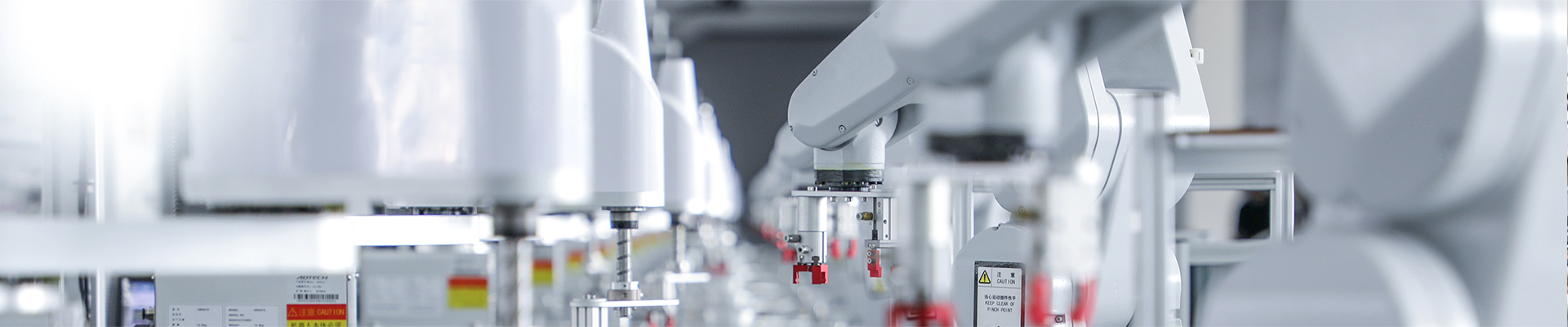
FAQ
"Overhead Line Stringing Accessories" are absolutely indispensable for preventing damage to conductors and ensuring safe, efficient tension stringing of overhead transmission lines. They are engineered to manage mechanical stress, facilitate smooth movement, and maintain the integrity of delicate conductors during the high-tension installation process.
Their crucial roles in damage prevention include:
-
Conductor Rollers (Stringing Blocks/Sheaves):
-
Friction Reduction: These robust rollers, typically made of high-strength aluminum alloy or steel with precision, sealed bearings, are hung from towers or poles. They provide an extremely smooth, low-friction path for the conductor to run through as it's pulled. This drastically reduces the friction that could abrade, scratch, or damage the conductor's outer strands, especially critical for bare aluminum or ACSR conductors.
-
Guiding and Support: They meticulously guide the conductor along the planned route, preventing it from snagging on structures, trees, or ground obstacles. They also consistently support the conductor's weight during stringing, preventing excessive sag and maintaining the required clearance from energized lines, roads, or obstacles.
-
Bundle Conductor Management: Specialized multi-sheave rollers are explicitly designed for stringing bundled conductors (e.g., two, three, or four conductors per phase). These ensure that the individual conductors within a bundle maintain their precise relative positions and do not clash or damage each other during the dynamic stringing process.
-
-
Pulling Swivels (Anti-Twist Devices):
-
Preventing Torsion: This is one of the most critical functions. A high-quality pulling swivel, positioned between the pulling rope and the conductor grip, prevents any rotational forces from the pulling rope (which can naturally twist under tension) from transferring to the conductor. This is absolutely vital for sensitive conductors like OPGW (Optical Ground Wire) which contain delicate optical fibers, or for bundled conductors where twisting can cause uneven sag, damage to spacers, or conductor deformation.
-
Smooth Rotation: Premium swivels feature robust, high-capacity, sealed ball or roller bearings that allow free and effortless rotation, effectively absorbing and isolating any torsional stress in the entire pulling system.
-
-
Conductor Grips (Pulling Socks/Stockings): While considered tools, their function as an accessory is vital. They securely connect the pulling rope to the conductor. Modern designs ensure:
-
Even Pressure Distribution: Sophisticated woven mesh designs (e.g., double or triple weave) distribute the pulling force evenly over a large surface area of the conductor, preventing localized crushing, kinking, or deformation, especially critical for soft aluminum alloys.
-
Non-Slip Connection: They provide a highly reliable, non-slip grip that holds securely even under very high tension, preventing costly and dangerous slippage.
-
-
Anti-Vibration Dampers & Spacers: While often installed after stringing, certain accessories like Stockbridge dampers or spacer dampers are designed to be integrated or considered during the stringing plan to mitigate Aeolian vibration and sub-span oscillation, which can cause fatigue damage to conductors over their lifetime.
-
Grounding Systems & Leads: Crucial safety accessories that ensure the conductor is effectively grounded during stringing to dissipate any induced currents, protecting both workers and the conductor itself from electrical hazards.
By meticulously minimizing friction, preventing twisting, providing controlled guidance, and managing dynamic stresses, these overhead line stringing accessories are fundamental to achieving damage-free, safe, and efficient overhead line construction, directly contributing to the long-term integrity and reliable performance of the transmission network.
For international clients, comprehensive after-sales services and technical support for "Cable Installation Accessories" are just as crucial as for major equipment. These services ensure correct usage, optimal performance, and efficient problem resolution across diverse global projects, ultimately contributing to project success and customer satisfaction.
Key after-sales services and support crucial for international clients include:
-
Comprehensive Product Documentation:
-
Multilingual User Manuals & Installation Guides: Providing clear, detailed instructions for proper use, application, installation sequences, and storage of each accessory, translated into key international languages. This is particularly vital for specialized accessories like cable joints and terminations.
-
Technical Data Sheets (TDS) & Material Safety Data Sheets (MSDS): Easily accessible documents providing critical technical specifications, performance parameters, and essential safety information regarding materials.
-
Installation Videos & Tutorials: High-quality visual guides (online or downloadable) demonstrating complex accessory installations (e.g., specific jointing or termination procedures), which can overcome language barriers and provide practical, step-by-step instruction.
-
-
Dedicated Technical Support & Consultation:
-
Responsive Helpdesk: Access to experienced technical personnel via phone, email, or online chat for immediate queries regarding accessory selection, application, or troubleshooting. The helpdesk should ideally offer support across different time zones.
