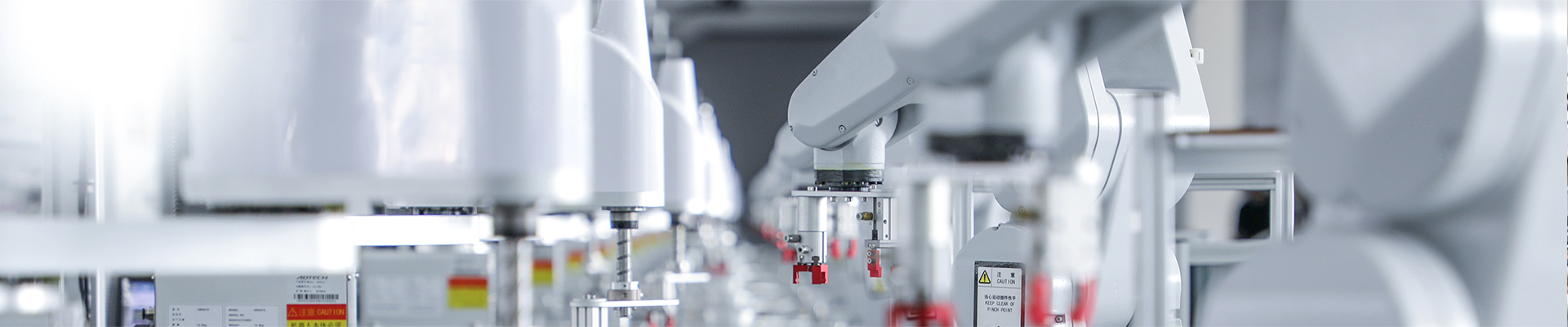
FAQ
"Wire stringing equipment" refers to the specialized machinery, tools, and accessories used for the efficient and safe installation of various types of conductors and cables for overhead and, in some cases, underground power transmission and distribution lines.
Its primary applications include:
-
Overhead Transmission Lines (OHTL): Installing high-voltage (HV), extra-high voltage (EHV), and ultra-high voltage (UHV) conductors, including single, bundled, and OPGW (Optical Ground Wire) cables. This often involves the precise "tension stringing" method to prevent ground contact and conductor damage.
-
Distribution Networks: Deploying smaller conductors and insulated cables for local power delivery.
-
Substation Construction: Facilitating the installation of busbars and connecting conductors within substations.
-
Renewable Energy Projects: Essential for connecting wind turbines and solar farms to the grid via new transmission lines.
-
Railway Electrification: Installing overhead catenary wires for electric trains.
Essentially, any project requiring the precise and safe deployment of long lengths of electrical or optical cable in infrastructure relies heavily on specialized wire stringing equipment.
While both are categories of "wire stringing equipment," the key distinction lies in the methodology and control:
-
Wire Pulling Equipment (General): This broader term encompasses any machinery (like winches, capstan pullers) designed to pull wire or cable. It might be used for simpler applications where precise tension control isn't critical, or where the conductor can be allowed to sag to the ground (e.g., initial pilot wire pulling, some underground cable pulling). The primary focus is on generating pulling force.
-
Tension Stringing Equipment: This is a specialized subset of wire pulling equipment used specifically for overhead line installation. It always involves a synchronized puller and tensioner (or a combined puller-tensioner) working in tandem to keep the conductor or wire elevated off the ground at a controlled, pre-set tension throughout the entire stringing process. This method is critical for protecting expensive conductors, maintaining safety clearances, and achieving precise sag profiles on transmission lines.
Our company specializes in sophisticated tension stringing equipment for OHTL, which inherently includes advanced wire pulling capabilities, ensuring maximum control and safety.
Modern "wire stringing equipment" is rapidly evolving with "smart technologies" and "automation features" to enhance efficiency, safety, and data management:
-
Real-time Digital Monitoring: Intuitive digital displays provide operators with precise, continuous data on pulling tension, speed, distance, engine diagnostics, and hydraulic parameters.
-
Automated Tension Control (ATC): Advanced closed-loop hydraulic and electronic systems automatically adjust pulling and tensioning forces to maintain a constant, pre-set tension, minimizing human error and ensuring cable integrity.
