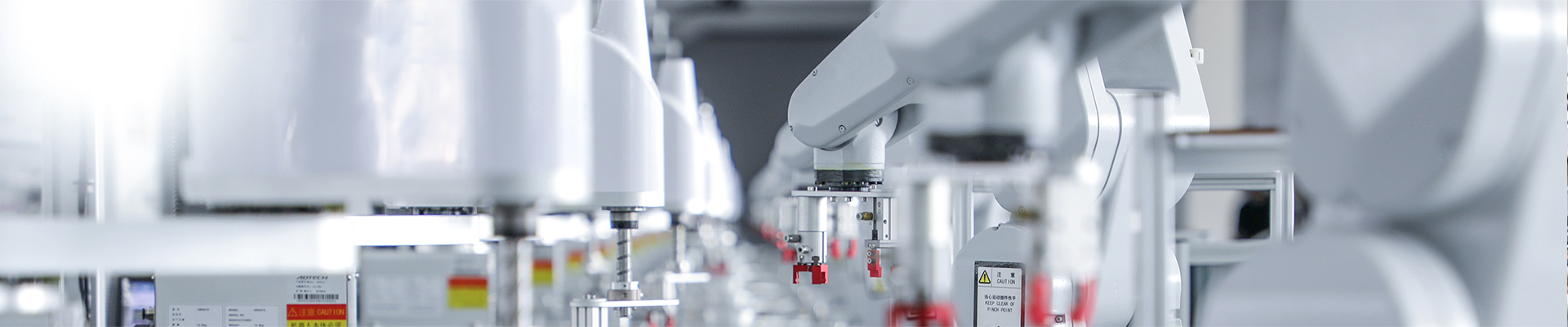
FAQ
The integration of "smart" features and automation is rapidly transforming Cable Installation Equipment, leading to unprecedented levels of precision, efficiency, and safety. Key trends include:
-
Real-time Data Acquisition & Telemetry (IoT Integration): Equipment is equipped with a multitude of sensors that continuously monitor critical operational parameters such as pulling force (tension), speed, length of cable installed, depth, hydraulic pressures, engine diagnostics, and more. This data is displayed on intuitive digital interfaces and transmitted wirelessly via IoT (Internet of Things) to remote monitoring platforms or mobile devices.
-
Automated Tension and Speed Control (Closed-Loop Systems): Advanced electronic and hydraulic control systems can be programmed to maintain a precise, constant pulling or stringing tension, automatically adjusting machine speed as ground conditions, friction, or terrain change. This is crucial for preventing over-tensioning and ensuring uniform sag in OHTL, or preventing damage to delicate underground cables.
-
High-Precision GPS/GNSS Integration: Integrated Global Navigation Satellite Systems (GNSS) with RTK (Real-Time Kinematic) accuracy allow for highly precise pre-mapping of cable routes and guide the machine exactly along the planned path. This ensures exact cable placement, minimizes deviations, and provides accurate "as-built" documentation, which is invaluable for future maintenance and digital twin initiatives.
-
Predictive Maintenance & AI Analytics: Leveraging real-time and historical operational data, onboard AI and machine learning algorithms can predict potential mechanical failures or maintenance needs (e.g., component wear, fluid degradation). This enables proactive scheduling of maintenance, significantly reducing unplanned downtime, costly emergency repairs, and extending equipment lifespan.
-
Remote Monitoring & Control Capabilities: Operators and project managers can monitor machine performance, track progress, and receive alerts from a central location. In some advanced systems, limited remote control functionalities (e.g., start/stop, speed adjustment) can be performed from a safe distance, enhancing operator safety and operational flexibility.
-
Integrated Diagnostics: Advanced diagnostic systems quickly identify and pinpoint issues, guiding technicians to efficient troubleshooting and repair.
-
Automated Cable Loading/Unloading & Management: For large cable drums, automated or semi-automated systems for loading, unwinding, and coiling ensure safer and more efficient material handling. Some offshore cable laying vessels even feature autonomous cable transfer systems.
These intelligent features transform cable installation into a highly controlled, data-driven, and safer process, delivering superior project outcomes and enabling the construction of more reliable power and communication networks.
Modern "Cable Installation Equipment" is increasingly designed with a strong focus on environmental sustainability, significantly reducing the ecological footprint of infrastructure projects:
-
Enabling Trenchless Technologies: A major contribution comes from the widespread adoption and advancement of trenchless installation methods. Equipment like Horizontal Directional Drills (HDD), vibratory plows, and micro-trenchers allow for cable installation with minimal surface disruption. This preserves existing landscapes, ecosystems, roads, and urban infrastructure, reducing the need for extensive excavation, backfilling, and surface restoration.
-
Reduced Ground Disturbance (OHTL): For overhead tension stringing, precise tensioners prevent conductors from dragging on the ground, thereby minimizing damage to sensitive topsoil, vegetation, and natural habitats along the right-of-way.
-
Lower Fuel Consumption & Emissions: Modern equipment is fitted with advanced, fuel-efficient engines that comply with stringent global emission standards (e.g., EU Stage V, EPA Tier 4 Final). Optimized hydraulic systems and smart controls reduce energy consumption during operation. The increasing availability of hybrid and electric-powered machines further reduces reliance on fossil fuels and cuts down on greenhouse gas emissions.
-
Minimized Material Waste & Cable Damage: Precise control systems, automated tension management, and real-time monitoring significantly reduce the risk of costly cable damage during installation. This minimizes material waste from damaged cables that would otherwise need to be scrapped, conserving resources.
-
Reduced Noise Pollution: Innovations in engine design, noise suppression technologies, and advanced hydraulics contribute to quieter operations, lessening the acoustic impact on local communities, wildlife, and improving worksite conditions.
