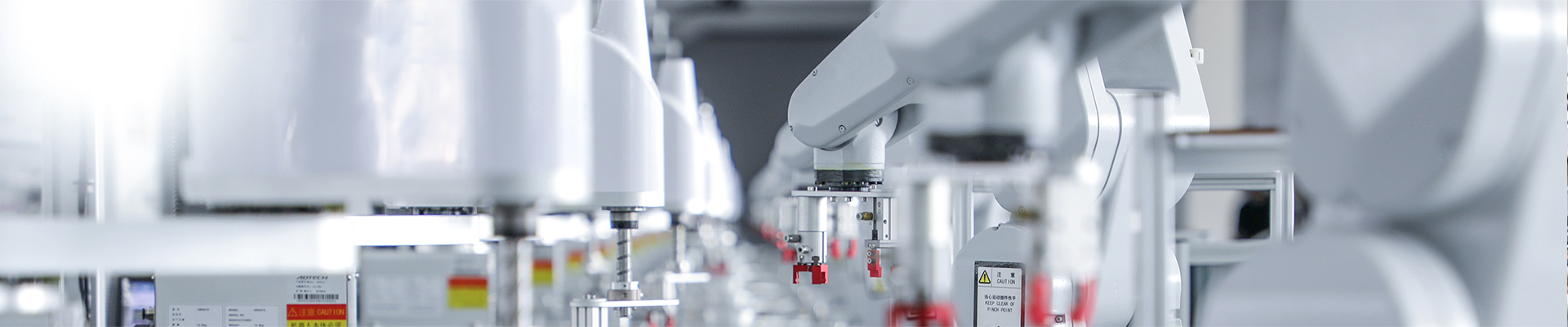
FAQ
For work in substations or on power lines where energized components are present, "insulated rigging links" and "hot stick attachment points" are crucial "Cable Rigging Accessories" for preventing electrical hazards:
-
Electrical Isolation: Insulated links provide a dielectric barrier, preventing the flow of current through the rigging system to personnel or equipment. They are rated for specific voltages.
-
Remote Operation: "Hot stick attachment points" allow linemen to manipulate rigging components (e.g., open/close hooks, attach slings) from a safe distance using insulated hot sticks, eliminating direct contact with potential live parts.
These specialized accessories are indispensable for maintaining safe working clearances and protecting personnel during sensitive rigging operations near energized infrastructure.
While often overlooked, the right "safety latch hooks" and "fall protection connectors" are critical "Cable Rigging Accessories" for preventing accidents:
-
Safety Latch Hooks: Feature a spring-loaded latch that automatically closes and locks over the hook opening, preventing the sling or load from inadvertently disengaging, even under slack conditions or shock loads. Options include self-locking hooks for added security.
-
Fall Protection Connectors: These are integral components of a personal fall arrest system for workers operating at height during rigging. They include specialized carabiners, snap hooks, and D-rings designed to withstand significant forces and prevent accidental disengagement, connecting harnesses to anchor points or lifelines.
These accessories significantly reduce the risk of dropped loads and personnel falls, which are major safety concerns in power line and substation work.
The demand for faster project completion drives the use of "quick-attach rigging hardware" and "modular rigging connectors." These "Cable Rigging Accessories" are designed for rapid, secure assembly and disassembly:
-
Reduced Setup Time: Features like quick-release pins, captive nuts, or cam-lock mechanisms allow for faster connection and disconnection of slings, shackles, and other components.
-
Increased Adaptability: Modular systems allow rigging configurations to be quickly altered or expanded to suit varying load shapes, sizes, and lifting requirements without needing entirely new setups.
-
Streamlined Logistics: Easier to transport and organize, reducing on-site clutter and improving workflow.
This trend directly impacts project efficiency, especially in dynamic construction environments.
Optical Ground Wire (OPGW) and other fiber optic cables are highly sensitive and require specific "Cable Rigging Accessories" to prevent damage to their delicate internal fibers:
-
Specialized OPGW Pulling Grips/Socks: Designed to evenly distribute gripping force over the metallic outer sheath without crushing the inner optical core.
