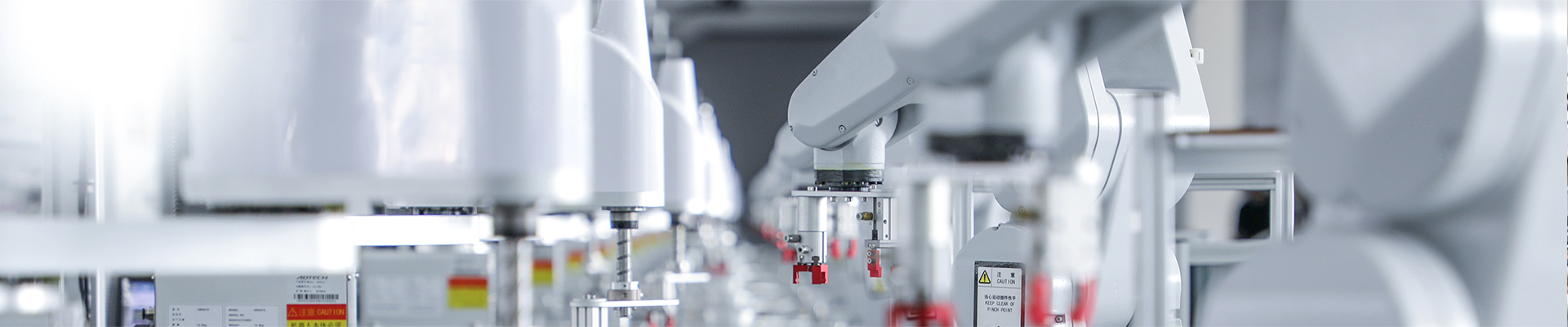
FAQ
For international customers undertaking complex projects with "Cable Laying Equipment," comprehensive after-sales support and services are absolutely crucial for maximizing equipment uptime, performance, and return on investment. Customers should expect:
-
Dedicated Technical Support:
-
Multilingual Helpdesk: 24/7 technical support available in multiple languages to overcome time zone differences and communication barriers.
-
Remote Diagnostics: Utilizing telematics and integrated smart features to remotely diagnose issues, reducing the need for immediate on-site visits and guiding local technicians.
-
-
Global Spare Parts Availability & Logistics:
-
Strategically Located Warehouses: A network of international warehouses or efficient logistics partnerships to ensure rapid delivery of critical spare parts, minimizing downtime.
-
Guaranteed Parts Supply: Commitment to providing spare parts for the entire operational life of the equipment, preventing obsolescence.
-
Online Parts Catalogues & Ordering: User-friendly online platforms for easy identification, selection, and ordering of parts.
-
-
Comprehensive Training Programs:
-
On-site & Virtual Training: Offering in-depth training for operators and maintenance personnel, either at the customer's project site or through interactive virtual platforms. This covers safe operation, advanced functions, and troubleshooting.
-
Certified Training: Providing certification programs for operators and technicians to ensure they meet international competency standards.
-
Detailed Documentation: Supplying comprehensive operation and maintenance manuals, schematics, and video tutorials in relevant languages.
-
-
Field Service & Expert Technicians:
-
Global Network of Certified Technicians: Access to highly skilled and certified field service engineers capable of complex repairs, major overhauls, calibrations, and specialized commissioning.
-
Rapid Dispatch: Efficient dispatch systems to deploy technicians quickly to international project sites when remote resolution isn't possible.
-
-
Warranty & Service Level Agreements (SLAs):
-
Robust Warranty: A clear and comprehensive warranty covering manufacturing defects and major components.
-
Flexible Service Contracts: Offering various tiers of service contracts (SLAs) that include scheduled preventative maintenance, priority support, and guaranteed response times to ensure maximum equipment availability.
-
-
Technical Updates & Continuous Improvement:
-
Software Updates: Regular provision of software updates for control systems to improve performance, add features, and enhance security.
-
Technical Bulletins: Dissemination of technical bulletins and service advisories to inform customers about best practices, potential issues, and preventative measures.
-
-
Customization & Consultation:
-
Application Engineering Support: Expert consultation to help customers select the most suitable equipment for specific project requirements, terrains, and cable types, or even custom-design solutions.
-
Pre-Project Planning: Assistance during the project planning phase to optimize equipment utilization and laying methodologies for maximum efficiency.
-
This level of robust after-sales support demonstrates a manufacturer's commitment to the long-term success and satisfaction of its international clientele.
The rapidly expanding HVDC networks and offshore renewable energy sectors are driving significant innovation in "Cable Laying Equipment" design, focusing on increased capacity, precision, and specialized capabilities:
-
Larger Capacity & Heavier Cables: HVDC cables and export cables for offshore wind farms are significantly larger, heavier, and stiffer than traditional AC cables. Equipment must be designed with much higher pulling/laying capacities, larger drum/reel systems, and more robust structures to handle these immense weights and dimensions.
-
Precise Tension Control for Subsea: For offshore applications, highly advanced active tension control systems are critical. These systems maintain extremely precise tension on the cable as it's laid on the seabed or buried, preventing over-stressing, ensuring proper catenary, and allowing for accurate placement in varying water depths and currents.
