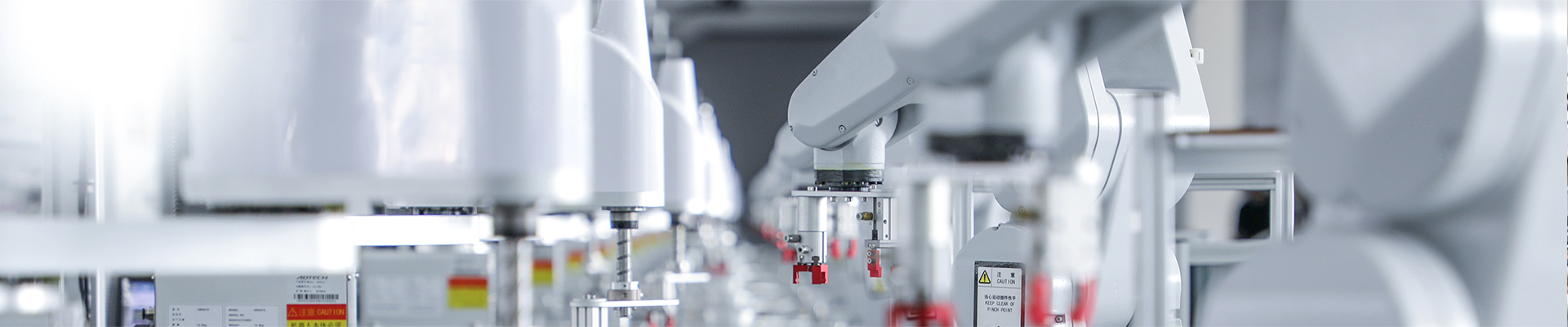
FAQ
Anti-Twist Swivels are crucial safety and conductor protection accessories, serving the vital role of preventing torsional forces from transferring to the conductor during stringing operations. Without them, the pulling rope's natural tendency to twist under load could cause conductors (especially bundled ones or OPGW) to rotate, leading to damage, unraveling, or compromised optical fibers.
The latest features ensuring their reliability include:
-
High-Capacity, Sealed Bearing Systems: Modern swivels incorporate robust, precision-engineered sealed bearings (e.g., thrust bearings, ball bearings) that allow for free rotation under extreme radial and axial loads. The sealed design protects against dirt, moisture, and corrosion, ensuring smooth operation in harsh environments.
-
High-Strength Forged Construction: Swivel bodies are typically forged from high-grade alloy steels, providing exceptional tensile strength and durability to withstand the substantial pulling forces.
-
Clear Working Load Limit (WLL) Markings: Each swivel is clearly marked with its WLL and often tested to a higher proof load, ensuring operators select the correct swivel for the anticipated forces.
-
Integrated Grease Fittings: While sealed bearings reduce maintenance, some high-capacity swivels still feature easily accessible grease fittings for periodic lubrication, ensuring longevity.
-
Compact and Ergonomic Design: Despite their strength, newer designs are often more compact and lighter, making them easier to handle and integrate into the stringing setup.
-
Corrosion-Resistant Finishes: Durable coatings or galvanization protect the metallic components from rust and environmental degradation.
These features ensure that anti-twist swivels reliably absorb rotational energy, safeguarding the conductor's integrity and enhancing overall stringing safety.
Conductor Pulling Grips and Running Boards are specifically designed to provide a secure, non-damaging connection between the pulling rope and the conductor(s) through various mechanisms:
-
Woven Mesh Design (Pulling Grips): For single conductor pulling grips, the "Chinese finger" or stocking design is key. The woven steel or aramid fiber mesh tightens circumferentially around the conductor as tension is applied, creating a distributed grip over a significant length. This even pressure prevents crushing or localized stress points.
-
Optimized Jaw/Clamping Mechanisms (Running Boards): Running Boards for bundled conductors feature individual, articulated clamping mechanisms for each conductor in the bundle. These clamps are precisely designed to grip the outer strands of each conductor securely without deforming the conductor's cross-section or internal components.
-
Material Compatibility: The inner surfaces of the gripping elements (whether mesh or clamps) are often designed or coated with materials compatible with the conductor's outer layer (e.g., aluminum, steel, composite), enhancing friction while preventing abrasion.
-
Load Distribution: Both types of accessories are designed to distribute the pulling force evenly over a large contact area of the conductor, preventing concentration of stress that could lead to kinking, denting, or strand damage.
-
Built-in Safety Factors: All grips and running boards are manufactured with significant safety factors above their rated Working Load Limit (WLL), meaning they are designed to withstand forces considerably higher than their intended operational load.
