, often requiring specialized de-icing procedures.
-
Access: Ensure heavy-duty vehicles or snowmobiles are available for access in snowy conditions.
-
-
-
4. Lightning and Thunderstorms:
-
Impact: A direct strike to exposed OPGW or towers during stringing can be catastrophic, posing extreme danger to personnel and equipment.
-
Stringing Challenge: Inherent electrical hazard.
-
Precaution:
-
Suspend Operations: Immediately suspend all operations and move personnel to safe shelters at the first sign of lightning or approaching thunderstorms.
-
Lightning Detection: Utilize lightning detection systems and weather forecasts.
-
Grounding: Ensure all equipment and OPGW are properly grounded at all times when not actively being pulled to provide a path for induced or stray currents.
-
-
-
5. Rain and Humidity:
-
Impact: Reduces visibility, makes ground conditions slippery, can lead to equipment malfunctions (if not weatherproofed), and affects the integrity of some materials.
-
Stringing Challenge: Reduced efficiency and increased safety risks.
-
Precaution:
-
Waterproof Gear: Provide appropriate rain gear for personnel.
-
Weatherproof Equipment: Ensure stringing equipment is weatherproof or protected.
-
Mud Management: Use ground mats or gravel in wet, muddy areas for equipment access.
-
-
Our robust OPGW stringing equipment is designed to operate reliably in a wide range of environmental conditions, and we strongly advocate for rigorous weather monitoring and adherence to safety protocols to ensure the successful and safe completion of every project.
ADSS (All-Dielectric Self-Supporting) cable has become the preferred choice for aerial fiber optic network deployment on utility poles and transmission towers due to its unique design and numerous advantages that address the specific challenges of overhead installations.
I. Core Advantages:
-
1. All-Dielectric (Non-Metallic) Construction:
-
Benefit: Being entirely non-metallic, ADSS cable is immune to electromagnetic interference (EMI) from high-voltage power lines and lightning strikes. This ensures signal integrity and eliminates the need for grounding.
-
Implication: Safely installable in close proximity to energized power conductors without concerns about induced currents or short circuits, which is critical for utility corridors.
-
-
2. Self-Supporting Design:
-
Benefit: ADSS cable incorporates its own strength members (typically aramid yarns or fiberglass rods) within its structure, allowing it to support its own weight and withstand environmental loads (wind, ice) over long spans without the need for a separate messenger wire or support strand.
-
Implication: Simplifies installation, reduces material costs, and minimizes pole loading compared to lashed or figure-8 cables.
-
-
3. Single-Pass Installation:
-
Benefit: Due to its self-supporting nature, ADSS cable can often be installed in a single pass using tension stringing methods, reducing labor time and equipment usage.
-
Implication: Faster deployment and lower installation costs compared to traditional lashed aerial cables. Our OHTL stringing equipment is perfectly suited for this.
-
-
4. High Tensile Strength and Durability:
-
Benefit: Designed to withstand the harsh outdoor environment, including high wind loads, ice accumulation, and extreme temperatures, while maintaining optical performance. Its robust outer jacket provides UV and track resistance.
-
Implication: Ensures long-term reliability and minimizes maintenance requirements, even in severe weather conditions.
-
-
5. Flexibility in Mounting Location:
-
Benefit: Can be mounted on existing or new utility poles, eliminating the need for new rights-of-way. Can be attached to the top of the pole, cross-arms, or even within the power space, provided sufficient clearances and electrical field considerations are met.
-
Implication: Offers significant cost savings and faster deployment by leveraging existing infrastructure.
-
-
6. Diverse Span Lengths:
-
Benefit: Available in various designs tailored for short, medium, and long spans (up to several kilometers), allowing for optimal selection based on the specific power line structure and environmental loading.
-
-
7. High Fiber Counts:
-
Benefit: Can accommodate a very high number of optical fibers within a relatively small diameter, providing ample bandwidth capacity for current and future communication needs.
-
Implication: Future-proofs the network for evolving data demands (e.g., 5G backhaul, smart grid communication, IoT).
-
In summary, ADSS cable is a highly efficient, robust, and cost-effective solution for deploying fiber optic networks in overhead environments, particularly in utility corridors. Our company provides the specialized tension stringing equipment and tools essential for the safe and efficient installation of ADSS cables, enabling our clients to fully leverage these powerful advantages.