-
Dynamic Positioning (DP) Systems for Vessels: Cable laying vessels for offshore projects are now equipped with advanced DP systems that use thrusters and GPS to maintain exact position and heading without anchors, minimizing seabed disturbance and enabling precise cable routes, even in harsh weather or near existing infrastructure.
-
Integrated Burial Tools: Offshore vessels often integrate subsea plows, trenchers (mechanical or water-jetting), or ROVs (Remotely Operated Vehicles) directly into the laying process. These tools allow for simultaneous laying and burial of cables on the seabed for protection against fishing gear, anchors, and environmental abrasion.
-
Automated Cable Handling & Route Optimization: Automation extends to complex cable loading, spooling, and payout systems on board vessels. Sophisticated software for route optimization, considering seabed topography, existing assets, and environmental sensitivities, is crucial for efficient and safe deployment.
-
Hybrid and Electric Propulsion for Vessels: To reduce fuel consumption and emissions, especially in sensitive marine environments, there's a growing trend towards hybrid or fully electric propulsion systems for cable laying vessels.
-
Enhanced Monitoring & Survey Capabilities: Integrated survey equipment (e.g., multibeam echosounders, sub-bottom profilers, ROV cameras) provides real-time data on seabed conditions, trenching progress, and cable lay position, ensuring accurate and compliant installation.
-
Specialized Equipment for Floating Wind: The emergence of floating offshore wind farms will require new approaches to cable laying, focusing on dynamic cables and potentially more flexible installation methods to accommodate movement between the floating platform and the seabed.
These cutting-edge advancements ensure that cable laying equipment can meet the unprecedented demands of the global energy transition, connecting powerful new energy sources to the grid with unparalleled efficiency and reliability.
"Cable Laying Tools" refer to the essential handheld devices, specialized implements, and smaller accessories that are directly used by technicians and installers during the precise process of guiding, supporting, measuring, and manipulating cables during their installation. They are distinct from the larger "Cable Laying Equipment" (like pulling machines or trenchers) and "Cable Pulling Accessories" (which include elements like rollers or lubricants, often working with the machine).
Cable Laying Tools fit into the overall installation process by:
-
Facilitating Precise Guidance: Ensuring the cable follows the exact path, especially around corners or into confined spaces.
-
Protecting Cable Integrity: Preventing damage such as kinking, twisting, or abrasion during manual handling or fine adjustments.
-
Enabling Accurate Measurement and Monitoring: Providing immediate feedback on critical parameters like tension or length.
-
Enhancing Worker Safety: Reducing manual strain, providing insulation, and improving control over heavy or difficult cables.
-
Supporting Termination and Splicing: Preparing cable ends for final connections.
They are the "fine instruments" that complement the heavy machinery, ensuring a high-quality, safe, and efficient cable installation from start to finish.
"Duct Rodders" and "Conduit Proofing Tools" are critical for preparing and verifying underground pathways before cable installation. Recent innovations focus on enhanced durability, usability, and data integration:
-
Advanced Composite Rod Materials: Modern duct rodders increasingly utilize fiberglass reinforced with specialized polymers, offering:
-
Higher Strength-to-Weight Ratio: Making them lighter for transport and easier to push over long distances, while maintaining exceptional tensile strength.
-
Improved Flexibility & Memory: Allowing them to navigate multiple bends and retain their original shape without permanent deformation.
-
Abrasion and UV Resistance: Ensuring longevity in harsh underground environments and during outdoor storage.
-
-
Integrated Measuring & Locating Technology: Some high-end rodders now incorporate:
-
Length Markings/Counters: Allowing for precise measurement of pulled length.
-
Embedded Sondes (Transmitters): Small, battery-powered transmitters at the rodder head that can be detected by surface locators, enabling precise mapping of underground conduit paths and identifying blockages.
-
-
Ergonomic & Portable Reels: Reels for duct rodders are designed to be more stable, with improved braking systems and larger wheels for easier maneuverability on job sites. Compact designs are also prevalent for confined spaces.
-
Advanced Conduit Proofing Mandrels:
-
Segmented and Articulated Designs: Mandrels are now often segmented or hinged to navigate complex bends more effectively, reducing the risk of getting stuck.
-
Brush/Scraper Attachments: Integrated brushes or scraping elements on mandrels help to clean the conduit as they pass through, removing debris that could damage cables or increase friction during the pull.
-
"Go/No-Go" Indicators: Some mandrels are designed with slight variations in diameter or flexible fins that clearly indicate if a conduit section is too narrow or has internal obstructions, providing immediate feedback.
-
These innovations ensure that underground conduits are thoroughly prepared and verified, preventing costly delays and cable damage during installation.
Specialized "Cable Cutting and Stripping Tools" are indispensable for efficient and safe cable termination, playing a crucial role in preparing cable ends for splicing or connection to equipment:
-
Precision and Clean Cuts: Modern cutters provide clean, burr-free cuts across various cable diameters and conductor types (copper, aluminum). This precision is vital for proper connection and minimizes wasted cable length. Hydraulic or battery-powered cutters are increasingly common for large diameter cables, significantly reducing manual effort and improving safety.
-
Damage-Free Insulation Removal: Stripping tools are designed to remove outer jackets and insulation layers precisely, without nicking or scoring the underlying conductors or insulation layers. This is critical for maintaining the dielectric strength of the cable and preventing future electrical faults. Adjustable blades and multi-stage strippers ensure a perfect cut depth for different cable constructions.
