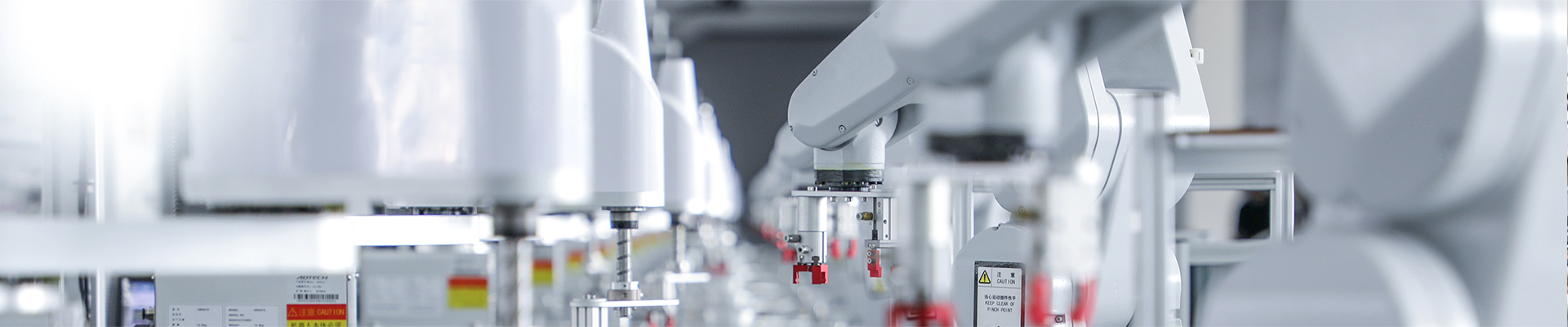
FAQ
Our OPGW installation equipment is evolving with the "smart grid" trend:
-
IoT & Telematics: Machines can be equipped with IoT modules that transmit real-time operational data (e.g., tension, speed, location, machine diagnostics) to cloud-based platforms. This enables remote monitoring, predictive maintenance, and optimized resource allocation.
-
Integrated GPS & Mapping: Allows for precise mapping of the installed OPGW route and accurate location of equipment during deployment.
-
Automated Sag Calculation Integration: Future advancements are focusing on integrating real-time sag measurement directly with tensioners for even more precise sag control, a critical aspect of smart grid implementation.
-
Digital Reporting: Automated generation of detailed installation reports, streamlining project documentation and compliance for smart grid infrastructure development.
These features enhance operational efficiency, provide invaluable data for grid optimization, and align with the future demands of intelligent power networks.
An "OPGW Installation Machine" refers to the specialized power equipment, primarily a hydraulic puller-tensioner, designed specifically for the safe and precise stringing of Optical Ground Wire (OPGW). While standard conductor stringing machines focus on pulling and tensioning metallic conductors, OPGW installation machines incorporate critical differences due to the delicate fiber optic core within the OPGW:
-
Ultra-Precise Tension Control: OPGW has a much lower permissible tension limit compared to traditional conductors. Our machines feature advanced closed-loop hydraulic systems and electronic controls that maintain a constant, pre-set low tension, preventing fiber damage.
-
Large Diameter, Lined Bullwheels: The bullwheels on OPGW machines have significantly larger diameters and are often lined with non-abrasive, high-friction materials (e.g., specific polyurethane, high-density nylon) to minimize the bending radius and prevent crushing or surface abrasion of the OPGW's outer strands.
-
Integrated Anti-Twist Mechanisms: Designed to work seamlessly with anti-twist swivels and devices to prevent torsional stress on the OPGW, which is critical for maintaining optical fiber integrity.
-
Advanced Monitoring Systems: Equipped with highly accurate digital dynamometers that provide real-time tension feedback and often feature automatic shutdown if safe limits are exceeded.
These specialized features are crucial for preserving the optical performance and ensuring the long-term reliability of OPGW.
Our "hydraulic OPGW tensioner-pullers" are central to fiber protection through their advanced hydraulic and electronic systems:
-
Closed Hydraulic Circuit: This system provides exceptionally smooth, stepless speed and tension control in both pulling and tensioning modes. It eliminates jerks and sudden changes in force that could stress or damage the optical fibers.
