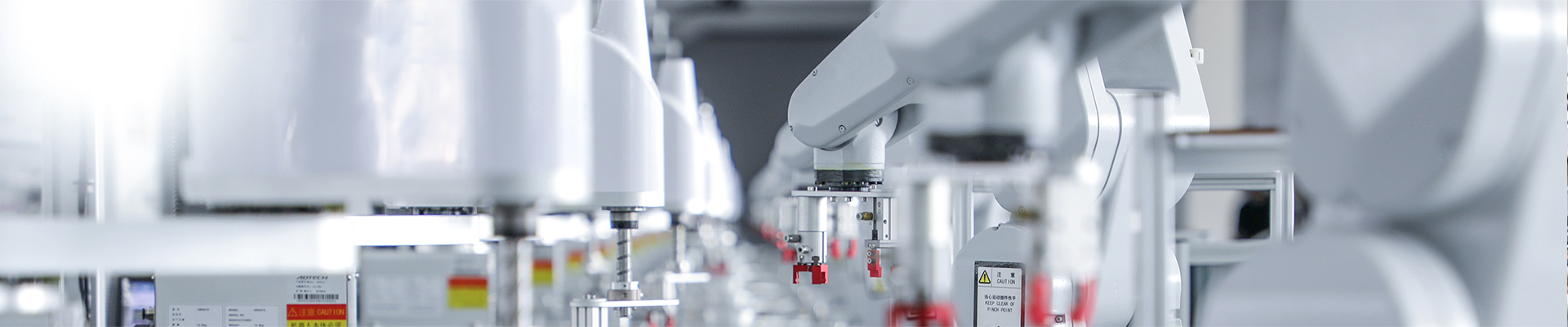
FAQ
Use manufacturer pulling/blowing tables that account for duct type, cable OD, run length and bends; use inline tension/force sensors or dynamometers during the operation to monitor peak loads. Stage the run or use intermediate reels for very long or high-friction routes.
Expect pavement-cut permits, traffic management approval, reinstatement specification (material and compaction) and possible warranties for the restored surface. Involve local agencies early and budget for reinstatement bonds and post-install inspections.
Use vacuum excavation near sensitive utilities, in urban sites, or for potholing to safely expose utilities without cutting or damaging them. Vacuum methods reduce strike risk and are often required by utility owners for verification before trenching.
Smart ducts include embedded sensors or access points for monitoring temperature, moisture and blockage, enabling proactive maintenance and easier troubleshooting. They are useful for critical corridors and reduce reactive excavation by reporting duct health remotely.
Yes — low-VOC and biodegradable lubricants are gaining adoption to meet sustainability goals and local environmental rules; they must still be compatible with cable jackets and duct materials. Test lubricant compatibility before large installs and include compatibility proof in procurement specs.
Always CCTV-inspect ducts for debris, crushing or silt, then perform mechanical brushing or air/fluid cleaning and re-inspect. Clean ducts reduce friction and prevent cable snagging; document the inspection video and cleaning report as part of acceptance.
Micro-duct systems use small continuous ducts that allow air-blown fiber and modular upgrades without full re-excavation; they lower installation time and future-proof networks. They are growing because of speed, scalability and reduced civil costs for subsequent upgrades.
Choose HDD for crossing under obstacles (roads, rivers) or in congested corridors where trenching would be disruptive; pick microtrenching for fast urban runs with short crossings, and open-cut for low-cost rural installs. Evaluate site constraints, cost, reinstatement and permitting when selecting the method.
Select blowing units based on duct diameter, cable outer diameter, total run length and number of bends; manufacturers provide charts correlating required CFM and pressure to those variables. Always validate with a site trial and follow vendor tables to avoid overpressure or cable damage.
Cable blowing (jetting) uses high-speed air to carry fiber through micro-ducts and is faster and gentler for long, multi-bend runs than mechanical pulling. Choose jetting for long runs, micro-duct systems and when minimized handling is needed; pulling can still be better for short or heavy cables.
Pre-plan recovery: include backup ropes, tether options, a grab/retrieval kit, and a trained retrieval crew. Define abort procedures, safe stand-down zones and a communications plan. Conduct practice drills during pre-job safety briefings.
Use controlled braking calibrated to the conductor type and payout speed to prevent slack and sudden surges. Combine braking with CTCS and feed sheaves to guide conductor. Test brake settings during setup and monitor during continuous payout.
Standard warranty covers manufacturing defects; extended warranty options available. We provide worldwide spare parts shipments, technical support, and reconditioning services. On-site service and preventive maintenance contracts are available to minimize downtime.
Yes — helicopters lift heavy pilot lines and equipment for very long spans or large-scale projects where heavier payloads and wind tolerance are needed. Drones are best for light pilot-line work and in locations where helicopter use is not viable or too expensive. Choose per payload and regulatory constraints.
Choose tools offering accurate mapping, conduit condition surveys and bend-count calculators; integrate with GIS for project planning. Use vendor pulling calculators that account for duct type, bends and lubricant to estimate tension and staging needs.
Common failures: worn sheaves/bearings, hydraulic leaks, rope slippage, and bad tension control. Prevent with routine inspections, scheduled oil/ filter changes, correct sheave sizing, and calibrating dynamometers. Keep spares for critical wear parts.
HTLS conductors have higher operating temps; design sag tables for operating temperature extremes and select tensioners that handle higher tensions. Use expansion allowances in dead-ends and fit vibration dampers where needed. Follow conductor supplier installation guidance.
Synthetic rope offers lighter weight, easier handling and lower stored energy on failure; wire rope is durable but heavier. Choose per environment, manufacturer recommendations and bullwheel design—ensure the rope type matches the machine’s groove and grip system.
Verify equipment load ratings, inspect sheaves/blocks, confirm reel and payout brake operation, test radios/communications, confirm grounding/earthing plan, and do a job-hazard analysis (JHA) with crews before work. Document results and ensure PPE and rescue plans are in place.
Get the latest price? We'll respond as soon as possible(within 12 hours)