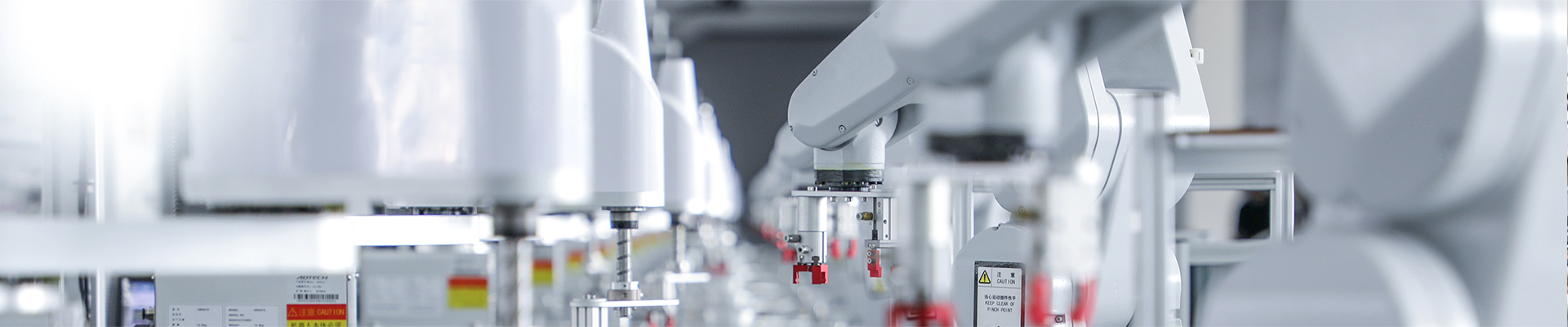
FAQ
Answer: Airspace rules, beyond-visual-line-of-sight (BVLOS) permissions, operator certification and proximity to live lines are the key constraints. Offer a downloadable “Drone Ops for OHTL — Regulatory Checklist” to capture leads.
Answer: Yes. Drones are widely used for inspection and increasingly for pilot-line placement in difficult terrain; they speed surveys and reduce helicopter/time costs. For pilot line tasks drones are effective on some projects but require special rigging, experienced drone operators and regulatory approvals. SEO tip: create a “Drone-assisted Stringing” technical note + safety/regulation checklist.
Answer: Not fully yet — robots/automation reduce high-risk manual tasks (e.g., motorized reel stands, remote winches, clamp automation), but experienced crews are still essential for planning, complex rigging and safety oversight. Position your products as “automation-assisted” tools that increase productivity and safety.
Answer: Yes — modern puller–tensioner units now include remote-control and automation options for safer, repeatable tensioning on long spans and difficult terrain. These systems deliver remote start/stop, precise tension profiles and diagnostics to reduce on-tower exposure and human error. SEO tip: publish a product/feature page “Remote-control Puller–Tensioners — Features & Specs” with specs, remote range, and case photos.
Safety measures include pre-use equipment inspection, proper grounding, ensuring minimum clearance from live lines, using personal protective equipment, and following international standards such as IEEE, IEC, and OSHA guidelines.
Choosing the right stringing equipment depends on conductor type, project length, terrain, and voltage class. Key considerations include machine pulling capacity, tension control, mobility, and compatibility with project safety regulations.
Recent advancements in overhead stringing equipment include hydraulic tensioners with digital controls, eco-friendly engines, drone-assisted conductor monitoring, and automated pulling winches that improve both efficiency and operator safety.
Overhead transmission stringing equipment is vital in 2025 as global demand for renewable energy and grid expansion grows. These tools ensure faster project execution, reduced downtime, and enhanced safety for high-voltage line construction.
Stringing equipment in overhead transmission refers to specialized machinery and tools used for installing, tensioning, and securing conductors and ground wires on transmission towers. It ensures safe, efficient, and precise placement of power lines over long distances.
Many EPC contractors choose a hybrid approach—owning essential machines like pullers and tensioners while renting specialized tools when needed. This balances costs and project efficiency.
Renting is more cost-effective for short projects or small contractors, while buying is better for utilities or EPCs with frequent long-term use. A cost analysis of project duration vs equipment price helps decide.
Rental contracts usually include daily, weekly, or monthly terms, with maintenance covered by the rental company. Some providers offer operator training and on-site support for safe use
Purchasing is best for long-term, large-scale projects where equipment will be used frequently. Owning conductor stringing equipment ensures availability, customization, and lower lifetime costs compared to repeated rentals.
Renting stringing equipment offers cost savings, flexibility, and access to the latest tension stringing machines without long-term ownership costs. It is ideal for short-term projects or contractors working in multiple regions.
Annual audits should review PM compliance, NDT outcomes, spare parts consumption, dynamometer calibrations, incident history, training records, telemetry anomaly logs and budgeted replacements. Produce an audit report with prioritized CAPEX/OPEX recommendations.
Use a CMMS or cloud folder with timestamped work orders, photos, calibration certificates and signed approvals. Keep warranty-related records easily exportable and back up to secure, tamper-evident storage; retain records for the vendor-specified warranty period.
Maintenance staff should have OEM-certified training for each model, hydraulic and electrical troubleshooting skills, competency records, and refresher training annually. Include digital competence for telemetry tools and a documented certification matrix for audit purposes.
Use corrosion-resistant coatings, more frequent inspections, stainless fasteners where possible, and aggressive cleaning (freshwater wash) after salt exposure. Increase lubrication frequency and record corrosion checks in a dedicated log.
Define PM intervals by hours of operation and duty cycle: light use quarterly, moderate use bi-monthly, heavy/continuous use monthly. Include PM items: hydraulic fluid change, filter replacement, NDT as scheduled, and dynamometer check.
Follow manufacturer storage charge levels, avoid full discharge for long storage, use battery heaters in cold climates, and comply with IATA/IMDG for transport packaging and declarations. Keep battery health logs and replace cells showing capacity loss beyond OEM thresholds.
Get the latest price? We'll respond as soon as possible(within 12 hours)