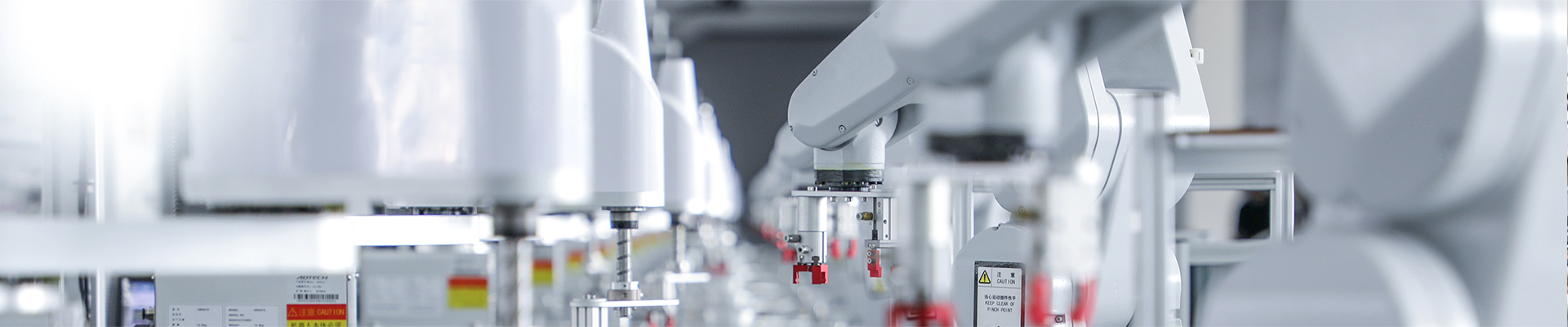
FAQ
"Load monitoring" is a critical safety and efficiency feature in modern "Cable Rigging Machines." Integrated sensors and digital readouts provide real-time information on the weight and distribution of the load. This prevents accidents by:
-
Detecting Overloads: Immediately alerting operators or halting operations if the load exceeds the machine's safe working limit, preventing structural failure or tipping.
-
Maintaining Stability: For multi-point lifts, load monitoring ensures even weight distribution, preventing imbalances that could lead to tipping or dropping the load.
-
Optimizing Operations: Allows operators to work efficiently within safe parameters, avoiding unnecessary stress on the machine and ensuring controlled, precise movements.
-
Data for Planning: Logged load data can be used for future project planning and risk assessment.
-
Yes, the demand for adaptable and efficient solutions has led to the development of highly "portable rigging solutions" and "modular rigging systems." These are ideal for:
-
Remote Locations: Where access for large cranes or heavy equipment is limited.
-
Smaller Substations or Distribution Lines: Where the scale of lifts is less extreme but precision is still needed.
-
Quick Deployments: For emergency repairs or rapid construction phases.
-
-
These can include lightweight aluminum gantries, compact hydraulic lifting systems, or specialized portable winches that can be easily transported and assembled on-site, offering flexibility without compromising on lifting capacity for their class.
Our prominent position as a "China rigging machine manufacturer" and "global exporter" for electrical construction stems from:
-
Specialized Expertise: Decades of focus on power line, substation, and electrical construction equipment.
-
Innovative R&D: Continuous investment in developing cutting-edge rigging technologies and smart solutions.
-
Robust Manufacturing Capabilities: State-of-the-art facilities ensure high-quality, durable, and reliable equipment.
-
Customization Flexibility: Ability to engineer and manufacture "custom rigging solutions" tailored to unique project challenges and international standards.
-
Competitive Global Pricing: Offering superior value and ROI to international clients.
-
Comprehensive One-Stop Service: Providing both the heavy machinery and the essential tools and accessories, backed by strong after-sales support and efficient global logistics.
"Cable Rigging Equipment" refers to specialized machinery and systems designed for the safe, controlled, and precise lifting, lowering, pulling, and positioning of extremely heavy and often oversized components within power infrastructure projects. While it can include elements used in cable pulling, its core functions extend to:
-
Transformer Installation: Lifting and precisely setting large power transformers within substations.
-
Tower & Pole Erection: Hoisting and assembling sections of transmission towers or positioning heavy poles.
-
Substation Busbar & Equipment Placement: Rigging and installing heavy busbar systems, circuit breakers, and other electrical apparatus.
-
Generator & Turbine Components: Handling large components within power generation facilities.
-
Heavy Conductor Reel Handling: Moving and positioning extremely large and heavy conductor drums for stringing operations.
Essentially, it's the critical equipment that enables the safe movement and installation of the most substantial elements of an electrical grid.
