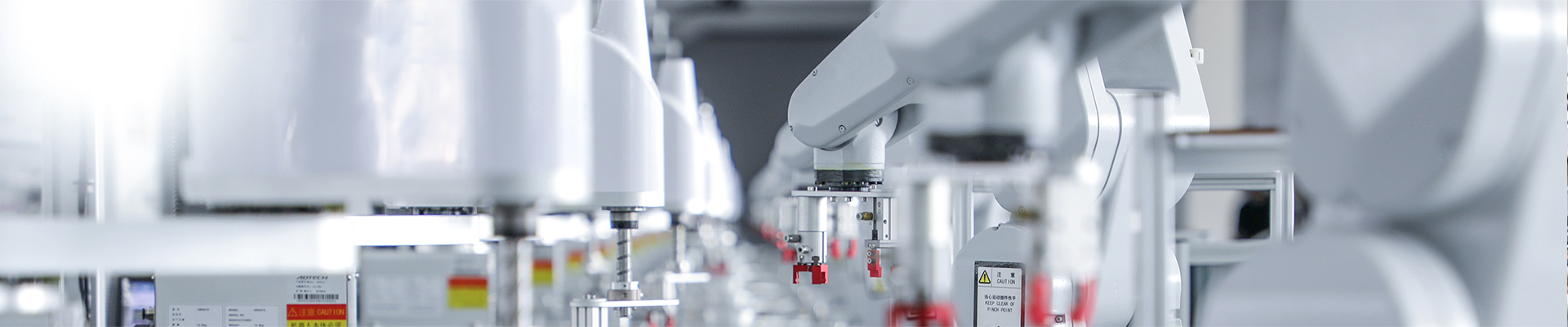
FAQ
The global transmission line equipment market is rapidly evolving, driven by several key trends:
-
Grid Modernization & Smart Grid Integration: A significant push for upgrading aging infrastructure with digital technologies, requiring equipment that can facilitate the installation of smart components, sensors, and communication systems.
-
Renewable Energy Integration: The massive growth of wind, solar, and other renewable energy sources necessitates extensive new transmission infrastructure and upgrades to connect these decentralized sources to the grid, driving demand for high-capacity and efficient stringing and laying equipment.
-
Increased Focus on Resilience & Durability: Extreme weather events and cybersecurity threats are prompting demand for equipment that helps build more resilient power lines and substations, capable of withstanding environmental stresses and ensuring operational continuity.
-
Electrification & Automation: A growing trend towards electric or hybrid-powered construction equipment to reduce emissions and noise, especially in urban or environmentally sensitive areas. Automation and remote control capabilities are also becoming standard for improved precision and safety.
-
UHV (Ultra-High Voltage) and HVDC (High-Voltage Direct Current) Projects: The need for long-distance power transmission, often from remote generation sites to consumption centers, is driving demand for specialized equipment capable of handling the heavier and larger conductors used in UHV AC and HVDC lines.
-
Predictive Maintenance & IoT Integration: Equipment increasingly incorporates IoT sensors for real-time monitoring, enabling predictive maintenance, optimizing operational efficiency, and reducing costly downtime for both stringing machines and the installed infrastructure.
Our commitment to sustainability is reflected in several aspects of our equipment:
-
Tension Stringing Expertise: Our advanced Overhead Transmission Line (OHTL) stringing equipment excels in tension stringing, which keeps conductors elevated off the ground throughout installation. This significantly minimizes environmental impact by reducing soil erosion, vegetation damage, and the overall footprint of the construction corridor.
-
Reduced Emissions: We offer machines equipped with the latest emission-compliant engines (e.g., meeting Tier 4 Final/Stage V standards), drastically reducing harmful exhaust emissions and noise pollution at construction sites. We are also actively developing and exploring hybrid and electric power options for select equipment to achieve even lower environmental impact.
-
Precision & Efficiency: Our equipment is designed for high precision and efficiency, meaning projects can be completed faster with less material waste and fewer disruptions to local ecosystems.
-
Support for Undergrounding Projects: Our comprehensive range of underground cable laying equipment facilitates the burial of power lines, which enhances aesthetics, reduces vulnerability to weather, and minimizes environmental impact above ground.
-
Durability & Longevity: By manufacturing robust and durable equipment, we contribute to a circular economy, reducing the need for frequent replacements and minimizing waste throughout the equipment's lifecycle.