-
Application Engineering Support: Providing in-depth guidance on selecting the correct accessories for specific cable types, voltage levels, environmental conditions (e.g., extreme heat, cold, corrosive environments), and unique installation challenges.
-
Troubleshooting Guides & FAQs: Comprehensive online resources for diagnosing common issues related to accessory performance and application.
-
-
Global Logistics & Parts Availability:
-
Efficient Supply Chain: A streamlined and reliable system for rapid delivery of accessories worldwide, ensuring projects stay on schedule and minimizing costly delays due to material shortages.
-
Consignment Stock/Local Distributors: For high-volume clients or critical projects, possibilities for local consignment stock or a robust network of authorized international distributors to ensure immediate availability.
-
Batch Traceability: The ability to trace accessories back to their manufacturing batch for quality control, material verification, and in case of any technical advisories.
-
-
Training & Workshops:
-
Product-Specific Installation Training: Offering specialized training sessions (on-site at the client's location or at the manufacturer's facility, or through advanced virtual platforms) for client technicians on the correct and safe installation techniques for critical accessories like joints, terminations, and specialized sealing solutions. This training is often a prerequisite for warranty validation.
-
Best Practices Workshops: Sharing industry best practices for accessory handling, storage, quality control, and application to maximize their effectiveness and extend cable lifespan.
-
-
Quality Assurance & Compliance Documentation:
-
Certifications & Standards Compliance: Providing documentation and certificates (e.g., IEC, ASTM, relevant national electrical codes) confirming that accessories meet all required international and regional standards for performance, safety, and environmental impact.
-
Performance Guarantees: Clear articulation of warranty terms and expected performance life under specified conditions.
-
-
Customer Feedback & Continuous Improvement:
-
Structured Feedback Channels: Establishing clear mechanisms for clients to provide feedback on accessory performance, ease of installation, and new requirements. This feedback loop is crucial for the manufacturer's continuous product improvement and adaptation to evolving global market needs.
-
By providing this comprehensive level of robust after-sales support, a manufacturer demonstrates its unwavering commitment to ensuring that its "Cable Installation Accessories" not only meet but exceed client expectations, contributing directly to the successful, safe, and reliable completion of international power and communication projects.
"Cable Stringing Equipment" refers specifically to the specialized machinery and systems used for the precise and controlled installation of wire cables and conductors for Overhead Transmission Lines (OHTL). It is designed to manage the immense forces and delicate nature of high-voltage conductors during deployment.
Its essential functions in OHTL construction include:
-
Tensioning: Applying precise, controlled back-tension to the conductor as it's pulled off the reel. This is critical to prevent the conductor from dragging on the ground, damaging sensitive surfaces (e.g., roads, agricultural land), or creating safety hazards by coming into contact with structures, trees, or personnel.
-
Pulling: Generating the necessary force to pull the conductor or pilot wire across spans, through stringing blocks (rollers) mounted on towers. Modern pullers offer constant tension control and real-time monitoring.
-
Conductor Management: Safely unwinding conductors from large reels (using reel winders/stands) and controlling their payout. This includes managing multiple conductors simultaneously for bundled lines.
-
Precision Control: Maintaining specific tension and speed parameters throughout the stringing operation to ensure the conductor is installed with the correct sag and clearance, adhering to strict engineering specifications.
-
Safety Integration: Incorporating critical safety features such as automatic overload protection, emergency stops, and data logging to protect personnel, the equipment, and the conductor itself.
-
Pilot Wire Installation: Often, smaller pulling units are used to first string a lightweight pilot wire, which then pulls a larger rope, and finally the conductor itself.
In essence, "Cable Stringing Equipment" is the backbone of efficient, safe, and high-quality overhead power line construction, enabling the rapid and precise deployment of electrical infrastructure over diverse terrains.
"Cable Stringing Equipment" plays a foundational role in the rapid and efficient development of renewable energy infrastructure, particularly for connecting wind farms and large-scale solar power plants to the main transmission grid.
Here's how it contributes:
-
Connecting Remote Generation to the Grid: Wind and solar farms are often located in remote areas with optimal natural resources (strong winds, abundant sunlight). Cable stringing equipment is essential for building the overhead transmission lines that carry the generated electricity from these remote sites to urban centers or existing grid connection points.
-
High-Capacity Transmission: Renewable energy projects often require the construction of new high-voltage (HV) and extra-high-voltage (EHV) transmission lines to handle the large volumes of power. "Cable Stringing Equipment" is specifically designed to handle the massive, heavy conductors and complex bundling required for these high-capacity lines.
-
Efficient Project Timelines: The efficiency and precision of modern stringing equipment significantly reduce the time required for line construction. This accelerates the commissioning of renewable energy projects, allowing green energy to be brought online faster.
-
Minimizing Environmental Impact: Tension stringing techniques, facilitated by this equipment, prevent conductors from dragging on the ground. This minimizes disturbance to sensitive ecosystems, agricultural land, or newly planted solar fields, reducing environmental restoration efforts and costs.
-
Adapting to Challenging Terrain: Renewable energy projects can be situated in diverse and challenging terrains (mountains, deserts, wetlands). Versatile "Cable Stringing Equipment" can be deployed in these environments, enabling the construction of critical transmission infrastructure where traditional methods would be difficult or impossible.
-
Supporting HVDC Transmission: For very long-distance transmission from large offshore wind farms or remote solar arrays, High-Voltage Direct Current (HVDC) lines are becoming more common. Specialized "Cable Stringing Equipment" is adapted to handle the unique characteristics and immense weight of HVDC overhead conductors.
-
Safety in Construction: The inherent risks of working with heavy conductors at height are mitigated by the advanced safety features and controlled operation offered by modern stringing equipment, protecting workers and reducing accidents on these large-scale projects.
In essence, reliable and efficient "Cable Stringing Equipment" is a key enabler for the global transition to renewable energy, allowing the rapid expansion of the infrastructure necessary to integrate clean power into the world's grids.
