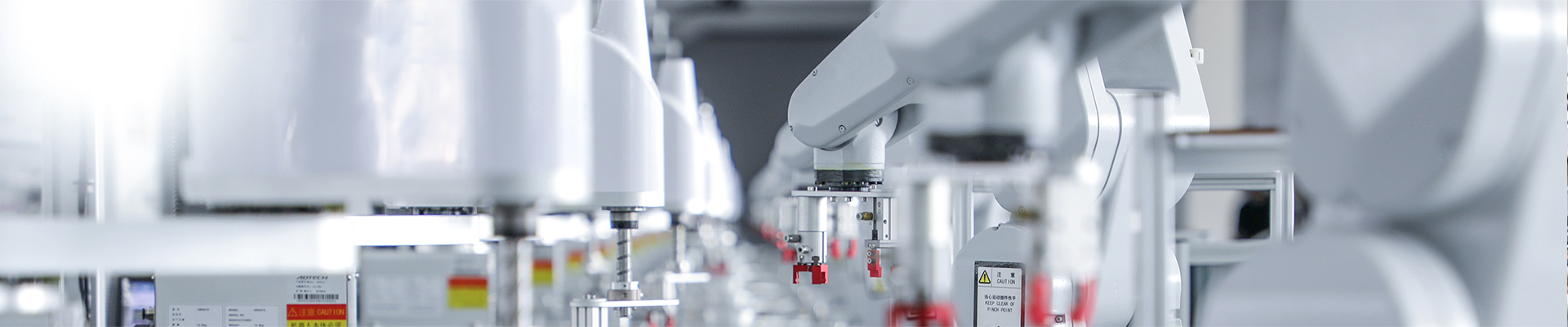
FAQ
"Cable Pulling Tools" are the smaller, often handheld or portable devices and accessories that directly interact with the cable or pulling line to facilitate its installation. They complement the larger "Cable Pulling Equipment" (which refers to the primary machines like winches or pullers that generate the main force) by providing crucial functions at the point of action.
The key differences are:
-
Scale and Function: Equipment provides the primary motive force (e.g., a hydraulic pulling machine), while tools perform specific, intricate tasks such as gripping, guiding, measuring, cutting, or splicing.
-
Portability: Tools are generally more portable and are used directly by technicians on the ground, in trenches, manholes, or at height, whereas equipment is typically larger, often trailer-mounted or self-propelled.
-
Cost: Tools are usually lower in individual cost compared to the capital investment in larger pulling equipment.
Examples of Cable Pulling Tools include pulling grips (socks), swivels, cable rollers, stringing blocks, dynamometers, cable lubricants, cutting tools, and specialized measuring devices. They are indispensable for achieving a successful, damage-free, and safe cable installation.
Cable pulling grips (often called "socks" or "stockings") are critical for creating a secure, non-damaging connection between the pulling rope and the cable. Recent innovations focus on enhanced material science, design, and versatility:
-
Advanced Material Construction: Grips are increasingly made from high-strength, flexible, and corrosion-resistant materials like galvanized steel, stainless steel, or even high-performance synthetic fibers (e.g., aramid or UHMWPE blends). These materials offer superior grip strength while being gentle on sensitive cable jackets and internal structures.
-
Optimized Weave Patterns: The woven mesh design has evolved to provide more uniform pressure distribution along the cable, minimizing stress concentrations that could lead to kinking, crushing, or damage to insulation, especially critical for delicate fiber optic or large power cables.
-
Integrated Swivels and Leading Edges: Many modern grips come with an anti-twist swivel directly integrated into the design, ensuring that any rotational forces from the pulling rope are not transferred to the cable. Additionally, reinforced "shoulders" or smooth leading edges protect the cable end as it encounters obstacles or enters conduits.
-
Double and Triple Eye Options: For heavier pulls or situations requiring redundancy, grips are available with multiple pulling eyes, allowing for attachment to various pulling lines or for use with specialized load-distributing devices.
-
Segmented/Adjustable Grips: Some specialized grips feature segmented designs or adjustable components that allow them to conform better to irregular cable shapes or accommodate a wider range of cable diameters with a single tool, increasing versatility.
-
Non-Metallic Options: For specific applications where electrical insulation is critical, entirely non-metallic pulling grips made from high-strength synthetic polymers are becoming more prevalent.
These innovations ensure that grips provide a reliable, damage-free, and safe connection, adapting to the diverse requirements of modern cable installations.
"Cable Rollers" and "Cable Guides" are indispensable for underground cable pulling, playing a crucial role in optimizing efficiency and preventing costly cable damage, particularly in challenging sections:
-
Friction Reduction: Their primary function is to elevate the cable off the ground or the bottom of the trench/conduit and provide smooth, rolling contact. This dramatically reduces friction between the cable and abrasive surfaces, significantly lowering the required pulling force and stress on both the cable and the pulling equipment.
