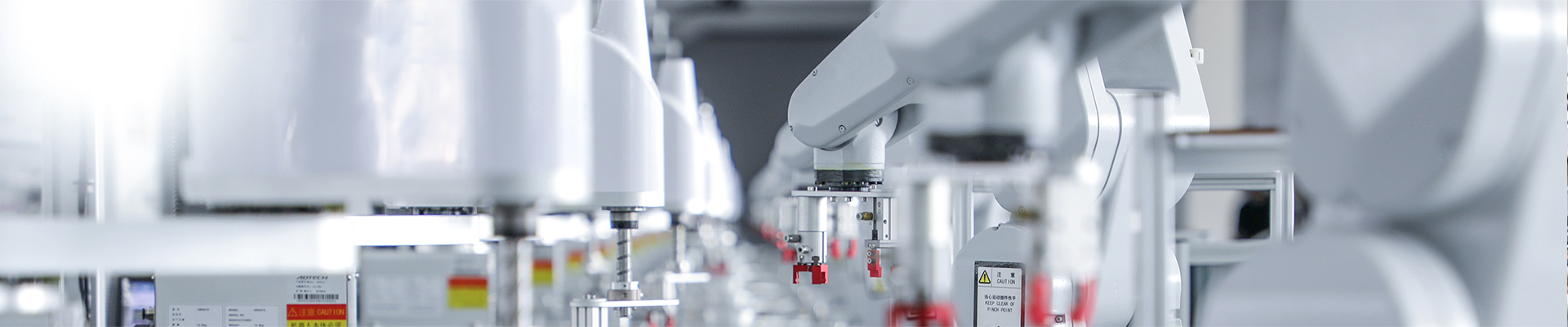
FAQ
Our "OPGW stringing equipment" is manufactured to meet rigorous international "safety standards" to ensure reliable and compliant operation worldwide:
-
ISO 9001 (Quality Management System): Ensures consistent quality control and adherence to documented manufacturing processes.
-
CE Marking (for European Union): Certifies conformity with EU health, safety, and environmental protection directives.
-
IEC (International Electrotechnical Commission) Guidelines: Relevant for electrical safety and performance, especially given the dual nature of OPGW.
-
Relevant ASME (American Society of Mechanical Engineers) Standards: For lifting and rigging components where applicable.
-
Built-in Safety Features: Including automatic over-tension release, emergency stop buttons, hydraulic fail-safe brakes, and operator protection guards, all designed to prevent accidents and protect personnel and equipment.
"OPGW stringing in mountainous terrain" demands specialized approaches and robust equipment features:
-
Portable & Modular Design: Equipment that can be easily transported, disassembled, and reassembled in remote or difficult-to-access locations (e.g., skid-mounted puller-tensioners, helicopter-transportable components).
-
Powerful Traction Systems: Machines with high tractive effort and stability, often with independent drive systems for enhanced maneuverability on slopes.
-
Longer Spans & Controlled Sag: Planning for longer spans to minimize the number of towers and thus setup points, while maintaining precise sag control to prevent cable damage.
-
Advanced Communication Systems: Reliable two-way communication among the stringing crew is crucial due to line-of-sight challenges in rugged terrain.
-
Specialized Auxiliary Tools: Such as heavy-duty gin poles, aerial cable carriers, and custom anchoring solutions adapted for rocky or uneven ground.
-
Experienced Operators: Highly trained personnel familiar with the unique challenges of mountain stringing are essential.
The "OPGW stringing equipment market" is dynamic:
-
Growing Demand for Smart Grids & Connectivity: The global push for smart grids and expanded fiber optic networks is a primary driver for OPGW deployment, directly increasing demand for specialized stringing equipment.
-
Automation & Digitalization: Increased adoption of automated processes, remote control, and data analytics in stringing operations to boost efficiency and safety.
-
Sustainability & Environmental Considerations: Demand for more energy-efficient equipment with lower emissions and reduced environmental impact.
