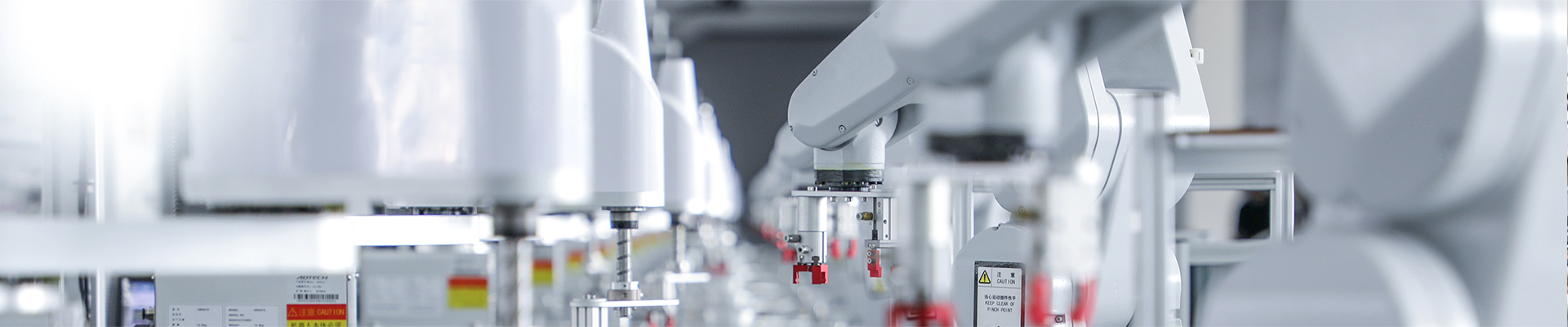
FAQ
The choice between overhead and underground power distribution lines involves a complex trade-off between cost, reliability, safety, and aesthetics. Each method has distinct advantages and disadvantages, making them suitable for different applications and environments. Our company provides both overhead transmission line (OHTL) wire cable conductor tension stringing equipment and underground cable laying equipment to cater to these diverse needs.
I. Overhead Power Distribution Lines:
-
Advantages:
-
Lower Installation Cost: Generally 5 to 10 times cheaper to install than underground lines due to simpler construction methods, less excavation, and less specialized materials.
-
Easier Fault Location and Repair: Faults are often visible (e.g., broken wires, damaged poles) and easier to pinpoint, leading to quicker repair times and lower maintenance costs.
-
Easier Capacity Upgrades: Adding or upgrading conductors is relatively straightforward.
-
Efficient Heat Dissipation: Air cooling allows conductors to dissipate heat effectively, providing higher current carrying capacity (ampacity) for a given conductor size.
-
Flexible Routing: Can be routed over various terrains with fewer physical obstacles.
-
-
Disadvantages:
-
Vulnerability to Weather: Highly susceptible to damage from severe weather (wind, ice storms, lightning), falling trees, and strong winds, leading to more frequent and prolonged outages.
-
Aesthetic Impact: Visually intrusive, impacting scenic views and property values, especially in residential or urban areas.
-
Lower Public Safety: Exposed conductors pose risks of electrocution, accidental contact, and vehicle collisions with poles.
-
Maintenance: Requires regular tree trimming, pole inspections, and vulnerability to vehicle impacts.
-
Environmental Impact: Can lead to more extensive tree clearing in forested areas and pose risks to wildlife (e.g., bird collisions).
-
II. Underground Power Distribution Lines:
-
Advantages:
-
Enhanced Reliability: Much less susceptible to weather-related outages (wind, ice, lightning, falling trees) and vehicular accidents, leading to fewer and shorter outages.
-
Improved Aesthetics: Eliminates visual clutter, preserving natural landscapes and enhancing urban environments and property values.
-
Increased Public Safety: Removes exposed energized conductors, significantly reducing risks of accidental contact, electrocution, and fire.