-
Smooth Guidance through Bends:
-
Corner Rollers: Specifically designed with multiple vertical and/or horizontal rollers, these guides ensure cables can navigate sharp bends in trenches, manholes, or conduit runs without kinking or exceeding minimum bend radii. They prevent the cable from rubbing against sharp edges.
-
Manhole/Vault Rollers: Often on sturdy frames, these allow for the smooth redirection of cables within confined underground structures, preventing costly abrasion and ensuring controlled movement.
-
-
Protection from Abrasion & Kinking: The rollers are typically made with durable, non-abrasive materials like high-density polyethylene (HDPE), robust rubber, or specialized polymers. This material prevents the cable jacket from being scuffed, cut, or otherwise damaged by rough surfaces or sharp edges during the pull.
-
Improved Safety: By ensuring predictable cable movement and reducing friction, these tools minimize the risk of sudden jerks or uncontrolled cable behavior, enhancing worker safety during the pulling operation.
-
Optimized Cable Laying: Strategic placement of rollers and guides ensures the cable is laid consistently and smoothly, conforming to design specifications and reducing the likelihood of future faults.
Proper selection and deployment of these essential tools are critical for successful, long-lasting underground cable installations.
Safety is paramount when working with Cable Pulling Tools, especially given the high forces and hazardous environments involved. Critical safety considerations and relevant certification requirements include:
-
Working Load Limit (WLL) & Safety Factor: Every load-bearing tool (grips, swivels, blocks, rollers, shackles) must be clearly marked with its WLL. This is the maximum safe working load the tool can handle and is determined by applying a significant safety factor (e.g., 3:1, 5:1) to its Minimum Breaking Load (MBL). Never exceed the WLL.
-
Proof Testing: Reputable manufacturers perform individual or batch proof testing on load-bearing tools, applying a load higher than the WLL to verify structural integrity before they leave the factory. Test certificates should be available.
-
Material Quality & Traceability: Tools should be constructed from high-grade, certified materials (e.g., heat-treated alloy steel, specific polymers). Manufacturers should provide material traceability to ensure quality and performance.
-
Anti-Twist Functionality (Swivels): Swivels must function perfectly to prevent torsional forces from transferring to the cable, which can cause catastrophic damage, especially to fiber optic cables. Regular inspection of swivel rotation is vital.
-
Non-Abrasive Surfaces (Rollers/Blocks): Any tool that comes into direct contact with the cable (rollers, stringing blocks, cable guides) must have smooth, non-abrasive surfaces or linings to prevent damage to the cable jacket or internal conductors.
-
Ergonomics & Ease of Use: Tools should be designed to reduce operator fatigue and minimize the risk of repetitive strain injuries. Good grips, balanced weight, and intuitive operation are important.
-
Insulation (for specialized tools): Any hand tools used near energized lines or for specific electrical work must have appropriate insulation ratings and comply with standards like IEC 60900 (for 1000V insulated hand tools).
-
Regular Inspection & Maintenance: Users must perform thorough visual inspections before each use for signs of wear, damage (cracks, bends, deformation), or corrosion. Follow manufacturer's guidelines for cleaning, lubrication, and replacement of worn parts.
-
Industry Standards & Certifications: While specific "tools" might not have the same broad certifications as large machines (like CE for equipment), reputable tools will adhere to relevant standards from organizations such as:
-
ASTM (American Society for Testing and Materials): For material properties and testing methods.
-
ISO (International Organization for Standardization): For quality management in manufacturing and specific product standards.
-
Local/National Occupational Safety & Health Regulations: Ensuring tools comply with legal requirements in the region of use.
-
-
User Training: The most critical safety aspect is proper training for all personnel on the correct selection, inspection, safe operation, and maintenance of each specific tool.
Beyond the core cable pulling tools, several essential accessories are crucial for a complete, efficient, and safe installation solution. These items ensure smooth operation and protect both the cable and personnel:
-
Cable Drum Jacks/Stands & Spooling Devices: Used to elevate and support large cable drums, allowing them to unwind smoothly and controllably without kinking or damaging the cable. Some include braking systems for tension control.
-
Cable Feeds/Payout Systems: Devices that assist in feeding the cable directly into a conduit or trench, often with integrated rollers, to minimize manual handling and friction at the entry point.
-
Dynamometers (Tension Meters): Portable devices (mechanical or digital) inserted into the pulling line to provide real-time measurement of the actual pulling tension. Absolutely critical for staying within the cable's maximum allowable pulling tension.
-
Swivels (Separate from grips): High-strength swivels (ball bearing or thrust bearing) are placed between the pulling rope and the cable grip to prevent any rotational forces from transferring to the cable, particularly vital for fiber optic or bundled conductors.
-
Cable Lubricant Applicators: Pumps, hoses, or specialized devices that ensure even and continuous application of cable lubricant as the cable enters the conduit, optimizing friction reduction.
-
Conduit Measuring Devices: Tools like measuring wheels or integrated meters on the pulling rope/mule tape to accurately track the length of cable installed.
-
Duct Rodders/Fish Tapes: Used to pre-install a pilot line or measuring tape through a conduit before the main pulling rope, essential for verifying conduit integrity and pulling capabilities.