-
Automatic Tension Control (ATC): The machine's electronic control unit continuously monitors the OPGW tension via a precise dynamometer. If the tension deviates from the pre-set value, the hydraulic system automatically adjusts to maintain the constant desired tension, ensuring the OPGW is always within its safe working limits.
-
Overload Protection: Integrated safety features, often with audible alarms and automatic machine shutdown, prevent the application of excessive tension, safeguarding both the OPGW and the equipment.
This combination of hydraulic precision and electronic control is paramount for achieving accurate sag and preventing any form of damage to the delicate optical core.
We embrace cutting-edge "smart technologies" to optimize OPGW installation:
-
IoT (Internet of Things) Connectivity: Machines can be equipped with telematics modules to transmit real-time operational data (tension, speed, engine status, GPS location) to a central cloud platform. This allows for remote monitoring, predictive maintenance, and optimized fleet management.
-
Digital Control Interface: Intuitive, user-friendly digital displays provide operators with comprehensive machine status, tension graphs, and error codes, improving operational efficiency and troubleshooting.
-
Automated Stringing Modes: Some advanced models feature programmable stringing profiles that can automate certain aspects of the pulling or tensioning process, ensuring consistency and reducing operator fatigue.
-
Integrated Data Logging: Automatic recording of critical parameters throughout the installation (e.g., tension profiles, timestamps, distances) for comprehensive project documentation, quality assurance, and post-analysis.
These integrations lead to safer operations, higher efficiency, and better data-driven decision-making for complex OPGW projects.
"High-speed OPGW reconductoring" requires a balance of power, precision, and specialized design:
-
Powerful Hydraulic Systems: Our machines are designed with robust hydraulic power units that can handle significant pulling/tensioning forces required for efficiently replacing existing ground wires with OPGW, even over long spans.
-
Optimized Bullwheel/Capstan Design: Large diameter, multi-groove bullwheels or capstans ensure efficient power transfer and gentle handling of the OPGW at higher speeds without causing damage.
-
Dynamic Tension Control: The advanced hydraulic and electronic systems provide rapid response to changes in line tension, ensuring that even at higher speeds, the OPGW is never subjected to damaging forces.
-
Integrated Communication: Seamless communication between pulling and tensioning machines (and potentially the pilot line winch) ensures synchronized operation crucial for high-speed reconductoring.
-
Specialized Accessories Compatibility: Designed to integrate with high-speed anti-twist devices and running boards that can withstand faster operation.
This combination allows for significantly reduced installation times, leading to cost savings without compromising the OPGW's integrity.
Installing OPGW in "mountainous terrain" presents unique challenges, which our machines address through:
-
Compact & Robust Design: Optimized for transportability, often with sturdy skid frames or trailer-mounted options suitable for rough access roads. Smaller models might be designed for helicopter lift.
-
Enhanced Mobility: Features like all-wheel drive, powerful engines, and high ground clearance for navigating difficult slopes and uneven ground.
-
Precise Braking & Control: Advanced braking systems ensure controlled descent and tension maintenance on steep inclines.
-
Remote Control Options: Allows operators to control the machine from a safe vantage point, away from direct hazards in challenging areas.
-
Integrated Leveling Systems: Some larger units incorporate hydraulic leveling jacks to ensure stable operation on sloped terrain.
These features ensure reliable performance and safety even in the most inaccessible and rugged environments.
"Live-line OPGW replacement" is a highly specialized operation that demands specific machine capabilities and safety considerations:
-
Precise Control & Stability: The machine's ability to maintain extremely steady and predictable tension and speed is paramount to prevent sudden movements that could compromise live-line clearances.
-
Integrated Grounding Points: Clear and robust grounding points on the machine itself are essential for safely managing induced voltages and fault currents.
-
Compatibility with Insulated Tools: Designed to work seamlessly with insulated pulling ropes, anti-twist devices, and other hot-stick operable accessories.
-
Fail-Safe Systems: Critical safety features like automatic hydraulic braking and emergency stops are designed to activate instantly in case of any system anomaly or operator intervention.
-
Visual & Audible Alarms: Clear alerts for tension limits, operational status, and potential hazards.