-
Reduced Long-Term Maintenance: Once installed, requires less routine maintenance (e.g., no tree trimming, fewer visual inspections for pole damage).
-
Security: Less vulnerable to physical tampering or sabotage.
-
Reduced Noise: Eliminates audible noise from corona discharge common in overhead lines.
-
-
Disadvantages:
-
Higher Installation Cost: Substantially more expensive due to extensive excavation (trenching, boring), specialized insulated cables, conduits, and complex splicing/termination requirements. Our underground cable laying equipment aims to optimize this process.
-
Difficult Fault Location and Repair: Locating faults (e.g., insulation breakdown, dig-ins) is complex, time-consuming, and expensive, requiring specialized equipment (e.g., thumper/TDR). Repair times are typically longer.
-
Heat Dissipation Challenges: Heat generated by current flow is harder to dissipate underground, potentially limiting current-carrying capacity or requiring larger, more expensive cables.
-
Environmental Impact of Trenching: Can cause significant disruption to soil, vegetation, and existing underground utilities during installation.
-
Vulnerability to "Dig-Ins": Susceptible to damage from third-party excavation if not properly marked or located.
-
Moisture Ingress: Vulnerable to insulation failure if moisture penetrates the cable system (splices, terminations) over time.
-
III. When Each is Preferred:
-
Overhead is Preferred for:
-
Rural and suburban areas where cost is a primary concern and visual impact is less critical.
-
Areas with challenging terrain where excavation is difficult or impossible.
-
Situations requiring quick deployment and easy access for maintenance and expansion.
-
-
Underground is Preferred for:
-
Dense urban and metropolitan areas where aesthetics and space are paramount.
-
Environments prone to severe weather events (e.g., hurricanes, ice storms) to enhance resilience.
-
Locations with high public safety concerns (e.g., near schools, parks).
-
New residential and commercial developments where integrated aesthetics are a key selling point.
-
Connections to critical infrastructure where maximum reliability is required.
-
Our company offers comprehensive solutions for both approaches. Our OHTL wire cable conductor tension stringing equipment supports efficient and safe overhead line construction, while our advanced underground cable laying equipment provides the specialized tools necessary for complex and reliable underground installations, enabling utilities to choose the optimal solution for their specific distribution needs.
Maintaining aging power distribution infrastructure is one of the most significant challenges facing utilities globally. Decades of service have led to an increased risk of failures, higher operational costs, and reduced reliability. Addressing this requires a strategic shift towards proactive maintenance and grid modernization.
I. Major Challenges with Aging Infrastructure:
-
1. Increased Failure Rates: Older equipment (transformers, circuit breakers, insulators, conductors, poles) is more prone to breakdown, leading to more frequent and longer power outages.
-
2. Higher Maintenance Costs: Reactive "fix-on-fail" maintenance becomes more common, which is typically more expensive and disruptive than planned maintenance. Repairing obsolete equipment can also be challenging due to parts availability.
-
3. Reduced Efficiency: Older equipment may not be as energy-efficient, leading to higher technical losses and increased operational expenditures.
-
4. Safety Risks: Deteriorating equipment can pose increased safety hazards for utility workers and the public (e.g., falling poles, exposed conductors, arc flash incidents).
-
5. Limited Capacity: Older infrastructure may not have the capacity to handle increasing load demands, the integration of distributed energy resources (DERs), or the surge from electric vehicles.
-
6. Workforce Skill Gap: A significant portion of the experienced utility workforce is retiring, leading to a knowledge gap in maintaining legacy systems.
II. Best Practices for Extending Asset Life and Ensuring Reliability:
-
1. Shift from Reactive to Predictive/Condition-Based Maintenance (CBM):
-
Practice: Instead of waiting for equipment to fail, utilities are deploying sensors and data analytics to monitor asset health in real-time. This includes thermal imaging for hot spots, partial discharge testing for insulation integrity, and vibration analysis for rotating equipment.