The "Cable Stringing Equipment" industry is undergoing significant technological advancements, integrating smart features and automation to revolutionize efficiency and safety:
-
Advanced Automation and Control Systems:
-
Constant Tension & Speed Control (Closed-Loop Systems): Modern pullers and tensioners use sophisticated electronic and hydraulic systems to automatically maintain a pre-set constant tension and speed, regardless of terrain changes or friction variations. This prevents over-tensioning (which can damage conductors) and ensures uniform sag.
-
Automated Synchonization: For puller-tensioner setups, automated synchronization ensures both machines work in perfect harmony, maintaining precise tension and speed across the entire span, crucial for complex bundled conductor stringing.
-
-
Real-time Data Acquisition & Telemetry (IoT Integration): Equipment is outfitted with numerous sensors that continuously monitor critical parameters such as pulling force, conductor length, speed, engine diagnostics, and hydraulic pressures. This data is displayed on intuitive digital operator interfaces and transmitted wirelessly via IoT (Internet of Things) to remote monitoring platforms for real-time supervision, analysis, and record-keeping.
-
High-Precision GPS/GNSS Integration: Integrated Global Navigation Satellite Systems (GNSS) with RTK (Real-Time Kinematic) accuracy allow for precise pre-mapping of the stringing route and monitor the exact position and progress of the operation. This is invaluable for accurate "as-built" mapping, ensuring adherence to design specifications, and optimizing logistics.
-
Remote Monitoring & Diagnostics: Operators and project managers can monitor machine performance, track progress, and receive alerts from a central location. This capability allows for proactive maintenance planning, rapid response to operational challenges, and enhanced safety oversight.
-
Predictive Maintenance & AI Analytics: Leveraging real-time and historical operational data, onboard AI and machine learning algorithms can predict potential mechanical failures or maintenance needs (e.g., component wear, fluid degradation). This enables proactive scheduling of maintenance, significantly reducing unplanned downtime, costly emergency repairs, and extending equipment lifespan.
-
Enhanced Safety Features: This includes advanced electronic overload protection with automatic shutdown, multiple emergency stop buttons, robust guarding of moving parts, fail-safe braking systems, and comprehensive alarm systems (audible and visual) to alert personnel to hazardous conditions.
-
Hybrid and Electric Drive Systems: Increasingly, manufacturers are offering hybrid or fully electric stringing equipment, significantly reducing fuel consumption, emissions, and noise pollution, aligning with global sustainability goals.
These advancements collectively lead to significantly higher productivity, reduced operational risks, improved precision in conductor placement, and a safer working environment.
Installing High-Voltage Direct Current (HVDC) overhead lines presents unique challenges compared to traditional AC lines due to larger conductor sizes, higher tensions, and often longer spans. This necessitates specific considerations and specialized "Cable Stringing Equipment":
-
Increased Capacity Pullers and Tensioners: HVDC lines often utilize larger diameter, heavier conductors, and sometimes complex conductor bundles to minimize losses over long distances. This requires pullers and tensioners with significantly higher pulling and braking capacities, often exceeding 100 kN (10 tons) per bullwheel, and sometimes requiring multi-drum configurations to achieve the required force.
-
Precision and Constant Tension Control: HVDC lines are designed for maximum efficiency, and even minor variations in sag can impact performance. The stringing equipment must offer extremely precise and consistent tension control throughout the entire pull, often with automated closed-loop systems, to ensure the conductor is installed exactly to specification.
-
Specialized Conductor Rollers (Stringing Blocks): The sheer size and weight of HVDC conductors demand heavy-duty stringing blocks with larger groove diameters, robust bearings, and higher load capacities to ensure smooth passage and prevent damage or deformation of the conductor. For bundled HVDC lines, multi-sheave blocks are specifically designed to maintain the relative positions of the individual conductors within the bundle.
-
Anti-Twist Swivels for Bundled Conductors: While crucial for all OHTL, anti-twist swivels are even more critical for HVDC bundled conductors, which can be particularly sensitive to torsional stress that could damage spacers or affect aerodynamic stability.
-
Conductor Grips (Pulling Socks) for Heavy Loads: Grips designed for HVDC conductors must have superior strength and an extended length to distribute the immense pulling forces evenly over a larger surface area of the conductor, preventing crushing or slippage.
-
Advanced Monitoring and Data Logging: Given the complexity and criticality of HVDC projects, the stringing equipment typically features advanced monitoring systems for tension, speed, distance, and environmental conditions. This data is logged for quality assurance, troubleshooting, and compliance verification.
-
Adaptation for Long Spans: HVDC lines are often used for very long transmission corridors, leading to longer individual spans between towers. The stringing equipment must be capable of handling these extended distances efficiently and safely.
-
Enhanced Safety Features: Due to the higher forces involved, all safety features (e.g., emergency stops, hydraulic lock-outs, overload alarms) are rigorously implemented and often redundant.
Investing in and properly utilizing this specialized "Cable Stringing Equipment" is fundamental to the successful and reliable construction of HVDC transmission infrastructure, which is increasingly vital for integrating renewable energy and strengthening national grids.
Safety is paramount in overhead line construction, and "Cable Stringing Equipment" incorporates numerous features and demands strict operational best practices to protect workers and prevent accidents.
Key Safety Features of the Equipment:
Emergency Stop Buttons: Strategically placed, clearly marked emergency stop buttons that immediately halt all machine operations.
Automatic Overload Protection: Sensors that detect when tension or load limits are exceeded, automatically reducing power or shutting down to prevent equipment failure or conductor breakage.
Fail-Safe Braking Systems: Hydraulic or mechanical braking systems that automatically engage in case of power loss or system malfunction, preventing uncontrolled conductor movement.
Enclosed Operator Cabins/Safety Guards: Modern cabins provide protection from elements and noise, while robust guards protect personnel from moving parts (e.g., bullwheels, drive shafts).
Audible & Visual Alarms: Warning systems for high tension, low fluid levels, system faults, or when the machine is operating in a potentially hazardous state.
Remote Control & Wireless Communication: Allows operators to control the equipment from a safe distance, away from potential pinch points or falling debris.
Integrated Lighting: Adequate lighting for night operations, ensuring clear visibility of the work area and controls.
Anti-Twist Swivels: Critical for preventing the accumulation of torsion in the pulling rope and conductor, which could lead to unexpected rotation and hazards.