-
Anti-Slippage Design: The geometry and material of the gripping elements are engineered to increase friction under load, actively resisting slippage and ensuring a continuous, controlled pull.
-
Clear Conductor Diameter Ranges: Each grip and running board is specified for a precise range of conductor diameters, ensuring a snug and effective fit.
By combining ingenious mechanical designs with appropriate materials, these accessories provide robust and non-damaging attachment crucial for successful stringing.
Digital Dynamometers are indispensable accessories in modern conductor stringing, offering significant benefits in terms of precision, safety, and operational control:
-
Real-time Tension Monitoring: They provide instantaneous, highly accurate digital readouts of the pulling or tensioning force (in kN, lbs, etc.). This allows operators to continuously monitor tension and ensure it remains within the conductor's specified safe working load limits and the project's sag requirements.
-
Enhanced Precision and Quality Control: By providing precise feedback, dynamometers enable crews to achieve exact sag and tension specifications, which is critical for the long-term electrical performance, structural stability, and longevity of the transmission line. This reduces deviations and ensures compliance with design parameters.
-
Improved Safety:
-
Overload Prevention: Operators are immediately alerted if tension approaches or exceeds safe limits, allowing them to stop the operation before conductor breakage, equipment failure, or injury occurs.
-
Snag Detection: Sudden spikes in tension indicate a potential snag or obstruction, allowing crews to investigate and resolve the issue before major damage to the conductor or equipment.
-
Controlled Braking: For tensioners, precise tension feedback ensures controlled braking and pay-out, preventing uncontrolled conductor run-away.
-
-
Data Logging and Reporting: Many digital dynamometers offer data logging capabilities, recording tension, time, and other parameters. This data can be downloaded for post-operation analysis, project documentation, quality assurance, and legal compliance.
-
Wireless Connectivity (Emerging): Some advanced models offer wireless connectivity, allowing tension data to be viewed on remote displays or integrated into broader project management systems, improving communication and coordination.
-
Versatility: They are used at both the puller and tensioner ends, and for various stringing scenarios, from initial pilot rope pulls to heavy conductor bundles.
Digital dynamometers transform tension stringing from an estimation to a precise, data-driven process, significantly improving safety, efficiency, and the quality of the final installation.
Conductor Stringing Accessories play a crucial, often overlooked, role in minimizing the environmental and ecological impact of overhead line construction:
-
Reduced Ground Disturbance: By enabling the tension stringing method, accessories like stringing blocks and specialized pulling grips keep conductors elevated well above the ground throughout the installation process. This drastically reduces the need for extensive vegetation clearing, avoids soil compaction, and prevents damage to sensitive ecosystems, waterways, and agricultural land.
-
Prevention of Conductor Damage and Waste: High-quality accessories like precision stringing blocks with non-abrasive linings, anti-twist swivels, and secure pulling grips protect the conductor from kinks, scratches, and twisting. This minimizes costly conductor waste due to damage and eliminates the need for re-stringing, conserving valuable resources.
-
Lowered Noise Pollution: Well-maintained stringing blocks with advanced bearings and smooth polymer linings reduce friction and operational noise compared to older, less sophisticated designs, lessening noise impact on local wildlife and communities.
-
Durability and Longevity: Accessories manufactured from high-grade, durable materials with corrosion-resistant coatings have extended lifespans. This reduces the frequency of replacement, thereby decreasing the environmental footprint associated with raw material extraction and manufacturing processes.
-
Efficient Resource Utilization: By enabling faster and more efficient stringing operations, these accessories contribute to reduced fuel consumption by the larger stringing machines, lowering carbon emissions and air pollution from heavy equipment.
-
Compliance with Environmental Regulations: By facilitating the "no-ground-contact" stringing method, accessories help utility companies and contractors comply with strict environmental protection regulations concerning land disturbance, habitat protection, and noise control.
In summary, selecting and properly utilizing high-quality Conductor Stringing Accessories is an integral part of sustainable and environmentally responsible power line construction.
A "Conductor Pulling Machine" (often referred to simply as a "puller" or "winch" in underground applications) is a powerful, specialized piece of equipment designed to generate and control the force required to pull electrical conductors or cables through various pathways. Its primary function is to draw the conductor along a specified route.
While often used in conjunction, a "Conductor Pulling Machine" differs from a "Conductor Tensioning Machine" (tensioner) in its primary role:
-
Conductor Pulling Machine (Puller): This machine is positioned at the receiving end of a cable or conductor run. Its main job is to apply a controlled pulling force to draw the conductor from the feeding end. For Overhead Transmission Lines (OHTL), it pulls the pilot rope, then the conductor, across stringing blocks. For Underground Cable Laying, it pulls the cable through conduits, ducts, or trenches.