-
Cable Ties/Banding Tools: For securing cables within trenches, on trays, or during racking in manholes after pulling.
-
Cable End Caps/Seals: Essential for protecting the exposed ends of cables from moisture, dirt, and physical damage before splicing or termination.
-
Personal Protective Equipment (PPE): While not a "pulling tool" directly, appropriate PPE (gloves, hard hats, safety glasses, high-visibility clothing, safety footwear) is an indispensable accessory for any cable pulling operation.
-
Communication Devices: Radios or intercom systems are crucial for clear communication between the pulling machine operator and personnel at the cable entry/exit points, ensuring synchronized and safe operations.
These accessories work in concert to ensure a precise, efficient, and damage-free cable installation process.
"Cable Pulling Accessories" are the various supplementary items, tools, and consumable products that work in conjunction with main cable pulling equipment (like winches or pullers) to ensure the safe, efficient, and precise installation of electrical conductors and cables. They are indispensable because they:
-
Facilitate Guidance: Accessories like cable rollers and stringing blocks ensure the cable follows the intended path, minimizing friction and preventing snags or kinks.
-
Protect Cable Integrity: They safeguard expensive cables and conductors from abrasion, crushing, or twisting during the pulling process, which is critical for their long-term performance and reliability, especially for sensitive fiber optic or HTLS cables.
-
Ensure Secure Connections: Pulling grips and swivels provide a robust yet non-damaging link between the pulling line and the cable.
-
Enable Monitoring & Control: Dynamometers and measuring devices offer real-time data crucial for maintaining specified tension limits and tracking progress.
-
Enhance Safety: By reducing friction, preventing uncontrolled cable movement, and providing clear visual cues, they significantly reduce risks to personnel and equipment on site.
These accessories are the critical "finishing touches" that turn a powerful pulling operation into a precise and damage-free installation.
"Cable Rollers" (primarily for underground) and "Stringing Blocks" (for overhead lines) have seen significant advancements to protect modern cable types and enhance efficiency:
-
Advanced Polymer Sheaves/Linings: The most notable innovation is the widespread use of high-performance polymers (e.g., Ultra-High Molecular Weight Polyethylene (UHMWPE), specialized polyurethanes, or MC Nylon) for the roller or sheave surfaces. These materials offer:
-
Extremely Low Friction: Significantly reduces the pulling force required, which lessens stress on the cable and extends equipment life.
-
Superior Abrasion Resistance: Provides excellent protection against wear on the cable jacket or conductor strands, crucial for sensitive cables like OPGW (Optical Ground Wire) and HTLS (High-Temperature Low-Sag) that are prone to damage from friction.
-
Non-Conductive Properties: Some polymers can also offer electrical insulation, adding a layer of safety.
-
-
Lightweight, High-Strength Frames: Frames are increasingly constructed from durable, yet lightweight, materials like high-grade aluminum alloys or composite materials. This makes the accessories easier and safer to handle, transport, and install, especially in challenging terrain or at height.
-
Sealed, Maintenance-Free Bearings: High-quality, sealed ball or roller bearings ensure smooth, consistent rotation under load with minimal friction. Their sealed design protects against dirt, moisture, and contaminants, significantly extending the lifespan and reducing maintenance requirements.
-
Modular & Versatile Designs: Many rollers and blocks now feature modular components, allowing for easier replacement of worn parts. Designs also cater to specific needs, such as multi-sheave blocks for bundled conductors or specialized corner rollers for sharp bends in underground conduits.
-
Integrated Measuring Devices: Some stringing blocks and rollers are now incorporating small, integrated digital counters that measure the exact length of conductor or cable passing through, providing real-time progress updates.
These innovations ensure optimal protection for all cable types while enhancing operational efficiency and safety.
"Anti-Twist Swivels" are critical accessories that serve as a crucial interface between the pulling rope and the cable, specifically designed to protect delicate and valuable cables:
-
Eliminating Torsional Stress: Their primary function is to prevent any twisting forces from being transferred from the pulling rope to the cable or conductor. Pulling ropes can naturally twist under tension, and without a swivel, this twisting would be directly transmitted to the cable.
-
For OPGW: This is paramount. The internal optical fibers of OPGW are extremely sensitive to twisting and can be permanently damaged (leading to signal loss) if torsional forces are applied. The swivel allows the rope to rotate freely while the OPGW remains untwisted.
-
For Large Power Cables: Twisting can cause internal conductor deformation, stress on the insulation, or damage to the outer jacket, potentially leading to premature failure. Swivels ensure the cable retains its original structure.
-
For Bundled Conductors: They prevent individual conductors within a bundle from spiraling or birdcaging during overhead stringing.
-
-
Smooth Passage: High-quality swivels are designed to be compact and have smooth, streamlined profiles, allowing them to pass easily through stringing blocks, rollers, and conduit entries without snagging.