-
IoT (Internet of Things) Connectivity: Machines can transmit operational data wirelessly (e.g., via 4G/5G or satellite) to cloud-based platforms for remote monitoring, performance analysis, predictive maintenance, and streamlined project reporting.
-
Wireless Remote Control: Allows operators to control machines from a safe distance, improving visibility, coordination, and safety, especially in challenging terrain.
-
GPS Integration: For accurate tracking of equipment location, stringing progress, and georeferencing of installation data.
These innovations lead to more precise conductor installation, reduced labor costs, enhanced safety protocols, and valuable data for project optimization and asset management.
Yes, our "wire stringing equipment" is designed with adaptability for "challenging terrains" in mind:
-
Compact & Mobile Designs: We offer a range of sizes, including compact units optimized for transport via narrow access roads or even helicopter lifting in remote, mountainous areas. Some units are skid-mounted for easy placement.
-
High Traction & Stability: Machines feature robust chassis, powerful drivetrains (for self-propelled units), and often include hydraulic outriggers or anchoring points for stability on uneven or sloped ground.
-
Precise Control for Obstacles: The advanced hydraulic and electronic control systems allow for extremely fine speed and tension adjustments, essential for navigating complex obstacles such as river crossings (where tension must be precisely maintained) or congested urban areas (where clearances are tight).
-
Customizable Accessories: Compatibility with specialized stringing blocks, anti-twist devices, and auxiliary equipment designed for unique environmental challenges.
-
Remote Operation Capabilities: Our smart equipment with remote control options allows operators to manage stringing from a safer vantage point when working in hazardous or difficult-to-access locations.
We can also provide tailored solutions and advise on optimal equipment configurations for your specific project's geographical and environmental challenges.
Our "wire stringing equipment" is designed to deliver significant improvements in installation speed and "reduced operational costs":
-
High Power-to-Weight Ratio: Efficient engines and optimized hydraulic systems deliver high pulling/tensioning forces quickly, enabling faster stringing speeds over long distances.
-
Advanced Controls: Precise and intuitive controls minimize the need for manual adjustments and reduce the risk of errors, streamlining the operation.
-
Durability & Reliability: Robust construction using high-quality components ensures maximum uptime and fewer breakdowns, leading to less project delay and lower repair costs.
-
Fuel Efficiency: Modern engines and intelligent power management systems optimize fuel consumption, reducing operational expenses.
-
Minimized Cable Damage: The controlled stringing process drastically reduces damage to expensive conductors, preventing costly reworks and material waste.
-
Reduced Labor: Automated features and efficient design can often reduce the number of personnel required for certain tasks, lowering labor costs.
By combining advanced engineering with user-centric design, our equipment maximizes productivity and delivers substantial cost savings over the lifespan of your projects.
-
Safety is our top priority, and our "wire stringing equipment" incorporates multiple critical "safety features":
-
Automatic Overload Protection: Systems that automatically detect and prevent pulling or tensioning forces from exceeding pre-set safe limits, protecting the conductor from damage and preventing equipment strain.
-
Emergency Stop Systems: Strategically placed, easily accessible emergency stop buttons (often multiple locations including remote controls) that instantly halt all machine operations.
-
Fail-Safe Braking Systems: Hydraulic braking systems are designed to engage automatically in the event of engine shutdown or hydraulic pressure loss, preventing uncontrolled movement of the conductor.
-
Operator Guarding & Ergonomics: Protective cages, safety barriers, and ergonomic control panels that provide a safe and comfortable working environment for operators.
-
Audible & Visual Alarms: Clear alerts for critical conditions such as over-tension, low fluid levels, or system malfunctions.
-
Robust Grounding Points: Clear and accessible terminals for proper earthing of the equipment to manage static build-up and fault currents.
-
Compliance: Designed and manufactured to stringent international safety standards (e.g., CE, relevant IEC guidelines).
-
-
These features are integral to minimizing risks, preventing accidents, and ensuring a safe working environment on dynamic power line construction sites.