-
Efficient Waste Management: Some integrated trenching systems are designed to manage excavated spoil more efficiently, and in trenchless methods, the volume of spoil is drastically reduced.
-
Water Conservation: Techniques like dry boring (for some HDD applications) or efficient dust suppression systems can reduce water usage on job sites.
By promoting less invasive methods, optimizing energy use, and minimizing waste, modern Cable Installation Equipment is crucial for developing sustainable and environmentally responsible power and communication infrastructure globally.
HVDC and offshore wind farm projects represent some of the most demanding cable installation challenges, requiring highly specialized "Cable Installation Equipment" designed for immense scale, extreme environments, and sensitive cable types:
-
For Offshore Wind Farm Export & Inter-Array Cables:
-
Specialized Cable Laying Vessels (CLVs): These are large, purpose-built ships equipped with massive carousels (some holding over 10,000 tons of cable), linear cable engines (LCEs) that precisely control payout tension, and sophisticated navigation systems (e.g., DP2 dynamic positioning) to maintain exact position in complex marine environments.
-
Subsea Plows & Trenchers: Towed or remotely operated vehicles (ROVs) deployed from CLVs that create trenches on the seabed and simultaneously or immediately bury the cable for protection against anchors, fishing gear, and environmental abrasion. They can be mechanical or use high-pressure water jetting.
-
ROVs (Remotely Operated Vehicles): Used for precise seabed surveys, pre-lay inspection, post-lay burial verification, and intervention during cable repair.
-
Cable Protection Systems (CPS) Installation Equipment: Tools and systems for installing protection sleeves, rock dump, or concrete mattresses over critical cable sections.
-
-
For HVDC Land Cables & Converter Station Connections:
-
Ultra-High Capacity Hydraulic Pullers/Tensioners: HVDC land cables are often extremely large, heavy, and stiff. Installation requires pullers with capacities sometimes exceeding 100 tons, featuring multi-bullwheel designs for even pressure distribution and advanced tension control.
-
Heavy-Duty Cable Conveyors/Pushers: These track-mounted units apply significant pushing force directly to the HVDC cable, reducing friction and sidewall pressure, especially crucial for long pulls through tunnels, bridges, or multiple bends.
-
Large-Scale Horizontal Directional Drills (HDDs): Capable of creating large-diameter bores over exceptionally long distances (several kilometers) for HVDC conduit crossings under major rivers, mountains, or densely populated areas.
-
Specialized Cable Drum Management Systems: Robust hydraulic drum stands and motorized re-winders designed to handle the immense weight and size of HVDC cable drums (often requiring specialized transport).
-
These pieces of equipment are at the forefront of engineering, enabling the crucial expansion of renewable energy and the development of high-capacity, efficient power transmission grids globally.
For international buyers investing in significant "Cable Installation Equipment," comprehensive after-sales support and services are absolutely vital for maximizing equipment uptime, ensuring project success, and realizing a strong return on investment. Customers should expect:
-
Dedicated Technical Support & Helpdesk:
-
Multilingual Support: Access to technical experts fluent in key international languages to bridge communication gaps across different time zones.
-
24/7 Availability: Critical support available around the clock to address urgent issues and minimize project downtime.
-
Remote Diagnostics: Leveraging telematics and IoT capabilities to remotely access machine data, diagnose issues, and guide local technicians through troubleshooting, often resolving problems without a physical visit.
-
-
Global Spare Parts Availability & Logistics:
-
Strategically Located Warehouses: A network of international warehouses or efficient logistics partnerships to ensure rapid delivery of critical, genuine spare parts to project sites worldwide, minimizing costly delays.
-
Guaranteed Parts Supply: A commitment from the manufacturer to provide spare parts for the entire operational lifespan of the equipment, preventing obsolescence.
-
Online Parts Catalogues & Ordering: User-friendly online platforms for easy identification, selection, and ordering of parts.
-
-
Comprehensive Training Programs:
-
On-site & Virtual Training: Offering in-depth training for operators and maintenance personnel, either directly at the customer's project site or through interactive virtual platforms. This covers safe operation, advanced functions, routine maintenance, and basic troubleshooting.
-
Certified Training: Providing certification programs to ensure operators and technicians meet international competency standards, enhancing safety and efficiency.
-
Detailed Documentation: Supplying comprehensive operation and maintenance manuals, schematics, parts lists, and video tutorials in relevant languages.
-
-
Field Service & Expert Technicians:
-
Global Network of Certified Technicians: Access to highly skilled, factory-trained field service engineers capable of performing complex repairs, major overhauls, software updates, and specialized commissioning.
-
Rapid Dispatch: Efficient dispatch systems to deploy technicians quickly to international project sites when remote resolution isn't sufficient.
-
-
Warranty & Service Level Agreements (SLAs):
-
Robust Warranty: A clear and comprehensive warranty covering manufacturing defects and major components.
-
Flexible Service Contracts: Offering various tiers of service contracts that include scheduled preventative maintenance, priority support, guaranteed response times, and even full-service agreements to ensure maximum equipment availability and predictable costs.
-
-
Technical Updates & Continuous Improvement:
-
Software Updates: Regular provision of software updates for machine control systems to improve performance, add new features, and enhance security.
-
Product Enhancements: Information and upgrades on new features or component improvements that can be retrofitted to existing equipment.
-
Technical Bulletins: Dissemination of important technical bulletins and service advisories.
-
This level of robust after-sales support reflects a manufacturer's dedication to its international clientele's long-term success and underscores the reliability of its "Cable Installation Equipment."