-
Focus on Reliability & Longevity: Clients prioritize durable equipment with minimal downtime, capable of performing in diverse climatic conditions.
-
Comprehensive Solutions: A preference for suppliers who can provide not just the stringing machine but a complete suite of integrated tools, accessories, and after-sales support.
As a prominent China manufacturer, we are actively addressing these trends by investing in R&D for next-generation OPGW equipment, expanding our product range for comprehensive solutions, and enhancing our global service network.
Choosing us as your "China OPGW stringing equipment manufacturer and exporter" provides distinct advantages:
-
Specialized Expertise: Decades of experience focused specifically on power line and substation equipment, including the unique requirements of OPGW.
-
Cutting-Edge Technology: We continuously innovate, leveraging advanced manufacturing processes and incorporating the latest smart technologies into our OPGW equipment for superior performance.
-
Comprehensive One-Stop Supply: We offer a full range of OPGW stringing machines, along with all necessary specialized tools and accessories, streamlining your procurement and ensuring compatibility.
-
Competitive Global Pricing: Our efficient production scale in China allows us to provide high-quality OPGW equipment at very competitive international prices, delivering excellent value.
-
Robust Quality & International Compliance: All our products are manufactured to stringent international quality and safety standards (e.g., ISO, CE), ensuring reliability and broad market acceptance.
-
Dedicated Global After-Sales Support: We provide comprehensive technical assistance, training, and a reliable supply of spare parts to ensure the smooth and long-term operation of your OPGW stringing projects worldwide.
"OPGW pulling grips" (often referred to as 'pulling socks' or 'stockings') are specifically engineered to protect the delicate fiber optic core within the OPGW during the pulling process. Unlike standard conductor grips, they feature:
-
Distributed Gripping Force: They typically have a longer, braided or woven design that spreads the pulling force evenly over a greater length of the OPGW's outer metallic strands, preventing localized stress or crushing of the optical tube inside.
-
Precisely Sized Jaw Inserts: Some advanced grips use custom-sized, non-abrasive inserts to ensure a snug, yet non-damaging, fit for specific OPGW diameters.
-
Integrated Swivel Compatibility: Often designed to seamlessly integrate with anti-twist swivels to prevent any torsional forces from being transferred to the cable during the pull.
Using standard grips can easily damage the OPGW, leading to signal loss and costly repairs. OPGW-specific grips are indispensable for maintaining the cable's optical performance.
"Large diameter, non-metallic grooved sheaves" (stringing blocks) are fundamental "OPGW Stringing Tools" because they minimize the risk of damage to the cable:
-
Minimum Bending Radius: The larger diameter ensures the OPGW is never bent beyond its specified minimum bending radius, which is vital for preventing stress and micro-bending loss in the optical fibers.
-
Fiber Protection: The grooves are precisely designed and often lined with soft, yet durable, non-abrasive materials like polyurethane or high-density nylon. This prevents scratching, crushing, or deforming the OPGW's outer metallic strands, which could indirectly impact the internal fibers.
-
Smooth Operation: High-quality, sealed bearings ensure smooth rotation and low friction, reducing wear on the OPGW and minimizing pulling tension requirements.
These specialized sheaves safeguard the OPGW's structural and optical integrity throughout the stringing operation.
"Digital dynamometers" and "wireless tension links" are indispensable "OPGW Stringing Tools" for accurate and safe tension management:
-
Real-time Feedback: These tools provide instant, highly accurate digital readouts of the pulling or tensioning force applied to the OPGW.
-
Fiber Protection: Since OPGW has strict maximum tension limits, continuous monitoring prevents over-tensioning that could damage the delicate optical fibers or outer metallic layers. Many units can be integrated with puller-tensioners to trigger alarms or even automatic shutdowns if tension exceeds pre-set limits.
-
Sag Control: Precise tension readings are directly correlated to the OPGW's sag, allowing operators to achieve the exact sag specifications required for clearances and optimal electrical/optical performance.