The unique all-dielectric and self-supporting nature of ADSS (All-Dielectric Self-Supporting) cables necessitates specialized stringing equipment designed to protect the cable's optical fibers and maintain its integrity throughout the installation process. Our comprehensive one-stop supply includes all essential equipment for ADSS installation:
I. Core Tension Stringing Equipment:
-
1. Hydraulic Pullers:
-
Function: Provide the controlled pulling force to string the ADSS cable from the reel through the stringing blocks.
-
Key Features: Must have precise digital tension control systems with a dynamometer to ensure the cable's Maximum Allowable Pulling Tension (MAPT) is never exceeded. They should also feature smooth-grooved bullwheels (often lined with durable, non-abrasive material) to prevent damage to the ADSS cable jacket.
-
Our Offering: Our range of hydraulic pullers offers the necessary power and precision for various ADSS cable sizes and span lengths, ensuring consistent tension control.
-
-
2. Hydraulic Tensioners:
-
Function: Apply continuous back tension to the ADSS cable as it's being paid out, preventing it from touching the ground, sagging excessively, or running uncontrolled.
-
Key Features: Similar to pullers, they require precise tension control and smooth, protective bullwheel linings.
-
Our Offering: Our tensioners work in perfect synchronization with our pullers to maintain optimal tension throughout the entire stringing operation, crucial for ADSS.
-
-
3. Puller-Tensioner Machines:
-
Function: Combined units that offer both pulling and tensioning capabilities from a single machine, providing operational flexibility and efficiency, particularly for complex or urban installations.
-
II. Specialized ADSS-Specific Accessories:
-
1. ADSS Stringing Blocks (Pulleys):
-
Function: Guide the ADSS cable along the span and around tower structures without exceeding its minimum bending radius or causing jacket damage.
-
Key Features: Absolutely critical. They must have large diameter sheaves (typically much larger than for conventional conductors, often 20-30 times the ADSS cable diameter) to prevent optical fiber stress. The grooves must be wide, smooth, and lined with highly protective, non-abrasive materials (e.g., polyurethane, neoprene) to prevent crushing, abrasion, or nicks to the all-dielectric jacket.
-
Our Offering: We provide a variety of ADSS-specific stringing blocks, meticulously designed for various cable diameters and span lengths, ensuring complete cable protection.
-
-
2. Non-Rotating Pulling Ropes:
-
Function: Essential for ADSS. These ropes (e.g., high-strength synthetic or braided steel) prevent torque from being transferred to the ADSS cable, which could induce twist and damage the internal fibers.
-
-
3. Anti-Twisting Devices (Swivels):
-
Function: Heavy-duty, ball-bearing swivels inserted between the pulling grip and the pulling rope to absorb any torsional forces, preventing the ADSS cable from twisting as it is pulled.
-
-
4. ADSS Pulling Grips (Stockings/Socks):
-
Function: Specifically designed to distribute the pulling force uniformly over a larger surface area of the ADSS cable, minimizing stress concentration on the jacket and internal strength members. They typically have a long, flexible, and often double-layered mesh design.
-
-
5. Cable Reel Stands/Trailers:
-
Function: Robust, high-capacity stands capable of safely unwinding large and heavy ADSS reels while maintaining controlled back tension.
-
-
6. Down-lead Clamps and Suspension/Dead-End Hardware:
-
Function: Specialized hardware used to secure the ADSS cable to the pole/tower, guide it down to splice points, and terminate it at dead-end structures. This hardware is often preformed or designed with elastomeric inserts to avoid crushing the ADSS jacket.
-
Our Offering: We supply a full range of compatible ADSS hardware to complement our stringing equipment.
-
III. Safety and Support Equipment:
-
1. Communication Systems: Reliable two-way communication (radios, headsets) between puller/tensioner operators and tower crews is paramount.
-
2. Sagging Tools: Optical or laser sagging tools for accurate sag measurement and adjustment.
-
3. Safety Gear: Standard fall protection, insulated gloves (if working near energized lines), and general PPE.
By providing this full spectrum of specialized ADSS installation tools and equipment, we ensure that our clients can achieve safe, efficient, and damage-free deployments of their aerial fiber optic networks worldwide.