-
Ergonomics and Reduced Strain: Designs prioritize ergonomic handles, lighter materials, and spring-loaded mechanisms to reduce operator fatigue and the risk of repetitive strain injuries, especially when working with many terminations.
-
Safety Features: Many tools include safety locks, blade guards, and insulated handles (for tools used near energized components, meeting standards like IEC 60900) to protect the user from accidental cuts or electrical shock.
-
Versatility: "Multi-tool" designs combine cutting, stripping, and sometimes even crimping capabilities into a single tool, reducing the number of tools needed on site and improving workflow efficiency.
-
Speed and Repeatability: Precision tools ensure consistent results, leading to faster termination times and higher quality connections, which is particularly important for large-scale projects.
By providing clean, accurate, and safe cable preparation, these tools directly contribute to the reliability and longevity of the entire electrical system.
Safe and efficient management of large, heavy cable drums on job sites is crucial. "Cable Drum Handling Tools" have seen advancements focused on improved stability, mobility, and ease of use:
-
Hydraulic Drum Jacks/Stands: Modern drum jacks are often hydraulic, allowing for effortless lifting of massive cable drums (even several tons) with minimal manual effort. They feature robust, wide bases for superior stability, especially on uneven terrain.
-
Integrated Braking Systems: Many drum stands now include integrated disc or friction braking systems that allow operators to control the payout tension of the cable. This prevents over-spooling, reduces the risk of entanglement, and provides a controlled unwind during pulling.
-
Mobile Drum Trailers/Transporters: These specialized trailers are designed not just for transport but also for controlled payout of cable directly from the trailer. They often feature robust suspension, integrated braking, and hydraulic lifting mechanisms for quick setup and efficient deployment on site.
-
Compact & Foldable Designs: For smaller drums or sites with limited space, compact and foldable drum stands are available, making them easier to transport and store.
-
Roller Cradles & Roll-Off Platforms: These accessories are used to facilitate the smooth unwinding of cable from drums positioned horizontally, preventing damage to the drum flange and ensuring a consistent payout. They often feature multiple rollers with high load capacities.
-
Safety Features: Enhanced safety features include quick-locking mechanisms for the drum spindle, robust safety chains, and non-slip feet to prevent accidental movement during operations. Clear load rating indicators are standard.
-
Motorized Drum Drives (for specific applications): For very large drums or precise feeding, some advanced systems incorporate small electric or hydraulic motors to assist in unwinding or rewinding the drum, providing even greater control.
These advancements minimize manual handling risks, reduce setup time, and ensure a smooth, controlled cable payout, enhancing overall site safety and efficiency.
Installing delicate fiber optic cables requires a specialized set of "Cable Laying Tools" to ensure the integrity of the optical fibers, which are highly sensitive to bending, crushing, and twisting:
-
Fiber Optic Blowing Machines & Accessories: While a "machine," the nozzles and seals are critical tools. These systems use compressed air to "blow" or "jet" the lightweight fiber optic cable through micro-ducts or conduits, drastically reducing friction and enabling very long runs without mechanical stress.
-
Fiber Optic Cable Strippers: Highly precise strippers are essential to remove the outer jacket and buffering layers without scoring or damaging the delicate glass fibers or their protective coatings. Multi-hole strippers for different fiber diameters are common.
-
Fiber Optic Cleavers: These are precision tools used to create a perfect 90-degree, flat-end face on the fiber. A clean cleave is absolutely critical for minimal signal loss during fusion splicing or mechanical termination.
-
Fusion Splicers: These advanced devices precisely align two fiber ends and then use an electric arc to "fuse" them together, creating a permanent, low-loss connection. While a complex "tool," it's handheld or portable for field use.
-
Optical Power Meters (OPM) & Light Sources: Used in conjunction, these tools measure the optical power transmitted through the fiber and quantify signal loss (attenuation), verifying the integrity of the installed cable and splices.
-
Optical Time Domain Reflectometers (OTDRs): A powerful troubleshooting and certification tool. It sends light pulses down the fiber and measures reflections, providing a "picture" of the fiber's condition, identifying breaks, excessive bends, or splice losses.
-
Cable Slitting Tools: Specialized tools designed to create precise longitudinal cuts (slits) in fiber optic cable jackets for mid-span access without damaging the internal fibers.
-
Kevlar Cutters: Scissors specifically designed to cut the aramid yarn (Kevlar) strength members within fiber optic cables, which are notoriously difficult to cut with regular tools.
-
Fiber Optic Cleaning Supplies: Lint-free wipes, specialized solvents, and alcohol are critical for cleaning fiber ends before cleaving and splicing, as even microscopic dust can cause significant signal loss.
These tools ensure that every step of fiber optic cable handling, from preparation to connection and testing, is performed with the precision required for high-performance data transmission.
Proper inspection, maintenance, and calibration are vital for ensuring the safety, accuracy, and longevity of "Cable Laying Tools":
-
Pre-Use Inspection (Every Time):
-
Visual Check: Before each use, thoroughly inspect all tools for signs of damage: cracks, bends, nicks, deformation, excessive wear, corrosion, or loose parts. Check handles for security and insulation integrity.
-
Functionality Check: For tools with moving parts (e.g., strippers, crimpers), test their action to ensure smooth operation without binding or excessive play. Verify that safety mechanisms (locks, guards) are fully functional.