In 2025, "Cable Installation Equipment" must adhere to a complex array of international and regional safety standards and certifications to ensure worker safety, environmental protection, and legal compliance. Key standards and certifications include:
-
CE Marking (European Conformity): Mandatory for equipment sold within the European Economic Area (EEA), indicating compliance with essential health, safety, and environmental protection requirements as outlined in various EU Directives (e.g., Machinery Directive 2006/42/EC, EMC Directive 2014/30/EU, Low Voltage Directive 2014/35/EU).
-
ISO Standards (International Organization for Standardization):
-
ISO 12100 (Safety of machinery – General principles for design – Risk assessment and risk reduction): Provides fundamental guidelines for safe machine design.
-
ISO 13849 (Safety of machinery – Safety-related parts of control systems): Specifies requirements for the design and integration of safety-related parts of control systems, including software.
-
ISO 4306-1 (Cranes – Vocabulary – Part 1: General): Relevant for hoisting and lifting components often integrated with installation equipment.
-
ISO 21975 (Construction and earth-moving machinery – Safety): General safety requirements for earth-moving machinery, applicable to trenchers and HDDs.
-
-
ANSI (American National Standards Institute) / OSHA (Occupational Safety and and Health Administration): In North America, equipment must comply with relevant ANSI standards (e.g., ANSI/ASSE A10 series for construction and demolition operations, ANSI B30.5 for mobile and locomotive cranes) and OSHA regulations (e.g., 29 CFR 1926 Subpart N for Cranes and Derricks in Construction).
-
IEC Standards (International Electrotechnical Commission):
-
EN IEC 60204-32:2025 (Safety of machinery - Electrical equipment of machines - Part 32: Requirements for hoisting machines): Highly relevant for the electrical components and systems of pulling machines, tensioners, and winches.
-
IEC 61000 series: For Electromagnetic Compatibility (EMC), ensuring the equipment does not interfere with other electronic devices and is immune to external electromagnetic disturbances.
-
-
National/Local Regulatory Bodies: Manufacturers must also adhere to specific country-level regulations and standards (e.g., WorkSafe in Australia, HSE in the UK, various national electrical codes).
-
ROPS/FOPS (Roll-Over Protective Structures / Falling Object Protective Structures): Essential certifications for operator cabins on mobile equipment, protecting personnel from rollovers or falling debris.
-
Environmental Standards: Compliance with local and international emission regulations (e.g., Tier 4 Final, Stage V for diesel engines) and noise limits.
A reputable manufacturer will provide documentation demonstrating compliance with these critical standards and offer equipment that integrates robust safety features such as automatic overload protection, emergency stop systems, comprehensive guarding, interlocks, and clear warning labels to ensure safe operation.
"Cable Installation Tools" refer to the portable, often handheld, specialized devices and instruments used directly by technicians and workers during various stages of cable deployment, termination, and maintenance. They are designed for precision, localized tasks, and direct interaction with the cable itself.
They differ from "Cable Installation Equipment" primarily in scale, function, and mobility:
-
Cable Installation Equipment: Encompasses large, often heavy-duty machinery and systems that perform the primary tasks of pulling, tensioning, trenching, or blowing cables over significant distances. Examples include hydraulic pulling winches, cable tensioners, trenchers, horizontal directional drills, and fiber optic blowing machines. These are typically vehicle-mounted, trailer-mounted, or self-propelled units.
-
Cable Installation Tools: These are the essential implements that complement the larger equipment. They are used for:
-
Preparation: Cutting, stripping, and preparing cable ends.
-
Guidance & Protection: Smaller rollers, cable guides, lubrication application.
-
Termination & Splicing: Crimpers, cleavers, fusion splicers (portable), punchdown tools.
-
Measurement & Testing: Portable multi-meters, network testers, visual fault locators.
-
Safety: Insulated hand tools, lockout/tagout devices.
-
Essentially, "Equipment" provides the power and bulk movement, while "Tools" provide the precision, intricate manipulation, and finishing touches that ensure a high-quality, safe, and reliable cable installation.
"Cable Cutting and Stripping Tools" are foundational for any cable installation, and recent innovations focus on improved precision, ergonomics, and versatility:
-
Battery-Powered Hydraulic Cutters: For larger power cables (MV/HV), compact, lightweight, battery-powered hydraulic cutters are revolutionizing efficiency. They offer:
-
Effortless Cutting: Significantly reduce manual effort, preventing fatigue and injuries.
-
Clean Cuts: Ensure precise, burr-free cuts critical for proper termination.
-
Portability: Eliminate the need for external power sources or heavy hydraulic pumps, increasing mobility on job sites.
-
Integrated Jaws: Interchangeable jaws for different cable types (copper, aluminum, armored, ACSR).
-
-
Precision Automatic Strippers: For both power and data cables, new strippers offer:
-
Self-Adjusting Blades: Automatically adapt to various cable diameters and insulation thicknesses, eliminating the need for manual adjustment and preventing conductor damage.
-
Multi-Stage Stripping: Capable of removing multiple layers of insulation in one action, speeding up termination processes.
-
Spring-Loaded & Ergonomic Designs: Reduce hand fatigue, provide comfortable grip, and increase leverage for easier stripping.
-
-
Specialized Armored Cable Tools: Innovations include rotary cable strippers and scoring tools designed specifically for armored cables, allowing for clean, precise cuts through the armor without damaging the internal conductors or insulation.
-
Fiber Optic Cleavers with Enhanced Durability: For fiber optic installations, cleavers now feature more robust designs and improved blade life, ensuring consistent, high-quality end-face preparation essential for low-loss splices.
-
Multi-Function Tools: Combining cutting, stripping, and sometimes crimping capabilities into a single, compact tool, reducing the number of tools a technician needs to carry and improving workflow.
These innovations significantly enhance the speed, accuracy, and safety of cable preparation, which directly impacts the quality and reliability of the final installation.