Operational Best Practices:
Thorough Planning & Risk Assessment:
Detailed Stringing Plan: Pre-plan the exact route, tension calculations, equipment placement, and communication protocols.
Job Hazard Analysis (JHA): Identify all potential hazards at the worksite and develop mitigation strategies before commencing work.
Pre-Construction Briefings: Review the plan and potential hazards with all personnel involved.
Qualified & Trained Personnel: Ensure all operators and ground crew are fully trained, certified, and competent in the operation of the specific equipment and adhere to safety procedures.
Pre-Operational Checks: Perform daily inspections of all equipment, including fluids, controls, safety features, ropes, and connections, before starting work.
Clear Communication Protocols: Establish clear radio communication channels between the puller operator, tensioner operator, and ground crew to ensure coordinated and safe operations.
Exclusion Zones: Maintain strict exclusion zones around tensioners, pullers, and conductors during stringing to protect personnel from moving lines or potential snap-back hazards.
Proper Grounding: Ensure all equipment is properly grounded to dissipate static electricity or induced currents.
Weather Monitoring: Suspend operations during adverse weather conditions (high winds, lightning, heavy rain) that could compromise safety.
Regular Equipment Maintenance: Adhere to manufacturer-recommended maintenance schedules to ensure all safety features and operational components are in peak condition.
Use of Proper PPE: Ensure all personnel wear appropriate Personal Protective Equipment (PPE), including hard hats, safety glasses, gloves, and high-visibility clothing.
By combining advanced equipment design with diligent operational practices, the risks associated with cable stringing can be significantly minimized, ensuring the safety of all involved.
To ensure the longevity, peak performance, and reliable operation of "Cable Stringing Equipment," a structured and professional maintenance schedule, coupled with robust support from the manufacturer, is essential. Due to the high forces and critical nature of this equipment, proactive maintenance is key to preventing costly downtime and ensuring safety.
1. Regular & Preventative Maintenance (OEM Recommended):
-
Daily/Shift Checks (Operator Level):
-
Fluid levels (engine oil, hydraulic fluid, coolant, fuel).
-
Visual inspection for leaks, loose fasteners, damaged hoses, worn components (e.g., bullwheel grooves, bearings), and cable/rope integrity.
-
Functionality check of emergency stops, safety guards, and control levers.
-
Cleaning of critical areas (e.g., operator cabin, sensor lenses).
-
-
Weekly/Bi-Weekly Checks (On-site Technician Level):
-
Greasing of all lubrication points according to the OEM manual.
-
Inspection of pulling ropes and conductor stringing lines for wear, fraying, or damage; check wire rope terminations.
-
Check tire pressure/track tension and overall chassis integrity.
-
Inspection of brake systems (disc brakes, fail-safe brakes) and hydraulic lines.
-
Check and clean air, fuel, and hydraulic filters.
-
-
Monthly/Quarterly Checks (Qualified Technician Level):
-
Full inspection of all structural components for cracks, fatigue, or deformation.
-
Comprehensive hydraulic system health check (pressure testing, flow rates, filter replacement).
-
Engine service (oil and filter changes, belt tension checks).
-
Calibration verification of tension/speed sensors, load cells, and digital displays.
-
Electrical system inspection (wiring, connections, battery health).
-
Thorough inspection of bullwheel surfaces for wear or damage.
-
-
Annual/Bi-Annual Major Service (Specialized Technician/OEM):
-
Comprehensive overhaul inspections of all major components.
-
Fluid analysis (engine oil, hydraulic fluid) to detect wear particles and fluid degradation.
-
Replacement of all critical filters and fluids.
-
Detailed inspection and potential rebuild of high-wear components (e.g., bullwheel bearings, drive motors, gearboxes).
-
Software updates and full diagnostic checks of control systems and telematics modules.
-
Load testing and re-calibration of the entire system under controlled conditions.
-
2. Professional Support & Services (From Manufacturer/Authorized Dealer):
-
Manufacturer's Comprehensive Manuals: Detailed operation, maintenance, parts, and troubleshooting guides provided in multiple languages, including schematics and wiring diagrams.
-
Dedicated Technical Support: Access to experienced technical support teams via phone, email, or online portals, often with 24/7 availability for international clients, trained specifically on your equipment models.
-
Remote Diagnostics & Telematics: Leveraging built-in telematics systems to remotely diagnose issues, monitor machine health, track performance, and provide proactive alerts, minimizing the need for on-site visits and speeding up issue resolution.
-
Global Spare Parts Availability: A robust supply chain with strategically located international warehouses or efficient logistics to ensure rapid delivery of genuine spare parts, minimizing unplanned downtime.
-
Certified Field Service Technicians: Access to highly skilled and factory-trained technicians who can be dispatched to perform complex repairs, major services, critical calibrations, and commissioning on-site worldwide.
-
Operator & Maintenance Training: Comprehensive training programs (on-site or virtual) for client personnel to ensure safe, efficient, and proper operation, routine maintenance, and basic troubleshooting of the machines. This often includes advanced training for complex operations.
-
Service Level Agreements (SLAs): Offering flexible service contracts that can include scheduled preventative maintenance, priority support, guaranteed response times, and even full-service agreements, providing peace of mind and optimizing asset uptime and cost predictability.
-
Software Updates & Upgrades: Regular provision of software updates for machine control systems to improve performance, add new features, and enhance security, ensuring your equipment remains cutting-edge.
Adhering to these rigorous practices, often in close partnership with the original equipment manufacturer, is paramount for maximizing the lifespan, reliability, safety, and resale value of your valuable "Cable Stringing Equipment."
"Cable Stringing Tools" refer to the portable, often handheld or manually operated implements and devices used by line workers directly on or around the conductor and support structures during overhead transmission line (OHTL) stringing operations. They are designed for precision, localized tasks, and direct interaction with the conductor, pilot wires, and associated hardware.
They differ from "Cable Stringing Equipment" primarily in scale, function, and mobility:
-
Cable Stringing Equipment: Encompasses the large, heavy-duty machinery that provides the main power and control for the stringing operation, such as hydraulic pullers, tensioners, reel winders, and large gin poles. These are typically vehicle-mounted, trailer-mounted, or self-propelled units.
