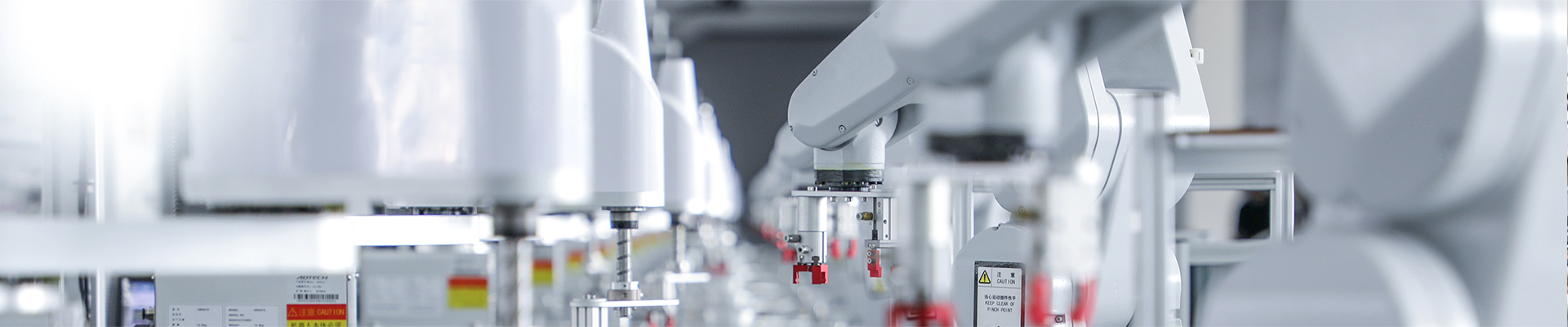
FAQ
"OPGW dead-end clamp installation tools" are specialized implements for securely terminating OPGW at anchor or tension towers:
-
Precision Application: These tools ensure the precise and even application of pre-formed helical dead-end grips or compression dead-end clamps onto the OPGW. Improper application can cause localized stress, fiber damage, or even catastrophic mechanical failure.
-
Fiber Protection: Unlike conventional conductor tools that might rely on aggressive gripping, OPGW tools prioritize distributed pressure and gentle handling to prevent crushing the delicate optical tubes within the OPGW.
-
Specific Designs: Tools may include specialized wrenches, hydraulic crimpers with custom dies for specific OPGW sizes, or winding tools for pre-formed dead-ends that ensure proper helix formation without deforming the cable.
Their distinction lies in their meticulous design to preserve the OPGW's structural integrity and optical performance at its most critical termination points.
Yes, absolutely. We recognize that "custom OPGW installation tools" are often required for highly specialized or challenging projects:
-
Tailored Solutions: Our engineering team possesses the expertise to design and fabricate bespoke OPGW tools to meet unique cable specifications (e.g., unusual diameters, composite structures), specific environmental conditions, or innovative installation methods.
-
Problem-Solving Focus: We collaborate closely with our clients' project engineers to understand their precise needs and develop custom tools that address specific challenges, such as installing OPGW in extremely tight spaces, over complex obstacles, or with non-standard hardware.
-
Prototyping & Testing: We offer prototyping and testing services to ensure that custom tools perform exactly as required before full-scale production.
This capability highlights our commitment to being a flexible and comprehensive solutions provider for the most demanding OPGW projects worldwide.
-
Choosing us as your "China OPGW Installation Tools" supplier provides distinct advantages:
-
Specialized Expertise: Our deep focus on power line and substation equipment ensures our tools are specifically designed and optimized for the delicate handling requirements of OPGW.
-
High Quality & Durability: We utilize premium-grade materials (e.g., hardened steels, durable polymers, corrosion-resistant alloys) and advanced manufacturing processes to produce tools that are robust, long-lasting, and perform reliably in various global conditions.
-
Cost-Effectiveness: Our efficient production scale in China allows us to offer competitively priced OPGW tools without compromising on quality, providing excellent value for your investment.
-
Comprehensive Product Range: We offer a full suite of OPGW installation tools, from preparation and stringing to testing and maintenance, serving as a convenient one-stop shop.
-
International Compliance: Our tools adhere to relevant international quality and safety standards, ensuring their suitability for global deployment.
-
Reliable Global Logistics: Our extensive experience as an exporter ensures efficient and secure delivery of tools to your project sites worldwide.
-
We are committed to providing comprehensive "technical support" and "warranty" for our "OPGW installation tools" globally:
-
Expert Technical Assistance: Our dedicated support team is available to provide guidance on tool usage, troubleshooting, and best practices for OPGW installation.