-
Benefit: Allows for proactive intervention, replacing or repairing components before they fail, minimizing unplanned outages, and optimizing maintenance schedules. Our substation maintenance tools are crucial for these advanced diagnostic procedures.
-
-
2. Comprehensive Asset Management Systems:
-
Practice: Implementing robust software systems to track the age, condition, maintenance history, and performance of every asset in the distribution network.
-
Benefit: Enables informed capital planning, helps prioritize investments, and facilitates optimal asset replacement strategies.
-
-
3. Regular Inspections and Preventative Maintenance (PM):
-
Practice: Scheduled visual inspections, cleaning, lubrication, and minor adjustments of equipment (e.g., tightening connections on overhead lines).
-
Benefit: Catches minor issues early, prevents wear and tear, and maintains equipment in optimal operating condition. Our electrical construction and maintenance tools support these routine inspections.
-
-
4. Strategic Modernization and Targeted Replacement Programs:
-
Practice: Systematically identifying and replacing the oldest or highest-risk assets. This often involves "reconductoring" feeders with advanced conductors (e.g., HTLS, ACCC) to increase capacity and reduce losses, or upgrading aging transformers and switchgear.
-
Benefit: Improves overall grid reliability, increases capacity, and reduces future maintenance burdens. Our OHTL wire cable conductor tension stringing equipment is essential for these reconductoring projects.
-
-
5. Vegetation Management:
-
Practice: Aggressive and regular tree trimming around overhead lines to prevent contact during storms, which is a leading cause of outages.
-
Benefit: Significantly reduces weather-related outages and enhances fire safety.
-
-
6. Grid Hardening and Resiliency Measures:
-
Practice: Investing in stronger poles (e.g., concrete or composite), more robust conductor types, and burying critical sections of lines in areas prone to extreme weather.
-
Benefit: Increases the physical resilience of the infrastructure against external threats.
-
-
7. Advanced Training for Workforce:
-
Practice: Providing continuous training for technicians and engineers on new technologies, diagnostic tools, and safety protocols for maintaining modern and aging infrastructure.
-
Benefit: Ensures a skilled workforce capable of handling complex maintenance tasks.
-
-
8. Standardization of Equipment and Procedures:
-
Practice: Using standardized equipment types and maintenance procedures where possible to simplify training, spare parts management, and overall logistics.
-
By proactively adopting these best practices, utilities can effectively manage their aging power distribution infrastructure, extend the lifespan of valuable assets, significantly improve service reliability, and ensure a safer working environment for their personnel. Our company, as a comprehensive manufacturer and exporter of tools and equipment for power lines, substations, electrical construction, and maintenance, provides the essential resources to implement these strategies globally.
Energy Storage Systems (ESS), particularly battery energy storage (BESS), are rapidly emerging as a transformative technology in power distribution networks. They play a crucial and multifaceted role in enhancing grid stability, improving efficiency, and facilitating the integration of intermittent renewable energy sources, ultimately contributing to a more resilient and flexible distribution system.
I. Role of Energy Storage in Power Distribution:
-
1. Grid Stability and Voltage Regulation:
-
Role: ESS can rapidly inject or absorb reactive power to provide dynamic voltage support, compensating for voltage fluctuations caused by fluctuating loads or variable renewable generation (like solar PV). They can also provide inertial response in a microgrid setting, contributing to frequency stability.
-
Benefit: Maintains power quality, prevents voltage sags or swells, and enhances the overall stability of the distribution network, especially in areas with high DER penetration.
-
-
2. Peak Shaving and Load Leveling:
-
Role: ESS can store excess electricity during off-peak hours (when electricity is cheaper or generation is high) and then discharge it during peak demand periods.
-
Benefit: Reduces the strain on distribution feeders and transformers during peak loads, defers the need for expensive infrastructure upgrades, lowers peak demand charges for consumers, and reduces reliance on expensive peaker plants.