-
Cable Stringing Tools: These are the essential implements that complement the larger equipment, enabling workers to perform crucial tasks at the tower, on the ground, or even in the air. Examples include:
-
Conductor Grips/Pulling Socks: For securely connecting pulling ropes to conductors.
-
Pulling Swivels: To prevent twisting of the pulling rope and conductor.
-
Line Hoists & Come-Along Clamps: For lifting, tensioning, and securing conductors temporarily.
-
Dynamometers: For measuring tension and ensuring safety limits are not exceeded.
-
Sag Sights & Measurement Tools: For precise conductor sag adjustment.
-
Temporary Grounding Sets: For ensuring electrical safety during work.
-
Specialized Hand Tools: For working with conductor hardware, splices, and fittings.
-
Essentially, "Equipment" handles the heavy pulling and tensioning over long distances, while "Tools" provide the necessary precision, control, safety, and manual manipulation required at specific points along the line.
Optical Ground Wire (OPGW) and High-Temperature Low-Sag (HTLS) conductors represent advanced conductor technologies, requiring specialized "Cable Stringing Tools" that prioritize precision, gentleness, and specific handling requirements to prevent damage and ensure long-term performance.
For OPGW (Optical Ground Wire):
-
OPGW Specific Pulling Grips (Pulling Socks): These are designed with longer, finer, and often softer mesh weaves that distribute the pulling force over a larger surface area, minimizing localized pressure that could crush or damage the delicate optical fibers within the OPGW's core. They often feature an internal steel thimble to prevent fiber compression.
-
Anti-Twist Swivels: Absolutely critical for OPGW. The optical fibers within OPGW are highly sensitive to torsion. High-quality, robust anti-twist swivels must be placed directly between the pulling grip and the pulling rope to absorb any rotational forces, ensuring the OPGW remains untwisted during the entire stringing process.
-
Larger Diameter Stringing Blocks/Sheaves: OPGW has a precise bend radius. Using larger diameter stringing blocks ensures that the OPGW is not bent too sharply, which could cause micro-bends or macro-bends in the optical fibers, leading to signal loss. The grooves must also be smooth and free of any imperfections.
-
Fiber Optic Testing Equipment (Post-Stringing): While not directly "stringing tools," portable OTDRs (Optical Time Domain Reflectometers) and Optical Power Meters (OPMs) are essential for immediate post-stringing testing to verify the integrity of the optical fibers and confirm no damage occurred during installation.
-
OPGW Splicing & Termination Tools: For the communication aspect, specialized fiber optic splicing tools (cleavers, fusion splicers, cleaning kits) are used once the OPGW is strung.
For HTLS (High-Temperature Low-Sag) Conductors:
-
Specialized HTLS Pulling Grips: HTLS conductors often have unique core materials (e.g., composite, Invar) and outer aluminum alloy strands that can be more susceptible to localized damage or deformation if not gripped correctly. Grips designed for HTLS ensure even pressure distribution and prevent "birdcaging" or strand damage.
-
Precise Tension Control Systems: While this is largely equipment-related, the tools (dynamometers, tension recorders) that interface with this equipment are crucial. HTLS conductors rely on very specific tensioning parameters to achieve their low-sag characteristics, making precise monitoring tools indispensable.
-
Larger Radius Stringing Blocks: Similar to OPGW, HTLS conductors, especially those with large diameters, benefit from larger radius stringing blocks to prevent excessive bending stress on the conductor and its composite core.
-
Anti-Vibration Dampers & Installation Tools: HTLS conductors can be more prone to certain types of vibration. The specialized tools for installing vibration dampers (e.g., Stockbridge dampers, spacer dampers) are essential once the conductor is strung and sagged.
In both cases, meticulous planning, use of manufacturer-approved tools, and highly trained personnel are non-negotiable for successful and reliable installation of these advanced conductors.
The evolution of "Cable Stringing Tools" has placed a strong emphasis on improving ergonomics and significantly reducing worker fatigue, recognizing that comfortable and less strained workers are safer, more productive, and less prone to injuries.
Key advancements include:
-
Lightweight Materials:
-
Aluminum Alloys: Many tools previously made from heavy steel are now manufactured from high-strength, lightweight aluminum alloys (e.g., stringing blocks, gin poles, come-along clamps), dramatically reducing the weight that workers need to carry and maneuver at height or across challenging terrain.
-
Composite Materials: Advanced composite materials are increasingly being used for components that require high strength-to-weight ratios, further lightening the load.
-
-
Optimized Leverage & Mechanical Advantage:
-
Ratchet Mechanisms: Tools like ratchet hoists and some types of crimpers/cutters incorporate ratchet mechanisms that provide mechanical advantage, requiring less manual force and making repetitive tasks easier.
-
Ergonomic Handles & Grips: Handles are designed with contours that fit naturally in the human hand, often with non-slip, shock-absorbing materials that reduce vibrations and provide a secure, comfortable grip, minimizing blisters and hand fatigue.
-
-
Battery-Powered Options:
-
Battery-Hydraulic Tools: For tasks like cutting and crimping smaller conductors or working with hardware, compact, battery-powered hydraulic tools have replaced many manual hydraulic or mechanical options. These eliminate manual pumping, significantly reducing physical exertion and speeding up tasks.
-
-
Balanced Designs: Tools are designed to be well-balanced in the hand, reducing awkward wrist or arm positions and minimizing strain during prolonged use.
-
Reduced Size and Portability: Smaller, more compact designs for tools that need to be carried up towers or into confined spaces, making them easier to transport and maneuver.
-
Ease of Use Features:
-
Quick-Release Mechanisms: For certain clamps or hoists, quick-release mechanisms simplify attachment and detachment, saving time and reducing fumbling.
-
Integrated Lighting: Some tools (especially those with electronic components) feature integrated LED lighting to illuminate the work area, improving visibility and reducing eye strain in low-light conditions.
-
These ergonomic improvements not only enhance worker comfort and reduce the risk of musculoskeletal injuries but also contribute directly to increased efficiency and higher quality work on overhead line construction projects.
Given the critical safety role and high-stress environment of "Cable Stringing Tools," rigorous inspection, maintenance, and proper storage are paramount to ensuring their longevity, preventing failures, and guaranteeing worker safety.