-
Comprehensive Documentation: Each tool comes with detailed operation and maintenance manuals, offering clear instructions and safety guidelines.
-
Standard Warranty: All our OPGW installation tools are backed by a robust warranty against manufacturing defects, demonstrating our confidence in their quality and reliability.
-
Spare Parts Availability: We ensure a ready supply of common wear-and-tear components and spare parts to minimize downtime and extend the lifespan of your tools.
-
Training Resources: We can provide training materials or even arrange on-site demonstrations for your teams to ensure proper and safe use of our specialized OPGW tools.
"OPGW protection rods" and "armor rods" are essential "OPGW Installation Accessories" designed to safeguard the cable at its attachment points:
-
Protection Rods (Helical Rods): These are pre-formed helical rods wrapped around the OPGW at suspension points (e.g., within suspension clamps or at the entrance to stringing blocks). Their primary function is to increase the bending radius of the OPGW, distribute clamping forces over a wider area, and prevent localized stress concentrations, abrasion, and fatigue damage caused by vibration or dynamic loads.
-
Armor Rods: Similar to protection rods but often thicker and used at dead-end or tension points. They provide superior protection against abrasion, crushing, and bending fatigue at the point where the OPGW is under constant tension.
Both types of rods are indispensable as they extend the mechanical lifespan of the OPGW, prevent damage to the outer strands, and, crucially, protect the delicate internal optical fibers from stress and micro-bending, ensuring uninterrupted communication.
"Vibration dampers" are crucial "OPGW Installation Accessories" engineered to mitigate Aeolian vibration (wind-induced oscillation) that can lead to fatigue failure in overhead lines, especially OPGW:
-
Energy Dissipation: Devices like Stockbridge dampers or spiral dampers are strategically clamped onto the OPGW. When the cable vibrates, the damper's weights or helical design oscillate out of phase with the cable, absorbing and dissipating the vibrational energy.
-
Fatigue Prevention: This dampening action significantly reduces the dynamic bending stress at critical points, such as where the OPGW enters a suspension clamp. Without effective dampening, prolonged vibration can cause repeated stress cycles, leading to metal fatigue, strand breakage, and eventual mechanical failure of the OPGW and potential optical fiber damage.
Properly selected and installed OPGW vibration dampers are vital for safeguarding the OPGW's structural integrity and ensuring its long-term operational reliability.
Selecting the correct "OPGW suspension clamps" and "dead-end clamps" is critical for mechanical support and optical fiber protection:
-
OPGW Suspension Clamps: These are designed for tangent and light-angle supports. Key considerations include:
-
Gentle Grip: Must distribute clamping pressure evenly over the OPGW's surface to avoid crushing the optical core. Often include elastomer inserts or incorporate protection rods.
-
Freedom of Movement: Should allow for limited longitudinal movement and rotation to prevent stress concentration from wind or temperature changes.
-
Large Radius: Designs that ensure the OPGW is never bent below its minimum bending radius.
-
-
OPGW Dead-End Clamps: Used at tension towers or termination points to securely grip the OPGW under full mechanical tension. Key considerations include:
-
Full Tension Capability: Must be capable of holding the OPGW's rated breaking strength (RBS) without slippage.
-
Fiber Protection: Designs, such as pre-formed helical dead-ends or specific compression types, ensure the tensile force is applied to the metallic components of the OPGW while protecting the optical fibers from excessive stress.
-
Material Compatibility: Chosen to prevent galvanic corrosion between the clamp and the OPGW's outer strands.
-
Proper selection, often based on OPGW type, diameter, and line tension, is paramount to ensure both mechanical integrity and the uninterrupted optical performance of the OPGW.
"OPGW splice enclosures" and "fiber optic splice trays" are fundamental "OPGW Installation Accessories" for protecting the delicate optical splices:
-
OPGW Splice Enclosures: These are robust, environmentally sealed housings (typically IP68 rated) designed to protect optical splices from external elements like moisture, dust, extreme temperatures, and UV radiation, as well as mechanical impact. They are engineered for easy re-entry for maintenance or future fiber additions. They often include secure entry ports for the OPGW cable and a grounding system for the metallic components.
-
Fiber Optic Splice Trays: Located inside the splice enclosure, these trays organize and secure the spliced optical fibers and any excess fiber length. They ensure that the fibers are routed within their minimum bending radius, preventing macro-bends or micro-bends that could cause signal loss. Each tray is designed to hold a specific number of fusion or mechanical splices safely.