"Crimping Tools" are essential for creating reliable, low-resistance electrical connections, and their evolution is driven by new conductor materials, stricter performance requirements, and a focus on ergonomics:
-
Battery-Powered Hydraulic Crimpers: Similar to cutters, battery-powered hydraulic crimpers have become standard for larger power cable connections (MV/HV terminals, lugs). They offer:
-
Consistent Crimp Force: Ensure a precise and repeatable crimp force, critical for electrical integrity, regardless of operator strength.
-
Reduced Manual Effort: Eliminate the need for laborious manual pumping, preventing operator fatigue and repetitive strain injuries.
-
Portability & Speed: Dramatically increase the speed of termination in the field.
-
Interchangeable Dies: Compatible with a wide range of crimping dies for different conductor sizes (AWG/MCM) and lug types (copper, aluminum, bimetallic).
-
-
Smart Crimpers with Data Logging: Some high-end crimpers now feature built-in sensors that record crimp force, time, and even GPS location. This data can be logged for quality assurance, providing proof of proper installation and traceability for critical connections.
-
Automatic Cycle Crimpers: These tools ensure a complete crimp cycle before the jaws release, preventing partial or insufficient crimps.
-
Ergonomic and Lightweight Designs: Even manual crimpers are designed with improved leverage mechanisms, comfortable grips, and lighter materials to reduce operator strain.
-
Precision Dies for Specialty Applications: Specific die sets are developed for new conductor materials (e.g., advanced aluminum alloys, compact stranded conductors) and connection types (e.g., those used in renewable energy systems, EV charging infrastructure).
-
Indenter-Type Crimpers for Flexible Conductors: For highly flexible conductors (e.g., welding cables), specialized indenter-type crimpers create a deformation that ensures excellent electrical contact without compromising flexibility.
These advancements in crimping technology ensure that connections are not only robust and electrically sound but also contribute to overall project efficiency and quality control.
Fiber optic cable termination and splicing demand a highly specialized suite of "Cable Installation Tools" due to the delicate nature of optical fibers and the precision required for low signal loss:
-
Fiber Optic Strippers: Multi-hole precision strippers (e.g., Miller, No-Nik) are crucial for carefully removing the outer jacket, buffer tube, and individual fiber coatings without nicking or damaging the delicate glass fiber itself.
-
Fiber Optic Cleavers: These are precision tools that create a perfect, perpendicular, mirror-smooth end-face on the fiber. A high-quality cleave is absolutely critical for minimal signal loss during fusion splicing or mechanical termination. Manual and semi-automatic cleavers are common, with advancements focusing on consistent angle and longer blade life.
-
Fusion Splicers: While often considered "equipment," compact, field-portable fusion splicers are essential tools for creating permanent, ultra-low-loss connections between two optical fibers. They precisely align the fibers and use an electric arc to melt and fuse them. Modern splicers feature automated alignment, touchscreens, and quick splice times.
-
Fiber Optic Cleaning Kits: Crucial for removing dust, oils, and contaminants from fiber ends before cleaving and splicing. These kits include lint-free wipes, specialized solvents (e.g., 99% isopropyl alcohol), and fiber cleaning pens/sticks. Contamination is a leading cause of signal loss.
-
Kevlar Shears: Specialized scissors designed to cut the aramid yarn (Kevlar) strength members found within many fiber optic cables, which are very difficult to cut with standard shears.
-
Visual Fault Locators (VFLs): Handheld laser devices that inject visible red light into the fiber. They are used to quickly identify breaks, tight bends, or poor connections by illuminating the fault location, making troubleshooting easier.
-
Optical Power Meters (OPMs) & Light Sources: Used together as a pair, these tools measure the optical power transmitted through the fiber and quantify signal loss, verifying the integrity of the installed cable and splices.
-
Mid-Span Access Tools: Specialized tools designed to open fiber optic cable jackets mid-span without cutting through the entire cable, allowing access to internal fiber bundles for branching or repair.
-
Protective Work Mats & Waste Bins: Black, non-reflective work mats help in easily identifying tiny fiber scraps, and dedicated waste bins for fiber shards are essential for safety.
The proper use and maintenance of these tools are paramount to achieving high-performance, reliable fiber optic networks.
Implementing rigorous inspection, maintenance, and calibration practices for "Cable Installation Tools" is crucial for ensuring worker safety, tool longevity, and the consistent quality of installations.
1. Regular Inspection (Before & After Each Use):
-
Visual Check: Inspect for any physical damage: cracks, bends, nicks, deformation, excessive wear, corrosion, loose fasteners, or compromised insulation (for insulated tools).
-
Functionality Check: For tools with moving parts (e.g., strippers, crimpers), test their action to ensure smooth operation without binding or excessive play. Verify that safety mechanisms (locks, guards) are fully functional.
-
Blades & Dies: Check cutting blades for sharpness, chips, or dullness. Inspect crimping dies for wear, deformation, or foreign material that could affect the crimp quality.
-
Insulated Tools: Thoroughly inspect the insulation of VDE-certified or insulated tools for any cuts, nicks, or cracks that could compromise electrical safety.
-
Cleanliness: Ensure tools are free of dirt, debris, grease, and cable residue.
2. Cleaning & Lubrication (After Each Use):
-
Clean Thoroughly: Remove all cable remnants, dirt, and moisture. Use appropriate cleaning agents based on the tool's material (e.g., mild soap and water, degreasers). For fiber optic tools, specialized cleaning solutions and lint-free wipes are critical.
-
Lubricate: Apply manufacturer-recommended lubricants to pivot points, hinges, and moving mechanisms to ensure smooth operation and prevent wear and corrosion.
3. Proper Storage:
-
Dry & Protected: Store tools in a dry, cool, and well-ventilated area, preferably in dedicated toolboxes, trays, or on shadow boards. Protect them from direct sunlight, extreme temperatures, dust, and moisture.