Maintenance Requirements:
-
Pre-Use Inspection: Before every use, visually inspect the swivel for any signs of damage: cracks, bends, distortion, excessive wear on the eyes, or signs of rust/corrosion.
-
Functionality Check: Manually rotate the swivel to ensure it turns freely and smoothly through 360 degrees without binding, grinding, or excessive play. Any stiffness indicates a problem.
-
Lubrication (if applicable): While many modern swivels feature sealed, maintenance-free bearings, some heavy-duty models may have grease fittings. If present, lubricate strictly according to the manufacturer's recommendations using the specified type of grease.
-
Load Rating Verification: Always confirm that the swivel's Working Load Limit (WLL) is clearly legible and adequate for the maximum anticipated pulling force of the job.
-
Cleaning: Keep the swivel clean from dirt, debris, and contaminants that could interfere with its rotational mechanism.
-
Immediate Removal from Service: Any swivel showing signs of damage, restricted rotation, or suspected compromise to its integrity must be immediately removed from service, tagged, and either repaired by a qualified professional or replaced. Never use a damaged or malfunctioning swivel.
Selecting the correct "Cable Pulling Lubricants" is vital for efficient, safe, and environmentally responsible cable installation. Key considerations include:
-
Friction Reduction Performance: The primary purpose is to significantly reduce the coefficient of friction between the cable and the conduit/duct. High-performance lubricants allow for longer pull distances, reduce strain on the cable and pulling equipment, and lower the required pulling force.
-
Cable Jacket Compatibility: Crucially, the lubricant must be chemically compatible with the specific material of the cable jacket (e.g., PVC, polyethylene, LLDPE, LSZH, rubber, etc.). Incompatible lubricants can cause swelling, softening, or cracking of the jacket, leading to premature cable failure. Always check manufacturer specifications.
-
Environmental Profile: A major trend and a key consideration today is the environmental impact. Look for lubricants that are:
-
Biodegradable: Decompose naturally in the environment, minimizing long-term ecological impact.
-
Non-Toxic: Safe for workers and local ecosystems if spilled.
-
Non-Flammable: Reduces fire risk on site.
-
Water-Based: Often easier to clean up and less harmful than petroleum-based alternatives.
-
-
Temperature Stability: The lubricant should maintain its effectiveness across the range of temperatures expected during the pull and during storage.
-
"Cling" and Film Durability: It should adhere well to the cable and form a persistent, slippery film that doesn't dry out too quickly, especially on long or complex pulls.
-
Cleanliness & Residue: High-quality lubricants should dry to a thin, non-sticky, non-conductive film that doesn't attract dirt or impede future operations (like splicing or termination).
-
Application Method: Consider the viscosity and packaging (e.g., squeeze bottles, drums, spray-on formulas) for easy and efficient application on site.
By choosing advanced, environmentally-friendly lubricants, projects can achieve greater efficiency, extend cable lifespan, and uphold strong environmental stewardship.
Beyond the main pulling line, several "Cable Measuring and Monitoring Accessories" are essential for ensuring precise installation, adherence to specifications, and maintaining safety:
-
Dynamometers (Tension Meters): These are perhaps the most critical. They are placed in-line with the pulling rope/cable and provide real-time, accurate measurements of the actual pulling tension. This allows operators to ensure the tension remains below the cable manufacturer's maximum allowable pulling tension (MAPT), preventing costly damage due to over-stressing. They come in mechanical (analogue) and digital versions, with digital often offering data logging.
-
Length Counters/Meters: Devices that accurately measure the length of cable or pulling rope that has been pulled into the conduit or along the route. These are vital for:
-
Confirming the exact length of cable installed.
-
Identifying potential blockages by comparing pulled length to theoretical length.
-
Accurate inventory management.
-
Often integrated into guide rollers or standalone units.
-
-
Proofing Mandrels/Duct Provers: For underground conduits, these are rigid, oversized slugs (usually slightly smaller than the conduit's internal diameter) pulled through the duct before the cable. They verify that the conduit is clear of obstructions, not crushed, and has no sharp edges that could damage the cable.
-
Cable Diameter Gauges: Simple tools to quickly verify the correct cable diameter for matching with pulling grips, rollers, and conduit sizes.
-
Infrared Thermometers: For large power cables, especially during long pulls, monitoring the cable's surface temperature can be important to ensure it's not overheating due to friction, especially in high ambient temperatures.
-
Communication Devices: While not "measuring," clear communication (e.g., two-way radios, headsets) between the pulling machine operator and personnel at the cable entry/exit points is absolutely essential for synchronizing operations and reacting quickly to any issues, thus enabling precise control and safety.
These accessories provide the critical data and verification points that transform a simple pull into a controlled, quality-assured installation.
Proper storage and rigorous maintenance are crucial for extending the lifespan and ensuring the reliability and safety of "Cable Pulling Accessories." Best practices include:
-
Routine Cleaning: After each use, thoroughly clean all accessories to remove dirt, mud, cable lubricant residue, and moisture. This prevents corrosion and build-up that could impede functionality. Use appropriate cleaning agents that won't damage materials (e.g., mild soap and water for polymer components).