"Cable Rigging Equipment" is paramount for both efficiency and safety:
-
Enhanced Safety: By providing controlled lifting capacities and stability, it minimizes the risks associated with manual handling of heavy loads, preventing injuries and equipment damage. Features like anti-overload systems and remote controls further mitigate hazards.
-
Precision Placement: Allows for millimeter-level accuracy in positioning large components, which is critical for electrical connections and structural integrity.
-
Increased Efficiency: Accelerates project timelines by enabling faster, more predictable lifts and reducing the need for multiple manual handling steps.
-
Damage Prevention: Protects expensive and sensitive electrical components from damage during transport and installation through stable and controlled movements.
-
Adaptability: Many modern systems are modular and adaptable, allowing for efficient setup in various challenging site conditions.
The industry is witnessing significant advancements in "smart rigging solutions," revolutionizing how heavy lifts are performed:
-
Integrated Load Monitoring Systems (LMS): Real-time digital readouts of load weight, center of gravity, and dynamic forces, often with predictive analytics to prevent overloads.
-
Remote Control & Wireless Operation: Operators can control complex lifts from a safe distance with enhanced visibility, improving precision and reducing personnel exposure to risk.
-
Automated Synchonization: For multi-point lifts (e.g., hydraulic gantries), systems automatically synchronize movements to maintain perfect load balance, preventing torsion and instability.
-
Telematics & IoT Integration: Remote diagnostics, GPS tracking, and operational data logging for optimized maintenance scheduling, asset management, and performance analysis.
-
Virtual Reality (VR) / Augmented Reality (AR) for Planning: Used to simulate complex rigging scenarios, identify potential clashes, and train operators before actual execution.
"Hydraulic lifting gantries" are increasingly the preferred "Cable Rigging Equipment" for heavy lifts in substations due to their versatility and precision, especially in confined spaces:
-
High Capacity & Stability: Capable of lifting enormous weights (hundreds or even thousands of tons), providing exceptional stability even with asymmetric loads.
-
Low Headroom Operation: Can operate effectively where overhead crane access is impossible or restricted due to existing structures or limited height.
-
Controlled Movement: Hydraulic cylinders allow for incredibly precise vertical lifting, lowering, and horizontal "walking" (skidding) of loads into exact positions.
-
Modular Design: Can be configured to various widths and heights, making them highly adaptable to different substation layouts and equipment dimensions.
They are indispensable for installing large transformers, reactors, and other critical substation components with minimal disruption.
When sourcing "Cable Rigging Equipment" globally, prioritizing safety is paramount. Look for equipment that complies with:
-
ISO 9001 (Quality Management System): Indicates a manufacturer's commitment to consistent quality control and adherence to documented processes.
-
CE Marking (for European markets): Demonstrates conformity with EU health, safety, and environmental protection directives.
-
ASME (American Society of Mechanical Engineers) Standards: Particularly ASME B30 series for lifting and rigging equipment, widely recognized for best practices.
-
IEC (International Electrotechnical Commission) Standards: Relevant for the electrical components and overall safety in an electrical environment.
-
Local/National Occupational Safety & Health (OSH) Regulations: Ensure the equipment can operate safely within your specific country's legal framework (e.g., OSHA in the US).
We ensure our equipment meets stringent global standards, providing the necessary documentation and certifications.
Adhering to "best practices" is crucial for maximizing safety and longevity:
-
Qualified Personnel: Only certified and experienced riggers and operators should handle "Cable Rigging Equipment."
-
Pre-Lift Planning: Thorough planning including load weight calculation, center of gravity determination, lift path analysis, and risk assessment.
-
Daily Equipment Inspection: Inspect all components (slings, shackles, hooks, wire ropes, hydraulics, controls) before each shift for wear, damage, or defects.
-
Adherence to Load Charts: Never exceed the manufacturer's rated capacities or work outside safe operating parameters.
-
Proper Communication: Clear and consistent communication among the rigging crew, often utilizing two-way radios.
-
Exclusion Zones: Establish and maintain clear exclusion zones around the lift area to protect personnel.
-
Regular Maintenance: Implement a preventative maintenance schedule as per manufacturer guidelines, including fluid checks, lubrication, and structural integrity inspections.
-
Comprehensive Training: Ongoing training and refresher courses for all personnel involved in rigging operations.
Absolutely. As a leading China manufacturer, we specialize in providing "custom rigging solutions" for the most challenging electrical construction projects. Our engineering team works closely with clients to understand their precise needs, including:
-
Specific Lifting Capacities & Dimensions: Designing equipment for loads exceeding standard capabilities or fitting into constrained spaces.