-
Large Radius Sheaves/Blocks: Rigging blocks with larger diameters and ultra-smooth, often non-metallic (e.g., polyurethane, nylon) linings to minimize bending stress and surface abrasion on the cable.
-
Anti-Twist Swivels: High-quality, low-friction swivels designed to prevent any torsional stress from being transferred to the OPGW during lifting or pulling.
-
Precise Load Limiting Devices: Often integrated into the pulling system or as standalone accessories, ensuring that pulling tension never exceeds the OPGW's specified limits.
These accessories are vital for preserving the integrity and performance of fiber optic cables.
As synthetic slings become more prevalent, "synthetic rope protectors" and "sling covers" are vital "Cable Rigging Accessories" for extending their lifespan:
-
High-Abrasion Resistant Materials: Made from durable materials like Cordura, Dyneema, or specialized composites that shield slings from sharp edges, rough surfaces, and abrasive environments.
-
Anti-Chafe Sleeves: Designed to prevent friction wear where slings pass over or around loads or other rigging components.
-
Cut-Resistant Guards: Offering enhanced protection against cuts from sharp corners or burrs on loads.
-
Magnetic or Velcro Attachments: For quick and secure positioning of protectors on slings or around loads.
These accessories significantly reduce wear and tear, lowering replacement costs and enhancing the safety margin of synthetic rigging tools.
Choosing us for your "Cable Rigging Accessories" offers numerous benefits to clients worldwide:
-
Competitive Pricing & High Value: Our robust manufacturing capabilities in China allow us to provide a wide array of high-quality rigging accessories at very competitive price points, ensuring excellent ROI.
-
Comprehensive One-Stop Solution: We offer a full range of rigging equipment, tools, and accessories, alongside our OHTL stringing and underground cable laying solutions, simplifying your procurement and logistics.
-
Global Standard Compliance: Our accessories are manufactured to stringent international quality and safety standards (e.g., ISO, CE, relevant ASME B30 guidelines), ensuring reliability and acceptance in various markets.
-
Customization & Specialization: We have the expertise to design and fabricate bespoke rigging accessories for unique project challenges or highly specialized applications.
-
Durable & Innovative Products: We invest in R&D to use advanced materials and incorporate smart technologies, ensuring our accessories are robust, long-lasting, and efficient.
-
Reliable International Logistics & Support: Our extensive export experience guarantees smooth, timely delivery and dedicated after-sales support globally.
While sharing core tensioning and pulling principles, an "OPGW Stringing Machine" is engineered with crucial specializations due to the delicate fiber optic core within the OPGW cable:
-
Ultra-Precise Tension Control: OPGW has a much lower permissible tension limit than traditional conductors before its optical fibers can be damaged. Our OPGW machines feature highly sensitive hydraulic or electronic control systems for constant, low-tension stringing.
-
Specialized Sheaves/Grooves: Tension wheels and stringing blocks (sheaves) on OPGW machines have larger diameters and often feature non-metallic, extra-smooth, or specially lined grooves (e.g., polyurethane, nylon) to prevent crushing, kinking, or abrasion of the cable's outer strands, which could damage the optical fibers.
-
Integrated Anti-Twist Mechanisms: Many OPGW machines and accessories incorporate sophisticated anti-twist devices and swivels designed to prevent torsional stress on the cable, which is critical for optical fiber integrity.
-
Advanced Dynamometers: Equipped with highly accurate digital dynamometers that provide real-time tension feedback and often have automatic shutdown features to prevent over-tensioning.
This specialization is crucial because any damage to the OPGW's outer layers or induced stress on the fibers can lead to signal loss, increased attenuation, and ultimately, system failure.
An "OPGW hydraulic puller-tensioner" is specifically designed to protect the delicate optical fibers:
-
Closed Hydraulic Circuit: Provides precise, stepless speed and tension control, allowing for extremely smooth and consistent cable payout or pull-in, eliminating sudden jerks or tension spikes.