-
-
3. Integration of Intermittent Renewables:
-
Role: ESS acts as a buffer, storing surplus power from solar and wind when generation exceeds demand, and then releasing it when generation drops or demand increases.
-
Benefit: Smooths out the variability of renewable energy output, making it more dispatchable and reliable, reducing curtailment of renewable energy, and enabling higher penetration of clean energy sources on the distribution grid.
-
-
4. Enhanced Grid Resilience and Black Start Capability:
-
Role: In the event of an outage, strategically placed ESS (especially within microgrids) can "island" and provide critical backup power to essential loads, maintaining service during grid disturbances. Some ESS can also provide "black start" capability, helping to restore power to a de-energized grid.
-
Benefit: Significantly improves the reliability and resilience of the distribution network against extreme weather events, natural disasters, or physical attacks.
-
-
5. Congestion Relief:
-
Role: ESS can absorb power from congested feeders or inject power into areas experiencing deficits, relieving localized congestion and optimizing power flow.
-
Benefit: Improves the efficiency of existing distribution assets and avoids costly upgrades.
-
-
6. Ancillary Services and Market Participation:
-
Role: Larger ESS connected to the distribution grid can participate in wholesale electricity markets by providing various ancillary services, such as frequency regulation, reactive power support, and operating reserves.
-
Benefit: Creates new revenue streams for ESS owners and contributes to overall grid flexibility and market efficiency.
-
-
7. Electric Vehicle (EV) Charging Management:
-
Role: ESS can manage large and fluctuating loads from EV charging stations, buffering the impact on the distribution grid and allowing for more controlled and efficient charging.
-
Benefit: Supports the rapid growth of EV adoption without overburdening existing distribution infrastructure.
-
As the deployment of ESS continues to accelerate, particularly at the distribution level, the demand for specialized electrical construction and maintenance tools and equipment for their installation and upkeep will grow proportionally. Our company's comprehensive supply of tools and equipment for substations, power lines, and electrical construction is directly relevant to these projects, from the underground cable laying equipment for battery connections to the maintenance tools for the associated power electronics and control systems, ensuring the safe and efficient integration of these vital storage assets into the power distribution network.
A complete OHTL stringing operation typically requires a coordinated set of specialized equipment. The core components include:
-
Hydraulic Pullers: Used to pull pilot ropes or conductors through stringing blocks. They provide precise control over pulling force and speed.
-
Hydraulic Tensioners: Apply controlled back tension to the conductor during stringing to prevent it from touching the ground or obstructions, ensuring consistent sag and minimizing damage.
-
Anti-Twist Steel Wire Ropes: High-strength, specialized ropes used with pullers for initial stringing, designed to resist twisting.
-
Conductor Stringing Blocks (Sheaves): Installed on towers to support and guide the conductor during the stringing process, minimizing friction.
-
Reel Stands (Conductor Reel Winders/Unwinders): Support the conductor reels and allow for controlled unwinding or winding of the conductor.
-
Conductor Grips/Come-Alongs: Devices used to grip and pull the conductor.
-
Swivels: Prevent twisting of the conductor during pulling operations.
-
Dynamometers: Measure and display the tension being applied during stringing.
-
Auxiliary Equipment: Includes gin poles, pole erection tools, anti-fall devices, grounding equipment, and various safety tools.
Conventional (Slack) Stringing: Involves pulling the conductor without controlled tension, allowing it to sag significantly between towers. This method can lead to conductor damage from dragging on the ground, increased risk of contact with obstacles, and requires more manual labor for sagging adjustments.
Tension Stringing: Involves maintaining continuous, controlled tension on the conductor throughout the pulling process, preventing it from touching the ground. This method is preferred because it:
-
Minimizes Conductor Damage: Prevents scratches, nicks, and abrasions that can compromise conductor integrity and lead to premature failure or corona effects.
-
Ensures Consistent Sag: Achieves precise sag and tension profiles as per design specifications, critical for line performance and clearance.