-
Organized: Proper organization prevents damage from tools rattling against each other and makes it easy to identify missing or damaged items.
-
Blade/Edge Protection: Use blade guards or ensure tools with sharp edges are stored in a way that prevents dulling or accidental cuts.
-
Protective Cases: Store sensitive tools (e.g., fiber cleavers, fusion splicers, measuring instruments) in their original padded, protective cases.
4. Periodic Professional Maintenance & Calibration:
-
Sharpening/Replacement: Regularly sharpen or replace cutting blades and worn crimping dies according to manufacturer guidelines.
-
Calibration: All measuring and testing tools (e.g., torque wrenches, dynamometers, optical power meters, OTDRs) must be professionally calibrated at regular, certified intervals (e.g., annually or bi-annually) to guarantee their accuracy. Maintain detailed calibration records.
-
Wear Parts: Proactively replace common wear parts (e.g., springs, certain jaws) before they fail.
5. Removal from Service:
-
Any tool showing significant damage, a compromise to its integrity (especially insulated tools), or failing a functional check must be immediately tagged and removed from service. Do not attempt to repair safety-critical tools unless you are a certified technician following strict manufacturer guidelines.
Adhering to these best practices significantly extends the working life of your valuable cable installation tools, maintains their performance, and, most importantly, ensures the safety of your personnel on every job.
Modern "Cable Installation Tools" are designed with safety and ergonomics as paramount considerations, reflecting a global emphasis on worker well-being and accident prevention:
Safety Standards & Certifications:
-
IEC 60900 (Live Working - Hand Tools for Use Up to 1000 V AC and 1500 V DC): This is a critical international standard for insulated hand tools used near live electrical components. Tools meeting this standard are individually tested and certified to provide protection against electrical shock.
-
ISO 12100 (Safety of machinery – General principles for design – Risk assessment and risk reduction): While primarily for machinery, its principles apply to the design of complex power tools (e.g., battery-powered cutters/crimpers) to identify and mitigate risks.
-
OSHA (Occupational Safety and Health Administration) & National Regulations: Compliance with specific national safety regulations is crucial (e.g., proper guarding, lockout/tagout provisions, eye/hand protection requirements).
-
Material Safety: Use of non-toxic, non-flammable materials where appropriate, especially for handles and lubricants.
-
Blade Guards & Safety Locks: Cutting tools often feature integrated blade guards or safety locks to prevent accidental deployment or contact with sharp edges when not in use.
Ergonomic Considerations:
-
Reduced Hand Fatigue & Strain:
-
Leverage & Gearing: Designs incorporate optimized leverage ratios, gearing mechanisms, or hydraulic assistance to minimize the force required by the operator, reducing repetitive strain injuries (RSI).
-
Spring-Loaded Mechanisms: Many strippers and pliers are spring-loaded to reduce the effort needed for repeated opening and closing.
-
Power Tools: The shift to battery-powered tools (cutters, crimpers, drills) significantly reduces physical exertion.
-
-
Comfortable & Non-Slip Grips: Handles are designed with soft, non-slip, often multi-component materials that fit comfortably in the hand, provide a secure grip, and absorb vibrations.
-
Balanced Weight Distribution: Tools are balanced to minimize awkward movements and muscle strain during prolonged use.
-
Compact & Lightweight Design: For tools used in confined spaces or overhead, compact and lightweight designs are preferred to improve maneuverability and reduce fatigue.
-
Visibility & Lighting: Some tools incorporate integrated LED lighting to illuminate the work area, improving precision and reducing the risk of accidents in low-light conditions.
-
Noise and Vibration Reduction: For power tools, efforts are made to reduce noise levels and vibration transmitted to the operator's hands and arms.
By prioritizing these safety and ergonomic features, manufacturers ensure that "Cable Installation Tools" not only perform their functions effectively but also contribute significantly to the health, safety, and productivity of the skilled professionals who use them daily.
"Cable Installation Accessories" are a diverse range of supplementary components, often passive or consumable, that are essential for the proper installation, protection, identification, and secure functioning of cables in both overhead transmission line (OHTL) and underground/subsea applications. Unlike "Equipment" (the machines) or "Tools" (the handheld implements), accessories are typically integrated with the cable or its immediate environment.
They are critical for long-term reliability because they:
-
Provide Electrical Integrity: Accessories like cable joints, terminations, and lugs ensure secure, low-resistance electrical connections, preventing hot spots, power loss, and failures.
-
Offer Mechanical Protection: Cable cleats, ties, ducts, and protective covers shield cables from physical damage (e.g., abrasion, crushing, impacts) during and after installation, extending their lifespan.
-
Ensure Environmental Sealing: Glands, seals, and heat/cold shrink tubes prevent moisture, contaminants, and corrosive elements from entering critical connection points, preserving insulation and conductor integrity.
-
Manage Stress and Vibration: Specialized dampeners, spacers, and rollers reduce mechanical stress, vibration, and friction on cables during stringing and throughout their operational life.
-
Facilitate Identification and Management: Markers, labels, and warning tapes provide crucial identification for maintenance, troubleshooting, and preventing accidental damage.
-
Maintain Performance: Lubricants reduce pulling friction, preventing cable damage during installation, while stress cones in terminations manage electrical fields to prevent premature breakdown.
Without these seemingly small but vital components, even the highest quality cables and equipment would fail to deliver the expected long-term performance and reliability that modern power and communication networks demand.
