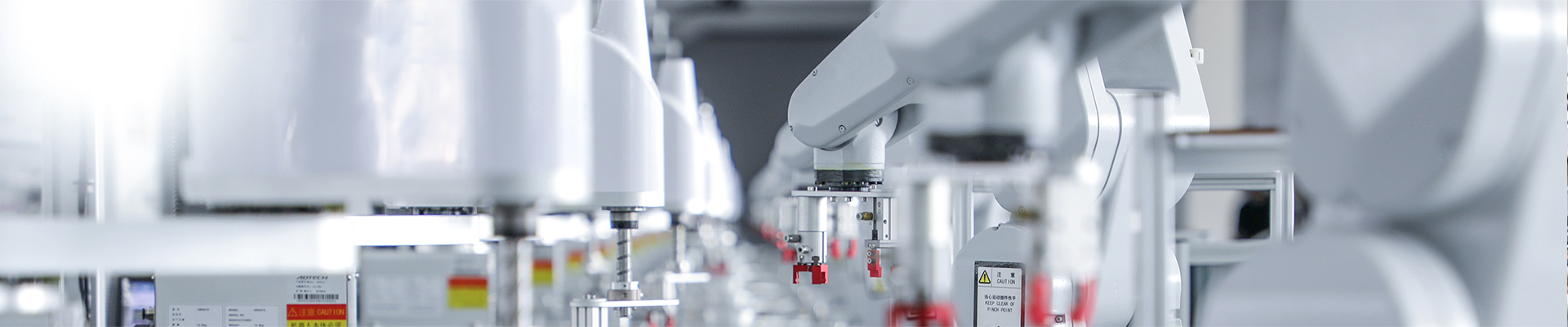
FAQ
A Conductor Stringing Machine is the core heavy equipment used in the construction and maintenance of overhead transmission lines for the precise and controlled installation of electrical conductors (wires) and ground wires. It's designed to manage the immense forces involved while preventing damage to the delicate conductors.
The primary components and their functions are:
-
Hydraulic Puller: This machine is located at one end of a stringing section. Its primary function is to pull the pilot rope (and subsequently the conductor or bundle of conductors) across the stringing blocks mounted on the towers. It precisely controls the pulling force and speed.
-
Hydraulic Tensioner: Positioned at the other end of the stringing section, the tensioner applies controlled back tension to the conductor as it is pulled. This critical function keeps the conductor elevated off the ground, preventing it from snagging on obstacles, damaging vegetation, or coming into contact with other structures, ensuring a safe and controlled sag profile.
-
Bullwheels: Large, grooved wheels (often multi-grooved for bundled conductors) on both pullers and tensioners that grip the rope or conductor to provide traction for pulling or tensioning. They are typically lined with special materials like polyurethane to prevent conductor damage.
-
Diesel Engine/Power Unit: Provides the hydraulic power to drive the bullwheels and other machine functions. Increasingly, hybrid-electric or fully electric options are emerging for quieter, lower-emission operation.
-
Control Panel: Modern machines feature advanced control panels, often with digital displays, allowing operators to precisely set and monitor parameters such as tension (kN), speed (km/h), and length of conductor pulled.
-
Reel Winders/Pay-off Devices: Integrated systems for managing the steel wire rope (pilot rope) or conductor reels, ensuring smooth and controlled pay-off and retrieval.
Together, the puller and tensioner work in synchronized tandem to perform the "tension stringing" method, which is the safest and most efficient way to install overhead conductors.
Modern Conductor Stringing Machines are engineered with advanced technologies to ensure precise tension control and prevent costly conductor damage:
-
Closed-Loop Hydraulic Systems: Our machines utilize sophisticated closed-loop hydraulic systems that automatically adjust the pulling or tensioning force in real-time. This means that once a target tension is set, the machine maintains it consistently, regardless of changes in speed or external factors like friction.
-
Electronic Tension Limiting Devices: Integrated sensors and control logic constantly monitor the actual tension. If the tension approaches a pre-set maximum limit (e.g., due to a snag or unexpected resistance), the machine automatically reduces speed or stops pulling/tensioning to prevent exceeding the conductor's safe working load.
-
Precise Bullwheel Linings: The bullwheels, which directly contact the conductor or pulling rope, are typically lined with durable, non-abrasive, and high-friction materials like polyurethane. This ensures a firm grip without damaging the conductor's outer strands or insulation.
-
Larger Bullwheel Diameters: For sensitive conductors like HTLS (High-Temperature Low-Sag) and OPGW (Optical Ground Wire), machines feature larger bullwheel diameters to reduce the bending stress on the conductor, preserving its structural integrity and internal components (like fiber optics).