-
Thorough Inspection (Before & After Each Use):
-
Visual Check: Inspect for any signs of physical damage: cracks, bends, nicks, deformation, excessive wear, or corrosion on frames, sheaves, rollers, grips, and swivels.
-
Functionality Check: For moving parts (e.g., rollers, swivels), manually test their rotation and movement to ensure they operate freely without binding or excessive play.
-
Wear Parts: Pay close attention to wear on sheave linings, grip weaves, and bearing surfaces. Replace worn components promptly.
-
-
Lubrication: For accessories with moving parts (e.g., swivels with grease fittings, certain rollers), lubricate according to the manufacturer's specific guidelines, using the recommended type and amount of lubricant.
-
Protection from Elements: Store accessories in a dry, well-ventilated area, preferably indoors. Protect them from direct sunlight, extreme temperatures, and excessive moisture to prevent rust, material degradation, and UV damage.
-
Organized Storage: Store accessories neatly on racks, in toolboxes, or on pallets, preventing them from being thrown together, which can cause damage, tangles, or make inspection difficult. Ensure small, critical components are not misplaced.
-
Load Rating Verification: Ensure the Working Load Limit (WLL) markings on all load-bearing accessories remain clearly legible. If they fade, re-mark them or replace the accessory.
-
Calibration (for measuring devices): Any measuring accessories like dynamometers or length counters must be periodically calibrated by certified technicians according to the manufacturer's recommendations (typically annually or bi-annually) to maintain accuracy. Keep calibration certificates on file.
-
Immediate Removal from Service: Any accessory showing signs of significant damage, malfunction, or compromised safety must be immediately removed from service, tagged "Do Not Use," and either professionally repaired by qualified personnel or replaced. Never attempt to use a faulty accessory.
Adhering to these practices ensures that your investment in cable pulling accessories provides reliable, safe, and efficient performance for many years.
A "Cable Laying Machine" is a specialized piece of heavy equipment designed to install electrical cables and conductors efficiently and safely, primarily in underground applications, but also with relevance to certain overhead tasks. Its primary functions in modern electrical infrastructure projects include:
-
Trenching/Excavation (for certain types): Some cable laying machines (like trenchers or plows) are designed to excavate the trench or create a pathway directly, often simultaneously laying the cable.
-
Cable Pulling/Feeding: The machine generates and precisely controls the force required to pull or feed cables through pre-existing conduits, ducts, or open trenches. This overcomes significant friction and resistance over long distances and around bends.
-
Cable Placement: It ensures the cable is laid at the correct depth and along the specified route, protecting it from future damage and ensuring long-term reliability.
-
Backfilling and Restoration (for certain types): More integrated machines can also perform initial backfilling of the trench, reducing the need for separate equipment.
-
Protection of Cable Integrity: By controlling tension and minimizing stress, the machine safeguards expensive and sensitive cables (e.g., high-voltage power cables, fiber optics) from kinking, crushing, or abrasion during installation.
These machines are fundamental to the rapid expansion and modernization of power grids, telecommunication networks, and renewable energy infrastructure globally.
Modern Cable Laying Machines play a significant role in promoting environmental sustainability and minimizing the ecological impact of infrastructure projects through several key advancements and capabilities:
-
Enabling Trenchless Technologies: Many modern cable laying machines are designed for, or integrate with, trenchless installation methods such as Horizontal Directional Drilling (HDD), vibratory plowing, or micro-trenching. These methods drastically reduce surface disruption, eliminate the need for large open trenches, and preserve existing landscapes, ecosystems, and urban infrastructure (roads, sidewalks, utilities).
-
Reduced Ground Disturbance: Even for traditional trenching, efficient machines excavate only the necessary width and depth, minimizing soil displacement. Integrated backfilling capabilities also ensure that excavated soil is returned effectively, aiding in faster site restoration.
-
Minimized Material Waste: Precision control features, automated tension management, and real-time monitoring significantly reduce the risk of costly cable damage during installation. This minimizes material waste from damaged cables that would otherwise need to be scrapped and replaced.
-
Lowered Fuel Consumption & Emissions: Modern cable laying machines are equipped with advanced, fuel-efficient engines that meet stringent emission standards. Optimized hydraulic systems and smart controls further reduce fuel consumption and associated greenhouse gas emissions during operation. Hybrid or electric-powered options are also emerging for certain applications, further reducing their carbon footprint.
-
Protection of Sensitive Areas: By allowing for precise route planning (with GPS integration) and less invasive installation techniques, these machines enable cable laying in environmentally sensitive areas (e.g., wetlands, forested areas, agricultural lands) with minimal disturbance.
-
Reduced Noise Pollution: Newer machine designs often incorporate noise reduction technologies, lessening the acoustic impact on local communities and wildlife.
-
Faster Restoration: The efficiency of these machines leads to quicker project completion, allowing for faster restoration of disturbed areas to their original state, which aids in ecological recovery.