-
Cleanliness: Ensure tools are free of dirt, debris, grease, and cable residue that could impair function or cause damage.
-
-
Post-Use Cleaning: After each job, clean tools thoroughly, removing any lubricant, mud, or cable remnants. Use appropriate cleaning agents based on the tool's material.
-
Lubrication (as required): For tools with pivot points or moving mechanisms, apply appropriate lubricants according to the manufacturer's recommendations to ensure smooth operation and prevent wear.
-
Storage:
-
Dry & Protected: Store tools in a dry, cool, and well-ventilated area, preferably in dedicated toolboxes or on racks, away from direct sunlight, extreme temperatures, and moisture.
-
Organized: Proper organization prevents tools from being damaged by being thrown together, makes inspection easier, and ensures readiness for the next job.
-
Blade/Edge Protection: For cutting and stripping tools, ensure blades are protected to prevent dulling or damage.
-
-
Periodic Professional Maintenance:
-
Sharpening/Replacement of Blades: Cutting and stripping tools require periodic sharpening or replacement of blades/dies to maintain precision.
-
Calibration: Measuring tools like dynamometers and specialized fiber optic test equipment (OTDRs, OPMs) must be professionally calibrated at regular intervals (e.g., annually or bi-annually) by certified facilities to ensure their accuracy. Maintain calibration certificates.
-
Wear Part Replacement: Proactively replace wear parts (e.g., specific rollers on drum handling tools, worn jaw inserts on crimpers) before they fail catastrophically.
-
-
Removal from Service: Any tool showing significant damage, a compromise to its integrity, or failing a functional check must be immediately tagged and removed from service. Do not attempt to repair safety-critical tools unless you are a certified technician, and follow manufacturer guidelines strictly.
Adhering to these best practices significantly extends the working life of your cable laying tools, maintains their performance, and most importantly, ensures the safety of your personnel on site.
"Cable Laying Accessories" are a broad range of supplementary items and components that directly assist in the precise and safe placement of cables during installation. Unlike the main "Cable Laying Equipment" (which refers to the primary machines like trenchers or large pullers) or "Cable Laying Tools" (which are typically handheld implements), accessories are often passive components or consumables that play a crucial role in managing the cable's interaction with its environment.
They enhance efficiency and safety by:
-
Minimizing Friction and Stress: Accessories like specialized rollers, sheaves, and guides ensure the cable moves smoothly along its path, significantly reducing pulling force requirements and preventing damage from abrasion or kinking.
-
Providing Secure Guidance: They maintain the cable's intended route, especially around bends, over obstacles, or when guiding it into conduits, preventing uncontrolled movement that could lead to accidents or damage.
-
Ensuring Proper Tension Management: Accessories like dynamometers (tension meters) provide critical real-time data, allowing operators to keep pulling forces within safe limits for the cable and equipment.
-
Protecting Cable and Personnel: From warning tapes that prevent accidental excavation to safety hooks that manage loose cables, these accessories are designed to create a safer work environment and preserve the integrity of the installed cable.
-
Facilitating Inspection and Quality Control: Mandrels for conduit proofing or precise measuring devices help verify the pathway and the installed length, ensuring adherence to project specifications.
Essentially, these accessories are the unsung heroes that optimize every stage of the cable laying process, leading to smoother operations, fewer errors, and safer outcomes.
"Cable Drum Braking Systems" and "Tension Control Accessories" are vital for overhead tension stringing and controlled underground cable payout, ensuring a smooth process and preventing costly damage:
-
Controlled Payout: Their primary function is to apply a consistent and adjustable back tension to the cable drum as the cable is being pulled. Without this controlled resistance, the drum would free-spin, leading to:
-
Over-spooling: Cable spilling off the drum, leading to tangles, kinks, and potential damage.
-
Loss of Control: Unpredictable cable movement, which is extremely dangerous, especially for heavy conductors or at height.
-
Snagging: Loose cable is far more prone to snagging on ground obstacles.
-
-
Preventing Conductor Damage:
-
Maintaining Minimum Bend Radius: By controlling tension, the accessories prevent the cable from kinking or being subjected to excessively tight bends, which can damage insulation, conductor strands, or optical fibers (in OPGW).
-
Reducing Sag for OHTL: In overhead tension stringing, the tensioner (which uses a braking system) applies back tension to keep the conductor elevated above ground, preventing it from touching obstacles, roads, or energized lines, thus avoiding abrasion and dangerous conditions.
-
-
Types of Systems and Accessories:
-
Hydraulic Braking Systems: Often integrated into larger tensioners or specialized drum stands, these provide highly precise and adjustable braking force. They can be electronically controlled for automated tension maintenance.
-
Disc Brakes/Friction Brakes: Manual or semi-automatic brake systems attached to the drum spindle, allowing operators to apply mechanical resistance.
-
Dynamometers (Tension Meters): Crucial accessories that provide real-time measurement of the actual pulling force. Operators use this data to adjust the braking system and ensure the tension stays within the cable's maximum allowable limits (MAPT).
-
Digital Readouts: Modern systems provide clear digital displays of current tension, speed, and length, enabling operators to make informed adjustments.
-
These accessories are indispensable for achieving a high-quality, damage-free, and safe cable installation, particularly when dealing with large or sensitive conductors.