-
Anti-Twist Swivel Compatibility: Conductor stringing machines work seamlessly with anti-twist swivels, which are crucial accessories installed between the pulling grip and the conductor to prevent any rotational forces from transferring to the conductor itself.
-
Smooth Start/Stop Capabilities: Advanced control systems enable extremely smooth acceleration and deceleration, preventing sudden jerks or impacts that could otherwise stress or damage the conductor.
-
Digital Readouts and Data Logging: Operators receive real-time digital readouts of tension, speed, and length. Many machines also log this data, allowing for post-operation analysis and verification of compliance with project specifications.
The latest generation of Conductor Stringing Machines incorporates several key technological innovations to significantly boost efficiency and safety:
-
Advanced Telematics & Remote Monitoring: Machines are equipped with IoT sensors that collect real-time data on performance, engine diagnostics, fuel consumption, and operational parameters (tension, speed). This data can be accessed remotely, enabling predictive maintenance, optimizing fleet management, and quick troubleshooting.
-
GPS Integration & Route Mapping: GPS capabilities allow for precise tracking of machine location and progress along the power line route. This can be integrated with project maps for better planning and coordination.
-
AI-Powered Synchronization (Puller-Tensioner): AI algorithms are increasingly used to achieve near-perfect synchronization between the puller and tensioner over long distances, ensuring consistent sag and tension profiles without constant manual adjustment.
-
User-Friendly Digital Interfaces: Modern control panels feature intuitive digital displays with clear graphics and easy-to-use controls, reducing the learning curve for operators and minimizing errors.
-
Hybrid & Electric Power Options: To meet environmental regulations and reduce operational costs, machines are increasingly offered with hybrid-electric drivetrains or as fully battery-electric units. These reduce emissions, fuel consumption, and noise levels.
-
Enhanced Diagnostics & Self-Correction: Onboard diagnostic systems can identify operational anomalies and even suggest corrective actions, allowing for faster problem resolution in the field.
-
Automated Wire Reel Handling: Innovations in reel stands and reel winders facilitate quicker and safer loading/unloading of conductor drums, streamlining the setup process.
-
Modular Design for Versatility: Machines are designed with modularity to easily adapt to different conductor sizes, bundle configurations, and project requirements, maximizing their versatility and return on investment.
Conductor Stringing Machines are specifically adapted to handle the unique properties of advanced conductors like HTLS and OPGW to prevent damage and ensure optimal performance:
-
Precise Tension Control Systems: Both HTLS and OPGW have very specific tension limits. Our machines feature extremely sensitive and accurate closed-loop hydraulic systems and electronic tension controls to maintain precise tension, preventing over-stressing of the conductor or its sensitive internal components.
-
Large-Diameter Bullwheels: To minimize bending stress on the conductor, especially crucial for OPGW's optical fibers and HTLS's composite cores, machines are equipped with bullwheels of significantly larger diameters than those used for conventional conductors.
-
Specialized Bullwheel Linings: The bullwheels are lined with very low-friction, non-abrasive, and resilient materials (such as specific polyurethane compounds) to gently cradle the conductor, preventing surface wear or crushing.
-
Slow-Speed Stringing Capabilities: For very delicate or heavy conductors, our machines can operate at extremely low, controlled speeds, allowing for meticulous placement and reducing dynamic stresses.
-
Compatibility with Specific Accessories: Our machines are designed to seamlessly integrate with OPGW-specific pulling grips (which distribute force over a wider area) and high-capacity anti-twist swivels, which are absolutely essential to prevent damage to the optical fibers.
-
Automated Load Monitoring: Continuous monitoring of pulling and tensioning forces ensures that the conductor remains within its specified mechanical limits throughout the stringing process.
Maximizing the lifespan and ensuring the utmost reliability of a Conductor Stringing Machine requires a comprehensive and rigorous maintenance regimen:
-
Adherence to Manufacturer's Schedule: Strictly follow the preventative maintenance schedule outlined in the machine's operation and maintenance manual, including daily, weekly, monthly, and annual checks.
-
Fluid Management: Regularly inspect and change hydraulic oil, engine oil, coolant, and filters (oil, fuel, air, hydraulic) according to recommended intervals. Use only manufacturer-approved fluids and filters.
-
Bullwheel and Lining Inspection: Frequently inspect bullwheel linings for wear, cracks, or grooves. Replace linings promptly if significant wear is detected to prevent conductor damage. Check bullwheel bearings for smooth rotation and excessive play.
-
Rope/Conductor Path Inspection: Ensure all guides, rollers, and contact points that the pulling rope or conductor passes through are clean, free of debris, and in good condition to prevent abrasion.