By adopting these advanced Cable Laying Machines, infrastructure projects can significantly lessen their environmental footprint, align with global sustainability goals, and achieve more responsible development.
The diverse requirements of various cable types and installation environments have led to the development of highly specialized Cable Laying Machines:
-
For Underground Power Cables (LV to EHV):
-
Hydraulic Pulling Machines (Winch Type): These are the most common, generating high, controlled pulling forces for large, heavy power cables through conduits or ducts. They feature robust hydraulic systems, constant tension control, and often bullwheel or capstan designs.
-
Trenchers: These machines (wheel trenchers, chain trenchers) excavate precise trenches for direct burial of cables, often simultaneously feeding the cable into the trench.
-
Vibratory Plows: For less rocky soil, these machines "slice" through the ground and simultaneously lay the cable without creating a wide open trench, ideal for rural or agricultural areas.
-
Cable Pusher/Feeder Machines: Used in conjunction with pulling winches, these caterpillar-track-based units apply a pushing force directly to the cable, assisting the pull and reducing friction, especially around bends in long conduit runs.
-
-
For Fiber Optic & Telecommunication Cables:
-
Fiber Optic Blowing Machines: These specialized machines use compressed air to "blow" or "jet" lightweight fiber optic cables through pre-installed ducts. This method drastically reduces friction, allows for extremely long, continuous runs, and minimizes mechanical stress on the delicate fibers.
-
Small-Scale Pulling Winches: Highly precise, low-tension winches are used for pulling bundled fiber cables or small copper communication cables where blowing isn't feasible.
-
Micro-Trenchers: For urban fiber deployment, these machines cut very narrow, shallow trenches (micro-trenches) into existing pavement, allowing for rapid, minimally invasive installation of fiber optic bundles.
-
-
For Submarine Cables:
-
Cable Laying Vessels (Cable Ships): These are large, specialized ships equipped with massive cable tanks, sophisticated payout systems, and precise navigation systems to lay submarine power or communication cables across oceans or waterways.
-
Subsea Plows/Trenchers (ROV-operated): Remotely Operated Vehicles (ROVs) or towed plows are deployed from vessels to create trenches on the seabed and bury the cable for protection against anchors, fishing gear, and environmental factors.
-
Jetting Machines: Used underwater, these machines create a trench using high-pressure water jets, then bury the cable into the seabed.
-
The selection of a Cable Laying Machine is dictated by the cable type, installation environment, project scale, and desired level of ground disturbance.
Given the high forces, heavy loads, and potentially hazardous environments, Cable Laying Machines are designed with critical safety features and must comply with stringent international and national regulatory standards:
-
Automatic Overload Protection: Electronic and hydraulic systems continuously monitor the pulling force. If the pre-set maximum load limit is approached or exceeded (e.g., due to a snag or excessive friction), the machine automatically reduces speed or stops the pull, preventing cable damage, equipment failure, and safeguarding personnel from runaway loads.
-
Emergency Stop Systems: Multiple, clearly marked, and easily accessible emergency stop buttons are strategically placed on the machine and sometimes on remote controls. These provide immediate power shutdown in any critical situation.
-
Fail-Safe Braking Systems: For machines with drums or bullwheels, robust, fail-safe braking systems automatically engage if power or hydraulic pressure is lost, preventing uncontrolled unwinding or movement of the cable.
-
Guarding of Moving Parts: All rotating components, such as drums, capstans, bullwheels, chains, and exposed drive mechanisms, are securely guarded to prevent accidental contact with operators or foreign objects.
-
Operator Protection: Features like enclosed cabins with ROPS/FOPS (Roll-Over Protective Structures / Falling Object Protective Structures), clear sightlines, ergonomic controls, and comfortable seating reduce operator fatigue and enhance safety.
-
Audible and Visual Alarms: Machines are equipped with alarms (e.g., for overload, low fluid levels, or system faults) and warning lights to alert operators and nearby personnel to potential hazards.
-
Remote Control Options: Many machines offer wireless remote control, allowing operators to position themselves in the safest vantage point away from the immediate operating area during critical phases.
-
Load-Rated Components & Traceability: All load-bearing components (hooks, shackles, anchoring points, pulling eyes) must be clearly marked with their Working Load Limit (WLL) and comply with relevant standards, ensuring they can safely withstand anticipated forces. Material traceability helps verify quality.
-
International Standards & Certifications: Manufacturers adhere to and obtain certifications from various bodies, which may include:
-
CE Marking (European Conformity): Mandatory for machines sold in the European Economic Area, indicating compliance with essential health, safety, and environmental protection requirements.
-
ISO Standards (e.g., ISO 12100 for machine safety, ISO 13849 for safety-related parts of control systems): Provide comprehensive guidelines for design, risk assessment, and risk reduction.
-
National/Local Safety Regulations: Compliance with specific occupational safety and health administration (OSHA) regulations or similar bodies in the target export markets.
-
ANSI (American National Standards Institute): For equipment standards in North America.
-
Prioritizing these safety features and regulatory compliance is paramount for protecting workers, the public, and ensuring the reliability of the installed infrastructure.