"Manhole/Duct Access Accessories" are crucial for safe and efficient cable laying in urban underground environments, which often involve confined spaces and high pedestrian/vehicle traffic:
-
Manhole Rollers:
-
Friction Reduction: These robust rollers are specifically designed to fit within manholes or vault entries. They elevate the cable off the rough edges or floor of the manhole, providing a smooth, low-friction path for the cable as it enters or exits the conduit, preventing costly jacket abrasion or kinking.
-
Guiding Through Bends: Many manhole rollers feature multiple sheaves or an articulated design to guide the cable smoothly through sharp turns within the manhole structure, accommodating the cable's minimum bend radius.
-
Heavy-Duty Construction: Built to withstand significant cable weight and pulling forces, often with sealed bearings for longevity in dirty environments.
-
-
Manhole Guards/Barriers:
-
Worker Safety: These foldable or portable barriers are erected around open manholes, clearly marking a hazardous area and preventing accidental falls by workers or the public. They are often bright, high-visibility colors with reflective strips.
-
Public Safety: They create a physical perimeter, keeping pedestrians and vehicles away from the open manhole and the moving cable, thus reducing the risk of injuries.
-
Security: They help deter unauthorized access to the underground network during construction.
-
Visibility: Many are equipped with flag holders or light attachments to enhance visibility, especially at night.
-
-
Manhole Covers and Lifters: Specialized tools like hydraulic manhole cover lifters make the safe and ergonomic removal and replacement of heavy manhole covers much easier, reducing the risk of back injuries to workers.
-
Duct Cones/Bellmouths: These accessories attach to the conduit opening within the manhole, providing a smooth, flared entry point for the cable. This prevents the cable from chafing against sharp conduit edges as it enters, particularly critical for large or stiff cables.
These accessories are indispensable for transforming potentially dangerous and inefficient urban underground cable installations into safe, controlled, and productive operations.
"Cable Grips" (also widely known as 'Chinese Fingers,' 'Cable Socks,' or 'Cable Stockings') are essential accessories that create a secure, temporary connection between the pulling rope and the cable or conductor. Their role is to transmit the pulling force efficiently while protecting the integrity of the cable.
Their evolution for modern cable types reflects demands for greater protection, higher strength, and versatility:
-
Enhanced Weave Patterns and Materials:
-
Uniform Pressure Distribution: Modern grips feature sophisticated woven mesh patterns (e.g., double or triple weave) that distribute the pulling force evenly along the cable's surface. This minimizes stress concentrations, preventing crushing, kinking, or damage to delicate insulation or optical fibers within the cable.
-
High-Strength Alloys & Composites: While galvanized steel remains common, grips are increasingly made from higher-strength stainless steel for corrosion resistance or even advanced synthetic fibers (like Aramid or UHMWPE blends) for applications requiring non-conductive properties or extreme strength-to-weight ratios.
-
-
Integrated Anti-Twist Swivels: Many premium grips now have a robust, high-quality anti-twist swivel directly integrated into the pulling eye. This is crucial as it prevents any rotational forces from the pulling rope (which can naturally twist under tension) from transferring to the cable, safeguarding internal conductors and especially sensitive fiber optics.
-
Reinforced Eyes and Shoulders: The pulling eye of the grip is often reinforced for durability, and the 'shoulder' where the cable enters the grip is smoothly tapered and often reinforced to prevent snagging and protect the cable end during entry into conduits or blocks.
-
Split-Type Designs: For situations where the cable end cannot be easily accessed (e.g., existing cables being replaced), split-type or open-ended grips allow the grip to be wrapped around the cable and secured, rather than requiring the cable to be fed through.
-
Specific Designs for Cable Types: Manufacturers now offer grips optimized for different cable jacket materials, diameters, and stiffness levels, including specialized grips for OPGW, underground power cables, and bundled conductors.
These advancements ensure that cable grips provide a reliable, damage-free, and safe connection, adapting to the complex demands of modern cable installation.
Proper maintenance and storage of "Cable Laying Accessories" are critical for ensuring their longevity, reliable performance, and, most importantly, the safety of personnel on job sites. Best practices include:
-
Thorough Cleaning After Each Use:
-
Remove all dirt, mud, lubricant residue, and moisture from rollers, guides, drum stands, and grips.
-
Use appropriate cleaning agents (e.g., mild soap and water for polymer components; degreasers for metal parts) that won't damage materials. Ensure no residue remains.
-
-
Detailed Inspection (Before & After Each Use):
-
Visual Check: Look for any signs of wear, damage (cracks, bends, nicks, deformation, excessive abrasion), corrosion, or loose fasteners on all components. Pay close attention to the surfaces that contact the cable (sheaves, rollers, grip mesh).
-
Functionality Check: For accessories with moving parts (e.g., drum stands, dynamometers, swivels), manually test their operation to ensure smooth movement, proper braking, and accurate readings.
-
Load Ratings: Verify that all Working Load Limit (WLL) markings on load-bearing accessories are clearly legible. If faded, re-mark or replace.
-
-
Proper Lubrication (as required):
-
For accessories with bearings, pivot points, or mechanical systems (e.g., some drum stands, tensioners, swivels), lubricate according to the manufacturer's specific recommendations, using the correct type and quantity of grease or oil.
-
Ensure any sealed bearings are intact.