-
Hose & Connection Checks: Inspect all hydraulic hoses, lines, and connections for leaks, cracks, chafing, or signs of wear. Replace damaged hoses immediately.
-
Engine & Electrical System Checks: Perform routine checks on the engine (e.g., belts, hoses, fluid levels), battery, wiring, and control panel connections.
-
Brake System Inspection: Crucial for tensioners, regularly inspect and test the braking system components for wear and proper function.
-
Calibration of Measuring Devices: Periodically re-calibrate tension sensors and dynamometers to ensure accurate readings.
-
Cleanliness: Keep the machine clean, especially the bullwheels, hydraulic components, and control panels, to prevent accumulation of dirt and debris that can cause wear or malfunction.
-
Proper Storage: When not in use, store the machine in a clean, dry, and secure location, ideally undercover, to protect it from weather elements.
Investing in high-quality Conductor Stringing Machines significantly impacts project timelines and overall construction costs through several key benefits:
-
Accelerated Installation Speed: Tension stringing allows for much faster installation of conductors over long spans, drastically reducing the time spent on site compared to traditional methods.
-
Reduced Labor Costs: The controlled and efficient operation of these machines minimizes the need for extensive manual labor, leading to lower wage expenditures and improved crew utilization.
-
Minimized Conductor Damage & Waste: Precise tension control and specialized bullwheel linings prevent costly damage to expensive conductors. This reduces material waste, eliminates the need for re-work, and avoids delays associated with replacing damaged sections.
-
Enhanced Safety, Lower Insurance Premiums: The inherent safety of tension stringing (keeping conductors off the ground) reduces accident risks, which can translate to lower insurance premiums and fewer costly injury-related delays.
-
Optimal Sag & Tension Achievement: Machines ensure conductors are strung to exact specifications, preventing future issues like excessive sag or conductor galloping, which could lead to costly repairs or power outages down the line.
-
Versatility & Adaptability: Modern machines can handle various conductor types and bundle configurations, allowing a single investment to serve a wide range of projects, maximizing equipment utilization.
-
Predictive Maintenance (via Telematics): Integrated smart features and telematics enable proactive maintenance, minimizing unexpected breakdowns and preventing costly project delays and penalties.
-
Reduced Environmental Impact & Fines: By minimizing ground disturbance, these machines help avoid environmental damage and potential fines, contributing to a smoother, more cost-effective project execution.
A complete "Conductor Stringing Equipment" setup involves a synchronized system of specialized machinery, tools, and accessories designed for the safe and efficient installation of overhead transmission line conductors. These components work in unison to perform the tension stringing method, ensuring conductors are installed with controlled sag and tension, keeping them off the ground.
The primary components and their collaborative functions include:
-
Hydraulic Pullers: Located at one end of the stringing section, the puller uses a powerful winch system to pull a pilot rope (often a synthetic fiber rope or steel wire rope) across the stringing blocks on the towers. Once the pilot rope is across, it's used to pull the heavier conductor(s).
-
Hydraulic Tensioners: Positioned at the opposite end, the tensioner applies controlled back tension to the conductor as it's pulled. This critical function prevents the conductor from touching the ground, damaging vegetation, or impacting existing infrastructure. It ensures precise sag profiles are achieved and maintained.
-
Conductor Stringing Blocks (Travelers/Sheaves): These specialized pulleys are mounted on the transmission towers or poles. They guide the pulling rope and then the conductor smoothly along the line, minimizing friction and protecting the conductor's surface from damage.
-
Anti-Twist Swivels: Essential accessories placed between the pulling rope/grip and the conductor. They prevent torsional forces from transferring to the conductor, which is vital for maintaining conductor integrity, especially for bundled conductors or OPGW (Optical Ground Wire).
-
Conductor Pulling Grips / Running Boards: These devices securely connect the pulling rope to the conductor(s). Pulling grips are for single conductors, while running boards are designed to pull multiple conductors simultaneously in bundled configurations, ensuring even force distribution.
-
Dynamometers / Tension Meters: Precision instruments integrated into the pulling or tensioning system to provide real-time, accurate measurements of the tension being applied to the conductor. This is critical for achieving precise sag and preventing over-tensioning.
-
Reel Stands / Cable Jacks: Used at the pay-off end to safely support and control the unwinding of large, heavy conductor drums, ensuring a consistent and smooth feed into the stringing setup.
-
Pilot Wire / Anti-Twisting Steel Ropes: Used for initial stringing, often pulled by lighter equipment or drones, to establish the path for the heavier pulling rope or main conductor.
The synchronized operation of pullers and tensioners, guided by stringing blocks and monitored by dynamometers, forms the backbone of safe and efficient overhead conductor installation.