Advancements in Cable Laying Machine technology are directly enabling and accelerating the global expansion of renewable energy and smart grid infrastructure:
-
Efficient Connection of Distributed Energy Resources (DERs): Renewable energy sources like solar farms, wind farms (both onshore and offshore), and battery storage systems are often distributed. Advanced cable laying machines efficiently connect these DERs to the main grid, requiring extensive cabling for power collection and transmission, often over long distances and diverse terrains.
-
Facilitating Undergrounding for Resilience: Smart grids prioritize resilience against extreme weather, physical threats, and cyber-attacks. This drives the increasing trend of undergrounding power lines. Modern cable laying machines, especially those using trenchless technologies, make this undergrounding economically viable and environmentally sound, significantly improving grid reliability.
-
Handling Advanced Cable Types: Smart grids and renewable projects utilize sophisticated, high-capacity, and often sensitive cables (e.g., HVDC cables, integrated fiber optic/power cables, superconductors). Advanced cable laying machines are designed with precise tension control, gentle handling mechanisms, and specialized features to install these cables without damage, preserving their performance.
-
Support for Offshore Wind Development: Submarine cable laying machines (cable ships, subsea plows) are crucial for connecting offshore wind farms to the mainland grid, which is a rapidly growing sector of renewable energy. These machines handle immense cable lengths and operate in challenging marine environments.
-
Integration with Digital Grid Management: The "smart" features of these machines (real-time data, GPS mapping, data logging) feed critical installation data directly into digital project management platforms. This data can then be integrated into broader smart grid planning and asset management systems, contributing to more efficient grid operation and maintenance.
-
Reduced Construction Time & Cost: The enhanced speed, precision, and automation of modern cable laying machines significantly reduce installation time and labor costs for large-scale projects, making renewable energy and smart grid upgrades more economically attractive.
-
Lower Environmental Footprint: As discussed previously, the shift towards trenchless methods and more efficient operations means that the expansion of critical energy infrastructure can occur with less environmental disruption, aligning with the sustainability goals of renewable energy initiatives.
In essence, these machines are not just tools; they are key enablers of the global transition to a cleaner, more reliable, and intelligent energy future.
"Cable Laying Equipment" is a comprehensive term that typically refers to the larger, specialized machinery and integrated systems primarily used for the installation and placement of cables, often involving significant ground work or specialized environments. While there's overlap, here's how it generally differs:
-
Cable Laying Equipment: This term implies a broader scope, often including machines that not only pull but also excavate (trenchers, plows), guide, feed, or even bury cables in a continuous operation. It can also refer to the sophisticated systems on board vessels for submarine cable installation. It focuses on the complete process of placing the cable from start to finish.
-
Examples: Hydraulic pulling winches (especially high-capacity ones), trenchers, vibratory plows, cable feeder units, cable drum stands with tension control, and even specialized cable laying vessels for offshore projects.
-
-
Cable Pulling Machines: This usually refers to the core engine-driven or hydraulic units that generate the primary pulling force for drawing cables through conduits, ducts, or across open terrain. While a "Cable Laying Machine" will often include pulling capabilities, "Pulling Machine" specifically emphasizes the force-generation aspect.
-
Examples: Dedicated hydraulic pullers (bullwheel or capstan type), often trailer-mounted.
-
-
Cable Pulling Tools: These are the smaller, often manual or handheld accessories and devices that directly interact with the cable or pulling line at the point of action. They support the larger equipment.
-
Examples: Cable grips, swivels, rollers, dynamometers, cable cutters, lubricants.
-
In essence, "Cable Laying Equipment" covers the complete suite of machinery and integrated systems required for comprehensive cable installation projects, both overhead and, predominantly, underground or subsea.
Cable Laying Equipment is fundamental to the global expansion of underground power infrastructure and the development of smart grids, playing several critical roles:
-
Enabling Undergrounding for Resilience: As smart grids prioritize reliability and resilience, there's a strong global trend towards burying power lines to protect them from extreme weather (storms, ice), natural disasters, and physical threats. Cable laying equipment provides the means to efficiently and economically install these vast networks of underground cables.
-
Supporting Urbanization & Aesthetics: In densely populated urban areas, overhead lines are often impractical or undesirable due to space constraints, safety concerns, and aesthetic impact. Modern cable laying equipment (especially trenchless solutions) allows for the efficient installation of vital power and communication lines without extensive surface disruption.
-
Connecting Distributed Energy Resources (DERs): The proliferation of renewable energy sources (solar farms, wind farms) and battery storage systems often involves connecting numerous distributed generation sites to the main grid. This requires extensive cabling, and specialized cable laying equipment ensures their rapid and safe deployment.
-
Handling Advanced & Sensitive Cables: Smart grids utilize advanced cable technologies, including high-capacity power cables (e.g., HVDC, XLPE) and integrated fiber optic cables for communication and control. Cable laying equipment is specifically designed to handle these delicate yet robust cables with precision, preventing damage that could compromise signal integrity or power transmission.