-
Conductor Tensioning Machine (Tensioner): This machine is located at the feeding end of an overhead conductor stringing operation. Its purpose is to apply a controlled back tension to the conductor as it is pulled. This prevents the conductor from touching the ground, damaging vegetation, or coming into contact with obstacles, ensuring a safe sag profile during installation.
In overhead tension stringing, the puller and tensioner work in precise, synchronized tandem. For underground cable laying, a puller is typically the standalone primary machine.
When evaluating a modern Conductor Pulling Machine, several key performance indicators (KPIs) and technical specifications are crucial for ensuring it meets project demands and offers optimal performance:
-
Maximum Pulling Force (kN or lbs): This is the peak force the machine can exert. It's critical to select a machine with a capacity well above the maximum anticipated pulling force for your specific conductors, cable lengths, and terrain/duct resistance.
-
Continuous Pulling Force (kN or lbs): The force the machine can sustain over extended periods of operation, indicating its durability for long pulls.
-
Maximum Pulling Speed (km/h or ft/min): The highest speed at which the machine can pull. Higher speeds can improve project timelines, but must be balanced with conductor safety and control.
-
Pulling Rope / Cable Capacity: The length and diameter of the pulling rope or cable the machine's drum or bullwheels can accommodate. This dictates the maximum length of a pull section.
-
Bullwheel Diameter & Lining Material: For OHTL pullers, larger bullwheel diameters minimize bending stress on conductors. The lining material (e.g., polyurethane, MC nylon) is crucial for grip and preventing conductor damage. For underground, the drum material and design are important.
-
Engine Power (HP or kW) & Fuel Efficiency: Indicates the machine's overall power and operational cost-effectiveness. Consider options like diesel, hybrid, or electric.
-
Control System Sophistication: Look for intuitive digital controls, real-time tension and speed readouts, automatic tension limiting, and data logging capabilities.
-
Mobility & Transportability: Whether it's a trailer-mounted unit, a self-propelled track machine, or designed for easy integration onto other vehicles, ease of transport to diverse job sites is vital.
-
Hydraulic System Quality: A robust, closed-loop hydraulic system ensures precise, smooth, and consistent pulling force control.
-
Safety Features: Overload protection, emergency stops, fail-safe braking, and operator protection are non-negotiable.
The integration of "Smart" technology is revolutionizing Conductor Pulling Machines, significantly enhancing both safety and operational efficiency:
-
Real-time Data Telemetry: Integrated sensors collect critical operational data (pulling force, speed, length pulled, hydraulic pressure, engine diagnostics). This data is often displayed on intuitive digital screens and can be transmitted wirelessly (telematics) to remote monitoring stations or mobile devices.
-
Automated Tension Control & Limiting: Smart machines can maintain a pre-set pulling tension automatically. They feature electronic overload protection that detects sudden spikes in tension (e.g., due to a snag or obstruction) and can automatically slow down or stop the pull, preventing conductor damage or equipment overload.
-
Predictive Maintenance: By continuously monitoring machine parameters and analyzing historical data, smart systems can predict potential mechanical failures (e.g., engine issues, hydraulic pump wear) before they occur. This enables proactive maintenance, reducing unplanned downtime and costly repairs.
-
GPS Tracking & Geofencing: GPS allows for precise tracking of machine location and progress. Geofencing can be set up to ensure machines operate only within designated safe zones, enhancing site management and security.
-
Remote Diagnostics & Troubleshooting: Technicians can often access machine diagnostics remotely, allowing for quicker identification and resolution of issues, potentially avoiding the need for on-site visits.
-
Optimized Power Management: Smart systems manage engine RPM and hydraulic flow more efficiently, leading to better fuel economy and reduced emissions.
-
Integrated Data Logging & Reporting: All operational data is logged and can be easily downloaded to generate detailed reports for project management, quality assurance, and compliance documentation. This provides an invaluable record of the stringing process.
-
Enhanced Operator Interface: User-friendly touchscreen interfaces with clear graphical displays make operation more intuitive, reducing the learning curve and potential for human error.
These smart features transform conductor pulling from a manual operation into a highly controlled, data-driven, and safer process.
Underground cable laying presents unique challenges, requiring specialized Conductor Pulling Machines distinct from those used for overhead lines. Their unique features focus on managing friction, navigating conduits, and handling heavy, rigid cables:
-
Constant Tension Winches: These winches are designed to pull cables through ducts with highly variable friction. They maintain a consistent, pre-set pulling tension, automatically adjusting speed to avoid over-stressing the cable or damaging the conduit.