Modern Conductor Stringing Equipment is designed with numerous innovations that significantly boost efficiency and accelerate project timelines:
-
Advanced Automation & Digital Control: Integrated PLC (Programmable Logic Controller) systems and sophisticated sensors allow for precise, automated control of pulling force, tension, and speed. This reduces manual intervention, minimizes human error, and ensures consistent performance over long stringing sections.
-
Real-time Data Telemetry: Machines are equipped with IoT connectivity, transmitting real-time operational data (tension, speed, length, machine diagnostics) to operators and project managers. This enables immediate adjustments, proactive troubleshooting, and more accurate progress tracking.
-
GPS Integration & Route Optimization: GPS capabilities allow for precise tracking of equipment along the line, aiding in efficient section planning and coordination, especially for complex or remote projects.
-
High-Speed Pulling Capabilities: Our latest models offer increased pulling and stringing speeds without compromising control or safety, directly reducing the time required to complete each stringing section.
-
Modular and Adaptable Designs: Equipment is increasingly designed to be versatile, easily adapting to different conductor types, sizes, and bundle configurations. This reduces the need for specialized equipment for every job, streamlining logistics and reducing setup times.
-
Integrated Reel Management Systems: Features like automatic level winders on pullers and powered reel stands ensure smooth, consistent conductor pay-off and tidy rope winding, preventing snags and re-spooling delays.
-
Predictive Maintenance Analytics: Data collected from smart equipment feeds into analytical platforms, enabling predictive maintenance. This minimizes unexpected breakdowns, reduces costly downtime, and ensures equipment readiness.
These innovations combine to create a highly optimized stringing process, leading to faster project completion and reduced overall costs.
Safety is our top priority, and our Conductor Stringing Equipment incorporates multiple paramount safety features to protect both personnel and the valuable conductor:
-
Automatic Overload Protection: Electronic and hydraulic systems automatically monitor pulling and tensioning forces. If the pre-set maximum force is exceeded (e.g., due to an obstruction or snag), the machine will automatically slow down or stop, preventing conductor breakage or equipment damage.
-
Spring-Applied, Hydraulically-Released Brakes: On tensioners, this fail-safe braking system automatically engages if hydraulic pressure is lost, immediately holding the conductor in place and preventing uncontrolled run-away.
-
Emergency Stop Buttons: Strategically located emergency stop buttons provide immediate shutdown capability in critical situations.
-
Operator Protection Cabins/Stations: Enclosed or protected operator stations offer shielding from weather elements and potential hazards, sometimes with climate control for comfort and focus.
-
Robust Anchoring Systems: Our machines are designed with strong anchoring points, and we provide guidelines for secure anchoring to ensure stability under extreme loads.
-
Hydraulic Fault Diagnostics: Onboard diagnostic systems can alert operators to hydraulic system anomalies, allowing for proactive intervention before a critical failure occurs.
-
Bullwheel Guarding: All rotating bullwheels are fitted with robust guards to prevent accidental contact by personnel.
-
Remote Control Options: Some advanced models offer remote control capabilities, allowing operators to manage the stringing process from a safer vantage point, away from direct machinery operation.
-
Clear Digital Readouts: Real-time digital displays of tension, speed, and distance allow operators to monitor critical parameters and ensure they remain within safe operating limits.
These features, combined with proper training and adherence to safety protocols, ensure the highest level of safety on the job site.
Installing advanced conductors like HTLS (High-Temperature Low-Sag) and OPGW (Optical Ground Wire) requires specialized capabilities, and our Conductor Stringing Equipment is specifically engineered to meet these demands:
-
Ultra-Precise Tension Control: Both HTLS and OPGW are highly sensitive to tension variations. Our machines feature extremely accurate, closed-loop hydraulic systems and electronic controls that maintain very tight tolerances on set tension, preventing over-stressing that could damage composite cores (HTLS) or optical fibers (OPGW).
-
Large-Diameter Bullwheels: We utilize bullwheels with significantly larger diameters, often exceeding conventional sizes. This minimizes the bending radius the conductor experiences as it passes over the wheels, crucially protecting the delicate internal structure of OPGW and the composite core of HTLS from micro-bending or cracking.
-
Specialized, Non-Abrasive Bullwheel Linings: The bullwheels are fitted with proprietary, highly durable, and ultra-low friction linings (e.g., specific polyurethane or MC nylon compounds) that prevent any surface damage, abrasion, or crushing of these expensive and sensitive conductors.
-
Lower Pulling Force Settings at High Speeds: Our machines can achieve desired stringing speeds at lower maximum pulling forces, which is gentler on the conductor during the stringing process.