Together, these accessories create a secure, stable, and protected environment for the optical connections, which are the most vulnerable points of the OPGW communication link, ensuring long-term signal reliability.
"Smart OPGW monitoring accessories" represent a significant advancement in power line management:
-
Integrated Sensors: These accessories incorporate miniature sensors capable of real-time monitoring of critical parameters such as OPGW conductor temperature, sag, vibration levels, ice accretion, and even tension.
-
IoT Connectivity: Data collected by these sensors is transmitted wirelessly (often via the OPGW's own fiber optic network or cellular/satellite links) to a central control system, integrating with "Smart Grid" platforms.
-
Predictive Maintenance: By continuously analyzing this data, utilities can detect anomalies and identify potential issues before they escalate into failures (e.g., high vibration indicating damper issues, rapid temperature changes signaling potential overload). This enables proactive maintenance, reducing costly outages and extending asset life.
-
Enhanced Situational Awareness: Provides operators with unprecedented real-time insight into the health and performance of their transmission lines, optimizing resource allocation and improving overall grid reliability.
These accessories are crucial for utilities aiming to build more resilient, efficient, and intelligent power grids.
"OPGW grounding accessories" are continuously evolving for enhanced safety and performance:
-
Low Resistance Grounding Clamps: Focus on designs that provide extremely low contact resistance for efficient current dissipation, particularly important for lightning strikes. Materials like high-conductivity copper or aluminum alloys are preferred.
-
Modular Grounding Kits: Comprehensive kits that include all necessary components (clamps, braids, bonding straps, connection hardware) for complete and reliable grounding at splice points, towers, and equipment.
-
Corrosion Resistance: Increased use of highly corrosion-resistant materials and coatings for all grounding components to ensure long-term effectiveness in diverse environmental conditions.
-
Ease of Installation: Designs that simplify installation procedures while ensuring secure, high-integrity connections, reducing labor time and potential for installation errors.
-
Compliance with Standards: Strict adherence to relevant international grounding and bonding standards (e.g., IEEE, IEC) for reliable lightning protection and fault current handling.
These trends emphasize maximizing safety, reliability, and ease of deployment for the critical grounding function of OPGW.
Partnering with us for your "OPGW Installation Accessories" offers significant benefits to international clients:
-
Specialized Expertise: Our core focus on power line and substation equipment ensures our accessories are specifically engineered to meet the stringent requirements of OPGW, guaranteeing optimal performance and cable protection.
-
Comprehensive One-Stop Supply: We offer a full range of OPGW installation accessories, from specialized clamps and dampers to splice enclosures and grounding kits, providing a convenient single source for all your project needs.
-
Exceptional Value & Cost-Effectiveness: Our advanced manufacturing facilities and efficient supply chain in China enable us to provide high-quality OPGW accessories at highly competitive international prices, optimizing your project budget.
-
Robust Quality Control & Compliance: All our accessories undergo rigorous quality inspections and are manufactured to meet or exceed relevant international standards (e.g., IEC, ISO), ensuring reliability and broad market acceptance worldwide.
-
Innovation & Customization: We continuously invest in R&D to incorporate the latest materials and designs, and we offer customization services to develop bespoke accessories for unique project specifications.
-
Reliable Global Logistics & Support: With extensive experience in international export, we ensure timely, secure, and compliant delivery of accessories to your project sites globally, backed by dedicated technical support.
Ensuring compatibility is paramount for efficient OPGW installation:
-
Precision Engineering: Our accessories are designed with precise specifications to ensure a perfect fit with a wide range of OPGW cable diameters and constructions (e.g., central tube, multi-tube, stranded types).
-
Universal Design Principles: Where possible, our accessories incorporate universal design elements that allow for broader compatibility with different brands and types of stringing equipment (e.g., standard attachment points for pulling grips, common sizes for stringing block mounting).
-
Material Compatibility: We carefully select materials for our accessories to prevent galvanic corrosion when in contact with various OPGW cable materials (e.g., aluminum alloy, aluminum clad steel, stainless steel).
-
Comprehensive Testing: Accessories undergo rigorous testing for mechanical fit, electrical performance (where applicable), and material interaction to ensure seamless integration and long-term reliability.
-
Technical Consultation: Our sales and engineering teams work closely with clients to understand their specific OPGW cable types and existing equipment, advising on the most suitable accessories and offering customized solutions where needed.