-
-
Correct Storage Conditions:
-
Dry & Protected: Store all accessories in a dry, well-ventilated area, preferably indoors, away from direct sunlight, extreme temperatures, and excessive humidity to prevent rust, material degradation (especially for plastics/rubbers), and UV damage.
-
Organized: Store accessories neatly on racks, in dedicated bins, or on pallets. Avoid simply piling them, which can lead to damage, tangles, or make inspection difficult. Ensure small, critical components are secured.
-
Protect Sensitive Parts: For components like dynamometers, store them in their protective cases. Ensure cutting edges or delicate parts are shielded.
-
-
Calibration for Measuring Accessories:
-
Any measuring or monitoring accessories (e.g., dynamometers, length counters) must be regularly calibrated by certified technicians according to manufacturer guidelines (typically annually or bi-annually) to guarantee their accuracy. Keep calibration certificates on file.
-
-
Immediate Removal from Service: Any accessory showing significant damage, a compromise to its structural integrity, or failing a functional check must be immediately tagged and removed from service. Do not attempt to repair safety-critical items unless you are a qualified professional following manufacturer specifications, or simply replace them.
Consistent adherence to these practices ensures that your investment in cable laying accessories yields reliable performance, contributes to project efficiency, and upholds the highest safety standards.
A "Cable Installation Machine" is a specialized, often heavy-duty, piece of equipment designed to efficiently and safely deploy various types of cables and conductors for both overhead transmission lines (OHTL) and underground/subsea infrastructure. It represents a comprehensive category of machinery tailored to the specific demands of cable deployment.
Its key functions in modern power and communication projects include:
-
Tension Stringing (for OHTL): Applying precise, controlled tension during the stringing of overhead conductors (wires) to prevent them from dragging on the ground, damaging sensitive surfaces, or causing hazards to traffic and personnel. This involves using specialized pullers and tensioners.
-
Cable Pulling/Feeding (for Underground): Generating and accurately controlling the force needed to pull or feed cables through conduits, ducts, or open trenches, overcoming friction and resistance over long distances and around bends.
-
Trenching/Excavation (for Underground): For direct-bury applications, some installation machines (like trenchers or vibratory plows) are designed to excavate the pathway, often simultaneously laying the cable, minimizing ground disturbance.
-
Precise Cable Placement: Ensuring the cable is laid or strung at the correct depth, height, and along the specified route, protecting it from future damage and ensuring long-term reliability and adherence to engineering designs.
-
Cable Drum Management: Efficiently handling large and heavy cable drums, controlling their unwinding and re-winding, often with integrated braking and lifting systems.
-
Data Logging and Monitoring: Increasingly, these machines collect real-time data on parameters like pulling tension, speed, length, and GPS coordinates, which is vital for quality control, project management, and future maintenance.
These machines are fundamental to building and maintaining the critical infrastructure of our global power grids, telecommunication networks, and renewable energy systems.
Modern "Cable Installation Machines" are incorporating cutting-edge technologies to revolutionize safety and operational efficiency:
-
Advanced Automation and Control Systems:
-
Automated Tension and Speed Control: Intelligent systems continuously monitor pulling or stringing tension and automatically adjust machine speed to maintain a pre-set constant tension. This prevents over-tensioning that could damage the cable or equipment, and minimizes sag for OHTL.
-
Electronic Overload Protection: Immediate detection of excessive loads, with automatic shutdown or speed reduction to prevent critical failures, cable breakage, and injuries.
-
-
Real-time Data Acquisition & Telemetry: Integrated sensors provide live data on pulling force, length, speed, engine diagnostics, and hydraulic pressures. This data is displayed on intuitive operator interfaces and can be transmitted wirelessly to remote monitoring stations via IoT (Internet of Things) for real-time supervision and analysis.
-
GPS/GNSS Integration for Precision: High-accuracy GPS/GNSS (Global Navigation Satellite System) allows for pre-programmed route guidance, ensuring precise cable placement, minimizing deviations, and providing accurate "as-built" mapping for future reference.
-
Remote Monitoring & Diagnostics: Operators and project managers can monitor machine performance, track progress, and diagnose potential issues remotely. This capability allows for proactive maintenance planning and rapid response to operational challenges.
-
Ergonomics and Operator Comfort: Modern cabins feature improved ergonomics, climate control, reduced noise levels, and better visibility, leading to reduced operator fatigue, increased focus, and enhanced safety.
-
Predictive Maintenance: Leveraging AI and machine learning, advanced sensors analyze operational data to predict potential component failures, allowing for scheduled maintenance before breakdowns occur, significantly reducing unplanned downtime and maintenance costs.
-
Enhanced Safety Features: This includes multiple emergency stop buttons, interlocks, robust guarding of moving parts, fail-safe braking systems, and comprehensive alarm systems (audible and visual) to alert personnel to hazardous conditions.
These advancements collectively lead to significantly higher productivity, reduced risks, and improved quality in cable installation projects.
"Cable Installation Machines" are increasingly designed and operated with environmental sustainability as a core consideration, minimizing ecological impact:
-
Facilitating Trenchless Technologies: Many modern installation machines are designed for, or integrate with, trenchless methods such as Horizontal Directional Drilling (HDD), vibratory plowing, and micro-trenching. These techniques drastically reduce surface disruption, eliminate the need for large open trenches, and preserve existing landscapes, ecosystems, and urban infrastructure.