-
Compatibility with OPGW/HTLS-Specific Accessories: The equipment is designed to work seamlessly with specialized OPGW/HTLS pulling grips (which distribute force over a larger area) and high-capacity anti-twist swivels, which are non-negotiable for these conductor types.
-
Smooth Start/Stop and Variable Speed Control: The ability to achieve extremely smooth acceleration and deceleration, along with infinitely variable speed control, prevents sudden jerks or dynamic stresses on the conductors.
-
Integrated Data Logging: Real-time data logging of tension and speed allows for post-installation verification that the conductor was strung within its specified parameters, crucial for warranty and performance guarantees.
Selecting the right Conductor Stringing Equipment is crucial for project success and involves considering several critical factors:
-
Conductor Type and Size: The most important factor. Determine if you're stringing conventional ACSR, AAC, AAAC, or advanced conductors like HTLS (e.g., ACCC, ACCR) or OPGW. The conductor's diameter, material, and weight dictate the required pulling force, tension capacity, bullwheel diameter, and lining material of the machines and accessories.
-
Number of Conductors in a Bundle: For bundled conductors (e.g., 2-, 3-, or 4-bundle), you'll need machines with multi-groove bullwheels and appropriate running boards.
-
Maximum Pulling Force and Tension Capacity: Calculate the maximum expected pulling force and tension based on the conductor's weight, span lengths, sag requirements, and terrain. Ensure the selected puller and tensioner capacities exceed these requirements with a sufficient safety margin.
-
Maximum Stringing Speed: Project timelines will influence the desired stringing speed. Ensure the equipment can achieve the necessary speed while maintaining control and precision.
-
Terrain and Accessibility: Consider the operating environment. For challenging terrains (steep, muddy, remote), track-mounted pullers/tensioners or highly mobile, compact units might be necessary.
-
Power Source: Evaluate diesel, hybrid, or electric options based on local regulations, fuel availability, and environmental considerations.
-
Automation and Control Systems: Assess the level of automation, digital controls, telematics, and data logging capabilities needed for your project's complexity and reporting requirements.
-
After-Sales Support & Spare Parts: Crucially, verify the manufacturer's global after-sales service, technical support, and spare parts availability to minimize potential downtime.
-
Budget and Return on Investment (ROI): Balance initial investment costs with long-term operational efficiency, maintenance costs, and projected lifespan.
As a leading global manufacturer, we understand that exceptional after-sales support and comprehensive training are as vital as the equipment itself. We are committed to ensuring our clients achieve maximum operational efficiency and reliability worldwide:
-
Dedicated Global Technical Support: Our experienced technical support team is available via multiple channels (phone, email, online portal) to provide prompt assistance, diagnostic guidance, and troubleshooting solutions for any operational or technical issues, regardless of your location.
-
Comprehensive Training Programs: We offer tailored training courses for your operators and maintenance personnel. These programs cover detailed machine operation, safety protocols, routine preventative maintenance, advanced troubleshooting, and best practices for specific conductor types (e.g., HTLS, OPGW). Training can be conducted on-site at your facility or remotely via digital platforms.
-
Extensive Documentation: Every piece of equipment comes with detailed operation and maintenance manuals, comprehensive spare parts catalogs, hydraulic and electrical schematics, and troubleshooting guides, often available in multiple languages and digital formats for easy access.
-
Guaranteed Spare Parts Availability: We maintain a vast inventory of genuine spare parts at our main facility and leverage a robust global logistics network to ensure timely and reliable delivery of components to your project site, minimizing downtime. We prioritize the availability of critical wear-and-tear parts.
-
On-Site Field Service Engineers: For complex installations, major overhauls, or specialized diagnostic requirements, our highly skilled field service engineers are available for dispatch to your project sites around the world.
-
Warranty Support: All our Conductor Stringing Equipment is backed by a comprehensive warranty, providing peace of mind and protecting your investment against manufacturing defects.
-
Long-Term Partnership & Consultation: We aim to build lasting relationships. Our team is available for ongoing consultation and advice to help you optimize the performance of your equipment and adapt to new project challenges.
"Conductor Stringing Tools" encompass the specialized handheld devices and portable equipment that are indispensable for precise and safe conductor installation, working in conjunction with larger stringing machines. These tools are used both by ground crews and linemen working aloft on towers:
For Ground Crews:
-
Conductor Cutting Tools: Manual or hydraulic cutters designed for specific conductor sizes and types (e.g., ACSR, AAAC, OPGW) to ensure clean, precise cuts without damaging strands.
-
Conductor Crimping/Compression Tools: Hydraulic or battery-powered tools used to make secure, high-integrity connections for splices, dead-ends, and connectors on conductors. These often come with interchangeable dies for various conductor sizes and types.