-
Data Logging: Many models can log tension data, providing invaluable records for quality assurance, troubleshooting, and project documentation.
They are critical for ensuring the OPGW is installed to exact specifications without compromising its integrity.
Ensuring the optical integrity of the OPGW is crucial. "Fiber optic continuity testing tools" are used at various stages of stringing:
-
Visual Fault Locators (VFLs): Emit a visible laser light into the fiber. Any breaks, sharp bends, or poor connections will cause the light to escape, allowing for quick visual identification of issues.
-
Optical Loss Test Sets (OLTS) / Power Meters & Light Sources: Measure the overall optical loss (attenuation) of the fiber segment. This confirms that the signal strength is within acceptable limits after stringing, indicating no significant damage.
-
Optical Time Domain Reflectometers (OTDRs): These are advanced tools that provide a "picture" of the fiber length. They can pinpoint the exact location and severity of breaks, splices, or other defects within the fiber, allowing for immediate corrective action during or after stringing.
These tools provide immediate feedback, preventing costly reworks after installation and guaranteeing the communication functionality of the OPGW.
When OPGW is strung near or on energized lines (live-line stringing), specialized "insulated tools" and "hot stick accessories" are paramount for safety:
-
Insulated Pulling Grips/Clamps: Designed with insulating properties to prevent current flow from the conductor to the rigging personnel or other equipment.
-
Hot Stick Operable Tools: Including specialized clamps, hooks, and even "hot stick attachment points" on stringing blocks or other accessories, allowing linemen to manipulate components from a safe distance using insulated hot sticks.
-
Insulated Link Sticks & Spreader Bars: Used to maintain clearances and provide electrical isolation during lifting or positioning tasks.
-
Grounding Tools & Clamps: Essential for safely grounding any potentially induced voltages or fault currents on the OPGW or equipment.
These tools adhere to strict electrical safety standards, providing critical protection against electrocution and arc flash hazards.
Proper maintenance is crucial for the longevity and safety of "OPGW Stringing Tools":
-
Thorough Cleaning: After each use, clean all tools, especially sheave grooves, to remove dirt, grit, and debris that can cause abrasion.
-
Regular Inspection: Conduct daily visual inspections for signs of wear, cracks, deformation, corrosion, or damage. Pay close attention to critical areas like sling eyes, shackle pins, and sheave linings. Remove any damaged tool from service immediately.
-
Proper Lubrication: Lubricate moving parts (e.g., bearings in sheaves, shackle pins) according to manufacturer recommendations to reduce friction and wear.
-
Correct Storage: Store tools in a clean, dry, and protected environment, away from direct sunlight, extreme temperatures, and corrosive agents. Prevent tools from being dropped or tangled.
-
Adherence to WLL: Never exceed the stated Working Load Limit (WLL) of any tool.
-
Manufacturer Guidelines: Always follow the specific operation and maintenance guidelines provided by the tool manufacturer.
Consistent maintenance extends tool life, prevents costly replacements, and, most importantly, ensures the safety of your crew.
Choosing us as your "OPGW Stringing Tools" supplier from China offers distinct advantages:
-
Specialized Expertise: We possess deep knowledge and extensive experience in manufacturing tools precisely tailored for the unique requirements of OPGW installation, ensuring optimal cable protection.
-
Cost-Effectiveness & Value: Our efficient production scale and supply chain in China enable us to offer high-quality, durable OPGW tools at highly competitive international prices, providing excellent value.
-
Comprehensive One-Stop Solution: We provide a full range of OPGW stringing machines, equipment, and all necessary specialized tools and accessories, streamlining your procurement process.
-
Robust Quality Control: All our tools undergo rigorous quality control and testing to meet stringent international standards (e.g., ISO, CE), guaranteeing reliability and safety in diverse global environments.