-
Reduced Ground Disturbance (for OHTL): In overhead tension stringing, the precise control of tension prevents conductors from dragging on the ground, minimizing damage to sensitive topsoil, vegetation, and existing infrastructure along the right-of-way.
-
Minimized Material Waste: Precision control features, automated tension management, and real-time monitoring significantly reduce the risk of costly cable damage during installation. This minimizes material waste from damaged cables that would otherwise need to be scrapped.
-
Lowered Fuel Consumption & Emissions: Modern machines are equipped with advanced, fuel-efficient engines that meet stringent global emission standards (e.g., EU Stage V, EPA Tier 4 Final). Optimized hydraulic systems and smart controls further reduce fuel consumption and associated greenhouse gas emissions. The growing availability of hybrid and electric-powered options is further reducing the carbon footprint.
-
Protection of Sensitive Areas: By allowing for precise route planning (with GPS integration) and less invasive installation techniques, these machines enable cable deployment in environmentally sensitive areas (e.g., wetlands, forested areas, agricultural lands) with minimal disturbance.
-
Reduced Noise Pollution: Newer machine designs often incorporate noise reduction technologies, lessening the acoustic impact on local communities and wildlife.
-
Faster Site Restoration: The efficiency of these machines leads to quicker project completion, allowing for faster restoration of disturbed areas to their original state, which aids in ecological recovery.
By adopting these advanced machines, infrastructure projects can significantly lessen their environmental footprint, aligning with global sustainability goals and promoting responsible development.
"Cable Installation Machines" are fundamentally important to the rapid and cost-effective deployment of fiber optic networks, especially for Fiber-to-the-Home/Building/Curb (FTTH/FTTB/FTTX) initiatives:
-
Fiber Optic Blowing Machines: These are highly specialized machines that use compressed air to "blow" or "jet" lightweight fiber optic cables through pre-installed micro-ducts or conduits. This method is incredibly efficient for:
-
Long Distances: Achieving very long, continuous runs with minimal friction and without exceeding the fiber's delicate pull tension limits.
-
Speed: Dramatically reducing installation time compared to traditional pulling methods.
-
Damage Prevention: Eliminating mechanical stress on the delicate optical fibers.
-
-
Micro-Trenchers: For urban and suburban fiber deployment, these compact machines cut very narrow, shallow trenches (micro-trenches) directly into existing pavement or sidewalks. This allows for rapid, minimally invasive installation of fiber optic bundles, significantly reducing restoration costs and traffic disruption.
-
Compact Horizontal Directional Drills (HDDs): Mini and midi-HDDs are extensively used to bore short to medium-length pathways for fiber optic conduits under roads, driveways, rivers, and other obstacles, avoiding the need for open cutting.
-
Small-Capacity Pulling Winches/Tractors: For shorter runs, internal building installations, or where blowing isn't feasible, precise, low-tension pulling machines are used for delicate fiber optic cables or sub-ducts.
-
Integrated Cable Feeder Units: Smaller, specialized versions of cable feeders are used to assist in pushing fiber optic cables or sub-ducts into conduits, especially around bends, to reduce friction and minimize pulling tension.
-
Vacuum Excavators: These are often used in conjunction with trenchless methods to safely expose existing utilities, reducing the risk of damaging vital infrastructure during fiber installation.
By providing efficient, precise, and minimally invasive installation solutions, these machines are essential enablers for the global rollout of high-speed broadband and the digital transformation.
"Cable Installation Machines" are highly specialized, with different types and capacities tailored to the specific voltage levels and characteristics of power lines:
-
For Low Voltage (LV) and Medium Voltage (MV) Cables (e.g., up to 33kV):
-
Smaller Hydraulic Pulling Winches: Often skid-mounted or on compact trailers, with capacities ranging from 1 to 5 tons. Used for pulling service lines, distribution feeders, and underground residential distribution (URD) cables.
-
Vibratory Plows & Compact Trenchers: Ideal for direct burial of LV/MV cables in urban and suburban areas or agricultural lands, offering minimal disruption.
-
Cable Feeder/Pusher Units: Smaller, often track-driven, units that assist in pushing cables into ducts, reducing friction and sidewall pressure.
-
Mini and Midi Horizontal Directional Drills (HDDs): For installing LV/MV conduits under roads, driveways, or sensitive landscapes without open trenching.
-
-
For High Voltage (HV) and Extra High Voltage (EHV) Cables (e.g., 66kV to 800kV and beyond):
-
High-Capacity Hydraulic Pullers/Tensioners: These are the workhorses for large overhead transmission lines and heavy underground HV/EHV cables.
-
Pullers (Winch Type): Extremely powerful, trailer-mounted machines with capacities often ranging from 10 to 100+ tons. They feature bullwheel or capstan designs with precise constant tension control for pulling long lengths of heavy conductors or cables.
-
Tensioners: Used in conjunction with pullers for OHTL stringing, these machines apply controlled back tension to the conductor drum, preventing conductor sag and ensuring safe clearance during stringing. They can be single, double, or even quad-bundle tensioners for multiple conductors.
-
-
Large Horizontal Directional Drills (HDDs): Massive drilling rigs capable of installing large-diameter conduits over very long distances (hundreds to thousands of meters) for HV/EHV underground cable crossings (e.g., rivers, major highways).