-
Caterpillar (Track-Type) Pullers: Often used in conjunction with winches, these machines provide a continuous "push-pull" action on the cable, particularly useful for reducing sidewall pressure in bends and overcoming friction in long, complex duct runs. They grip the cable directly with rubber or metal tracks.
-
Modular & Portable Designs: Many underground pulling machines are designed to be compact and highly portable, allowing them to be easily transported to confined spaces, manholes, or vaults where traditional large equipment cannot access.
-
Automatic Level Winders: Integrated mechanisms on the winch drum ensure that the pulling rope or cable is spooled on evenly, preventing tangles, maximizing drum capacity, and facilitating smooth pay-out on the next pull.
-
Integrated Force & Length Monitoring: Essential for underground pulls, these systems provide real-time data on pulling force and the exact length of cable pulled, crucial for avoiding over-tensioning and accurately locating cable segments.
-
Hydraulic Power Units: Often separate from the pulling head, these provide versatile power to various pulling attachments in confined spaces.
-
Specialized Pulling Ropes/Mule Tape: Designed for underground applications, these ropes have high tensile strength, low stretch, and are often made from materials that reduce friction within ducts.
These specialized machines, combined with appropriate lubricants and rollers, are critical for the safe and efficient installation of underground power and communication cables.
Proper maintenance is paramount for ensuring the longevity, reliability, and peak performance of a Hydraulic Conductor Pulling Machine, given the heavy loads and demanding environments they operate in:
-
Adherence to Manufacturer's Manual: This is the foundational rule. Strictly follow all recommended service intervals and procedures for fluid changes, filter replacements, and inspections.
-
Hydraulic System Management:
-
Fluid Quality: Regularly check hydraulic fluid levels and cleanliness. Change hydraulic oil and filters (return, pressure, suction) according to schedule. Contaminated or degraded fluid is the leading cause of hydraulic system failure.
-
Leak Detection: Daily inspect all hydraulic hoses, fittings, and cylinders for any signs of leaks, chafing, or damage. Address leaks immediately to prevent fluid loss and contamination.
-
-
Engine Maintenance: Perform routine engine checks including oil levels, coolant, fuel filters, air filters, and fan belts. Ensure the engine is running smoothly without unusual noises or excessive smoke.
-
Bullwheel/Drum Inspection:
-
OHTL Pullers: Regularly inspect bullwheel linings for wear, cracks, or grooves. Replace linings if significant wear is present to prevent conductor damage. Check bullwheel bearings for smooth rotation and excessive play.
-
Underground Pullers: Inspect the pulling drum for damage, wear, or debris. Ensure the level winder mechanism operates smoothly.
-
-
Brake System Check: For machines with braking systems, regularly inspect brake pads, discs, and hydraulic components for wear and proper function.
-
Rope/Cable Path Inspection: Ensure all guides, rollers, and fairleads that the pulling rope or cable passes through are clean, free of debris, and in good condition to prevent abrasion and friction.
-
Electrical System Check: Inspect wiring, connections, sensors, and the control panel for any signs of damage or loose connections.
-
Structural Integrity: Periodically inspect the machine frame, chassis, anchoring points, and lifting points for cracks, bends, or corrosion.
-
Cleanliness & Storage: Keep the machine clean, especially hydraulic components and control panels. Store the machine in a dry, protected environment when not in use to prevent weather-induced degradation.
-
Calibration: Ensure that integrated tension sensors and dynamometers are regularly calibrated by certified technicians to maintain accuracy.
While there are specialized machines for each, our range of Conductor Pulling Machines offers specific models and adaptable features that cater to the distinct demands of both Overhead Transmission Line (OHTL) and Underground Cable Laying applications:
For Overhead Transmission Line (OHTL) Applications:
-
Bullwheel Design: Our OHTL-focused pulling machines feature large-diameter, multi-groove bullwheels with specialized, non-abrasive linings (e.g., polyurethane) to grip pilot ropes and conductors gently yet firmly.
-
Precise Tension Synchronization: When paired with our tensioners, these pullers operate in a closed-loop hydraulic system to maintain synchronized, consistent tension and speed, crucial for tension stringing.
-
Integrated Rope Winders: Often include hydraulic rope winders for neatly coiling the pilot rope, facilitating subsequent pulls.
-
Designed for Open Terrain: Typically trailer-mounted or self-propelled track machines suitable for traversing varied terrain along power line rights-of-way.
For Underground Cable Laying Applications:
-
Drum/Winch Design: Our underground-specific pulling machines primarily feature large, robust drums or winches designed to spool significant lengths and weights of pulling rope or cable.