This meticulous approach guarantees that our OPGW installation accessories integrate flawlessly into your projects, enhancing performance and minimizing installation complexities.
A complete "tension stringing equipment set" works as a synchronized system to control conductor installation:
-
Hydraulic Puller: Located at one end of the section being strung, it pulls the pilot rope, which in turn pulls the conductor through the stringing blocks on the towers. It provides the necessary pulling force with precise speed control.
-
Hydraulic Tensioner: Positioned at the other end, it applies a continuous, controlled back tension to the conductor as it is pulled. This prevents the conductor from slacking and ensures it remains clear of the ground and obstacles.
-
Reel Stands (Conductor Drum Stands): Support the large conductor reels and often include braking systems to provide additional tension or prevent overruns.
-
Stringing Blocks (Sheaves): Specialized, large-diameter pulleys mounted on towers that guide the conductor smoothly and protect its surface as it is pulled.
-
Pulling Grips & Swivels: Connect the pilot rope to the conductor and allow for rotation to prevent twisting of the conductor.
-
Communication System: Essential for continuous coordination between pulling and tensioning sites.
These components work in unison, typically controlled by skilled operators communicating via radio, to ensure the conductor is installed safely, efficiently, and to exact specifications.
Safety is our top priority, and our "wire stringing equipment" incorporates multiple critical "safety features":
-
Automatic Overload Protection: Systems that automatically detect and prevent pulling or tensioning forces from exceeding pre-set safe limits, protecting the conductor from damage and preventing equipment strain.
-
Emergency Stop Systems: Strategically placed, easily accessible emergency stop buttons (often multiple locations including remote controls) that instantly halt all machine operations.
-
Fail-Safe Braking Systems: Hydraulic braking systems are designed to engage automatically in the event of engine shutdown or hydraulic pressure loss, preventing uncontrolled movement of the conductor.
-
Operator Guarding & Ergonomics: Protective cages, safety barriers, and ergonomic control panels that provide a safe and comfortable working environment for operators.
-
Audible & Visual Alarms: Clear alerts for critical conditions such as over-tension, low fluid levels, or system malfunctions.
-
Robust Grounding Points: Clear and accessible terminals for proper earthing of the equipment to manage static build-up and fault currents.
-
Compliance: Designed and manufactured to stringent international safety standards (e.g., CE, relevant IEC guidelines).
These features are integral to minimizing risks, preventing accidents, and ensuring a safe working environment on dynamic power line construction sites.
"Smart tension stringing machines" represent the next generation of conductor installation, leveraging integrated IoT (Internet of Things) and real-time monitoring to enhance efficiency, safety, and data insights:
-
Precise Real-time Data: Operators receive continuous, accurate feedback on pulling tension, speed, distance, engine performance, and hydraulic parameters via digital displays.
-
Automated Control: Advanced systems can maintain a pre-set tension automatically, adjusting hydraulic output to compensate for variations in terrain, conductor weight, or friction, minimizing human error.
-
IoT Connectivity: Machines can transmit operational data wirelessly to cloud platforms, enabling remote monitoring, predictive maintenance scheduling, and comprehensive project documentation for quality assurance.
-
Enhanced Safety Alarms: Smart systems provide instant alerts and automatic shutdowns if tension limits are exceeded, hydraulic pressure drops, or other critical safety parameters are violated.
-
Data Logging & Analytics: Automatic recording of all key stringing parameters provides valuable data for post-project analysis, optimizing future operations, and regulatory compliance.
These smart features lead to superior precision, reduced operational risks, and significant long-term cost savings for utilities and contractors.
Our "high-capacity tension stringing equipment" is specifically engineered to handle the demands of large-diameter and bundle conductors over long spans:
-
Robust Hydraulic Power: Equipped with powerful diesel engines and advanced hydraulic systems that deliver consistently high pulling and tensioning forces (e.g., up to 4x50kN or more) required for heavy conductors.
-
Large Bullwheel/Capstan Diameters: Designed with generously sized, wear-resistant bullwheels or capstans (often 1.5 meters or more in diameter) to minimize the bending stress on large conductors and bundles, preventing damage.
-
Multi-Groove & Dedicated Sheaves: Many models feature multiple grooves or separate bullwheels for simultaneous stringing of bundle conductors, ensuring even tension distribution across all sub-conductors.
-
Heavy-Duty Construction: Built with reinforced frames and components to withstand the immense forces and continuous operation associated with large-scale projects.
-
Advanced Braking Systems: Incorporate robust negative self-acting hydraulic brakes to ensure precise and safe control, even with very heavy conductor loads.