While live-line work relies heavily on human expertise and detailed procedures, our OPGW installation machines provide the technical precision and reliability to support these critical operations safely.
Partnering with us for your "OPGW Installation Machines" offers significant advantages:
-
Specialized Expertise: Decades of focused experience in designing and manufacturing power line equipment, with a deep understanding of OPGW's unique installation requirements and challenges.
-
Advanced Technology & Innovation: We leverage cutting-edge manufacturing techniques and continuously invest in R&D to incorporate the latest smart technologies, precision controls, and durable materials into our OPGW machines.
-
Comprehensive One-Stop Solution: Beyond the core machine, we offer a full range of compatible OPGW stringing equipment, tools, and accessories, providing a seamless and efficient procurement experience.
-
Competitive Global Pricing: Our advanced production capabilities and optimized supply chain in China allow us to deliver high-quality OPGW installation machines at globally competitive prices, offering superior value.
-
Robust Quality Assurance: Our machines are built to stringent international quality and safety standards (e.g., ISO, CE, relevant IEC guidelines), ensuring reliability and performance in diverse operational environments worldwide.
-
Dedicated Global After-Sales Support: We provide comprehensive technical support, training for operators, and readily available spare parts to ensure the long-term success and minimal downtime of your OPGW projects.
We design our "OPGW Installation Machines" for exceptional "long-term durability" and "low maintenance" across diverse global climates:
-
High-Quality Components: We source critical components (engines, hydraulic pumps, electrical systems) from globally recognized, reputable manufacturers known for their reliability and performance.
-
Robust Construction: Heavy-duty steel frames, precision-machined parts, and durable welding techniques ensure structural integrity and resistance to operational stresses.
-
Advanced Coatings & Materials: Machines are treated with industrial-grade, anti-corrosion paints and coatings. Critical wear parts (like bullwheel linings) are made from highly durable, abrasion-resistant polymers or specialized alloys.
-
Designed for Accessibility: Components requiring routine maintenance (filters, fluid levels) are easily accessible, simplifying regular checks and reducing service time.
-
Comprehensive Testing: Each machine undergoes rigorous factory testing under various load conditions to ensure all systems perform reliably before shipment.
-
Detailed Manuals & Training: We provide comprehensive operation and maintenance manuals and offer training programs to empower your teams to properly care for and troubleshoot the equipment, maximizing its lifespan.
A complete set of "OPGW Installation Equipment" provides a comprehensive solution for efficient and safe OPGW deployment. It typically includes:
-
Hydraulic Puller-Tensioners: The primary machines for applying precise pulling force and controlled back tension to the OPGW.
-
Stringing Blocks (Sheaves): Specialized pulleys with large diameters and non-metallic, lined grooves to guide the OPGW along the line without damage.
-
Anti-Twist Devices & Swivels: Crucial components to prevent torsional stress on the OPGW cable during pulling.
-
OPGW Pulling Grips: Designed to securely hold the OPGW without crushing its delicate fiber optic core.
-
Reel Stands & Drum Brakes: For controlled payout of the OPGW from the drums, often with integrated tensioning capabilities.
-
Measuring & Monitoring Tools: Such as digital dynamometers, tension load cells, and sometimes sag measurement devices for real-time control.
-
Auxiliary Tools & Accessories: Including grounding equipment, pilot ropes, communication systems, and various clamps and connectors.
A unified system approach is highly beneficial as it ensures seamless compatibility between all components, optimizes workflow, minimizes potential for cable damage, and simplifies procurement and maintenance from a single, reliable supplier like us.
Our "OPGW installation equipment" features sophisticated "integrated control systems" that significantly enhance precision and mitigate risks:
-
Centralized Monitoring: A single operator interface provides real-time data on pulling tension, speed, distance, engine parameters, and hydraulic pressure, allowing for immediate adjustments.
-
Automated Tension Regulation: The system automatically adjusts hydraulic output to maintain a constant, pre-set tension, crucial for OPGW's low permissible tension limits, preventing overstressing and fiber damage.
-
Synchronized Operation: When using separate puller and tensioner machines, the integrated system can synchronize their speeds and forces, ensuring a smooth, coordinated stringing process over long spans.