Yes, our "wire stringing equipment" is designed with adaptability for "challenging terrains" in mind:
-
Compact & Mobile Designs: We offer a range of sizes, including compact units optimized for transport via narrow access roads or even helicopter lifting in remote, mountainous areas. Some units are skid-mounted for easy placement.
-
High Traction & Stability: Machines feature robust chassis, powerful drivetrains (for self-propelled units), and often include hydraulic outriggers or anchoring points for stability on uneven or sloped ground.
-
Precise Control for Obstacles: The advanced hydraulic and electronic control systems allow for extremely fine speed and tension adjustments, essential for navigating complex obstacles such as river crossings (where tension must be precisely maintained) or congested urban areas (where clearances are tight).
-
Customizable Accessories: Compatibility with specialized stringing blocks, anti-twist devices, and auxiliary equipment designed for unique environmental challenges.
-
Remote Operation Capabilities: Our smart equipment with remote control options allows operators to manage stringing from a safer vantage point when working in hazardous or difficult-to-access locations.
We can also provide tailored solutions and advise on optimal equipment configurations for your specific project's geographical and environmental challenges.
Partnering with us for your "wire stringing equipment" offers significant advantages to international clients:
-
Specialized Expertise & Innovation: With decades of experience exclusively in power line equipment, we possess deep technical knowledge and continuously integrate the latest innovations in smart technology, hydraulics, and materials science into our designs.
-
Comprehensive One-Stop Solution: We are unique in offering a full spectrum of overhead transmission line (OHTL) and underground cable laying equipment, tools, and accessories. This streamlines your procurement, logistics, and ensures seamless compatibility across all your needs.
-
Exceptional Value & Cost-Effectiveness: Leveraging our advanced manufacturing capabilities, economies of scale, and optimized supply chain in China, we deliver high-quality, high-performance wire stringing equipment at globally competitive prices, maximizing your project's ROI.
-
Robust Quality Assurance & Compliance: All our equipment is manufactured under stringent ISO 9001 quality management systems and holds international certifications (e.g., CE marking, adherence to relevant IEC standards), ensuring reliability, safety, and broad market acceptance.
-
Dedicated Global After-Sales Support: We commit to long-term partnerships, providing comprehensive technical support, operator training, readily available spare parts, and efficient logistics to ensure the continuous success and minimal downtime of your international projects.
We provide robust "maintenance, spare parts, and technical assistance" for our "wire stringing equipment" to ensure long-term operational success globally:
-
Comprehensive Documentation: Each piece of equipment comes with detailed operation, maintenance, and spare parts manuals, available in multiple languages where possible.
-
Dedicated Technical Support: Our expert technical team is available via phone, email, and video conference to provide remote troubleshooting, operational guidance, and technical consultations.
-
Global Spare Parts Distribution: We maintain a comprehensive inventory of genuine spare parts and critical components, ensuring rapid dispatch to any location worldwide to minimize equipment downtime.
-
Operator Training: We can provide tailored training programs (on-site or remote) for your operational and maintenance personnel to ensure they are fully proficient in using, maintaining, and basic troubleshooting of our equipment.
-
Service Network Development: We are actively expanding our network of authorized service partners and distributors in key regions to offer localized support and maintenance services.
-
Warranty & Follow-up: All our equipment is backed by a comprehensive warranty, and our after-sales team conducts regular follow-ups to ensure client satisfaction and address any ongoing needs
"Conductor stringing equipment" refers to the specialized machinery and tools used to install electrical conductors (such as ACSR, AAAC, HTLS, OPGW) on overhead transmission and distribution lines. The process involves pulling the conductor from a reel, guiding it over stringing blocks on towers, and finally tensioning it to achieve the correct sag.
Tension stringing is the preferred modern method because it:
-
Prevents Conductor Damage: Keeps the conductor elevated off the ground and away from obstacles, preventing scratches, nicks, or crushing that can compromise its electrical and mechanical integrity.
-
Enhances Safety: Maintains safe clearances over roads, railways, existing energized lines, and other infrastructure, significantly reducing risks to personnel and property.
-
Achieves Precise Sag Control: Allows for accurate application of tension to meet specific sag and clearance requirements, crucial for line performance and avoiding overstressing the conductor or structures.