-
Variable Speed & Constant Pulling Force: Engineered to handle high friction and resistance, they can often maintain a constant pulling force while automatically adjusting speed through long, often winding, underground conduits.
-
Integrated Length & Force Measurement: Crucial for precise placement and avoiding over-tensioning in buried ducts, these machines provide accurate readouts of pulled length and force.
-
Compact & Mobile: Many models are designed for maneuverability in tight urban environments, manholes, or trenches, with options for skid mounting or highly compact trailer designs.
-
Caterpillar Track Integration: Some models can be combined with or are themselves caterpillar-type pullers that push cables through difficult sections, reducing overall pulling tension.
Adaptability & Shared Core Technologies:
-
Robust Hydraulic Systems: Both applications benefit from our advanced, reliable hydraulic systems that provide smooth, controlled power transmission.
-
Advanced Control Systems: Digital controls, real-time feedback, and safety features like overload protection are standard across both types of machines, ensuring precise operation and operator safety.
-
Durability and Reliability: All our pulling machines are built with high-strength materials and robust construction to withstand the demanding conditions of both overhead and underground work.
By offering a specialized range and incorporating adaptable core technologies, we provide the right Conductor Pulling Machine for any power line construction challenge.
"Conductor Pulling Equipment" refers to the comprehensive suite of machinery, tools, and accessories specifically designed to generate, control, and monitor the force required to pull electrical conductors or cables. This equipment is crucial for both overhead transmission line (OHTL) construction and underground cable laying due to its ability to:
-
Generate High Force: Capable of overcoming significant friction and resistance over long distances and through complex pathways.
-
Ensure Precision: Allows for controlled speed and tension, preventing damage to sensitive conductors and ensuring installation meets exact engineering specifications (e.g., sag in OHTL, bend radius in underground conduits).
-
Enhance Safety: By mechanizing heavy and hazardous pulling tasks, it significantly reduces manual labor, minimizes the risk of worker injury, and prevents uncontrolled conductor movement.
-
Improve Efficiency: Automates and speeds up the installation process, leading to shorter project timelines and reduced labor costs.
-
Versatility: Specific equipment within this category is tailored for the unique challenges of aerial stringing (tension pulling) and subterranean installation (through ducts or trenches).
It forms the backbone of modern electrical infrastructure development, enabling the rapid and safe deployment of power and communication networks.
Modern Conductor Pulling Equipment is increasingly incorporating "smart" technologies and advanced automation to optimize performance, enhance safety, and provide real-time data for better project management:
-
Telematics & Remote Monitoring: Equipment is outfitted with IoT sensors that collect real-time data on pulling force, speed, length pulled, hydraulic pressure, and engine diagnostics. This data can be accessed remotely via cloud platforms or mobile apps, enabling supervisors to monitor progress, identify anomalies, and facilitate proactive maintenance from anywhere.
-
Automated Tension/Force Control: Advanced closed-loop hydraulic systems with integrated electronic sensors can automatically maintain a pre-set pulling tension or force. If unexpected resistance or a snag occurs, the system can automatically adjust speed or stop the pull to prevent conductor damage or equipment overload.
-
Integrated GPS & Geofencing: GPS technology tracks the exact location and progress of the pulling operation along the route. Geofencing capabilities can be set up to ensure equipment operates within designated work areas, enhancing site safety and security.
-
Predictive Maintenance Analytics: By continuously analyzing operational data, smart systems can predict potential mechanical failures (e.g., worn components, fluid degradation) before they occur. This allows for scheduled maintenance, minimizing unexpected downtime and costly emergency repairs.
-
User-Friendly Digital Interfaces: Operators benefit from intuitive, often touchscreen, control panels that provide clear graphical readouts of all critical parameters, simplifying operation and reducing the likelihood of human error.
-
Automated Cable/Rope Winding: For underground applications, features like automatic level winders ensure the pulling rope or cable is spooled neatly and evenly onto the drum, preventing tangles and optimizing drum capacity.
-
Data Logging and Reporting: All key operational data is automatically logged and can be easily downloaded for comprehensive project documentation, quality assurance, and compliance reporting.
These innovations create a highly controlled, data-driven, and safer environment for conductor installation.
Underground cable laying, especially in dense urban areas or challenging terrains, requires highly specialized Conductor Pulling Equipment to overcome unique obstacles:
-
Compact & Modular Designs: Equipment is often designed to be highly portable and compact, allowing easy access and setup in confined spaces like manholes, vaults, or narrow trenches where larger, traditional machinery cannot operate. Many units can be broken down into smaller modules for easier transport.