-
Terrain Adaptations: Developing systems for challenging ground conditions, slopes, or remote access sites.
-
Integration with Existing Systems: Ensuring compatibility with other construction machinery or project-specific interfaces.
-
Specialized Environmental Conditions: Designing for extreme temperatures, corrosive environments, or high wind loads.
Our ability to offer bespoke solutions sets us apart in the global market.
Choosing us as your "global rigging equipment supplier" offers distinct advantages:
-
One-Stop Comprehensive Solution: We provide not just "Cable Rigging Equipment" but a full spectrum of OHTL stringing and underground cable laying equipment and tools, simplifying procurement.
-
Competitive Global Pricing: Leverage our efficient manufacturing and supply chain in China to access high-quality equipment at highly competitive prices.
-
Robust Quality & Reliability: Our products are engineered and manufactured to stringent international quality standards, ensuring durability and performance in diverse global operating conditions.
-
Innovation & Advanced Technology: We integrate the latest advancements in automation, safety, and efficiency into our equipment.
-
Dedicated Global Support: Comprehensive after-sales service, including technical consultation, training, and prompt spare parts availability, no matter where your project is located.
-
Proven Export Experience: Seamless logistics and customs handling for worldwide delivery.
The essential "Cable Rigging Tools" form the backbone of any safe and efficient heavy lift. These include:
-
Shackles: Crucial for connecting various rigging components (slings, hooks, lifting points), available in bow and D-shapes, made from high-strength alloy steel, often galvanized for corrosion resistance.
-
Slings: Used to cradle or attach to the load. Types include wire rope slings, chain slings, and synthetic slings (e.g., polyester round slings or web slings) – chosen based on load weight, shape, and surface protection needs.
-
Hooks: Connectors for slings to lifting machines or other rigging points, often with safety latches to prevent accidental disengagement.
-
Turnbuckles: Adjustable devices used to tension rigging lines or make fine length adjustments for precise load positioning.
-
Wire Rope Clips & Thimbles: Used to create secure loops or eyes in wire ropes, protecting them from wear at connection points.
Each of these tools plays a vital role in distributing load forces and ensuring safe handling.
Innovation in "rigging slings" focuses on increased strength-to-weight ratios, durability, and enhanced conductor/component protection:
-
High-Performance Synthetic Slings: Made from advanced fibers like UHMWPE (Ultra-High Molecular Weight Polyethylene), these slings are incredibly strong yet lightweight, highly resistant to abrasion, chemicals, UV, and are non-conductive, making them ideal for sensitive electrical equipment.
-
Alloy Chain Slings (Grade 80, 100, 120): Continuous improvements in alloy steel provide higher working load limits (WLL) with smaller chain sizes, making them more compact yet robust.
-
Wire Rope Slings: Advancements in wire rope construction (e.g., compacted strands, specialized coatings) offer improved fatigue resistance and longer service life.
-
Built-in Wear Indicators & RFID Tags: Newer slings may feature visual wear indicators or embedded RFID tags for easier inspection, tracking, and compliance management.
Installing massive substation transformers and other heavy electrical components requires highly specialized "Cable Rigging Tools" designed for precision and control:
-
Transformer Skidding Systems: Often a combination of low-friction pads, hydraulic pushing cylinders, and track systems for horizontally moving transformers with extreme precision.
-
Heavy-Duty Shackles & Slings: With capacities designed for the immense weight of transformers, often multiple slings used in a basket or bridle hitch.
-
Spreader Beams & Lifting Beams: Crucial for distributing the load over multiple points, preventing crushing or deformation of the transformer's delicate structure.
-
Hydraulic Jacks & Climbing Jacks: For precise vertical positioning and leveling of equipment.
-
Precision Alignment Tools: Used to ensure accurate placement and connection of busbars and other electrical interfaces.
These tools work in concert with heavy lifting equipment (like hydraulic gantries) to ensure safe and accurate installation.
Safety is engineered into every "Cable Rigging Tool" we manufacture:
-
High Safety Factors: All tools are designed with a significant safety margin (e.g., 5:1 or higher) between their ultimate breaking strength and their rated working load limit (WLL).
-
Clear Markings: Every tool is permanently marked with its WLL, size, and manufacturer for easy identification and compliance.
-
Proof Testing: Many critical rigging tools undergo individual proof testing to a percentage of their WLL to verify their strength and integrity.
-
Material Traceability: Full traceability of raw materials ensures quality and consistency.
-
Anti-Corrosion Coatings: Galvanization, painting, or specialized finishes protect tools in harsh environments, preventing material degradation that could compromise strength.