1. Pre-Use & Post-Use Inspection (Operator Level):
-
Visual Damage Check: Before each use, thoroughly inspect all tools for visible damage: cracks, bends, deformation, excessive wear, corrosion, loose fasteners, fraying on ropes or slings, or compromised insulation (for hot sticks or insulated tools). Pay special attention to load-bearing components like jaws on grips, sheave grooves on blocks, and connecting pins.
-
Functionality Check: Operate all moving parts to ensure smooth action without binding, excessive play, or unusual noises. Test safety mechanisms (e.g., locks on clamps, emergency releases on hoists).
-
Cleanliness: Ensure tools are free of dirt, mud, grease, and cable residue. For stringing blocks, check that the sheave rotates freely and the groove is clean.
2. Regular Preventative Maintenance (Qualified Technician Level - Monthly/Quarterly):
-
Cleaning & Lubrication: Thoroughly clean all tools. Apply manufacturer-recommended lubricants to all pivot points, bearings (on swivels and blocks), and moving mechanisms to prevent wear, corrosion, and ensure smooth operation.
-
Wear Part Inspection & Replacement: Regularly inspect components prone to wear, such as the liner materials in stringing blocks (if replaceable), jaws on grips, and cutting edges. Replace worn parts according to manufacturer guidelines before they compromise performance or safety.
-
Rope & Sling Integrity: For fiber ropes or steel wire slings used with tools, inspect for cuts, abrasions, excessive wear, kinks, or damaged splices. Retire damaged ropes immediately.
-
Hardware Checks: Inspect all shackles, clevises, pins, and connection points for deformation, wear, or cracks.
-
Insulated Tools: For hot sticks and other insulated tools, perform dielectric integrity checks as per industry standards and manufacturer recommendations. Any visible damage to insulation should lead to immediate removal from service.
3. Calibration & Certification (Specialized Service Provider - Annually/Bi-Annually):
-
Dynamometers & Load Cells: These critical measuring tools must be professionally calibrated by a certified laboratory at regular intervals (typically annually or bi-annually) to ensure their accuracy. Maintain meticulous calibration records.
-
Crimping Heads/Dies: If hydraulic crimping tools are part of your stringing tools, ensure their heads and dies are inspected for wear and that the hydraulic system provides the correct pressure for consistent crimps.
4. Proper Storage:
-
Clean & Dry Environment: Store all tools in a clean, dry, and well-ventilated area, protected from direct sunlight, extreme temperatures, dust, and moisture to prevent rust and material degradation.
-
Organized Storage: Use dedicated toolboxes, racks, or shadow boards to organize tools. This prevents damage from tools rattling against each other and makes it easy to identify missing or damaged items quickly.
-
Protective Covers/Cases: Store sensitive tools (e.g., dynamometers, precision measuring tools) in their original padded, protective cases to shield them from impacts and environmental factors.
-
Separate Insulated Tools: Store insulated tools separately to prevent damage to their insulation from contact with other tools or sharp objects.
5. Removal from Service:
-
Immediate Tagging: Any tool that shows significant damage, a compromise to its integrity (especially safety-critical components or insulation), or fails a functional check must be immediately tagged "OUT OF SERVICE" and removed from use.
-
Professional Repair/Replacement: Do not attempt to repair safety-critical or specialized tools unless you are a certified technician following strict manufacturer guidelines. Often, replacement is safer and more cost-effective than attempting field repairs.
Adhering to these rigorous practices significantly extends the working life of your valuable "Cable Stringing Tools," maintains their precision and performance, and, most importantly, safeguards the lives of your line workers.
"Cable Stringing Accessories" are the various supplementary components, often passive or consumable, that are installed with the conductor or are integral to the stringing process itself, but are distinct from the primary machinery ("Equipment") and handheld items ("Tools"). They are typically left in place (like conductor accessories) or are integral to the temporary setup for stringing.
They differ as follows:
-
Cable Stringing Equipment: Refers to the large, powered machinery that performs the primary tasks of pulling and tensioning conductors over long spans (e.g., hydraulic pullers, tensioners, reel winders).
-
Cable Stringing Tools: Encompasses portable, often handheld or manually operated items used by line workers for specific tasks at the tower or on the ground (e.g., pulling grips/socks, swivels, dynamometers, line hoists, crimping tools, sag sights).
-
Cable Stringing Accessories: These are the items that enable the smooth and safe passage of the conductor, or are added to the conductor for long-term performance and protection. Key examples include:
-
Conductor Rollers (Stringing Blocks/Sheaves): Guide the conductor along the route, reducing friction.
-
Anti-Vibration Dampers: Installed on conductors post-stringing to mitigate vibration.
-
Spacers & Spacer Dampers: Maintain spacing between bundled conductors and provide damping.
-
Repair Sleeves/Armor Rods: Used for minor conductor repairs or reinforcement.
-
Conductor Splicing Accessories: Components for permanent conductor joints.
-
Overhead Ground Wire (OHGW) Hardware: Specialized fittings for earth wires.
-
Temporary Grounding Sets: Crucial for safety during stringing.
-
Pilot Wire Accessories: Connectors and devices for handling pilot lines.
-
In essence, "Equipment" provides the power, "Tools" provide the direct manipulation, and "Accessories" provide the critical components that ensure the conductor's integrity and the efficiency of its installation and long-term performance.
Material science is a critical consideration for "Cable Stringing Accessories" due to the extreme mechanical stresses, diverse environmental conditions, and long service life expected of these components globally. The choice of materials directly impacts durability, performance, and safety.
Key material considerations include:
-
High-Strength & Lightweight Alloys:
-
Aluminum Alloys: Widely used for stringing block sheaves, frames, and some grips due to their excellent strength-to-weight ratio. Alloys are chosen for specific properties like resistance to deformation under high load, corrosion resistance, and good machinability.
-
Heat-Treated Steel Alloys: Used for components requiring maximum strength and wear resistance, such as pins, shafts, load-bearing frames, and critical parts of pulling swivels and heavy-duty clamps. Heat treatment processes (e.g., quenching and tempering) enhance their hardness and toughness.