-
High-Capacity, Constant Tension Winches: These winches are engineered to pull long, heavy cables through complex, multi-bend duct systems while maintaining a consistent, precise pulling tension. They automatically adjust speed to overcome variable friction along the route, preventing over-stressing the cable.
-
Caterpillar (Track-Type) Pullers: Often used as feeder systems or in conjunction with winches, these direct-drive machines grip the cable with rubber or steel tracks, providing additional pushing or pulling force to reduce sidewall pressure in bends and minimize friction over long runs.
-
Integrated Force, Speed, and Length Monitoring: Precise digital readouts of pulling force, speed, and exact length pulled are critical. This prevents costly over-tensioning, accurately tracks cable placement, and helps identify blockages in ducts.
-
Wireless Remote Control: Many units offer wireless remote control, allowing operators to position themselves optimally for visibility and safety, especially when working in hazardous or confined spaces.
-
Hydraulic Power Units: Often separate from the pulling head, these provide versatile hydraulic power to various pulling attachments in locations where a full machine cannot be positioned.
-
Specialized Lubrication Systems: Compatible with eco-friendly cable lubricants, these systems ensure friction is minimized as cables enter conduits, reducing the required pulling force and protecting cable jackets.
By integrating these features, our Conductor Pulling Equipment ensures safe, efficient, and precise underground cable installations, even in the most demanding environments.
Safety is paramount in all power line and cable construction, and our Conductor Pulling Equipment is designed with stringent safety features and adherence to international standards:
-
Automatic Overload Protection: Electronic and hydraulic systems continuously monitor pulling force. If pre-set maximum limits are approached or exceeded, the machine automatically reduces speed or stops, preventing equipment damage, conductor breakage, and potential injury to personnel.
-
Emergency Stop Buttons: Prominently located and easily accessible emergency stop buttons provide immediate shutdown capability in any critical situation.
-
Fail-Safe Braking Systems: For machines utilizing tensioning (like OHTL pullers or tensioners), spring-applied, hydraulically-released brakes automatically engage if hydraulic pressure is lost or power fails, preventing uncontrolled conductor movement.
-
Operator Protection: Machines often feature guarded areas, safety cages, or enclosed cabins to protect operators from moving parts, noise, and environmental elements.
-
Clear Working Load Limits (WLL): All load-bearing components and the machine itself are clearly marked with their WLL, and operators are trained to never exceed these limits, ensuring a sufficient safety factor.
-
Guarding of Moving Parts: All rotating components, bullwheels, drums, and pinch points are securely guarded to prevent accidental contact.
-
Robust Anchoring Points: Equipment is designed with strong, clearly defined anchoring points to ensure stable setup and prevent movement during high-force pulling operations.
-
Compliance with International Standards: Our equipment is designed and manufactured to meet relevant international safety standards such as those from ISO (e.g., ISO 12100 for machine safety), CE Marking (for European market compliance), and local occupational safety and health regulations (e.g., OSHA where applicable). We provide comprehensive safety manuals and training guidelines.
-
Real-time Diagnostics: Onboard diagnostic systems alert operators to potential malfunctions or unsafe operating conditions, allowing for immediate corrective action.
Our Conductor Pulling Equipment solutions are engineered to deliver significant cost savings and optimize operational efficiency throughout the entire project lifecycle:
-
Reduced Labor Requirements: Automated and powerful pulling systems minimize the need for extensive manual labor, leading to lower wage expenditures and more efficient utilization of highly skilled crews.
-
Faster Project Completion: High pulling speeds, precise control, and robust reliability enable quicker installation of conductors and cables over long distances, directly shortening project timelines and avoiding costly delays or penalties.
-
Minimized Conductor/Cable Damage: Precise tension control, non-abrasive bullwheel/drum linings, and advanced safety features prevent costly damage to expensive conductors and cables, reducing material waste and eliminating the need for expensive re-pulls.
-
Optimal Resource Utilization: Smart features like telematics and predictive maintenance minimize unplanned downtime, ensuring equipment is available and operational when needed, maximizing its utilization across multiple projects.
-
Fuel Efficiency: Modern engines and optimized hydraulic systems in our pulling equipment are designed for enhanced fuel efficiency, significantly reducing operational fuel costs.
-
Increased Safety, Lower Costs: Enhanced safety features reduce the risk of accidents and injuries, which can translate to lower insurance premiums, fewer compensation claims, and avoided legal liabilities.
-
Versatility & Adaptability: Equipment designed to handle a wide range of conductor types, sizes, and applications (OHTL and underground) offers greater flexibility, reducing the need for specialized single-purpose machines and maximizing your return on investment.