-
Increases Efficiency: Enables faster installation over long spans and challenging terrains compared to traditional methods, leading to reduced project timelines and costs.
A complete "conductor stringing equipment" system typically consists of highly synchronized machines working together:
-
Hydraulic Puller: Located at the start of the stringing section, this machine generates the controlled pulling force. It typically pulls a pilot rope (often steel anti-twist wire rope), which is then connected to the conductor. Our pullers offer infinitely variable speed control and can be pre-set for maximum pulling force.
-
Hydraulic Tensioner: Positioned at the other end of the section, the tensioner applies a precise, continuous back tension to the conductor as it's being pulled. This crucial function prevents the conductor from sagging uncontrollably or touching the ground.
-
Conductor Reel Stands (Drum Stands): These robust stands support the large conductor reels, allowing them to rotate freely while often incorporating braking systems to manage payout or add additional back tension.
-
Stringing Blocks (Sheaves): Specialized, large-diameter pulleys with non-abrasive linings mounted on the towers to guide the conductor smoothly and protect its surface during the pull.
-
Pulling Grips & Swivels: Connect the conductor to the pulling rope and prevent torsional stress during stringing.
-
Communication System: Essential for continuous, clear coordination between the puller and tensioner operators, often via two-way radios or interlinked digital systems.
These components are designed to work seamlessly, ensuring a controlled, safe, and efficient conductor installation process.
-
Our "conductor stringing equipment" incorporates cutting-edge "smart control systems" and "IoT integration" to revolutionize power line construction:
-
Automated Tension Regulation: The system automatically maintains a constant, pre-set tension by precisely adjusting hydraulic output, minimizing manual intervention and ensuring consistent quality.
-
Real-time Data Monitoring: Operators have instant access to critical parameters like pulling force, tension, speed, distance, engine diagnostics, and hydraulic pressure on intuitive digital displays.
-
IoT Connectivity: Machines can transmit real-time operational data wirelessly to cloud-based platforms. This enables remote monitoring, predictive maintenance, and comprehensive data logging for quality assurance, project optimization, and compliance reporting.
-
Remote Control Capabilities: Allows operators to manage the stringing process from a safer vantage point, improving visibility and coordination, especially in challenging or hazardous environments.
-
Integrated Diagnostics: Self-diagnostic features can identify potential issues early, reducing downtime and simplifying troubleshooting.
-
-
These advancements lead to superior precision, enhanced safety, reduced operational costs through optimized performance, and invaluable data insights for modern grid development.
Our "conductor stringing equipment" is specifically engineered to handle the unique demands of "bundle conductors" and "HTLS conductors":
-
High Rated Capacities: We offer pullers and tensioners with high pulling and tensioning capacities (e.g., up to 4x50 kN or more) to manage the increased weight and tension requirements of multiple sub-conductors in a bundle or the specialized HTLS materials.
-
Multi-Conductor Bullwheels: Our tensioners often feature bullwheels with multiple precisely machined grooves or separate bullwheel sets to accommodate 2, 3, 4, or even more sub-conductors simultaneously, ensuring even tension distribution.
-
Large Bullwheel Diameter: Crucially, the bullwheel diameters are generously sized (e.g., typically 35 times the conductor diameter or more) to prevent excessive bending stress on the large-diameter HTLS cables or the individual sub-conductors in a bundle, thus protecting their integrity.
-
Specialized Linings: The bullwheel grooves are lined with durable, non-abrasive materials (e.g., high-density polyurethane) to prevent surface damage to the advanced materials of HTLS conductors or the outer strands of bundle conductors.
-
Precision Control: The advanced hydraulic and electronic controls provide the fine-tuned speed and tension regulation essential for the delicate handling of these high-performance conductors.
These specialized capabilities ensure efficient, safe, and damage-free installation of even the most technologically advanced and complex conductor configurations.
Safety is the cornerstone of our "conductor stringing equipment" design:
-
Automatic Over-Tension/Over-Pull Protection: Our machines feature intelligent systems that monitor tension/pulling force in real-time. If pre-set maximum limits are exceeded, the system automatically slows down or stops, preventing damage to the conductor, line hardware, and the equipment itself.