Selecting the optimal suspension and dead-end hardware for ADSS (All-Dielectric Self-Supporting) cables is paramount for ensuring the long-term mechanical integrity, optical performance, and longevity of the fiber optic network. Unlike metallic conductors, ADSS requires hardware that never compromises its all-dielectric structure or compresses its optical fibers.
I. Critical Considerations for Hardware Selection:
-
1. Cable Diameter and Sag-Tension Data:
-
Consideration: Hardware must be precisely matched to the ADSS cable's exact outer diameter (OD) and the calculated sag and tension values for the specific span and environmental loading (wind, ice, temperature).
-
Implication: Mismatched hardware can lead to crushing, slippage, or localized stress, resulting in fiber attenuation or sheath damage.
-
-
2. Protection of the Cable Jacket (Outer Sheath):
-
Consideration: The outer jacket of ADSS cable is crucial for UV, tracking, and environmental protection. Hardware must not abrade, nick, or deform this jacket.
-
Solution: All contact surfaces of the hardware with the ADSS cable must be smooth, wide, and preferably lined with elastomeric (rubber or polymer) inserts. Preformed helical rods are designed to distribute gripping pressure over a long length.
-
-
3. Prevention of Concentrated Stress:
-
Consideration: ADSS cables are designed to withstand distributed loads. Concentrated stress points (e.g., from sharp edges, overtightened clamps, or improper bending) can lead to micro-bends in the fibers, causing signal loss, or eventually mechanical failure.
-
Solution: Suspension clamps for tangent poles must cradle the cable gently, allowing for free movement. Dead-end clamps must distribute the tensile load uniformly along the cable's strength members, not the jacket or fiber unit.
-
-
4. Minimum Bending Radius (Static):
-
Consideration: Every ADSS cable has a specified static minimum bending radius (MBR). Hardware components, especially those used for down-leads or at termination points, must ensure the cable is never bent below this radius.
-
Solution: Down-lead clamps and cable guides should have gentle curves and large radii to prevent sharp bends.
-
-
5. Aeolian Vibration Damping:
-
Consideration: ADSS cables are susceptible to Aeolian vibration (wind-induced oscillation), which can cause fatigue damage at support points.
-
Solution: For spans susceptible to vibration (typically longer spans, open terrain), vibration dampers (e.g., Stockbridge dampers or spiral vibration dampers) must be installed. Suspension clamps that incorporate damping features are also available.
-
-
6. Electrical Field Considerations (Tracking Resistance):
-
Consideration: For ADSS cables installed in the high electric field regions of power towers (especially > 35-60kV), the hardware, particularly the suspension points, must be designed to mitigate dry-band arcing and electrical tracking on the cable surface.
-
Solution: Selection of ADSS cables with "AT" (Anti-Tracking) jackets is essential for high-voltage applications. Hardware design should also minimize electrical field distortion at the attachment point, and sometimes external corona rings or grading rings are used on the cable itself at the hardware interface.
-
-
7. Material Compatibility and Corrosion Resistance:
-
Consideration: Hardware materials must be durable, UV-resistant, and corrosion-resistant, matching the expected lifespan of the ADSS cable in the specific environment (e.g., coastal areas).
-
Solution: Use of galvanized steel, aluminum alloys, or high-strength, UV-stabilized polymers.
-
-
8. Installation Ease and Reusability (for temporary hardware):
-
Consideration: While for permanent hardware, ease of installation and durability are key. For temporary stringing hardware, reusability and quick installation/removal are important.
-
Solution: Hardware designs that are intuitive to install and do not require specialized crimping or extensive tooling.
-
II. Types of ADSS Hardware:
-
Suspension Clamps: Used at tangent (straight) poles, typically incorporating elastomeric inserts or preformed helical rods to gently support the cable.
-
Dead-End (Tension) Clamps: Used at termination poles, large angle towers, or section breaks. These are designed to grip the strength members (aramid) of the cable without crushing the optical unit. Preformed helical dead-ends are very common.
-
Down-Lead Clamps: Guide the ADSS cable safely down the pole from the suspension point to a splice enclosure or ground entry.
-
Vibration Dampers: Attached to the cable near the suspension points to dissipate Aeolian vibration energy.
Our company provides a full array of high-quality, manufacturer-recommended ADSS suspension, dead-end, and ancillary hardware, all designed and tested to meet stringent performance requirements and ensure the long-term reliability of your ADSS fiber optic network. We can assist in selecting the optimal hardware for your specific ADSS cable and project conditions.