-
Electronic Control & Feedback: Advanced electronic systems monitor and regulate tension, often with pre-set tension limits and automatic emergency braking/shutdown if limits are exceeded.
-
Large Diameter Bullwheels: Minimizes the bending radius of the OPGW, crucial for preventing stress on the optical fibers.
-
Multi-Grooved, Lined Bullwheels: The bullwheels are typically multi-grooved and lined with wear-resistant, non-abrasive materials (like specific rubber compounds or urethane) to cushion and grip the OPGW without damaging its surface.
-
Integrated Anti-Twist System Compatibility: Designed to work seamlessly with anti-twist swivels at the pulling head, preventing rotational forces from being transmitted to the cable.
These features collectively ensure the OPGW is installed under optimal conditions to preserve its optical performance.
An "OPGW hydraulic puller-tensioner" is specifically designed to protect the delicate optical fibers:
-
Closed Hydraulic Circuit: Provides precise, stepless speed and tension control, allowing for extremely smooth and consistent cable payout or pull-in, eliminating sudden jerks or tension spikes.
-
Electronic Control & Feedback: Advanced electronic systems monitor and regulate tension, often with pre-set tension limits and automatic emergency braking/shutdown if limits are exceeded.
-
Large Diameter Bullwheels: Minimizes the bending radius of the OPGW, crucial for preventing stress on the optical fibers.
-
Multi-Grooved, Lined Bullwheels: The bullwheels are typically multi-grooved and lined with wear-resistant, non-abrasive materials (like specific rubber compounds or urethane) to cushion and grip the OPGW without damaging its surface.
-
Integrated Anti-Twist System Compatibility: Designed to work seamlessly with anti-twist swivels at the pulling head, preventing rotational forces from being transmitted to the cable.
These features collectively ensure the OPGW is installed under optimal conditions to preserve its optical performance.
An "OPGW hydraulic puller-tensioner" is specifically designed to protect the delicate optical fibers:
-
Closed Hydraulic Circuit: Provides precise, stepless speed and tension control, allowing for extremely smooth and consistent cable payout or pull-in, eliminating sudden jerks or tension spikes.
-
Electronic Control & Feedback: Advanced electronic systems monitor and regulate tension, often with pre-set tension limits and automatic emergency braking/shutdown if limits are exceeded.
-
Large Diameter Bullwheels: Minimizes the bending radius of the OPGW, crucial for preventing stress on the optical fibers.
-
Multi-Grooved, Lined Bullwheels: The bullwheels are typically multi-grooved and lined with wear-resistant, non-abrasive materials (like specific rubber compounds or urethane) to cushion and grip the OPGW without damaging its surface.
-
Integrated Anti-Twist System Compatibility: Designed to work seamlessly with anti-twist swivels at the pulling head, preventing rotational forces from being transmitted to the cable.
These features collectively ensure the OPGW is installed under optimal conditions to preserve its optical performance.
-
"Real-time tension monitoring systems" are fundamental to safe and precise OPGW stringing. These systems, integrated with digital dynamometers, provide continuous, accurate feedback on the pulling or tensioning force applied to the OPGW:
-
Precise Sag Control: By correlating tension directly to sag (using pre-calculated sag-tension charts for specific OPGW types and temperatures), operators can achieve the exact sag required, ensuring clearances and optimal performance.
-
Fiber Protection: Immediate alerts if tension approaches the cable's maximum permissible limits, allowing operators to reduce tension and prevent irreversible damage to the optical fibers.
-
Safety Against Overload: Prevents machine overload and potential structural failure, protecting both personnel and equipment.
-
Data Logging: The ability to log tension data throughout the stringing process provides invaluable records for quality assurance, troubleshooting, and future project planning.
-
Stringing OPGW in "challenging terrains" (mountainous, forested, swampy) demands specialized machine design:
-
Compact & Lightweight Design: Many OPGW stringing machines, particularly smaller capacity models, are designed to be highly portable, often trailer-mounted or with skid bases for easy transport by smaller vehicles or even helicopters to remote sites.