-
Innovation & Advanced Materials: We continuously invest in R&D to incorporate the latest materials (e.g., advanced synthetics, non-metallic composites) and smart features into our tools, enhancing performance and longevity.
-
Reliable Global Logistics & Support: Our proven export experience ensures smooth, timely delivery worldwide, backed by dedicated technical support and readily available spare parts.
Yes, absolutely. As a prominent China manufacturer, we understand that OPGW projects can have unique requirements based on cable type, terrain, or specific installation methodologies. Our engineering and R&D teams are fully equipped to:
-
Design Bespoke Tools: Develop and fabricate "custom OPGW stringing tools" tailored to your exact specifications, including specialized pulling grips for unusual OPGW constructions, unique sheave designs for challenging angles, or custom hot stick attachments.
-
Adapt Existing Designs: Modify our standard tools to optimize performance for specific project parameters or environmental conditions.
-
Collaborate on Solutions: Work closely with your project engineers to provide innovative solutions for complex OPGW installation challenges.
This customization capability is a key differentiator, ensuring you have the precise tools needed for successful OPGW deployment.
"OPGW protection rods" and "armor rods" are crucial "OPGW Stringing Accessories" designed to safeguard the cable from mechanical stress and damage at points of attachment:
-
Protection Rods: These helical rods are applied over the OPGW at suspension points (like stringing blocks or suspension clamps). They increase the bending radius and distribute clamping forces over a longer area, preventing concentrated stress, abrasion, and fatigue that could damage the outer strands and ultimately the optical fibers.
-
Armor Rods: Used similarly, often pre-formed and applied at dead-end or tension points. They provide superior protection against abrasion and fatigue from vibration and tension, ensuring the OPGW maintains its structural and optical integrity under constant load.
Both are vital for extending the service life of the OPGW, especially in areas prone to wind-induced vibration or high tension.
"Vibration dampers" are critical "OPGW Stringing Accessories" that mitigate fatigue damage caused by wind-induced vibration (Aeolian vibration).
-
Energy Dissipation: These devices (e.g., Stockbridge dampers, spiral dampers) are strategically clamped onto the OPGW. When the cable vibrates, the damper's weights or specific design oscillate out of phase with the cable, absorbing and dissipating the vibrational energy.
-
Fatigue Prevention: This dampening action significantly reduces the dynamic bending stress at critical points like suspension clamps, where the OPGW is most susceptible to fatigue failure. Without effective dampening, prolonged vibration can lead to strand breakage and eventual failure of the entire OPGW cable.
Properly sized and installed OPGW vibration dampers are essential for ensuring the long-term mechanical and optical integrity of the line.
"OPGW guide clamps" and "downlead clamps" are specialized "OPGW Stringing Accessories" that manage the cable's path from the top of the tower to its termination point or splice enclosure:
-
Guide Clamps: Used during the stringing process to guide the OPGW along the tower structure, preventing it from swinging freely, hitting obstacles, or interfering with other conductors. They ensure a controlled descent.
-
Downlead Clamps: These are permanently installed clamps that secure the OPGW cable along the pole or tower leg. They ensure the cable follows a smooth, controlled path, preventing abrasion, excessive bending, or damage from wind and ice. They also maintain the minimum bending radius of the OPGW.
Both are essential for precise OPGW installation, preventing physical damage and maintaining aesthetic and safety clearances on the structure.
"Conductor counterweights" and "running boards" are "OPGW Stringing Accessories" used to manage tension and maintain clearance during specialized stringing operations:
-
Conductor Counterweights: These are strategically placed weights that can be attached to the pulling rope or a temporary pilot line during stringing. Their primary function is to increase sag on the pulling line, keeping it lower to the ground and preventing it from fouling on obstacles or other conductors, especially in areas with uneven terrain or crossings.
-
Running Boards: These are elongated, rigid frames with multiple rollers or sheaves that provide a stable platform for the OPGW and its associated pulling hardware to traverse structures or difficult sections. They ensure even tension distribution and prevent twisting or kinking of the OPGW as it moves.