After ADSS (All-Dielectric Self-Supporting) cable installation, comprehensive testing and commissioning are crucial steps to verify the optical performance of the fiber network and the mechanical integrity of the cable and its hardware. This ensures the system is ready for reliable long-term operation.
I. Optical Testing and Commissioning (Fiber Optic Performance):
-
1. Optical Time Domain Reflectometer (OTDR) Testing:
-
Purpose: The most critical optical test. An OTDR acts like a "radar" for fiber, sending light pulses down the fiber and analyzing the reflected light to measure:
-
Total Fiber Length: Verifies the installed length.
-
Optical Loss: Identifies and quantifies loss at splices, connectors, and along the cable itself.
-
Event Location: Pinpoints the exact location of splices, connectors, and any anomalies (e.g., micro-bends, macro-bends, breaks, poor connections).
-
Reflectance: Measures reflections from connectors or faults.
-
-
Procedure: Performed bi-directionally (from both ends) for each individual fiber in the ADSS cable, at multiple wavelengths (typically 1310 nm and 1550 nm for single-mode fiber). Results are documented as "as-built" records.
-
-
2. Optical Power Meter (OPM) and Light Source Testing (Insertion Loss Testing):
-
Purpose: To measure the total end-to-end attenuation (loss) of each fiber link, including all splices and connectors. This confirms the link meets the design's optical loss budget.
-
Procedure: A calibrated light source injects light at one end, and an OPM measures the received power at the other end. Loss is calculated in dB. Performed bi-directionally for each fiber.
-
-
3. Visual Fault Locator (VFL):
-
Purpose: A simple, red laser light tool for quick continuity checks and identifying macro-bends, breaks, or poor connections in short distances where the red light might escape the fiber jacket.
-
Procedure: Light leakage indicates a problem. Useful for troubleshooting and verifying patch cord connections.
-
-
4. Fiber End-Face Inspection:
-
Purpose: To ensure that fiber optic connector end-faces (where ADSS is terminated into patch panels) are clean and free from scratches, dust, or defects, which can cause significant optical loss and reflectance.
-
Procedure: Using a fiber inspection microscope or probe. Cleaning is performed if necessary.
-
-
5. Chromatic Dispersion (CD) and Polarization Mode Dispersion (PMD) Testing:
-
Purpose: For very high-speed (e.g., 10 Gbps and above) and long-haul ADSS networks, these tests measure signal distortion that can limit bandwidth and reach.
-
Procedure: Specialized equipment measures dispersion characteristics.
-
II. Mechanical and Visual Inspection (Cable and Hardware Integrity):
-
1. Visual Inspection:
-
Purpose: A thorough visual check of the entire ADSS installation to identify any visible mechanical damage to the cable jacket, proper seating of suspension and dead-end hardware, correct sag, and proper down-lead routing.
-
Procedure: Conducted from the ground, binoculars, drones, or bucket trucks. Look for jacket nicks, tight bends, loose hardware, or signs of stress.
-
-
2. Sag and Tension Verification:
-
Purpose: To confirm that the ADSS cable has been sagged to the correct values specified in the design for the given ambient temperature, ensuring it meets clearance requirements and is not over-tensioned.
-
Procedure: Using optical or laser sagging tools, measure sag in representative spans and compare against the sag chart.
-
-
3. Hardware Inspection:
-
Purpose: To ensure all ADSS suspension, dead-end, and down-lead hardware is correctly installed, tightened to specifications (if applicable), and providing proper support and protection to the cable jacket.
-
Procedure: Close-up visual inspection from bucket trucks or by climbing crews.
-
III. Documentation and Reporting:
-
All test results (optical and mechanical observations) are meticulously documented, compared against design specifications, and retained as critical "as-built" records. This data is invaluable for future maintenance, troubleshooting, and overall network management. A comprehensive commissioning report is typically submitted to the client.
Our company not only provides the robust ADSS installation equipment but also supports our clients with essential testing solutions and expertise, including advanced fiber optic test equipment and guidance on best practices for mechanical verification, ensuring that every ADSS installation meets the highest standards of performance and longevity.
The landscape of aerial fiber optic networks is constantly evolving, with ADSS (All-Dielectric Self-Supporting) cable technology and installation methods at the forefront of innovation. These advancements are driven by the demand for higher bandwidth, increased network resilience, and more cost-effective deployments.