-
Emergency Stop Buttons: Multiple, clearly marked emergency stop buttons are strategically placed for immediate shutdown in critical situations.
-
Fail-Safe Braking Systems: The hydraulic braking system is designed to automatically engage and hold tension in the event of engine failure, hydraulic pressure loss, or an emergency stop, preventing uncontrolled conductor movement.
-
Enclosed Operator Cabs & Safety Guards: Many models offer enclosed, climate-controlled cabs with excellent visibility for operator comfort and protection. All moving parts are guarded to prevent accidental contact.
-
Built-in Grounding Provisions: Easily accessible and robust grounding terminals are provided for proper electrical earthing of the machine.
-
Comprehensive Alarms: Audible and visual alarms alert operators to critical conditions such as low fuel, hydraulic issues, or tension excursions.
-
Compliance with International Standards: All equipment is designed and manufactured in strict adherence to relevant international safety and performance standards (e.g., CE marking, IEC guidelines).
We are committed to fostering "sustainability" in power line construction:
-
Fuel Efficiency: Our modern diesel engines are chosen for their high fuel efficiency, reducing fuel consumption and associated emissions during operation.
-
Reduced Noise Emissions: Engine and hydraulic system designs are optimized to minimize noise pollution, a critical factor for projects in urban or environmentally sensitive areas.
-
Hybrid & Electric Options: We are actively developing and offering "electric tension stringing equipment" and hybrid models. These provide zero local emissions, lower operating noise, and reduced reliance on fossil fuels, aligning with global green initiatives.
-
Durable & Recyclable Materials: We prioritize the use of high-quality, long-lasting materials in our equipment, extending product lifespan and minimizing waste. We also consider the recyclability of components at end-of-life.
-
Minimized Environmental Footprint: By enabling precise tension stringing, our equipment helps prevent ground contact, reducing disturbance to ecosystems, agricultural land, and public areas.
Our dedication to sustainability ensures that our conductor stringing solutions not only deliver performance but also contribute to a greener future for energy infrastructure.
Partnering with us for your "conductor stringing equipment" offers significant advantages to international clients:
-
Specialized Expertise & Innovation: With decades of concentrated experience in power line construction equipment, we are leaders in designing and manufacturing advanced, application-specific conductor stringing solutions, incorporating the latest hydraulic, electronic, and smart technologies.
-
Comprehensive One-Stop Supply: We provide a complete range of OHTL tension stringing equipment, underground cable laying equipment, and all necessary tools and accessories from a single source, simplifying your procurement and logistics.
-
Exceptional Value & Cost-Effectiveness: Leveraging our state-of-the-art manufacturing facilities, efficient production processes, and optimized supply chain in China, we deliver high-quality, high-performance conductor stringing equipment at globally competitive prices, ensuring excellent return on your investment.
-
Robust Quality Assurance & International Compliance: All our equipment undergoes rigorous testing and adheres strictly to international quality management systems (ISO 9001) and relevant safety and performance standards (e.g., CE marking, IEC guidelines), guaranteeing reliability and broad market acceptance.
-
Dedicated Global After-Sales Support: We are committed to your long-term success, offering comprehensive technical support, expert operator training programs, readily available genuine spare parts, and efficient global logistics to minimize downtime and ensure continuous project progress worldwide.
We are dedicated to providing robust "after-sales service" and support for our "conductor stringing equipment" to ensure maximum operational uptime for our international customers:
-
Technical Support: Our highly experienced technical team is available for remote troubleshooting, operational guidance, and technical consultations via phone, email, and video conference.
-
Operator & Maintenance Training: We offer comprehensive training programs, which can be conducted remotely or on-site, to ensure your personnel are fully proficient in operating, maintaining, and performing basic troubleshooting on our equipment.
-
Genuine Spare Parts Availability: We maintain a significant inventory of genuine spare parts and critical wear-and-tear components, ensuring rapid dispatch to any location worldwide to minimize any potential downtime.