Protecting underground and direct-buried cables from external threats is paramount for network longevity. Recent advancements in "Cable Protection Accessories" focus on enhanced durability, detectability, and intelligent features:
-
High-Strength, Lightweight Ducting & Troughing:
-
Advanced Polymers & Composites: Replacing traditional concrete, new ducting and troughing systems are made from high-density polyethylene (HDPE), polypropylene (PP), or Glass Reinforced Polymer (GRP) composites. These offer superior impact resistance, chemical resistance, UV stability, and are significantly lighter, making installation faster and safer (e.g., single-person lift solutions for troughing).
-
Interlocking Systems: Innovative interlocking mechanisms ensure quick, secure, and flexible assembly of ducting and troughing sections, adapting to varied terrain and curves.
-
Fire Retardant Options: For sensitive applications (e.g., rail, data centers), fire-retardant GRP troughing systems are now common.
-
-
Detectable Warning Tapes & Electronic Markers:
-
Integrated Metal Strips/Wires: Non-metallic warning tapes now commonly embed a metallic or conductive strip, allowing them to be easily located from the surface using standard cable/pipe locators, even if the cable beneath is non-metallic or de-energized.
-
Passive RFID Markers: Small, passive RFID markers can be buried with the cable, programmable with detailed information (cable type, installation date, depth, ownership). These can be precisely located and read by handheld RFID readers, offering highly accurate asset identification.
-
-
Advanced Duct Seals & Plugs: Enhanced designs and materials (e.g., silicone gel-filled, rubber, or mechanical compression seals) provide superior watertight and gas-tight sealing of conduits at manhole entries, building penetrations, or between duct sections. This prevents moisture ingress, rodent entry, and gas migration, critical for maintaining cable integrity.
-
Anti-Dig Mesh/Grids: Robust, often brightly colored, polymer mesh or grid systems are laid above direct-buried cables as an additional physical barrier and visual warning layer, deterring accidental excavation.
-
Customizable Solutions: Manufacturers now offer highly customizable options for ducting (different sizes, colors for utility identification), warning tapes (custom messaging, logos), and markers.
These innovations collectively ensure a more robust, identifiable, and durable underground cable infrastructure, significantly reducing the risk of costly damage and service interruptions.
"Cable Pulling Lubricants and Gels" are indispensable accessories that significantly reduce friction during cable installation, preventing damage and ensuring successful pulls, especially over long distances or through complex conduit runs with multiple bends.
Their contributions include:
-
Drastic Friction Reduction: They form a low-friction film between the cable jacket and the inner surface of the conduit/duct. This can reduce pulling tensions by as much as 50-80%, greatly minimizing the stress on the cable and the pulling equipment.
-
Preventing Cable Damage:
-
Abrasions & Kinking: By reducing friction, lubricants prevent the cable jacket from abrading against conduit walls, especially around bends or rough spots. They also help prevent the cable from kinking or buckling under excessive compression from pulling forces.
-
Overheating: Lower friction also means less heat generation during the pull, protecting cable insulation from thermal damage.
-
Stretch: Minimizing pulling tension reduces the risk of stretching or deforming the conductor or sensitive optical fibers.
-
-
Facilitating Longer Pulls: With reduced friction, longer continuous cable pulls become feasible, minimizing the need for intermediate pulling pits, saving time and costs.
-
Optimizing Equipment Performance: Lower pulling tensions reduce the strain on pulling winches and other equipment, extending their lifespan and requiring less power consumption.
-
Environmental Compatibility: Modern lubricants are typically:
-
Non-Toxic & Biodegradable: Formulated to be environmentally safe, non-flammable, and easily biodegradable, especially important for outdoor applications.
-
Residue-Free: Designed to dry to a thin, non-tacky film that doesn't clog conduits and is easy to clean up.
-
Temperature Stable: Maintain their lubricating properties across a wide range of temperatures, from freezing to high heat.
-
-
Compatibility with Cable Jackets: Formulated to be compatible with all common cable jacket materials (e.g., PVC, polyethylene, rubber), ensuring they do not degrade the cable over time.
Selecting the right lubricant, specifically designed for the cable type, conduit material, and environmental conditions, is a critical step in effective and damage-free cable installation.
In smart grids and increasingly complex network environments, precise "Cable Marking and Identification Accessories" are more crucial than ever for efficient operations, maintenance, and safety. Advancements focus on durability, digital integration, and comprehensive data:
-
Durable & Weather-Resistant Materials:
-
UV-Stable Polymers: Markers and labels are made from highly UV-resistant and chemically inert polymers (e.g., specialized PVC, polyester, vinyl, or heat-shrinkable polyolefin) that withstand harsh outdoor conditions, extreme temperatures, moisture, and common industrial chemicals without fading, cracking, or degrading.
-
Laser-Etched & Thermal Transfer Printing: These printing methods offer superior durability compared to traditional ink, ensuring legends remain legible for decades, even in challenging environments.
-
-
Digital Integration (QR Codes & RFID):
-
QR Codes/Barcodes: Markers can now feature QR codes or barcodes. Scanning these with a smartphone or tablet immediately links technicians to digital documentation, schematics, installation history, maintenance records, and real-time network data, revolutionizing troubleshooting and asset management.
-
RFID (Radio Frequency Identification) Tags: Embedded RFID tags in cable markers allow for wireless, precise identification and tracking. When scanned with an RFID reader, they can instantly retrieve comprehensive cable data, location, and maintenance history, enabling advanced inventory management and predictive maintenance strategies.
-
-
Enhanced Legibility & Customization:
-
High-Contrast Colors: Optimized color schemes for maximum legibility in various lighting conditions.
-
Pre-Printed & Customizable Options: Manufacturers offer a vast array of pre-printed legends for common applications and robust systems for custom printing specific project IDs, cable numbers, voltage levels, or company logos on demand.
-
-
Multi-Function Markers: Some accessories combine marking with other functions, such as heat-shrink markers that also provide insulation or protection, or clip-on markers that can be easily repositioned.