I. Latest Trends in ADSS Cable Technology:
-
1. Ultra-High Fiber Counts:
-
Trend: While standard ADSS often has 24-96 fibers, there's a growing demand for ultra-high fiber count ADSS, reaching 144, 288, 432, or even 864+ fibers within a single cable.
-
Implication: This caters to the explosive growth in data traffic, 5G backhaul requirements, and the need for ample dark fiber capacity for future expansion or wholesale opportunities.
-
-
2. Mini-Span and Micro-ADSS Cables:
-
Trend: Development of smaller diameter, lighter ADSS cables optimized for very short spans (e.g., street lights, distribution poles, FTTH last-mile drops).
-
Implication: Easier handling, lower visual impact, and reduced pole loading for granular network deployments.
-
-
3. Advanced Jacket Materials (Enhanced Tracking Resistance & Durability):
-
Trend: Continuous improvement in outer jacket materials, particularly for "AT" (Anti-Tracking) jackets. These new formulations offer superior resistance to dry-band arcing and electrical tracking, even in extremely high electrical fields, and enhanced UV and abrasion resistance.
-
Implication: Increased reliability and longer service life for ADSS cables installed on high-voltage transmission lines.
-
-
4. Compact and High-Density Fiber Units:
-
Trend: Innovations in fiber optic subunit designs (e.g., micro-modules, ribbon fibers, SpiderWeb Ribbon®) allow for packing more fibers into smaller diameter loose tubes or within the overall cable, contributing to higher fiber counts in compact ADSS designs.
-
Implication: Reduces cable weight and diameter without sacrificing fiber count, making stringing easier and reducing material costs.
-
-
5. Integrated Functionality:
-
Trend: While still niche, there's exploration into ADSS cables that integrate other functionalities, such as distributed acoustic sensing (DAS) or temperature sensing fibers, for smart grid monitoring.
-
II. Innovations in ADSS Installation Methods and Equipment:
-
1. Advanced Tension Stringing Machines with Data Logging:
-
Innovation: Our latest hydraulic pullers and tensioners feature integrated digital load cells, GPS, and onboard computers that provide real-time tension, speed, distance, and even weather data. This data is logged and can be wirelessly transmitted to a central control point or cloud platform.
-
Implication: Unprecedented precision in maintaining the ADSS cable's MAPT, real-time quality control, verifiable "as-built" records, and enhanced safety by preventing over-tensioning.
-
-
2. Drone-Assisted Pilot Rope Installation:
-
Innovation: Drones are increasingly used to efficiently and safely install pilot ropes over long spans, challenging terrain, or across obstacles (e.g., rivers, congested areas), significantly reducing the need for manual methods or helicopters.
-
Implication: Faster setup times, improved safety for crews, and reduced environmental impact.
-
-
3. Optimized Stringing Blocks and Hardware:
-
Innovation: Development of lighter, stronger composite materials for stringing blocks, with improved bearing systems and highly protective, low-friction linings (e.g., advanced polymers, specialized elastomers) that minimize stress on the ADSS jacket and fibers.
-
Implication: Further protection against cable damage during installation, smoother pulls, and extended equipment lifespan.
-
-
4. Automated Sagging and Monitoring Tools:
-
Innovation: Laser-based or optical sagging tools that provide highly accurate, real-time sag measurements, sometimes integrated with tensioning equipment to fine-tune final sag.
-
Implication: Ensures precise adherence to design specifications, critical for maintaining required clearances.
-
-
5. Streamlined Splicing and Termination Solutions:
-
Innovation: Faster fusion splicers with automated features, user-friendly fiber preparation tools, and compact, robust splice enclosures specifically designed for aerial environments. Pre-terminated ADSS solutions are also emerging for certain applications.
-
Implication: Quicker and more reliable fiber optic connections, reducing installation time and potential for errors.
-
These trends and innovations highlight a future where ADSS installation is even more efficient, reliable, and capable of supporting the most demanding communication needs of power grids and beyond. Our company is at the forefront of providing the cutting-edge ADSS installation equipment and tools that drive these advancements, ensuring our global clients can build robust and future-proof aerial fiber networks.
Electrical installations are inherently dangerous if not performed correctly, making adherence to strict safety standards and regulations paramount worldwide. While specific codes vary by region, they all share common goals: preventing electric shock, fire, electrocution, and explosions, and ensuring the long-term reliability of electrical systems.