-
Cable Pulling Grips / Running Boards: Crucial for attaching the pulling rope to the conductor(s). Pulling grips are for single conductors, while running boards are specialized for bundled conductors, ensuring even tension distribution.
-
Anti-Twist Swivels: Installed between the pulling grip and the pulling rope, these prevent torsional forces from transferring to the conductor, protecting it from damage, especially critical for OPGW and bundled conductors.
-
Dynamometers / Tension Meters (Portable): Handheld or integrated devices to measure and verify the actual tension on the conductor or pulling rope.
-
Reel Stands / Cable Jacks: Portable devices used to safely lift, support, and control the unwinding of conductor drums at the pay-off site.
-
Grounding Sets: Essential for establishing protective equipotential zones for worker safety by connecting conductors to earth.
-
Pilot Wire / Anti-Twisting Steel Ropes: Used for initial stringing, often lighter and designed to prevent twisting before the main conductor pull.
For Linemen on Towers:
-
Conductor Stringing Blocks (Travelers/Sheaves): Installed on tower arms, these pulley systems guide the pulling rope and conductor smoothly along the line, reducing friction and preventing abrasion.
-
Come-Along Clamps (Wire Grips): Versatile temporary clamps used to grip and hold conductors, often for tensioning or securing before permanent attachments.
-
Insulated Hand Tools: Pliers, wrenches, screwdrivers, etc., specifically rated for electrical work (e.g., VDE 1000V) to protect against accidental contact with energized components.
-
Hot Sticks (Telescopic/Sectional): Insulated tools for working on or near energized lines from a safe distance, equipped with various interchangeable heads for specific tasks.
-
Gin Poles / Hoisting Tackles: Portable lifting devices used to hoist heavy equipment or conductors onto towers.
-
Fall Protection Equipment: Harnesses, lanyards, and other safety gear that are essential for personnel working at heights.
Battery technology, particularly advanced Lithium-ion (Li-ion) systems, is a major driver of innovation in portable Conductor Stringing Tools, offering significant improvements in efficiency and ergonomics:
-
High-Power Cordless Crimpers & Cutters: Modern battery-powered hydraulic crimpers and cutters deliver comparable force to their hydraulic pump-driven counterparts, but with vastly improved portability and freedom of movement. They are essential for quick and reliable connections on conductors of various sizes.
-
Enhanced Battery Life & Fast Charging: Latest generation Li-ion batteries offer extended run-times, reducing the need for frequent battery changes. Rapid charging capabilities mean batteries can be recharged quickly during breaks, maximizing uptime.
-
Smart Battery Systems: Integrated electronics in batteries and tools communicate to optimize power delivery, monitor battery health, and prevent overheating, extending both tool and battery lifespan.
-
Lighter Weight & Better Balance: The overall design of cordless tools focuses on reducing weight and improving balance, significantly reducing operator fatigue during repetitive tasks or when working in challenging positions on towers.
-
Ergonomic Grip & Design: Tools are designed with improved ergonomics, featuring comfortable grips, reduced vibration, and intuitive controls, making them easier and safer to use for extended periods.
-
LED Work Lights: Integrated LED lights illuminate the work area, especially beneficial in low-light conditions or inside enclosures, improving precision and safety.
-
One-Key/Connected Tools: Some tools now feature Bluetooth connectivity, allowing for tool tracking, usage monitoring, and even remote disabling for security or compliance purposes.
These innovations make field operations more efficient, safer, and less physically demanding for linemen and ground crews.
Preventing damage to sensitive and expensive advanced conductors like HTLS and OPGW is paramount. Our Conductor Stringing Tools are specifically designed with features to ensure their integrity:
-
Specialized Pulling Grips / Running Boards: These tools are engineered with a longer, more flexible mesh or multi-conductor contact points to distribute the pulling force evenly over a greater surface area. This prevents localized stress points that could crush the delicate composite core of HTLS conductors or the optical fibers within OPGW.
-
Precision Crimping Dies: For crimping tools, dedicated dies are manufactured to exact tolerances for each specific HTLS or OPGW conductor type. This ensures the correct compression force is applied, creating a secure connection without deforming or damaging the conductor's internal structure.
-
High-Capacity, Low-Friction Stringing Blocks: For HTLS and OPGW, stringing blocks feature larger sheave (wheel) diameters to minimize the bending radius and reduce stress on the conductor. The sheave linings are made of ultra-low friction, non-abrasive materials (e.g., specific polyurethanes) to protect the conductor's outer strands.