-
Safety Interlocks & Alarms: Built-in safeguards automatically trigger alarms or emergency shutdowns if tension limits are exceeded, equipment malfunctions, or other critical parameters are violated, protecting both the cable and personnel.
-
Data Logging & Analysis: Comprehensive data logging capabilities allow for post-installation analysis, quality control, troubleshooting, and provide valuable insights for future project planning.
Our "OPGW installation equipment" is designed for efficiency, leading to significant "reduced installation time" and "cost savings":
-
High Efficiency & Speed: Advanced hydraulic systems and optimized design allow for consistent, higher stringing speeds while maintaining precise control, directly cutting down project duration.
-
Minimized Cable Damage: The specialized OPGW-specific features (e.g., large bullwheels, precise tension control) drastically reduce the risk of costly cable damage, preventing expensive reworks and material waste.
-
Reduced Labor Requirements: Automated functions and intuitive controls streamline operations, potentially reducing the number of personnel required on-site.
-
Reliability & Uptime: Our equipment's robust construction and advanced diagnostics minimize breakdowns, ensuring higher operational uptime and avoiding project delays.
-
Optimized Resource Utilization: Efficient fuel consumption and streamlined logistics contribute to lower overall operational costs.
By combining speed, precision, and reliability, our equipment delivers a strong return on investment for OPGW installation projects.
Our "OPGW installation equipment" is designed and manufactured to meet stringent "international safety certifications" for global applicability:
-
CE Marking: For compliance with European Union health, safety, and environmental protection directives.
-
ISO 9001 Certification: Ensures a robust Quality Management System throughout our manufacturing process.
-
Adherence to IEC Standards: Particularly relevant for electrical safety and performance in line with International Electrotechnical Commission guidelines for overhead line equipment.
-
Integrated Safety Features: This includes automatic overload protection and shutdown, emergency stop buttons, hydraulic fail-safe braking systems, operator protection guards, and clear warning labels.
-
Grounding Provisions: Built-in and clearly marked grounding points to ensure proper earthing during operations, crucial for safety.
These certifications and features underscore our commitment to providing equipment that is safe, reliable, and compliant with global industry best practices.
Yes, absolutely. As an experienced China manufacturer and exporter, we understand that OPGW projects often present unique challenges. We offer:
-
Customization Capabilities: Our engineering team can adapt our standard OPGW installation equipment to meet specific project requirements, including modifications for different OPGW cable diameters, unique terrain challenges, or specialized operational needs.
-
Live-Line Application Compatibility: While live-line work requires highly specialized procedures and trained personnel, our machines can be configured to integrate seamlessly with insulated tools, remote control systems, and grounding provisions necessary for safe live-line OPGW replacement.
-
Extreme Weather Enhancements: We can incorporate features such as enhanced cold-weather packages (specialized lubricants, engine heaters), or additional protection against dust, humidity, and corrosive environments to ensure reliable operation in diverse global climates.
We work closely with clients to develop tailored solutions that ensure safe and efficient OPGW installation, no matter how challenging the conditions.
Selecting us as your "China OPGW installation equipment supplier" offers distinct advantages:
-
Specialized Expertise & Innovation: With deep industry knowledge and continuous R&D, we offer state-of-the-art equipment specifically engineered for OPGW's unique demands.
-
Comprehensive One-Stop Solution: We provide not just the core machines, but also a full range of compatible OPGW tools, accessories, and associated equipment, simplifying your procurement process.
-
Exceptional Value & Cost-Effectiveness: Leveraging our advanced manufacturing capabilities and efficient supply chain in China, we deliver high-quality OPGW equipment at globally competitive prices, ensuring excellent return on investment.
-
Robust Quality Assurance: Our commitment to international quality standards (ISO, CE) and rigorous testing ensures that our equipment is reliable, durable, and performs consistently worldwide.
-
Reliable Global Export & Support: We have extensive experience in international logistics, ensuring timely and compliant delivery. Our dedicated after-sales service team provides technical support, training, and readily available spare parts to clients across the globe.
We are committed to ensuring the long-term success of your OPGW projects with comprehensive "after-sales support" and "maintenance services":
-
Technical Support: Our expert technical team is available to provide remote assistance for troubleshooting, operational guidance, and technical inquiries.