I. Key Global & Regional Standards:
-
1. International Electrotechnical Commission (IEC) Standards (IEC 60364 series):
-
Reach: Widely adopted or serve as the basis for national standards in Europe, Asia, Africa, and many other parts of the world.
-
Focus: Covers fundamental principles of safety, protection for safety, common rules for design, selection and erection of electrical equipment, inspection, and testing. It's a comprehensive framework for low-voltage electrical installations.
-
How they ensure safety: They dictate requirements for earthing (grounding) and bonding, overcurrent protection (circuit breakers, fuses), isolation and switching devices, protection against electric shock (e.g., RCDs/GFCIs), cable selection, and proper installation techniques to prevent overheating and short circuits.
-
-
2. National Electrical Code (NEC) / NFPA 70 (United States):
-
Reach: Enforced in all 50 U.S. states and often referenced in other countries.
-
Focus: A benchmark for safe electrical design, installation, and inspection, protecting people and property from electrical hazards. It's updated every three years to incorporate new technologies and safety practices.
-
How it ensures safety: Mandates specific wiring methods, conductor sizing, overcurrent protection, grounding, bonding, and requirements for arc-fault circuit interrupters (AFCIs) and ground-fault circuit interrupters (GFCIs) in specific locations (e.g., bathrooms, kitchens, outdoors) to prevent shock and fire.
-
-
3. BS 7671 (IET Wiring Regulations) (United Kingdom):
-
Reach: Governs electrical installations in the UK and influences standards in some Commonwealth countries.
-
Focus: Sets out requirements for the design, erection, and verification of electrical installations.
-
How it ensures safety: Includes detailed provisions for earthing and bonding, automatic disconnection of supply, protection against overcurrents, surge protection, and specific requirements for special installations or locations (e.g., bathrooms, construction sites).
-
-
4. Occupational Safety and Health Administration (OSHA) Standards (United States):
-
Reach: Federal regulations in the US, particularly for workplaces.
-
Focus: Specifies requirements for electrical safety in the workplace, focusing on preventing injuries from electrical hazards.
-
How it ensures safety: Covers topics like lockout/tagout procedures, personal protective equipment (PPE) for electrical work, safe work practices around live parts, and requirements for guarding electrical equipment. Similar occupational health and safety bodies exist globally.
-
II. Universal Principles for Ensuring Safety:
Beyond specific codes, fundamental principles underpin safe electrical installation:
-
Competent Personnel: All electrical work must be performed by qualified, trained, and competent electricians and technicians who understand the risks and safety procedures.
-
De-energization & Lockout/Tagout (LOTO): The safest practice is to de-energize circuits and apply LOTO procedures before working on electrical systems.
-
Grounding and Bonding: Essential for creating a safe path for fault currents, preventing dangerous voltage differences, and protecting against shock.
-
Overcurrent Protection: Circuit breakers and fuses are vital to protect circuits from overload and short circuits, preventing fires and equipment damage.
-
Protection Against Electric Shock: RCDs/GFCIs rapidly detect imbalances in current (leakage to ground) and trip circuits, preventing severe electric shock.
-
Proper Insulation and Enclosure: Conductors must be adequately insulated, and live parts must be enclosed to prevent accidental contact.
-
Minimum Clearances: Maintaining specified distances from live parts, particularly overhead lines, is crucial for preventing arc flashes and contact.
-
Personal Protective Equipment (PPE): Appropriate PPE (e.g., insulated gloves, arc-rated clothing, safety glasses) must be worn by workers exposed to electrical hazards.
-
Regular Inspection and Maintenance: Electrical systems must be periodically inspected and maintained to identify and rectify potential hazards before they escalate.
Our company, as a manufacturer of specialized tools and equipment for electrical construction, is committed to producing products that not only meet but exceed these international safety standards, ensuring that our clients can perform their electrical installations safely and efficiently. We also advocate for continuous training and adherence to all applicable local and international codes.
Smart technology and the Internet of Things (IoT) are fundamentally revolutionizing electrical installations across all sectors, moving beyond simple automation to create intelligent, energy-efficient, and highly responsive environments. This transformation impacts design, functionality, and operational efficiency.