-
High-Efficiency Anti-Twist Swivels: These are non-negotiable for OPGW and bundled HTLS conductors. They are designed to freely rotate under load, absorbing any torsional forces from the pulling rope and preventing them from transferring to the conductor, which could otherwise unravel bundles or damage optical fibers.
-
Controlled Tension Measurement: Accurate dynamometers and tension meters allow for precise monitoring of the forces applied during stringing, ensuring that the conductor remains within its safe working load limits at all times.
-
Smooth-Action Design: Tools are designed for smooth, controlled operation, minimizing sudden jerks or impacts that could stress conductors. This applies to manual tools, as well as powered ones with controlled acceleration/deceleration.
Consistent maintenance and rigorous inspection are critical for the reliability, safety, and longevity of Conductor Stringing Tools. Neglect can lead to failures, injuries, and costly project delays:
-
Pre-Use Inspection (Daily/Before Each Use):
-
Visual Check: Inspect for any visible damage: cracks, bends, nicks, frayed cables/ropes, loose bolts, deformation, or corrosion.
-
Functionality Check: Test all moving parts for smooth operation, ensure safety latches engage correctly, and verify that any spring mechanisms work properly.
-
Insulation Check (for insulated tools): Look for any cuts, punctures, or signs of wear on insulated handles or hot sticks.
-
-
Post-Use Cleaning & Storage:
-
Clean all tools thoroughly after each use to remove dirt, grease, moisture, and debris. For insulated tools, keep insulating surfaces meticulously clean.
-
Store tools in dry, protected environments, ideally in dedicated cases or racks to prevent physical damage and exposure to elements.
-
-
Periodic Detailed Inspection (Weekly/Monthly/Quarterly):
-
Lubrication: Lubricate moving parts (e.g., jaws of crimpers, bearings of swivels/blocks) with appropriate, non-conductive lubricants as per manufacturer guidelines.
-
Wear Parts: Inspect critical wear parts like bullwheel linings, pulling grip mesh, and crimping dies for excessive wear or damage and replace as necessary.
-
Calibration: Measuring tools like dynamometers require regular professional calibration (typically annually or bi-annually) to ensure accuracy.
-
-
Dielectric Testing (Insulated Tools): Hot sticks and insulated hand tools must undergo regular dielectric testing by certified facilities to verify their insulating integrity. This is often a regulatory requirement.
-
Load Testing: For critical load-bearing tools like pulling grips and stringing blocks, periodic load testing by qualified personnel or specialized service providers can be necessary to confirm their continued integrity.
-
Immediate Tag-Out & Repair/Replacement: Any tool showing signs of damage, excessive wear, or malfunction that could compromise its safety or effectiveness must be immediately removed from service, tagged "Do Not Use," and either professionally repaired by authorized personnel or replaced. Never attempt makeshift repairs on critical safety tools.
Conductor Stringing Tools are fundamental to achieving and maintaining compliance with stringent international safety standards, directly protecting workers and ensuring reliable line installation:
-
Live Working Safety: Insulated tools (like hot sticks and VDE-rated hand tools) are designed and tested to international standards (e.g., IEC 60900, ASTM F711) to provide electrical insulation, allowing work to be performed safely on or near energized lines when de-energization is not possible or practical.
-
Overload Prevention: Tools such as pulling grips and stringing blocks are manufactured with clearly defined Working Load Limits (WLL) and safety factors. Their proper use, combined with tension-measuring dynamometers, helps prevent overloading that could lead to tool failure, conductor breakage, or serious injury.
-
Ergonomics and Injury Prevention: Tools designed with ergonomic considerations (e.g., comfortable grips, reduced vibration in powered tools, balanced weight) comply with occupational health standards by minimizing operator fatigue and the risk of musculoskeletal disorders.
-
Fall Protection Integration: While not tools themselves, the proper rigging and use of stringing tools often depend on secure attachment points for fall protection equipment, ensuring compliance with fall safety regulations.
-
Quality and Traceability: Reputable manufacturers adhere to ISO quality management systems (e.g., ISO 9001), ensuring that tools are manufactured to consistent quality standards, are traceable, and meet material specifications, which is a core part of safety compliance.
-
Environmental Protection: Tools that facilitate tension stringing inherently minimize ground disturbance, helping projects adhere to environmental protection regulations by preventing damage to flora, fauna, and waterways.
-
Clear Markings and Documentation: Tools are typically marked with their load capacities, insulation ratings, and other critical safety information. Comprehensive user manuals provide detailed instructions on safe operation, maintenance, and limitations, supporting compliance with training requirements.