-
Enhances Safety: Reduces the risk of accidental contact with energized lines (in live-line stringing), obstacles, or personnel.
-
Increases Efficiency: Faster installation, especially for long spans and multiple conductors, and reduces post-stringing adjustments.
-
Environmental Protection: Less impact on vegetation and ground features as conductors are kept clear.
Safety is paramount in all our equipment designs and operational recommendations. Our solutions ensure safety through:
-
Precise Control Systems: Hydraulic pullers and tensioners feature advanced control systems for smooth, predictable operation, preventing sudden jerks or over-tensioning.
-
Fail-Safe Braking Systems: Our tensioners incorporate robust braking mechanisms that automatically engage in case of power loss or emergency, holding the conductor securely.
-
Integrated Safety Features: Overload protection, emergency stop buttons, and robust structural designs prevent equipment failure.
-
Insulated Components: For live-line stringing applications, our specialized equipment includes insulated components to protect personnel from energized lines.
-
Ergonomic Design: Equipment is designed for ease of operation, reducing operator fatigue and the potential for human error.
-
Compliance with Standards: All our equipment is manufactured to rigorous international safety and quality standards (e.g., ISO, CE, specific regional requirements). We also provide clear operation manuals and recommend comprehensive training.
The industry is constantly evolving, and we incorporate the latest innovations into our equipment:
-
Automation & Remote Control: Increased use of automated processes and remote control capabilities for pullers and tensioners, allowing operators to manage operations from a safer distance and with greater precision.
-
Data Logging & Telemetry: Equipment now often includes integrated sensors and data logging capabilities to monitor tension, speed, and other parameters in real-time, providing valuable data for quality control, troubleshooting, and project management.
-
Enhanced Hydraulic Systems: More efficient and responsive hydraulic systems for smoother operation, reduced energy consumption, and quieter performance.
-
Modular and Compact Designs: For easier transportation, quicker setup, and adaptability to various terrains, especially in challenging environments.
-
Environmentally Friendly Solutions: Development of equipment with lower emissions and reduced noise pollution, aligning with global sustainability efforts.
-
Integration with UAVs (Drones): Drones are increasingly used for pilot rope pulling in difficult terrains, inspection, and route surveying, integrating with traditional stringing methods.
Challenging terrains require specialized approaches and robust equipment. We offer solutions tailored for these conditions:
-
High-Capacity Equipment: Our heavy-duty pullers and tensioners are designed to handle longer spans and heavier conductors, common in mountainous or large river crossings.
-
Specialized Stringing Methods: We support methods like helicopter stringing for pilot rope installation over inaccessible areas, and utilize robust aerial stringing blocks for large sag differentials.
-
Customizable Solutions: We can provide customized stringing blocks, hauling systems, and anchoring solutions to adapt to specific site challenges.
-
Terrain Adaptability: Our equipment is built for durability and stability on uneven ground, often featuring enhanced traction and leveling systems.
-
Logistical Support: We can advise on logistical planning for equipment deployment and material handling in remote or difficult-to-access sites.
Regular and proper maintenance is crucial for maximizing the lifespan and ensuring optimal performance of your stringing equipment:
-
Routine Inspections: Daily checks of hydraulic hoses, fluid levels, wire ropes, sheaves, and braking systems for wear, damage, or leaks.
-
Lubrication: Regular lubrication of moving parts, bearings, and critical joints as per manufacturer guidelines.
-
Hydraulic System Checks: Monitoring hydraulic fluid quality, filter replacement, and pressure checks to ensure system efficiency.
-
Wire Rope Care: Regular inspection, cleaning, and replacement of anti-twist steel wire ropes as they are subject to significant wear.
-
Sheave Maintenance: Inspection and replacement of worn or damaged stringing block liners and bearings to prevent conductor damage.
-
Calibration: Periodic calibration of dynamometers and control systems to ensure accurate tension and speed readings.