-
Safety Latches on Hooks: Designed to prevent accidental disengagement of loads.
-
Conductor Protection Features: Smooth surfaces, non-metallic linings, or specific geometries to prevent damage to cables and conductors.
Rigorous inspection and maintenance are vital for "Cable Rigging Tools":
-
Pre-Use Inspection: A mandatory visual check for damage, deformation, corrosion, cracks, or excessive wear before every shift. Any defective tool must be immediately removed from service.
-
Frequent & Periodic Inspections: Regular, documented inspections by a competent person (daily, weekly, monthly, or annually based on usage and regulations) ensure ongoing compliance and safety.
-
Load Testing: Periodic load testing, especially for critical or repaired tools, verifies their continued load-bearing capacity.
-
Proper Storage: Storing tools in a clean, dry environment, protected from impacts and extreme temperatures, prevents premature degradation.
-
Lubrication: Proper lubrication of moving parts (e.g., shackles pins, turnbuckle threads) reduces wear and extends lifespan.
-
Training: Proper training ensures personnel understand how to correctly inspect, use, and maintain rigging tools, directly impacting their safety and efficacy.
-
Partnering with us for your "Cable Rigging Tools" offers significant benefits to international clients:
-
Cost-Effectiveness & Value: Our efficient manufacturing processes allow us to offer high-quality, durable rigging tools at highly competitive prices, providing excellent value for your investment.
-
Comprehensive Range: As a one-stop supplier, we provide a vast selection of rigging tools alongside our tension stringing and underground cable laying equipment, streamlining your procurement.
-
Adherence to Global Standards: All our tools are manufactured to comply with international quality and safety standards (e.g., ISO, CE, ASME principles), ensuring global usability and acceptance.
-
Robust Quality Control: Rigorous testing and inspection throughout the production process guarantee the reliability and safety of every tool.
-
Customization Capabilities: We can fabricate specialized or custom "rigging tools" to meet unique project specifications or challenging lifting scenarios.
-
Reliable Global Logistics: Our experience as an international exporter ensures smooth, efficient, and timely delivery of tools to job sites worldwide.
-
We prioritize durability and longevity for demanding global applications:
-
Premium Materials: We utilize only high-grade alloy steels, specialized composites, and advanced synthetic fibers known for their strength, fatigue resistance, and wear characteristics.
-
Advanced Manufacturing Processes: Precision forging, heat treatment, and specialized welding techniques ensure structural integrity and consistent performance.
-
Superior Corrosion Protection: Tools are treated with robust coatings (e.g., hot-dip galvanization, powder coating, or marine-grade finishes) to withstand harsh weather, corrosive atmospheres, and marine environments.
-
Robust Design: Our tools are engineered to minimize stress concentrations and withstand the repeated cycles of heavy-duty lifting.
-
Quality Assurance & Testing: Each batch undergoes stringent quality control, including material analysis, dimensional checks, and destructive/non-destructive testing to validate performance and lifespan.
The latest "wireless load shackles" and "Bluetooth dynamometers" are revolutionary "Cable Rigging Accessories" that provide real-time, accurate load data. These smart devices are designed to be integrated directly into your rigging setup (e.g., as part of a sling or between a shackle and a hook).
-
Real-time Monitoring: They transmit precise weight and force measurements wirelessly to a handheld device (smartphone/tablet with an app) or a dedicated receiver.
-
Enhanced Safety: Operators get immediate alerts for approaching overload conditions, allowing for proactive adjustments and preventing dangerous situations.
-
Precision Lifting: Enables highly accurate load distribution in complex multi-point lifts, ensuring stability and preventing damage to delicate components like transformers or busbars.
-
Data Logging & Reporting: Automatically record lift data, crucial for compliance, post-operation analysis, and optimizing future rigging plans.
These accessories are transforming rigging by making operations safer, more efficient, and data-driven.
"Smart rigging sensors" (which can include integrated load cells, tilt sensors, or even RFID tags) are a growing trend in "Cable Rigging Accessories." Beyond real-time monitoring, they gather data over time about:
-
Usage Patterns: How frequently and heavily rigging components are used.
-
Environmental Exposure: Data on temperature, humidity, or corrosive elements.
-
Stress Cycles: Recording fatigue on specific components.
This data, often integrated via IoT (Internet of Things) platforms, feeds into predictive maintenance programs. Instead of relying on time-based schedules, maintenance can be performed when it's genuinely needed, extending the lifespan of accessories, reducing unexpected downtime, and ensuring the highest level of safety and operational efficiency for long-term projects.