-
Standardization & Compliance: Emphasis on adhering to international and regional labeling standards (e.g., ANSI/TIA 606-B for telecommunications, specific electrical codes) to ensure uniformity and clarity across complex installations.
These advanced marking and identification accessories bridge the gap between physical infrastructure and digital information, enabling more intelligent, efficient, and reliable management of modern power and communication networks.
"Overhead Line Stringing Accessories" are indispensable for preventing damage to conductors and ensuring safe, efficient tension stringing of overhead transmission lines. They manage mechanical stress and facilitate smooth movement:
-
Conductor Rollers (Stringing Blocks/Sheaves):
-
Friction Reduction: These robust rollers, typically made of aluminum alloy or steel with precise bearings, are hung from towers or poles. They provide a smooth, low-friction path for the conductor to run through as it's pulled, significantly reducing friction that could abrade or damage the conductor's outer strands.
-
Guiding and Support: They guide the conductor along the planned route, preventing it from snagging on structures, trees, or ground obstacles. They also support the conductor's weight during stringing, maintaining the required sag and clearance.
-
Multi-Conductor Options: Specialized multi-sheave rollers are designed for stringing bundled conductors (e.g., two, three, or four conductors per phase), ensuring they maintain their relative positions and do not get damaged by touching each other during the process.
-
-
Pulling Swivels (Anti-Twist Devices):
-
Preventing Torsion: The most critical function of a pulling swivel is to prevent rotational forces from the pulling rope (which can naturally twist under tension) from transferring to the conductor. This is especially vital for sensitive conductors like OPGW (Optical Ground Wire) which contain delicate optical fibers, or for bundled conductors where twisting can cause uneven sag or damage to spacers.
-
Smooth Rotation: High-quality swivels feature robust, sealed ball bearings that allow free rotation, absorbing any torsional stress in the pulling system.
-
-
Conductor Grips (Pulling Socks/Stockings): While also "tools," they function as accessories. They securely connect the pulling rope to the conductor. Modern designs ensure:
-
Even Pressure Distribution: Woven mesh designs distribute pulling force evenly over the conductor's surface, preventing localized crushing or deformation.
-
Non-Slip Connection: Provide a reliable, non-slip grip that holds securely even under high tension.
-
-
Grounding Systems & Leads: Crucial for safety, these accessories ensure that the conductor is effectively grounded during stringing to dissipate any induced currents, protecting workers and equipment.
-
Pilot Wire Sheaves & Accessories: For initial pilot wire installation, specialized smaller sheaves and accessories ensure smooth deployment before the heavier conductors are pulled.
By minimizing friction, preventing twisting, and providing controlled guidance, these accessories are fundamental to damage-free and safe overhead line construction, ensuring the long-term integrity and performance of the transmission network.
For international clients, comprehensive after-sales services and technical support for "Cable Installation Accessories" are just as crucial as for major equipment, ensuring correct usage, optimal performance, and problem resolution across diverse global projects. Key expectations include:
-
Comprehensive Product Documentation:
-
Multilingual User Manuals: Detailed instructions for proper use, application, and storage of each accessory, available in multiple languages.
-
Technical Data Sheets (TDS) & Material Safety Data Sheets (MSDS): Providing critical technical specifications, performance parameters, and safety information.
-
Installation Videos & Tutorials: Visual guides for complex accessory installations (e.g., specific jointing or termination procedures).
-
-
Technical Support & Consultation:
-
Responsive Helpdesk: Access to experienced technical personnel for immediate queries regarding accessory selection, application, or troubleshooting.
-
Application Engineering Support: Assistance in selecting the correct accessories for specific cable types, voltage levels, environmental conditions, and installation methods.
-
Troubleshooting Guides: Resources for diagnosing common issues related to accessory performance.
-
-
Global Logistics & Parts Availability:
-
Efficient Supply Chain: A streamlined system for rapid delivery of accessories worldwide, ensuring project timelines are met.
-
Inventory Management: Advice on optimal stocking levels for consumable accessories based on project scale.
-
-
Training & Workshops:
-
Product-Specific Training: Specialized training sessions (on-site or virtual) for client technicians on the correct and safe installation techniques for critical accessories like joints, terminations, and specialized seals. This is often crucial for warranty validation.
-
Best Practices Workshops: Sharing industry best practices for accessory handling, storage, and application to maximize their effectiveness.
-
-
Quality Assurance & Compliance:
-
Certifications & Standards Compliance: Providing documentation that accessories meet relevant international standards (e.g., IEC, ASTM, national electrical codes) for performance and safety.
-
Traceability: Ensuring traceability of accessory batches and materials for quality control and recall purposes if ever necessary.
-
-
Feedback & Continuous Improvement:
-
Customer Feedback Channels: Establishing clear channels for clients to provide feedback on accessory performance, enabling continuous product improvement and adaptation to market needs.
-
By providing this level of comprehensive support, a manufacturer demonstrates its commitment to ensuring that its "Cable Installation Accessories" contribute directly to the successful, safe, and reliable completion of international power and communication projects.
"Cable Installation Accessories" are a diverse range of supplementary components, often passive or consumable, that are essential for the proper installation, protection, identification, and secure functioning of cables in both overhead transmission line (OHTL) and underground/subsea applications. Unlike "Equipment" (the machines) or "Tools" (the handheld implements), accessories are typically integrated with the cable or its immediate environment, and they remain as permanent parts of the installed system.
They are critical for long-term reliability because they:
-
Provide Electrical Integrity: Accessories like cable joints, terminations, and lugs ensure secure, low-resistance electrical connections, preventing hot spots, power loss, and premature failures.
-
Offer Mechanical Protection: Cable cleats, ties, ducts, protective covers, and armor repair kits shield cables from physical damage (e.g., abrasion, crushing, impacts) during and after installation, significantly extending their operational lifespan.