-
Storage: Proper storage of equipment when not in use, protecting it from elements and unauthorized access. We provide detailed maintenance manuals with all our equipment and can offer training on best maintenance practices.
Yes, our equipment is versatile and designed for both new overhead transmission line construction and re-conductoring (upgrading existing lines). For re-conductoring projects, our tension stringing methods are particularly beneficial as they allow for the controlled removal of old conductors and simultaneous installation of new ones, often without requiring complete power outages or with minimal disruption. This method is crucial for maintaining system reliability during grid upgrades.
8. What factors should be considered when selecting the right stringing equipment for a project?
Answer: Selecting the appropriate equipment depends on several project-specific factors:
-
Conductor Type and Size: The diameter, weight, and material of the conductor dictate the required pulling force and tension capacity.
-
Line Voltage and Capacity: Higher voltage lines often require more robust equipment and specialized safety features.
-
Span Lengths: Longer spans necessitate higher tension capacities and often more powerful pullers.
-
Terrain and Environmental Conditions: Mountainous, swampy, or urban areas, as well as extreme weather conditions, influence equipment selection (e.g., tracked vs. wheeled, remote control needs).
-
Project Scale and Timeline: Larger projects may require multiple sets of equipment or higher-capacity machines to meet deadlines.
-
Budget and Logistics: Balancing equipment cost, operational efficiency, and transportation logistics.
-
Safety Standards and Regulations: Ensuring the equipment meets all relevant local and international safety guidelines.
Beyond the major stringing equipment, a range of specialized hand tools and accessories are critical for efficient, safe, and precise OHTL stringing. These include:
-
Conductor Grips / Come-Alongs: Used for securely holding and tensioning conductors during splicing, sagging, and other operations.
-
Stringing Blocks / Conductor Sheaves: Installed on towers to support and guide conductors, reducing friction during stringing. These come in various sizes and configurations (single, bundle) and are often lined with materials like nylon or polyurethane to protect the conductor.
-
Anti-Twist Swivels: Placed between the pulling rope and conductor to prevent twisting and torque buildup, especially important for bundled conductors or OPGW.
-
Running Boards / Pulling Socks: Connect multiple conductors for simultaneous stringing, ensuring even tension and preventing individual conductor damage.
-
Pilot Wire / Anti-Twisting Steel Ropes: Used for initial pulling, designed with specific constructions (e.g., hexagonal, braided) to resist rotation.
-
Dynamometers / Tension Meters: Essential for accurately measuring the tension applied to conductors, critical for achieving target sag and ensuring safety.
-
Hydraulic Cutters and Crimpers: For precise cutting and splicing of conductors, ensuring strong and reliable connections.
-
Grounding Equipment: Temporary grounding clamps and cables are vital for safety, de-energizing lines before work.
-
Personal Protective Equipment (PPE): Insulated gloves, hard hats, safety glasses, harnesses, and fall arrest systems are non-negotiable for worker safety.
Stringing blocks are meticulously designed to protect conductors by:
-
Smooth Surfaces: The inner grooves of the sheaves are typically lined with a durable, low-friction material like high-grade nylon, polyurethane, or aluminum alloy. This smooth surface minimizes abrasion and scratching on the conductor's outer strands.
-
Appropriate Diameter: Blocks are sized correctly for the conductor diameter to ensure the conductor sits securely within the groove and avoids excessive bending, which can lead to stress points or deformation.
-
Robust Bearings: High-quality, sealed ball bearings ensure the sheave rotates freely with minimal friction, reducing the pulling force required and preventing localized heating or wear on the conductor.
-
Proper Alignment: When installed correctly on towers, stringing blocks guide the conductor smoothly along the line, preventing kinks or sharp angles that could cause damage.
-
Bundle Configurations: For bundled conductors, specialized multi-groove blocks ensure each sub-conductor is adequately supported and spaced, preventing inter-conductor abrasion.