Both "Conductor Pulling Grips" and "Running Boards" are essential tools for attaching a pulling rope to a conductor during stringing operations, but they are designed for different applications:
-
Conductor Pulling Grips (also known as Wire Grips or Cable Socks):
-
Design: These typically consist of a woven steel mesh tube that tightens around a single conductor when tension is applied. They have an eye or thimble at one end for attachment to the pulling rope or swivel.
-
Application: Primarily used for stringing single conductors (e.g., a single ACSR, AAAC, or even a single OPGW). They provide a secure, self-tightening grip as pulling force increases.
-
Advantages: Simple, lightweight, cost-effective for single-conductor pulls.
-
Limitation: Not suitable for pulling multiple conductors simultaneously as part of a bundle, as they cannot ensure even tension distribution across separate conductors.
-
-
Running Boards (also known as Conductor Running Boards or Bundled Conductor Running Boards):
-
Design: These are specialized, more complex tools designed with multiple attachment points, often with individual, articulated clamps or secure pockets for each conductor in a bundle. They are rigid structures that maintain the exact spacing of the bundle while being pulled.
-
Application: Exclusively used for stringing bundled conductors (e.g., two, three, or four conductors simultaneously as a single unit). The running board ensures that each conductor in the bundle experiences the same pulling force and maintains its relative position, preventing twisting or spiraling. They are essential for efficient and safe bundle installation.
-
Advantages: Ensures even tension distribution across all conductors in a bundle, maintains bundle integrity, and significantly speeds up the installation of bundled lines. Crucial for large transmission projects.
-
Limitation: Heavier and more complex than single pulling grips; specifically designed for bundled applications.
-
In summary, if you are pulling a single conductor, a Conductor Pulling Grip is the appropriate tool. If you are installing multiple conductors as a pre-designed bundle, a Running Board is the essential tool to maintain the bundle's configuration and ensure a smooth, synchronized pull.
"Conductor Stringing Accessories" are the various supplementary components and consumables that facilitate the safe, controlled, and efficient installation of conductors during overhead transmission line construction and maintenance. While not the main machines or handheld tools, these accessories are absolutely indispensable because they:
-
Guide and Support Conductors: Without proper stringing blocks, conductors would drag on the ground, damaging both the conductor and the environment.
-
Prevent Conductor Damage: Accessories like anti-twist swivels and specialized pulling grips prevent torsional forces, abrasion, and crushing, protecting expensive conductors (especially sensitive ones like OPGW and HTLS).
-
Ensure Safety: Correctly rated and maintained accessories are critical for worker safety by managing loads, preventing uncontrolled movement, and ensuring stable rigging.
-
Maintain Precision: Dynamometers provide real-time tension data, essential for achieving the exact sag and tension specifications of the line, which impacts electrical performance and long-term reliability.
-
Enhance Efficiency: Smooth-running blocks, easy-to-use grips, and robust reel stands significantly streamline the stringing process, reducing labor and project time.
In essence, these accessories are the critical interface between the heavy equipment, the conductor, and the environment, ensuring the entire stringing operation is performed to the highest standards.
Stringing Blocks are fundamental accessories, and their performance has been vastly improved by advancements in materials science:
-
Advanced Polymer Linings: The most significant innovation lies in the sheave lining material. Modern blocks utilize high-performance polymers such as specialized polyurethanes, Ultra-High Molecular Weight Polyethylene (UHMWPE), or MC Nylon. These materials offer:
-
Extremely Low Friction: Minimizing resistance during conductor passage, which reduces pulling force requirements and stress on the conductor.
-
Superior Abrasion Resistance: Protecting the conductor's surface, especially critical for sensitive conductors like OPGW and HTLS, by preventing nicks, scratches, or wear.
-
Increased Durability: These linings have significantly longer wear lives compared to older materials, reducing replacement frequency and maintenance costs.
-
Reduced Noise: The polymer interface also contributes to quieter operation.
-
-
Lightweight High-Strength Alloys: The frames and structural components of stringing blocks are increasingly made from aerospace-grade aluminum alloys or high-tensile steel. This reduces the overall weight of the blocks, making them easier and safer for linemen to handle and install on towers, while maintaining exceptional strength and load capacity.
-
Corrosion-Resistant Coatings: Metallic components are often treated with advanced galvanization processes, powder coatings, or specialized paints that offer superior resistance to environmental factors like salt spray, humidity, and industrial pollutants, extending the block's lifespan in diverse global climates.
-
Improved Bearing Technology: Sealed, maintenance-free, and high-quality bearings (e.g., precision ball bearings or tapered roller bearings) are standard, ensuring smooth, consistent rotation and reducing the likelihood of seizing or premature failure.
These material innovations lead to more efficient, safer, and longer-lasting stringing blocks, ultimately reducing project costs and improving conductor integrity.