I. Impact on Residential Electrical Installations:
-
1. Smart Panels and Circuit Breakers:
-
Transformation: Traditional electrical panels are being replaced by "smart panels" with integrated connectivity. Smart circuit breakers (e.g., with Wi-Fi) allow homeowners to monitor energy consumption at the circuit level, receive alerts for abnormal usage, and remotely control or reset individual circuits via a smartphone app. Some can even identify malfunctioning appliances.
-
Benefit: Enhanced energy monitoring, fault detection, predictive maintenance, and greater control over home energy usage.
-
-
2. Integrated Home Automation and Energy Management Systems (HEMS):
-
Transformation: Electrical installations are designed with a central hub that integrates smart lighting, thermostats, smart appliances, EV chargers, and renewable energy sources (solar, battery storage).
-
Benefit: Optimized energy consumption, automated climate control, personalized lighting scenes, and seamless management of diverse smart devices.
-
-
3. Wireless Lighting Systems and Controls:
-
Transformation: Wireless switches, dimmers, and smart bulbs connect via protocols like Wi-Fi, Bluetooth, Zigbee, or Matter, reducing the need for extensive traditional wiring runs for control circuits.
-
Benefit: Greater flexibility in lighting design, easy retrofitting, energy savings through occupancy sensors and daylight harvesting, and voice control.
-
-
4. EV Charger Integration:
-
Transformation: Home electrical systems are being upgraded to accommodate dedicated circuits and smart EV charging stations that can monitor usage, schedule charging during off-peak hours, and even integrate with solar power.
-
Benefit: Convenient and cost-effective charging, optimized energy use, and support for the growing EV market.
-
II. Impact on Commercial and Industrial Electrical Installations:
-
1. AI-Driven Energy Management Systems (EMS):
-
Transformation: Large-scale installations incorporate AI-powered EMS that learn building occupancy patterns, optimize HVAC and lighting based on real-time data, and predict energy demand.
-
Benefit: Significant energy cost savings, reduced carbon footprint, demand-side management, and improved operational efficiency.
-
-
2. Smart Building Management Systems (BMS):
-
Transformation: Electrical infrastructure is integrated into a unified BMS that controls not only power distribution but also security, fire alarms, access control, and environmental systems.
-
Benefit: Centralized control, proactive fault detection, predictive maintenance for critical electrical components, and enhanced occupant comfort and safety.
-
-
3. Predictive Maintenance for Electrical Assets:
-
Transformation: IoT sensors are deployed on motors, transformers, switchgear, and even power lines (e.g., through OPGW/ADSS monitoring systems). These sensors continuously monitor temperature, vibration, current, and voltage.
-
Benefit: Enables early detection of anomalies, preventing costly equipment failures, reducing downtime, and extending asset lifespan. Our tools for electrical maintenance are vital here.
-
-
4. Decentralized Energy Resources (DER) Integration:
-
Transformation: Commercial and industrial sites are integrating solar panels, wind turbines, battery energy storage systems (BESS), and sometimes microgrids directly into their electrical infrastructure. Smart inverters and control systems manage energy flow between DERs, the grid, and local loads.
-
Benefit: Increased energy independence, resilience against grid outages, reduced energy costs, and enhanced sustainability.
-
-
5. Data Centers and Critical Infrastructure:
-
Transformation: Electrical installations in data centers rely heavily on smart power distribution units (PDUs), uninterruptible power supplies (UPS) with IoT monitoring, and advanced cooling systems for maximum uptime and energy efficiency.
-
Benefit: Real-time visibility into power consumption, improved redundancy, and optimization of power usage effectiveness (PUE).
-
III. Implications for Electrical Contractors and Equipment Manufacturers:
-
Increased Demand for Skilled Labor: Need for electricians with specialized knowledge in networking, IT, and software integration.
-
Emphasis on Interoperability: Solutions must be compatible across various platforms and devices (e.g., Matter standard).
-
Shift to Data-Driven Design: Electrical designs increasingly consider data flow, sensor placement, and communication protocols.
-
New Tools and Testing Equipment: Requirements for specialized diagnostic tools, network testers, and software for commissioning and troubleshooting smart systems.
As a manufacturer and exporter of electrical construction and maintenance equipment, our company recognizes these trends. We are continually developing and supplying tools that support the installation, upgrade, and maintenance of smart electrical systems, from advanced power line equipment for grid modernization to precise tools for panel upgrades and EV charging infrastructure.