-
Independent Drive Systems: Individual hydraulic motors for each bullwheel or capstan provide enhanced traction and control, especially on uneven ground.
-
Robust Chassis & Undercarriage: Engineered for durability to withstand rough terrain and difficult access roads.
-
Remote Control Options: Allows operators to control the machine from a safe and advantageous position, especially important in hazardous or difficult-to-access areas.
-
Integrated Leveling Systems: Some machines include hydraulic leveling features to ensure stable operation on sloped ground.
These features ensure that OPGW can be reliably and safely installed even in the most inaccessible locations.
Our "OPGW stringing machines" prioritize safety:
-
Automatic Over-Tension Shutdown: The machine automatically stops if the pulling or tensioning force exceeds a pre-set maximum, preventing damage to the OPGW fibers and preventing catastrophic failures.
-
Emergency Stop Buttons: Strategically located for immediate machine shutdown in emergencies.
-
Fail-Safe Braking Systems: In case of power loss or hydraulic failure, the braking system automatically engages to hold the cable securely.
-
Operator Protection Guards: Physical barriers around rotating parts and bullwheels to prevent entanglement.
-
Hydraulic Pressure Relief Valves: Prevent over-pressurization of the hydraulic system.
-
Integrated Grounding Points: For proper earthing of the machine to dissipate induced currents, enhancing safety in energized environments.
-
Clear Operational Controls & Indicators: Intuitive controls and visible gauges (tension, speed, engine status) for safe and informed operation.
Successful "OPGW stringing" relies on adhering to strict "best practices":
-
Thorough Pre-Job Planning: Detailed route survey, sag-tension calculations, equipment selection, and a comprehensive Job Safety Analysis (JSA).
-
Proper Equipment Setup: Correct machine alignment, secure anchoring, and proper grounding of all equipment.
-
Use of OPGW-Specific Tools & Accessories: Utilizing specialized stringing blocks, anti-twist swivels, and pulling grips designed for OPGW.
-
Constant Tension Monitoring: Continuously monitoring tension via the machine's dynamometer to stay within the OPGW's limits.
-
Controlled Speed: Maintaining a consistent, appropriate stringing speed, often slower than for traditional conductors, to avoid dynamic stresses.
-
Minimum Bending Radius Adherence: Ensuring the OPGW cable is never bent below its specified minimum bending radius at any point.
-
Cable Protection: Avoiding any contact of the OPGW with the ground or obstacles during stringing.
-
Experienced Personnel: Employing and properly training operators and crew members experienced in OPGW installation.
The "OPGW stringing machine market" is seeing several key trends in 2024-2025:
-
Increased Demand for Optical Connectivity: Global expansion of communication networks and smart grid initiatives continues to drive OPGW deployment.
-
Focus on Automation & Digitalization: Integration of smart sensors, remote control, and data analytics for enhanced precision, safety, and efficiency.
-
Development of Lighter, More Portable Machines: For easier deployment in challenging and remote terrains.
-
Emphasis on Eco-Friendly Operations: Machines with lower emissions and reduced noise levels.
-
Demand for Comprehensive Solutions: Clients seek suppliers who can offer not just the machine, but also all related tools, accessories, and technical support.
Our company is addressing these trends by continuously investing in R&D for smarter, more versatile, and environmentally conscious OPGW stringing solutions, ensuring we remain at the forefront of the market.
Our position as a leading "China OPGW stringing equipment manufacturer and exporter" provides unique advantages:
-
Specialized Expertise: Deep understanding and extensive experience in designing and manufacturing equipment tailored specifically for OPGW's unique requirements.
-
Cutting-Edge Technology: We leverage advanced manufacturing capabilities and continuous innovation to deliver state-of-the-art OPGW stringing machines with superior precision and control.
-
Comprehensive One-Stop Supply: We offer a full range of OPGW stringing equipment, along with all necessary tools and accessories, providing a complete solution from a single, reliable source.