-
Ensure Environmental Sealing: Glands, seals, heat/cold shrink tubes, and end caps prevent moisture, contaminants, and corrosive elements from entering critical connection points, preserving insulation and conductor integrity.
-
Manage Stress and Vibration: Specialized dampeners, spacers, and conductor rollers reduce mechanical stress, vibration, and friction on cables during stringing and throughout their operational life, particularly important for overhead lines.
-
Facilitate Identification and Management: Markers, labels, and warning tapes provide crucial identification for maintenance, troubleshooting, and preventing accidental damage, which is vital for complex modern grids.
-
Maintain Performance: Cable pulling lubricants reduce pulling friction, preventing cable damage during installation, while stress cones in high-voltage terminations manage electrical fields to prevent premature insulation breakdown.
Without these seemingly small but vital components, even the highest quality cables and equipment would fail to deliver the expected long-term performance and reliability that modern power and communication networks demand.
Protecting underground and direct-buried cables from external threats is paramount for network longevity and reliability. Recent advancements in "Cable Protection Accessories" are driven by needs for enhanced durability, improved detectability, and increased environmental compatibility.
Key innovations include:
-
High-Strength, Lightweight Ducting & Troughing:
-
Advanced Polymers & Composites: Traditional materials are being supplemented or replaced by high-density polyethylene (HDPE), polypropylene (PP), or Glass Reinforced Polymer (GRP) composites. These offer superior impact resistance, chemical resistance, UV stability, and are significantly lighter, facilitating faster and safer installation.
-
Interlocking & Modular Systems: Innovative interlocking mechanisms for ducting and troughing ensure quick, secure assembly and flexibility to adapt to varying terrains and curves, minimizing installation time and reducing material waste.
-
Fire Retardant & Halogen-Free Options: For sensitive environments (e.g., data centers, tunnels), accessories made from fire-retardant, low-smoke, zero-halogen (LSZH) materials are becoming standard, enhancing safety.
-
-
Enhanced Detectable Warning Tapes & Smart Markers:
-
Integrated Metallic Strips/Wires: Non-metallic warning tapes now commonly embed a metallic or conductive strip, allowing them to be easily and precisely located from the surface using standard cable/pipe locators, even if the cable beneath is non-metallic or de-energized.
-
Passive RFID Markers: Small, passive RFID (Radio Frequency Identification) markers can be buried with the cable, programmable with detailed information (cable type, installation date, depth, ownership, GPS coordinates). These can be precisely located and read by handheld RFID readers, offering highly accurate asset identification and integration with digital asset management systems.
-
-
Advanced Duct Seals & Plugs: Enhanced designs and materials (e.g., silicone gel-filled, mechanical compression seals, or rubber-based systems) provide superior watertight and gas-tight sealing of conduits at manhole entries, building penetrations, or between duct sections. This prevents moisture ingress, rodent entry, and gas migration, all critical for maintaining cable integrity.
-
Anti-Dig Mesh/Grids: Robust, often brightly colored, polymer mesh or grid systems are laid above direct-buried cables as an additional physical barrier and visual warning layer, effectively deterring accidental excavation and providing a last line of defense.
These innovations collectively ensure a more robust, identifiable, and durable underground cable infrastructure, significantly reducing the risk of costly damage, service interruptions, and improving long-term network resilience.
"Cable Pulling Lubricants and Gels" are indispensable accessories that significantly reduce friction during cable installation, preventing damage and ensuring successful pulls, especially over long distances or through complex conduit runs with multiple bends. Their role is critical for both the cable's integrity and the efficiency of the installation process.
Their contributions include:
-
Drastic Friction Reduction: They form a low-friction film between the cable jacket and the inner surface of the conduit/duct. This can reduce pulling tensions by as much as 50-80%, greatly minimizing the stress on the cable and the pulling equipment. Lower friction translates to less effort required, enabling longer pulling distances without intermediate pulling pits.
-
Preventing Cable Damage:
-
Abrasions & Kinking: By reducing friction, lubricants prevent the cable jacket from abrading against conduit walls, especially around bends or rough spots. They also help prevent the cable from kinking or buckling under excessive compressive forces generated by pulling.
-
Overheating: Lower friction also means less heat generation during the pull, protecting cable insulation from thermal damage.
-
Stretch: Minimizing pulling tension reduces the risk of stretching or deforming the conductor or sensitive optical fibers within communication cables.
-
-
Facilitating Longer & More Complex Pulls: With reduced friction, longer continuous cable pulls become feasible, minimizing the need for costly and time-consuming intermediate pulling pits. They also enable successful installation through conduits with numerous bends or smaller diameters.
-
Optimizing Equipment Performance: Lower pulling tensions reduce the strain on pulling winches, rope, and other equipment, extending their lifespan and requiring less power consumption, leading to fuel savings.
-
Environmental Compatibility: Modern lubricants are typically:
-
Non-Toxic & Biodegradable: Formulated to be environmentally safe, non-flammable, and easily biodegradable, especially important for outdoor applications where they might come into contact with soil or water.
-
Residue-Free & Non-Clogging: Designed to dry to a thin, non-tacky film that doesn't clog conduits and is easy to clean up after installation.
-
Temperature Stable: Maintain their lubricating properties across a wide range of temperatures, from freezing to high heat, ensuring consistent performance in diverse climates.
-
-
Compatibility with Cable Jackets: Formulated to be compatible with all common cable jacket materials (e.g., PVC, polyethylene, rubber), ensuring they do not degrade the cable's material properties or long-term performance.
Selecting the right lubricant, specifically designed for the cable type, conduit material, and environmental conditions, is a critical step in achieving a safe, efficient, and damage-free cable installation.