-
Cable Conveyors/Pushers (Heavy-Duty): Larger, more robust versions of feeder units, providing substantial pushing force to aid pulling of extremely heavy HV/EHV cables through long conduit runs, particularly in tunnels or long ducts.
-
Specialized Subsea Cable Laying Vessels (for Offshore HVDC/HVAC): For offshore wind farms or interconnector projects, these are highly specialized ships equipped with massive cable tanks, linear cable engines (LCEs), and sophisticated payout/burial systems to install immense HVDC or HVAC submarine cables.
-
The choice of "Cable Installation Machine" depends critically on the cable's weight, diameter, stiffness, the terrain, project scale, and the required installation method (overhead, direct bury, or duct).
To ensure the longevity, peak performance, and reliable operation of "Cable Installation Machines," a structured and professional maintenance schedule, coupled with robust support, is essential:
1. Regular & Preventative Maintenance (OEM Recommended):
-
Daily/Shift Checks:
-
Fluid levels (engine oil, hydraulic fluid, coolant).
-
Visual inspection for leaks, loose fasteners, damaged hoses, or worn components.
-
Functionality check of emergency stops and safety guards.
-
Cleaning of critical areas (e.g., operator cabin, sensor lenses, bullwheel grooves).
-
-
Weekly/Bi-Weekly Checks:
-
Greasing of all lubrication points.
-
Inspection of cables, ropes, and wire rope terminations for wear or damage.
-
Check tire pressure/track tension.
-
Inspection of brake systems and hydraulic lines.
-
Filter checks (air, fuel, hydraulic).
-
-
Monthly/Quarterly Checks:
-
Full inspection of all structural components for cracks or fatigue.
-
Hydraulic system health check (pressure, flow, filter replacement).
-
Engine service (oil and filter changes).
-
Calibration verification of tension/speed sensors and load cells.
-
Electrical system inspection (wiring, connections, battery).
-
-
Annual/Bi-Annual Major Service:
-
Comprehensive overhaul inspections.
-
Fluid analysis (oil, hydraulic fluid) to detect wear particles.
-
Replacement of all critical filters.
-
Detailed inspection and potential rebuild of high-wear components (e.g., bullwheels, drive motors, gearboxes).
-
Software updates and diagnostic checks of control systems.
-
2. Professional Support & Services:
-
Manufacturer's Comprehensive Manuals: Detailed operation, maintenance, and troubleshooting guides provided in multiple languages.
-
Dedicated Technical Support: Access to experienced technical support teams via phone, email, or online portals, often with 24/7 availability for international clients.
-
Remote Diagnostics & Telematics: Leveraging built-in telematics systems to remotely diagnose issues, monitor machine health, and provide proactive alerts, minimizing the need for on-site visits.
-
Global Spare Parts Availability: A robust supply chain with strategically located warehouses or efficient logistics to ensure rapid delivery of genuine spare parts, minimizing downtime.
-
Certified Field Service Technicians: Access to highly skilled and factory-trained technicians who can be dispatched to perform complex repairs, major services, and critical calibrations on-site.
-
Operator & Maintenance Training: Comprehensive training programs (on-site or virtual) for client personnel to ensure safe, efficient, and proper operation and routine maintenance of the machines.
-
Service Level Agreements (SLAs): Offering flexible service contracts that can include scheduled preventative maintenance, priority support, and guaranteed response times, providing peace of mind and optimizing asset uptime.
-
Software Updates & Upgrades: Regular updates for machine control software to improve performance, add new features, and enhance security.
Adhering to these practices, often in partnership with the manufacturer, is crucial for maximizing the lifespan, reliability, and resale value of your cable installation machines.
"Cable Installation Equipment" refers to the specialized machinery, systems, and integrated solutions designed for the complete deployment of electrical cables and conductors, encompassing both Overhead Transmission Lines (OHTL) and underground/subsea cable networks. It goes beyond just pulling or laying machines, representing the entire suite of robust engineering tools needed for complex infrastructure projects.
It provides a comprehensive solution by:
-
Covering Both Overhead and Underground Methods: This includes tension stringing equipment for OHTL (pullers, tensioners, reel winders, anti-twist devices) and a wide range of machinery for underground installations (hydraulic pulling winches, trenchers, vibratory plows, horizontal directional drills, cable feeder units).
-
Managing the Entire Cable Lifecycle (Installation Phase): From the initial preparation of the route (e.g., conduit proofing, trenching) to the precise feeding, pulling, or laying of the cable, and often initial backfilling or tension control for OHTL.
-
Handling Diverse Cable Types and Sizes: Designed to safely and efficiently install everything from delicate fiber optic cables to massive High-Voltage Direct Current (HVDC) power cables and multi-conductor bundles.
-
Ensuring Precision and Control: Modern equipment incorporates advanced control systems to manage critical parameters like tension, speed, and positioning, minimizing stress on the cable and ensuring a high-quality installation.
-
Prioritizing Safety and Efficiency: By automating heavy tasks, providing real-time feedback, and incorporating robust safety features, this equipment significantly reduces manual labor, enhances worksite safety, and accelerates project timelines.
Essentially, "Cable Installation Equipment" offers a one-stop solution for deploying any type of cable infrastructure, ensuring project efficiency, safety, and long-term reliability across various environments.