Choosing the correct conductor grip or come-along is crucial for safe and effective stringing. Key factors include:
-
Conductor Material and Type: Grips are designed for specific conductor types (e.g., ACSR, AAAC, AAC, OPGW) and materials (aluminum, copper). Using the wrong grip can damage the conductor.
-
Conductor Diameter: The grip must match the exact diameter range of the conductor to ensure a secure, non-slip hold without deforming the conductor.
-
Required Pulling Capacity: The grip's rated capacity (working load limit) must exceed the maximum tension it will experience during stringing.
-
Jaw Design: Different jaw designs are available for various applications, such as parallel jaw for general use, or specific designs to minimize damage on sensitive conductors.
-
Safety Features: Look for grips with positive locking mechanisms or safety latches to prevent accidental release.
-
Durability and Material: Grips should be made from high-strength, durable materials that resist wear and corrosion, ensuring long-term reliability.
Anti-twist swivels are critically important, especially for OPGW (Optical Ground Wire) and bundled conductors, for several reasons:
-
Preventing Twisting: OPGW cables contain delicate optical fibers that are highly susceptible to damage from twisting. Swivels allow the cable to rotate freely, preventing torsional stress from being transferred from the pulling rope to the OPGW.
-
Maintaining Conductor Integrity: For bundled conductors, swivels prevent individual sub-conductors from twisting around each other, which can lead to damage, uneven tensioning, and difficulty in installing spacers.
-
Smooth Stringing: By eliminating torque buildup, swivels ensure a smoother pulling operation, reducing stress on the pulling equipment and the conductor itself.
-
Improved Sagging Accuracy: A twisted conductor can impact the accuracy of sag measurements and lead to an uneven sag profile, which affects line performance and clearances. Swivels help maintain a consistent conductor orientation.
When selecting stringing tools, always prioritize those that meet or exceed recognized international safety standards and certifications. Key standards and certifications include:
-
ISO 9001: Demonstrates a commitment to quality management systems in manufacturing.
-
CE Marking (for European markets): Indicates conformity with health, safety, and environmental protection standards.
-
ASTM (American Society for Testing and Materials): Many specific ASTM standards apply to materials, testing, and performance of various tools (e.g., for conductor grips, ropes).
-
OSHA (Occupational Safety and Health Administration - USA): While not a certification for tools directly, compliance with OSHA regulations is often expected in regions that follow US safety protocols.
-
Local and National Regulations: Always verify compliance with the specific safety regulations of the country or region where the tools will be used.
-
Manufacturer's Load Ratings: Ensure tools are clearly marked with their Safe Working Load (SWL) or Working Load Limit (WLL) and always adhere to these limits.
-
Material and Testing Certifications: Reputable manufacturers provide material certifications and test reports for critical components like ropes, swivels, and grips.
Hot-line or live-line stringing and maintenance require specialized tools designed with advanced insulation and safety features to protect workers from energized lines. Key tools and their safety aspects include:
-
Insulated Hot Sticks/Tools: Made from fiberglass or other non-conductive materials, these tools allow workers to perform tasks from a safe distance while maintaining clearance from energized conductors. They must be regularly tested for dielectric strength.
-
Insulated Link Sticks and Hoists: Used for lifting and maneuvering components while maintaining insulation between the worker and the energized line.
-
Temporary Insulating Devices: Such as line covers, insulator blankets, and conductor covers, provide temporary protection over energized components.
-
Grounding and Bonding Equipment: Specialized clamps and cables used to create equipotential zones, ensuring workers are at the same potential as the conductor, even if it's energized.
-
Voltage Detectors and Phasing Tools: Essential for verifying the presence or absence of voltage and confirming phase relationships before work begins.
-
Specialized PPE: Including insulated rubber gloves with leather protectors, flame-resistant clothing, and dielectric boots.
The safety of these tools primarily comes from their dielectric strength (ability to resist electrical current), robust construction, regular testing and inspection protocols, and strict adherence to live-line work procedures.