-
Spare Parts Supply: We maintain a readily available inventory of genuine spare parts to minimize downtime, ensuring quick replacement and long operational life for your equipment.
-
Operation & Maintenance Manuals: Detailed documentation is provided with every machine, offering clear instructions for safe operation, routine maintenance, and basic troubleshooting.
-
Training Programs: We can offer on-site or remote training sessions for your operators and maintenance personnel to ensure they are proficient in using and maintaining our OPGW installation equipment.
-
Warranty & Guarantee: Our equipment comes with a comprehensive warranty, providing peace of mind and demonstrating our confidence in product quality and reliability.
Our goal is to be a long-term partner, supporting your OPGW installation efforts effectively and efficiently throughout the equipment's lifespan.
Ensuring the optical core's integrity is paramount. Essential "fiber optic preparation tools" for OPGW include:
-
OPGW Cable Sheath Slitters: Precisely score and cut the outer metallic layers without damaging the inner optical tubes.
-
Loose Tube Strippers/Cutters: Designed to safely remove the plastic buffer tubes, exposing the bare optical fibers without nicking or scoring them.
-
Fiber Strippers: Remove the fiber's protective coating (acrylate) without damaging the delicate glass cladding.
-
Fiber Cleavers: Create a perfectly flat and perpendicular end-face on the fiber, crucial for low-loss fusion splicing.
-
Fiber Optic Cleaning Kits: Essential for removing dirt, dust, and contaminants from fiber end-faces before splicing to prevent signal attenuation.
These tools ensure that the OPGW's optical fibers are perfectly prepared for splicing, guaranteeing optimal signal transmission and long-term reliability.
While often integrated into stringing equipment, these are also standalone "OPGW Installation Tools" that are critical:
-
Non-Metallic, Lined Grooves: The grooves of our stringing blocks are precisely machined and typically lined with specialized, soft yet durable materials like high-density polyurethane or nylon. This ensures a gentle, non-abrasive contact surface that prevents crushing, scratching, or deforming the OPGW's outer strands, which could indirectly damage the internal optical fibers.
-
Large Sheave Diameter: This design ensures that the OPGW is bent at a radius significantly greater than its minimum permissible bending radius, eliminating stress on the optical fibers and preventing micro-bending losses.
-
Smooth, Sealed Bearings: High-quality, sealed bearings ensure exceptionally smooth and consistent rotation, minimizing friction and drag on the OPGW, further protecting it during the pull.
These design considerations are fundamental to preserving the OPGW's structural and optical integrity throughout the entire stringing process.
Immediate verification of optical performance is crucial. Key "fiber optic testing tools" include:
-
Visual Fault Locators (VFLs): A handheld tool that injects a visible laser light into the fiber. It quickly identifies breaks, macro-bends, or faulty splices by making the light visible at the fault location.
-
Optical Loss Test Sets (OLTS) / Power Meters & Light Sources: Used in combination to measure the optical attenuation (signal loss) of the OPGW span. This confirms that the signal strength meets specifications and indicates no significant damage occurred during installation.
-
Optical Time Domain Reflectometers (OTDRs): A sophisticated tool that provides a graphical trace of the fiber link, pinpointing the exact location and nature of any faults, splices, or connectors within the OPGW. It's essential for comprehensive post-installation analysis.
These tools allow for quick and accurate assessment of the OPGW's optical health, enabling immediate corrective action if needed.
"Insulated OPGW hand tools" and "hot stick attachments" are absolutely critical for personnel safety during "live-line OPGW work":
-
Insulated Hand Tools: These tools feature multi-layered, dielectric insulation designed to protect against electrical shock up to specified voltage levels. They are used for direct contact with or in close proximity to energized conductors while maintaining isolation.
-
Hot Stick Attachments: These are specialized tool heads that can be securely mounted onto insulating hot sticks. They allow linemen to perform tasks such as installing clamps, making adjustments, or applying grounding devices from a safe distance, eliminating direct contact with energized components.
-
Compliance: All such tools must strictly adhere to international standards like IEC 60900 (for insulated hand tools) or ASTM F711 (for hot sticks and attachments), and undergo rigorous dielectric testing.
These tools are indispensable safety barriers, enabling essential OPGW maintenance or reconductoring operations on energized lines without outages.