-
Longer Equipment Lifespan: High-quality materials, robust construction, and comprehensive maintenance support ensure a longer operational lifespan for the equipment, deferring capital expenditure on replacements.
Selecting the appropriate Conductor Pulling Equipment is crucial for project success and varies significantly based on the type of conductor or cable and the installation method:
For Overhead Transmission Line (OHTL) Applications:
-
Conductor Type & Material:
-
Conventional (ACSR, AAAC): Requires robust pulling force and good tension control. Standard bullwheel diameters and linings are often sufficient.
-
HTLS (High-Temperature Low-Sag, e.g., ACCC, ACCR): Extremely sensitive to bending and crushing. Requires pulling machines with significantly larger bullwheel diameters and ultra-low friction, non-abrasive polymer linings to protect the composite core. Precise tension control is paramount.
-
OPGW (Optical Ground Wire): Highly delicate due to internal fiber optics. Requires pullers with large bullwheel diameters, gentle, non-abrasive linings, and absolutely no torsional forces (necessitating high-quality anti-twist swivels and extremely stable pulling).
-
-
Bundle Configuration: For bundled conductors, pullers must have multi-groove bullwheels and be paired with running boards that can accommodate the specific number of conductors in the bundle while maintaining their spacing.
-
Maximum Pulling Force & Speed: Calculate based on conductor weight, span lengths, sag, and terrain. Ensure the puller's capacity safely exceeds this.
For Underground Cable Laying Applications:
-
Cable Type & Material:
-
Power Cables (MV/HV): Often large diameter, heavy, and less flexible. Requires high-capacity winches with robust drums and precise force control to navigate ducts without exceeding cable tension limits.
-
Communication Cables (Fiber Optic, Copper): Can be lighter but often more fragile. May require constant tension winches to avoid over-stressing.
-
-
Duct/Conduit Characteristics: Length of pull, number of bends, conduit diameter, and internal friction all influence the required pulling force and machine type (e.g., constant tension winch vs. caterpillar puller).
-
Accessibility & Space Constraints: Urban environments often necessitate compact, portable, or modular pulling machines that can operate in confined spaces like manholes or vaults.
-
Environmental Conditions: Consideration for water ingress, soil conditions, and temperature extremes for equipment durability and performance.
General Considerations for Both:
-
Control System: The need for automated tension/force control, digital readouts, and data logging.
-
Power Source: Diesel, hybrid, or electric, based on site availability, environmental regulations, and noise concerns.
-
After-Sales Support: Critical for maintaining uptime and ensuring the longevity of your investment.
By carefully matching the equipment's specifications and features to the specific demands of the conductor/cable type and project environment, optimal efficiency, safety, and conductor integrity can be achieved.
"Conductor Pulling Tools" are specialized handheld devices and portable accessories that work in conjunction with larger conductor pulling machines to facilitate the safe, efficient, and precise installation of wires and cables. While the pulling machine generates the main force, these tools act as the crucial interface, supporting the operation by:
-
Providing Secure Attachment: Tools like pulling grips securely connect the conductor to the pulling rope, ensuring a reliable and non-damaging link.
-
Guiding and Protecting: Accessories such as stringing blocks (for OHTL) or cable rollers (for underground) guide the conductor along its path, minimizing friction and preventing abrasion or kinking.
-
Monitoring and Control: Portable dynamometers provide real-time tension data, allowing for precise control and ensuring that critical limits are not exceeded.
-
Facilitating Connection and Termination: Specialized cutters, crimpers, and stripping tools prepare conductors for splicing, connecting, or terminating.
-
Ensuring Safety: Many tools are designed with specific safety features, such as insulation for live-line work or load-rated components to prevent failures.
These tools are indispensable for addressing the intricate details and critical points of contact during the conductor pulling process, ensuring the integrity of the conductor and the safety of the crew.
Conductor pulling grips are critical for secure and non-damaging attachment, and recent advancements have focused on enhancing their versatility, strength, and gentle handling capabilities:
-
Material Innovation for Gentle Grip: For sensitive conductors like OPGW (Optical Ground Wire) and HTLS (High-Temperature Low-Sag), grips now utilize advanced materials like high-strength aramid fibers (e.g., Kevlar) or finely woven stainless steel meshes. These materials distribute the pulling force more evenly over a larger surface area, preventing localized stress that could crush optical fibers or composite cores.
-
Adjustable Jaw/Mesh Systems: Some modern grips feature adjustable or interchangeable jaw inserts or mesh sections to accommodate a wider range of conductor diameters with a single tool, increasing versatility and reducing the number of specialized tools needed.