Modern stringing tools play an increasingly important role in minimizing environmental impact:
-
Reduced Ground Disturbance: Tension stringing, facilitated by precise pullers and tensioners, keeps conductors off the ground, significantly reducing damage to vegetation, soil erosion, and disruption to ecosystems.
-
Precision and Efficiency: Advanced tools allow for more accurate and faster installation, reducing the overall project footprint and the duration of environmental disturbance.
-
Lower Emissions: Newer hydraulic systems in equipment are often more fuel-efficient, reducing greenhouse gas emissions. Some innovations also include electric or hybrid power options for smaller tools.
-
Minimized Waste: Tools designed for precise cuts and secure splices reduce material waste.
-
Helicopter Stringing Integration: While helicopters themselves have an environmental footprint, their use with specialized stringing tools can minimize ground access requirements in sensitive or difficult terrains, thus protecting untouched areas.
-
Noise Reduction: Continuous development aims at quieter operation of tools to reduce noise pollution in natural habitats or populated areas.
A transmission line stringing machine, encompassing hydraulic pullers and tensioners, is specifically designed for the precise and controlled installation of overhead transmission line conductors (wires) and ground wires. Its primary function is to:
-
Pullers: Generate a controlled pulling force to draw pilot ropes or actual conductors through stringing blocks along the transmission line route.
-
Tensioners: Apply a continuous, controlled back tension to the conductor during the stringing process, keeping it elevated above the ground and obstacles.
Unlike general construction equipment (like excavators or cranes), stringing machines are specialized for linear pulling and tensioning applications, prioritizing precise force control, speed synchronization, and conductor protection over brute force or lifting capabilities. They are engineered to handle delicate conductors over long distances and varied terrains with minimal damage.
The two main types of stringing machines are:
-
Hydraulic Pullers: These machines use a hydraulic system to generate pulling force. They are characterized by their bullwheels (large grooved wheels) or capstans that grip and pull the rope/conductor.
-
Applications: Primarily used to pull pilot ropes, then the main conductors, across spans. They are essential for long-distance stringing, pulling multiple conductors simultaneously (bundle stringing), and re-conductoring projects. They offer precise speed control and overpull protection.
-
-
Hydraulic Tensioners: These machines are designed to pay out conductor under controlled tension. They also feature bullwheels or friction brakes to regulate the back tension.
-
Applications: Critical for tension stringing, preventing the conductor from touching the ground, ensuring consistent sag, and minimizing damage during installation. They are used in conjunction with pullers to maintain a continuous tensioned system.
-
Puller-Tensioners: Some machines combine both functions, capable of acting as a puller or a tensioner, offering versatility for various project phases or smaller operations.
-
Modern stringing machines have seen significant advancements, enhancing both efficiency and safety:
-
Advanced Hydraulic Control Systems: Provide extremely precise and infinitely variable control over pulling force and tension, enabling smoother operation and preventing sudden jerks that could damage conductors.
-
Automated Data Logging and Monitoring: Integrated sensors and digital displays provide real-time data on tension, speed, length, and engine parameters. This data can be logged for quality assurance, project reporting, and predictive maintenance.
-
Remote Control Capabilities: Many modern machines offer wired or wireless remote control, allowing operators to manage stringing operations from a safer vantage point, improving visibility and coordination.
-
GPS Integration: For accurate mapping of the line route, precise conductor length management, and location tracking during stringing.
-
Self-Diagnostics and Alarms: Built-in systems can detect malfunctions or operational anomalies, alerting operators to potential issues before they become critical.
-
Enhanced Braking Systems: Fail-safe, automatic braking systems ensure that the conductor is held securely in place in case of power loss or emergency stops.
-
Environmentally Friendly Engines: Adoption of more fuel-efficient and lower-emission diesel engines, and in some cases, electric or hybrid power options for reduced environmental footprint and quieter operation.