-
Cost-Effectiveness & Value: Our efficient production processes enable us to offer high-quality OPGW machines at competitive global prices, ensuring excellent return on investment.
-
Robust Quality & International Compliance: Our equipment is built to rigorous international quality and safety standards, ensuring reliable performance and global acceptance.
-
Dedicated Global Support: We provide comprehensive technical support, training, and efficient spare parts supply to our international clientele, minimizing downtime and maximizing operational success.
"OPGW Stringing Equipment" encompasses a complete suite of machinery, tools, and accessories specifically designed for the delicate and precise installation of Optical Ground Wire (OPGW). This typically includes:
-
Hydraulic Puller-Tensioners: Machines that apply both pulling force and controlled back tension.
-
Stringing Blocks (Sheaves): Specially designed pulleys that guide the OPGW along the line.
-
Anti-Twist Devices & Swivels: Critical components to prevent torsional stress on the cable.
-
OPGW Pulling Grips: Connectors that secure the pulling rope to the OPGW without damaging its sensitive core.
-
Reel Stands & Drum Brakes: For controlled payout of the OPGW from the drums.
-
Measuring & Monitoring Devices: Such as dynamometers and sag meters.
Specialized equipment is crucial because OPGW integrates delicate fiber optic strands within a metallic conductor. Standard stringing methods and equipment could easily crush, kink, or induce torsional stress on the OPGW, leading to irreversible damage to the optical fibers and communication failure. Our specialized equipment ensures the integrity of both the optical and electrical functions of the OPGW.
Our "OPGW hydraulic puller-tensioners" are engineered with multiple safeguards to protect the optical fibers:
-
Closed Hydraulic Circuit: Provides ultra-smooth, stepless speed and tension control, eliminating sudden jerks or tension spikes that could damage the fibers.
-
Constant Tension Control: The machine automatically adjusts to maintain a pre-set, low tension, ensuring the OPGW is never overstressed.
-
Large Diameter Bullwheels & Sheaves: Minimizes the bending radius of the OPGW, which is critical for preventing stress on the optical fibers.
-
Non-Metallic, Lined Grooves: The bullwheels and all stringing blocks feature grooves lined with soft, abrasion-resistant materials (e.g., specific polyurethanes, high-density nylon) to cushion and grip the OPGW gently, preventing surface damage or crushing.
-
Advanced Over-Tension Protection: Integrated digital dynamometers with automatic shutdown features prevent the tension from exceeding the OPGW's safe working limit.
We integrate "smart technology" to elevate OPGW stringing operations:
-
Digital Tension & Speed Control: Precise electronic regulation and real-time digital displays of pulling/tensioning force and speed, allowing for fine-tuned control and accurate sag setting.
-
Wireless Data Transmission: Load cells and dynamometers can wirelessly transmit data to monitoring stations or handheld devices, enabling remote oversight and data logging.
-
GPS Integration: For precise location tracking of equipment and mapping of the stringing progress.
-
Automated Fault Detection: Systems can detect anomalies in tension or speed and trigger alarms or automatic shutdowns, preventing potential cable damage.
-
Telematics & Remote Diagnostics: Allows for remote monitoring of machine performance, predictive maintenance, and troubleshooting, minimizing downtime.
"OPGW stringing blocks" (sheaves) are critical "Cable Rigging Accessories" designed with specific features to prevent damage:
-
Larger Sheave Diameter: Ensures the OPGW is bent at a radius greater than its minimum permissible bending radius, protecting the optical fibers.
-
Precision Machined & Lined Grooves: The grooves are meticulously crafted and often lined with highly durable, non-abrasive materials like polyurethane or nylon. This provides a smooth, low-friction surface that prevents abrasion, crushing, or kinking of the OPGW's outer strands.
-
Anti-Jump Guards: Designed to prevent the OPGW from accidentally dislodging from the groove during operation, especially in windy conditions or uneven terrain.
-
Sealed Bearings: Ensure smooth, consistent rotation and minimal friction, reducing drag on the cable and enhancing the overall efficiency of the pull.