-
-
Corrosion Resistance:
-
Galvanization: Steel components are often hot-dip galvanized or electro-galvanized to provide a sacrificial zinc coating that protects against rust and corrosion in humid, coastal, or industrial environments.
-
Stainless Steel: Used for fasteners, springs, and components exposed to highly corrosive conditions (e.g., marine environments, chemical plants) due to its inherent corrosion resistance.
-
-
Wear-Resistant & Low-Friction Polymers/Composites:
-
MC Nylon (Cast Nylon), Polyurethane, HDPE: Increasingly used for sheave liners in stringing blocks (especially for sensitive conductors like OPGW or covered cables). These materials offer:
-
Excellent Abrasion Resistance: Withstand continuous rubbing from conductors.
-
Low Coefficient of Friction: Significantly reduce pulling friction and prevent damage to conductor jackets.
-
Impact Resistance: Absorb shocks without deforming.
-
Chemical Resistance: Stand up to lubricants, pollutants, and various environmental chemicals.
-
-
-
Elastomers (Rubbers/Synthetics):
-
Neoprene/EPDM: Used for seals in bearings (e.g., in swivels) to protect against dust, moisture, and contaminants, extending bearing life. Also used in anti-vibration dampers for their elastic and energy-absorbing properties.
-
-
UV Stability: For accessories permanently exposed to sunlight (e.g., some types of spacers, helical dampers), materials must be UV-stabilized to prevent degradation, embrittlement, and color fading over time.
-
Temperature Performance: Materials must maintain their mechanical properties and dimensional stability across the expected operating temperature range, from extreme cold to high heat, without becoming brittle or softening.
-
Dielectric Properties (for Insulated Accessories): For tools used near live lines or for insulating components (e.g., hot sticks, temporary cover-ups), materials with high dielectric strength and good tracking resistance (e.g., fiberglass, specialized polymers) are crucial.
By carefully selecting and processing these advanced materials, manufacturers ensure that "Cable Stringing Accessories" provide the necessary strength, durability, and protective qualities to perform reliably in the demanding environments of global overhead transmission line construction.
While "Anti-Vibration Dampers" are typically installed after the primary stringing and sagging is complete, they are considered essential "Cable Stringing Accessories" because they are a crucial, permanent component for ensuring the long-term mechanical integrity and lifespan of overhead conductors. Their primary function is to mitigate conductor vibration that can lead to fatigue damage.
Why They Are Essential:
-
Fatigue Protection: Overhead conductors are susceptible to Aeolian vibration (wind-induced oscillation) and sub-span oscillation (in bundled conductors). Without damping, these continuous vibrations can cause:
-
Fatigue Breakage: Repeated stress cycles can lead to fatigue failure of individual strands, particularly at suspension clamps or points of stress concentration.
-
Damage to Hardware: Vibration can also loosen or damage insulators, clamps, and other line hardware.
-
Arcing Damage: In severe cases, vibration can cause clashing of conductors within a bundle, leading to arcing and localized heat damage.
-
-
Extended Conductor Lifespan: By effectively dampening vibrations, these accessories significantly extend the operational life of the conductor, reducing maintenance costs and ensuring grid reliability.
-
Improved System Reliability: Preventing conductor fatigue failures means fewer unscheduled outages, enhancing the overall reliability and availability of the transmission line.
Common Types of Anti-Vibration Dampers:
-
Stockbridge Dampers: The most common type. They consist of a central clamp that attaches to the conductor and two masses (often made of cast iron or zinc alloy) connected by a steel messenger cable. When the conductor vibrates, the damper's masses vibrate out of phase with the conductor, dissipating the vibratory energy. They are highly effective over a broad range of frequencies.
-
Spiral Vibration Dampers (Helical Dampers): Made from a resilient, non-metallic material (e.g., PVC, HDPE) in a helical shape. They are wrapped around the conductor and dissipate vibration energy through friction and impact with the conductor. They are typically used on smaller conductors and distribution lines.
-
Spacer Dampers: Used exclusively on bundled conductors. They serve a dual purpose:
-
Maintain Bundle Geometry: Physically separate and maintain the precise spacing between individual conductors within a bundle.
-
Dampen Sub-span Oscillation: Incorporate elastomeric or hinged components that absorb and dissipate energy from oscillations between the individual conductors within a bundle.
-
-
Mid-Span Dampers: Less common, but used to address specific vibration issues in very long spans.
The correct selection and precise placement of these dampers, based on conductor type, tension, span length, and wind data, are critical engineering considerations for any successful OHTL project.
"Temporary Grounding Sets" and "Insulating Cover-Up Equipment" are absolutely non-negotiable "Cable Stringing Accessories" because they are fundamental to ensuring the safety of line workers during all phases of overhead line stringing, especially when working near or on de-energized or induced voltage lines.
1. Temporary Grounding Sets:
-
Purpose: These sets are designed to safely discharge any electrical energy (residual charge, induced voltage from adjacent energized lines, or accidental re-energization) on a de-energized conductor or structure to earth. This creates a "zone of protection" for workers.
-
Components: Typically consist of:
-
Grounding Clamps: Heavy-duty, high-conductivity clamps designed to securely connect to conductors, equipment, or structural components.
-
Grounding Cable: Flexible, high-conductivity copper cable with a durable jacket, connecting the clamps to each other and to a reliable earth ground.
-
Hot Sticks: Used to apply and remove the grounding clamps from a safe distance.
-
-
Why Non-Negotiable:
-
Induced Voltage Protection: Even seemingly "dead" lines can carry dangerous induced voltages from nearby energized lines (especially in multi-circuit corridors). Grounding safely dissipates this energy.
-
Accidental Re-energization: Prevents serious injury or death if a line is accidentally re-energized while workers are on it. The grounds create a short-circuit path, tripping protective devices.
-
Residual Charge: Discharges any stored capacitive or inductive energy in the line.
-
Safety Protocol: A mandatory part of "Lockout/Tagout" and "Permit-to-Work" procedures, creating a visible and verifiable safe working environment.