These accessories are crucial for complex installations, reducing friction, minimizing stress on the OPGW, and enhancing overall stringing efficiency and safety.
"OPGW splice enclosures" and "fiber optic splice trays" are vital "OPGW Stringing Accessories" that protect the most critical part of the OPGW system – the optical connections:
-
Splice Enclosures: These robust, environmentally sealed housings (often rated IP67 or higher) protect the delicate optical splices from moisture, dust, extreme temperatures, UV radiation, and mechanical damage. They are designed for easy re-entry for maintenance.
-
Fiber Optic Splice Trays: Located inside the enclosure, these trays organize and secure the spliced optical fibers and any excess fiber length. They ensure the fibers are routed without exceeding their minimum bending radius, protecting the splices from physical stress and ensuring signal integrity.
-
Grounding and Bonding: Enclosures also provide secure grounding and bonding points for the metallic components of the OPGW.
These accessories are indispensable for maintaining the long-term optical performance and reliability of the OPGW communication link.
"Smart OPGW accessories" are at the forefront of grid modernization:
-
Integrated Sensors: These accessories can incorporate micro-sensors for real-time monitoring of parameters like cable temperature, sag, vibration levels, and even ice loading.
-
IoT Connectivity: Data from these sensors can be transmitted wirelessly (via cellular, satellite, or the OPGW's own fiber) to central control systems, leveraging the Internet of Things (IoT).
-
Predictive Maintenance: By continuously analyzing this data, utilities can move from reactive to predictive maintenance, identifying potential issues (e.g., excessive vibration indicating damper failure, high temperature indicating overload) before they become critical.
-
Enhanced Grid Awareness: Provides unprecedented insight into the real-time health and performance of the transmission line, improving reliability, optimizing power flow, and facilitating quicker fault location.
These accessories are transforming OPGW from just a ground wire into an intelligent data backbone for the power grid.
As a prominent "China manufacturer and exporter" of "OPGW stringing accessories," we offer significant advantages:
-
Superior Value: Our efficient production processes and established supply chain enable us to provide high-quality OPGW accessories at highly competitive global prices, maximizing your project budget.
-
Comprehensive Range: We offer a full spectrum of OPGW stringing accessories, from pulling grips and blocks to clamps, dampers, and splice enclosures, providing a convenient one-stop procurement solution.
-
Robust Quality & Reliability: All our accessories are manufactured to stringent international quality standards, ensuring durability and consistent performance in diverse environments.
-
Customization Capabilities: We can design and produce specialized OPGW accessories tailored to unique project specifications or non-standard OPGW cable types.
-
Proven Export Experience: Our extensive experience in international logistics ensures smooth, timely, and compliant delivery of accessories to your project sites worldwide.
-
Innovation: We continually invest in R&D to incorporate the latest material science and smart technologies into our accessories.
Ensuring our "OPGW stringing accessories" perform reliably worldwide is paramount:
-
Multi-Standard Compliance: We design and manufacture our accessories to meet or exceed relevant international standards such as IEC (International Electrotechnical Commission), IEEE (Institute of Electrical and Electronics Engineers) guidelines for OPGW hardware, and specific national standards (e.g., ANSI, BS, DIN) where required.
-
Premium Material Selection: We utilize high-grade materials like corrosion-resistant aluminum alloys, hot-dip galvanized steel, and UV-stabilized polymers, selected for their durability and performance in varying climates (e.g., extreme temperatures, high humidity, corrosive coastal environments).
-
Rigorous Testing: All accessories undergo extensive testing, including mechanical strength tests (tension, compression, fatigue), environmental tests (salt spray, UV exposure, temperature cycling), and electrical tests where applicable, to ensure they withstand the demands of global environments.
-
Design for Maintainability: Accessories are designed for easy inspection, installation, and replacement of components, contributing to long-term reliability and reduced maintenance costs for our international clients.