-
Integrated Swivels & Shoulders: Many grips now come with integrated anti-twist swivels directly incorporated into their design, providing a seamless connection to the pulling rope while effectively preventing torsional forces from damaging the conductor. "Shoulders" or reinforced leading edges protect the very end of the cable from abrasion or damage as it passes through obstacles.
-
Non-Conductive Options: For certain applications, non-conductive grips made entirely from high-strength synthetic materials are available, adding an extra layer of safety.
-
Enhanced Durability & Corrosion Resistance: Grips are increasingly made from higher-grade galvanized steel or stainless steel, with improved manufacturing processes ensuring greater longevity and resistance to corrosion in diverse environmental conditions.
-
Quick-Release Mechanisms: While maintaining a secure grip under load, some designs incorporate features for easier and quicker release after the pull is completed, improving efficiency.
These advancements ensure that pulling grips provide a reliable and safe connection for all conductor types, from robust bare cables to the most delicate optical ground wires.
Specialized "Conductor Rollers" and "Cable Guides" are vital for underground cable pulling, significantly improving efficiency and protecting expensive cables by managing friction and guiding pathways:
-
Reduced Friction: Their primary function is to minimize friction between the cable and the conduit, trench, or manhole edges. This reduces the required pulling force, lessens stress on the cable, and extends the life of the pulling equipment.
-
Smooth Navigation: Rollers and guides ensure a smooth path for the cable, especially around bends, corners, and entries/exits of conduits. This prevents kinking, abrasion, and damage to the cable jacket or internal conductors.
-
Protection from Abrasion & Crushing: Rollers are often equipped with durable, non-abrasive materials (e.g., high-density polyethylene, rubber, or specialized polymers) on their surfaces to prevent direct metal-to-cable contact, safeguarding the cable's integrity.
-
Optimized Cable Laying:
-
Straight Rollers: Used in trenches or long straight runs to keep the cable elevated and reduce drag.
-
Corner Rollers: Designed with multiple rollers or specific geometries to guide cables smoothly through sharp turns in manholes or conduits, preventing excessive sidewall pressure.
-
Conduit Mouth/Duct Entry Guides: Bell-mouth or trumpet-shaped guides are placed at the entry points of conduits to provide a smooth, flared opening, preventing the cable from snagging or rubbing against sharp edges.
-
Manhole/Vault Rollers: Specialized frames and roller configurations are used to manage cables within confined underground spaces, facilitating easy movement.
-
-
Improved Safety: By ensuring smooth cable movement and reducing the need for manual intervention in hazardous areas, these tools enhance overall site safety.
The proper selection and strategic placement of these rollers and guides are paramount for successful and damage-free underground cable installations.
"Anti-Twist Swivels" are critical "Conductor Pulling Tools" that act as a buffer between the pulling rope and the conductor/cable. Their primary role is to absorb and prevent any torsional (twisting) forces from being transferred from the pulling rope to the conductor. This is absolutely essential for:
-
Preventing Conductor Damage: Without a swivel, the pulling rope's natural tendency to twist under load can cause conductors to birdcage (unravel strands), kink, or for bundled conductors, to spiral unevenly. For OPGW (Optical Ground Wire), twisting can severely damage or break the delicate optical fibers inside.
-
Ensuring Bundle Integrity: For multi-conductor bundles, swivels ensure that each individual conductor maintains its correct relative position within the bundle, preventing unwanted rotation or entanglement.
-
Smooth Pulling Operation: By allowing free rotation, swivels contribute to a smoother, more controlled pulling process, reducing stress on both the conductor and the pulling equipment.
Maintenance Requirements for Anti-Twist Swivels:
-
Regular Inspection: Before each use, visually inspect the swivel for any signs of damage: cracks, bends, distortion, excessive wear on the eyes/shackles, or signs of rust/corrosion.
-
Functionality Check: Manually rotate the swivel to ensure it turns freely and smoothly without binding or excessive play. Any stiffness or grinding indicates a problem.
-
Lubrication: While many modern swivels feature sealed, maintenance-free bearings, some heavy-duty models may have grease fittings. If present, lubricate according to the manufacturer's recommendations using the specified type of grease.
-
Load Rating Verification: Always confirm that the swivel's Working Load Limit (WLL) is appropriate for the anticipated pulling force of the job.
-
Cleaning: Keep the swivel clean from dirt, debris, and contaminants that could interfere with its rotational mechanism.
-
Immediate Removal from Service: Any swivel showing signs of damage, restricted rotation, or suspected compromise to its integrity must be immediately removed from service, tagged, and either repaired by a qualified professional or replaced. Never attempt to use a damaged or malfunctioning swivel.