These specialized design elements ensure efficient, safe, and precise installation of the heaviest and most complex conductor configurations.
-
Safety is paramount in our "tension stringing equipment" design philosophy:
-
Automatic Overload Protection: Integrated sensors and control systems automatically detect and prevent the application of excessive tension, protecting both the conductor and the equipment from damage.
-
Emergency Stop Systems: Easily accessible emergency stop buttons and automatic hydraulic braking ensure rapid and safe shutdown in critical situations.
-
Operator Protection: Features such as protective cages, anti-vibration seats, clear visibility from the control panel, and ergonomic controls reduce operator fatigue and enhance safety awareness.
-
Fail-Safe Hydraulic Systems: Designed so that hydraulic pressure loss or engine shutdown automatically applies brakes, preventing uncontrolled movement of the conductor.
-
Robust Grounding Points: Clearly marked and easily accessible grounding terminals ensure proper earthing of the equipment, critical for electrical safety.
-
Compliance with Standards: All equipment is designed and manufactured to meet international safety standards, including CE marking and relevant IEC guidelines.
-
-
These integrated safety features minimize risks to personnel and protect valuable equipment and conductors during all stringing operations.
To ensure "long-term durability" and optimal performance of your hydraulic tension stringing equipment, we recommend:
-
Regular Fluid Checks & Replacement: Routinely inspect hydraulic oil levels and quality, and replace filters and fluid according to manufacturer schedules to prevent contamination and ensure smooth hydraulic operation.
-
Lubrication: Regularly lubricate all moving parts, including bearings, pivot points, and sheaves, to reduce friction and wear.
-
Component Inspection: Periodically inspect bullwheels/capstans for wear, damage, or buildup. Check hoses, fittings, and seals for leaks or deterioration. Inspect all structural welds and fasteners.
-
Engine Maintenance: Follow the engine manufacturer's guidelines for oil changes, air filter replacement, and general tune-ups.
-
Calibration Checks: Periodically verify the accuracy of the tension display and control system using a calibrated dynamometer to ensure precise tension application.
-
Cleanliness: Keep the machine clean, especially hydraulic components and cooling systems, to prevent overheating and contamination.
Adhering to a strict preventive maintenance schedule, coupled with using genuine spare parts and qualified technicians, will significantly extend the lifespan and reliability of your investment.
Choosing us as your "China tension stringing equipment" supplier offers significant advantages for international clients:
-
Specialized Expertise: Decades of focused experience in power line equipment, guaranteeing machines specifically engineered for the complexities of overhead transmission line construction.
-
Advanced Technology & Innovation: We continuously invest in R&D, incorporating the latest smart technologies, precision controls, and durable materials, placing our equipment at the forefront of the industry.
-
Comprehensive One-Stop Solution: Beyond primary pullers and tensioners, we offer a full range of compatible accessories, tools, and services, streamlining your procurement and project management.
-
Exceptional Value & Cost-Effectiveness: Our advanced manufacturing scale and efficient supply chain in China enable us to deliver high-quality, high-performance tension stringing equipment at globally competitive prices, maximizing your project budget.
-
Robust Quality Assurance: All our equipment is manufactured under strict ISO 9001 quality management systems and adheres to international safety standards (e.g., CE, relevant IEC guidelines), ensuring reliability and broad market acceptance.
-
Dedicated Global After-Sales Support: We provide comprehensive technical support, operator training programs, and readily available spare parts to ensure the long-term success and minimal downtime of your projects worldwide.
The power line construction industry is increasingly embracing "sustainable practices," and "electric tension stringing equipment" is a key component:
-
Reduced Emissions: Electric or hybrid tension stringing equipment significantly reduces reliance on fossil fuels, leading to lower carbon emissions and air pollution on job sites.
-
Lower Noise Pollution: Electric motors operate much quieter than traditional diesel engines, which is particularly beneficial for urban projects or environmentally sensitive areas, reducing disturbance to local communities and wildlife.
-
Regenerative Braking: Some advanced electric tensioners can feature regenerative braking systems, converting energy generated during tensioning back into electrical power, improving energy efficiency.
-
Eco-Friendly Materials: A growing focus on utilizing recyclable materials and reducing waste in the manufacturing process of the equipment itself.
-
Precision Control: Advanced electric drives often offer even finer control over tension and speed, further minimizing conductor damage and ensuring efficient energy use.
These innovations align with global efforts towards a greener infrastructure, offering a more environmentally responsible approach to overhead transmission line construction.