-
2. Insulating Cover-Up Equipment:
-
Purpose: These accessories provide temporary insulation and mechanical protection for workers and equipment from accidental contact with energized conductors, substation components, or other electrical apparatus that cannot be de-energized.
-
Components: Include:
-
Insulating Blankets: Flexible, high-dielectric strength sheets (rubber, synthetic) used to cover energized busbars, insulators, or adjacent conductors.
-
Insulating Line Hoses: Segmented, flexible tubes that snap around energized conductors to provide continuous insulation.
-
Insulating Pole Covers: Cylindrical covers placed over energized poles or cross-arms.
-
Rubber Gloves & Sleeves: Essential PPE for direct contact with or proximity to energized parts.
-
-
Why Non-Negotiable:
-
Live Work Protection: Essential when work must be performed in close proximity to, or directly on, energized lines or equipment.
-
Accidental Contact Prevention: Creates a physical barrier to prevent inadvertent contact, flashovers, and electrocution.
-
Tool Protection: Protects non-insulated tools or equipment from becoming energized.
-
Compliance: Adherence to strict industry safety standards (e.g., OSHA, national electrical codes) mandates the use of appropriate cover-up for live-line work clearances.
-
Both grounding sets and insulating cover-up equipment are critical layers of defense, forming part of a comprehensive safety strategy to protect personnel from electrical hazards inherent in overhead line construction and maintenance. Proper training in their application and regular inspection are paramount.
"Pilot Wire & Hauling Rope Accessories" are crucial "Cable Stringing Accessories" that facilitate the initial stages of multi-stage conductor stringing, particularly for heavy conductors or long spans. They act as intermediate connections, gradually scaling up the pulling capacity.
Their roles include:
-
Establishing the Initial Pulling Path:
-
Pilot Wire Connectors: Small, lightweight connectors designed to securely attach the initial, lightweight pilot wire (often made of synthetic rope or small-diameter steel wire) to the lead end of the hauling rope.
-
Pilot Wire Sheaves/Blocks: Smaller, lightweight stringing blocks specifically designed for the pilot wire, enabling its initial deployment without snagging or undue friction across the spans.
-
-
Scaling Up Pulling Capacity:
-
Hauling Rope Grips/Connectors: Robust connectors or grips designed to securely attach the hauling rope (which is heavier and stronger than the pilot wire) to the conductor pulling grip. These connections must be strong enough to withstand significant tension.
-
Hauling Rope Swivels: Essential to prevent any twist from the hauling rope from transferring to the conductor or pilot wire. These are similar to conductor swivels but sized for the hauling rope.
-
-
Preventing Damage & Streamlining Process:
-
Anti-Twist Hauling Systems: Some accessories include specialized anti-twist devices designed to manage torque in the hauling rope, protecting both the rope and subsequent conductors from torsional stress.
-
Hauling Rope Guides & Fairleads: Devices that help guide the hauling rope smoothly onto and off the pulling equipment, preventing tangling or wear.
-
Breakaway Links/Fuses: In some scenarios, a "breakaway fuse" or link might be incorporated into the pilot wire or hauling rope connection. This accessory is designed to intentionally break at a predetermined overload, protecting the more expensive conductor or equipment from damage in case of snagging or excessive tension.
-
-
Facilitating Complex Stringing:
-
Swivel Connectors: Allow for the smooth rotation of pulling elements, preventing the accumulation of twists that could damage conductors or cause snags.
-
Line Connectors: Simple, robust connectors (often "bull-nose" or tapered designs) used to smoothly connect sections of hauling rope or to connect the hauling rope directly to the conductor pulling grip, ensuring easy passage through stringing blocks.
-
By systematically building up the pulling strength from a lightweight pilot wire to the robust hauling rope, and finally to the conductor, these accessories enable controlled and damage-free stringing of even the heaviest and longest overhead lines, improving both safety and efficiency on complex projects.
"Conductor Stringing Blocks," also known as sheaves or rollers, are fundamental "Cable Stringing Accessories." They are designed to guide the conductor smoothly along the overhead line route, minimizing friction and preventing damage during tension stringing. Latest innovations focus on enhanced materials, advanced designs, and features for specialized conductors:
-
Advanced Sheave Materials:
-
High-Strength Aluminum Alloys: Continuously refined for lighter weight, increased load capacity, and better resistance to wear and corrosion.
-
Polymer/Nylon Composite Liners: For very sensitive conductors (e.g., OPGW, covered conductors, some HTLS types), composite liners (e.g., MC nylon, polyurethane) are used. These non-metallic materials offer:
-
Reduced Friction: Lower coefficient of friction compared to bare metal.
-
Superior Conductor Protection: Prevent scratching, abrasion, and flattening of the conductor's outer strands or delicate insulation.
-
Noise Reduction: Contribute to quieter stringing operations.
-
-
-
Optimized Bearing Technology:
-
Sealed, High-Precision Bearings: Enhanced, sealed bearings (ball or roller) minimize internal friction, increase load capacity, and extend service life, even in dusty or harsh environments. They require less maintenance.
-
-
Larger Sheave Diameters: The trend towards larger diameter stringing blocks is crucial for:
-
Reduced Bending Stress: Minimizing the bending radius on large or sensitive conductors (like OPGW and some HTLS conductors) to prevent internal damage to optical fibers or composite cores.
-
Lower Pulling Tension: Larger diameters contribute to even lower friction, reducing the overall pulling tension required.
-
-
Modular & Versatile Designs:
-
Interchangeable Sheaves: Some blocks allow for interchangeable sheaves or liners, providing versatility for different conductor types or sizes with the same block frame.
-
Universal Attachments: Designed with versatile attachment mechanisms (clevis, shackle, suspension plate) for compatibility with various tower types and installation scenarios.
-
-
Integrated Grounding Attachments: Some blocks incorporate convenient attachments for temporary grounding leads, enhancing safety during stringing by ensuring potential induced voltages are safely dissipated.
-
Specialized Designs for Bundled Conductors: Multi-sheave blocks are continually refined to ensure each conductor within a bundle is guided independently and smoothly, preventing clashing or tangling during stringing.
These innovations in stringing blocks directly contribute to safer, more efficient, and damage-free conductor installation, which is critical for the long-term reliability of modern overhead transmission lines.