-
Detailed Documentation: Each machine is supplied with comprehensive operation and maintenance manuals, spare parts catalogs, and electrical/hydraulic schematics, often available in multiple languages.
-
Warranty & Follow-up: All our conductor stringing equipment comes with a strong manufacturer's warranty, and our dedicated after-sales team provides proactive follow-up to address any ongoing needs or concerns.
Our commitment extends beyond the sale, ensuring you receive continuous, reliable support for the entire lifespan of your equipment.
"Tension stringing" is indeed the universally recognized best practice for high-voltage transmission lines due to its unparalleled benefits in safety, conductor integrity, and quality:
-
Conductor Protection: By maintaining the conductor continuously elevated above the ground and obstacles, tension stringing virtually eliminates scraping, kinking, or damaging the conductor's surface. This preserves its electrical properties (e.g., minimizing corona losses) and mechanical strength, crucial for expensive, high-performance conductors.
-
Enhanced Safety: It drastically reduces the risk of accidental contact with energized lines, roads, railways, or other infrastructure. Crews work with a controlled and predictable environment, minimizing hazards for personnel and the public.
-
Precise Sag and Tension Control: The synchronized operation of pullers and tensioners allows for exact control of conductor tension throughout the entire stringing process. This ensures the conductor is installed to its precise design sag, which is vital for maintaining clearance requirements and optimizing line performance and lifespan.
-
Efficiency on Complex Terrains: It allows for efficient conductor installation over diverse and challenging topographies, including mountainous regions, river crossings, and urban environments, where ground-level stringing would be impractical or unsafe.
This method guarantees the highest quality installation, maximizing the lifespan and reliability of the transmission line.
"Smart technologies" and "IoT integration" are revolutionizing "transmission stringing equipment," bringing unprecedented levels of precision, safety, and operational intelligence:
-
Automated Tension & Speed Control: Advanced algorithms and hydraulic systems automatically adjust pull and tension to maintain pre-set values, compensating for varying conditions and significantly reducing human error.
-
Real-time Data Analytics: Integrated sensors provide continuous, precise data on pulling force, tension, speed, distance strung, engine performance, and hydraulic parameters, all displayed on intuitive HMI screens.
-
IoT Connectivity & Remote Monitoring: Equipment can transmit operational data wirelessly to cloud platforms, enabling remote supervision, predictive maintenance scheduling, and comprehensive project performance analysis from anywhere in the world.
-
Enhanced Safety Protocols: Automated warnings, intelligent emergency stop systems, and self-diagnostic features detect anomalies and prevent overloads or malfunctions, significantly enhancing site safety.
-
Digital Documentation: Automatic logging of all stringing parameters provides an immutable record for quality assurance, regulatory compliance, and future project optimization.
These innovations empower operators with superior control, reduce operational risks, and provide valuable data for optimizing complex transmission line projects.
Our "transmission stringing equipment" is engineered to excel in the installation of challenging "multi-bundle conductors" and "HTLS conductors":
-
High-Capacity Design: Our pullers and tensioners are available with very high pulling and tensioning forces (e.g., SA-YZ4X50 for 4x50kN or SA-YQ300 for 300kN pull), necessary for the increased weight and tension of multiple sub-conductors or the specialized HTLS materials.
-
Optimized Bullwheel Design: Features large-diameter bullwheels (up to 1600mm or more) with multiple precisely machined and abrasion-resistant grooves (often MC nylon or polyurethane lined). This minimizes bending stress, prevents surface damage to sensitive HTLS conductors, and ensures even tension distribution across all sub-conductors in a bundle.
-
Dedicated Bundle Stringing: Some models are specifically designed with separate or easily convertible bullwheel configurations for simultaneous stringing of 2, 3, 4, or even 6 bundled conductors, maintaining their relative positions.
-
Advanced Control Precision: Our hydraulic systems provide the extremely fine speed and tension regulation critical for the delicate handling of HTLS conductors, which have unique thermal and mechanical characteristics.
-
Heavy-Duty Construction: Built with reinforced frames and components to withstand the rigorous forces and continuous operation associated with these demanding applications.
These features ensure that even the most advanced and complex conductor types can be strung safely, efficiently, and without compromising their integrity.