-
Minimizing Environmental Impact: As discussed, the increasing adoption of trenchless technologies (facilitated by specific cable laying equipment) drastically reduces excavation, preserves landscapes, and lessens the carbon footprint of infrastructure projects, aligning with sustainability goals.
-
Data Integration for Optimization: The "smart" features of modern cable laying equipment (real-time data, precise mapping) generate valuable installation data. This data can be integrated into broader grid management systems, informing network optimization, asset management, and predictive maintenance for the entire smart grid infrastructure.
By making underground installation more efficient, precise, and environmentally friendly, Cable Laying Equipment is an indispensable enabler of the modern, resilient, and intelligent power networks of the future.
Modern Cable Laying Equipment is undergoing rapid technological evolution to meet the demands for faster, more precise, and less disruptive installations:
-
Advanced Hydraulic and Drive Systems: State-of-the-art closed-loop hydraulic systems provide extremely precise and responsive control over pulling tension and speed, crucial for protecting high-value cables. Electronically controlled engines (often diesel) offer higher power output with improved fuel efficiency and lower emissions.
-
Integrated GPS/GNSS and Telematics: High-precision Global Navigation Satellite Systems (GNSS) are integrated for accurate route planning, real-time machine guidance, and precise "as-built" documentation of cable positions. Telematics systems enable remote monitoring of machine performance, diagnostics, and operational data, allowing for optimized fleet management and predictive maintenance.
-
Automated Tension and Speed Management: Intelligent control systems can automatically adjust pulling speed to maintain a constant pre-set tension, even as ground conditions or friction change. This prevents over-tensioning and minimizes stress on the cable, enhancing both safety and efficiency.
-
Enhanced Operator Interfaces: Intuitive digital control panels with real-time graphical displays of pulling force, speed, length, and diagnostic information make operation easier and more accurate. Touchscreen interfaces and even remote control options are becoming standard.
-
Modular and Adaptable Designs: Equipment is increasingly designed with modular components that can be easily configured or reconfigured for different cable sizes, installation methods (e.g., direct burial, conduit pulling), or challenging terrains, maximizing versatility and return on investment.
-
Specialized Cable Handling Systems: For large power cables, features like integrated cable feeder units (caterpillar pushers) reduce friction and sidewall pressure in bends. For fiber optics, advanced blowing machines offer unparalleled speed and gentle handling.
-
Reduced Noise and Vibration: Innovations in engine and hydraulic system design, along with improved isolation techniques, contribute to quieter operations, minimizing environmental and community impact.
These advancements collectively lead to higher productivity, reduced operational costs, and superior installation quality.
Deploying "Cable Laying Equipment" in highly challenging environments like mountainous regions or dense urban areas requires specialized considerations and adapted machinery:
For Mountainous/Rugged Regions:
-
Tracked or All-Terrain Mobility: Machines often need to be track-mounted (crawler-type) or have advanced all-wheel-drive systems to navigate steep slopes, uneven terrain, and muddy conditions.
-
Increased Tractive Effort & Braking: Higher pulling and braking forces are required to manage cables on inclines and declines, often with specialized winches that can operate effectively under these conditions.
-
Compact & Modular Design: For areas with limited access or narrow trails, equipment needs to be easily transportable in sections or have a compact footprint. Skid-mounted or helicopter-transportable units are sometimes necessary.
-
Enhanced Stability Systems: Machines feature advanced stabilization systems (e.g., wider tracks, outriggers, precise weight distribution) to prevent rollovers on uneven or sloped ground.
-
Remote Control & Wireless Communication: Operators may need to control machines from a safe distance, especially on steep slopes or in hazardous areas. Reliable long-range communication systems are vital.
-
Robust Construction: Extra-durable frames and components are essential to withstand the stresses of operating in harsh, rocky, or abrasive environments.
For Dense Urban Areas:
-
Minimal Footprint & Compact Size: Equipment must be exceptionally compact to operate on narrow sidewalks, within busy streets, or inside confined manholes/vaults without causing major disruption to traffic or pedestrians.
-
Trenchless Technologies: Horizontal Directional Drilling (HDD), micro-trenching machines, and vibratory plows are preferred as they minimize surface excavation, allowing for cable installation under roads, buildings, and existing utilities without major disruption.
-
Reduced Noise and Emissions: Urban environments demand quieter machinery (electric or hybrid options, noise suppression technology) and lower emissions to minimize impact on residents and air quality.
-
Precision Control & GPS Mapping: Accurate GPS integration is crucial for navigating complex underground utility maps and avoiding existing infrastructure during drilling or trenching. Precise control prevents damage to other buried services.
-
Integrated Waste Management: Some machines are designed to collect and manage excavated spoil efficiently, minimizing debris on public streets.
-
Safety Features for Public Interaction: Clear safety signage, barriers, and integrated warning systems are vital for protecting the public in busy urban settings.
For both environments, robust design, intelligent controls, and adaptability are key to successful and safe cable laying operations.