High-voltage (HV) and Ultra-High Voltage (UHV) transmission lines demand specialized, high-capacity equipment due to the large, heavy conductors and extreme tensions involved. We offer:
-
Heavy-Duty Hydraulic Pullers & Tensioners: Our range includes models with significantly higher pulling and tensioning capacities, specifically designed for large diameter, heavy conductors (including bundled configurations) and very long spans common in HV and UHV projects.
-
Large Diameter Stringing Blocks: Robust stringing blocks (sheaves) with larger diameters and specialized linings to accommodate massive conductors, minimizing bending stress and protecting their integrity.
-
High-Strength Anti-Twist Ropes & Swivels: Specialized ropes with very high tensile strength and anti-twist properties, along with heavy-duty swivels, are essential for handling the immense forces and preventing damage to UHV conductors and OPGW.
-
Conductor Drum Stands with Braking Systems: Reinforced reel stands capable of supporting very large and heavy conductor drums, equipped with precise braking systems for controlled unwinding.
-
Specialized Auxiliary Equipment: This includes robust gin poles, heavy-duty conductor grips, tension meters (dynamometers) with extended ranges, and specialized safety equipment designed for UHV working environments.
-
Customization Capabilities: We also offer customized equipment solutions to meet the unique demands and complex challenges of specific UHV project requirements worldwide.
Our equipment plays a crucial role in building and maintaining power grids that are more resilient to extreme weather:
-
Precision Stringing for Optimal Sag: Our tension stringing equipment ensures conductors are installed with precise sag values, minimizing exposure to wind and ice loading, and maintaining critical ground clearances even under harsh conditions.
-
Facilitating Stronger Infrastructure: By enabling the installation of heavier, more robust conductors and components, our equipment supports the construction of lines designed to withstand higher wind speeds, ice accretion, and seismic activity.
-
Rapid Deployment & Repair: Our efficient stringing and cable laying equipment allows for faster initial construction and, critically, quicker repair and re-stringing after storm damage, significantly reducing outage durations.
-
Undergrounding Solutions: Our underground cable laying equipment provides the means to bury power lines, protecting them from direct exposure to storms, high winds, ice, and falling trees, thus enhancing grid resilience, especially in vulnerable areas.
-
Condition Monitoring (Indirectly): While our equipment builds the lines, the precision of our installation (facilitated by our machines) enables better long-term performance and reduces the likelihood of weather-induced failures that stem from initial installation deficiencies.
The choice between overhead and underground equipment depends on several project-specific factors:
-
Project Location & Environment:
-
Urban/Dense Areas: Undergrounding is often preferred for aesthetics, space constraints, and reduced vulnerability to weather, using trenchers, directional drills, and cable pullers.
-
Rural/Open Terrain: Overhead lines are typically more cost-effective and faster to install using OHTL stringing equipment.
-
Environmentally Sensitive Areas: Tension stringing for OHTL or careful undergrounding methods (like Horizontal Directional Drilling) are chosen to minimize disturbance.
-
-
Cost: Initial installation costs for underground cables are generally significantly higher than for overhead lines due to excavation, specialized equipment, and repair complexity.
-
Maintenance & Repair: Fault location and repair are more challenging and time-consuming for underground cables. Overhead lines are generally easier to inspect and repair.
-
Reliability & Resilience: Underground cables offer higher resilience against weather-related outages (storms, ice), while overhead lines are more susceptible but easier to diagnose and fix.
-
Voltage Level & Capacity: Both methods can handle various voltage levels, but specific equipment types are optimized for each.
-
Public Safety & Aesthetics: Undergrounding enhances public safety by eliminating visible wires and poles, improving visual appeal.
-
Regulatory Requirements: Local regulations, zoning laws, and environmental policies often dictate the preferred method.
Our company provides comprehensive solutions for both, allowing clients to select the optimal equipment based on their specific project needs and priorities.
Our tools and equipment for substations are designed to optimize efficiency, safety, and longevity in both construction and maintenance phases:
-
Specialized Installation Tools: We provide precision tools for the installation of large components like transformers, circuit breakers, and switchgear, ensuring correct alignment and secure connections.
-
Insulated & Safety Equipment: Our range includes essential safety tools such as insulated hot sticks, grounding equipment, and lockout/tagout (LOTO) kits, crucial for protecting personnel during live-line work or de-energized maintenance.
-
Diagnostic & Testing Equipment: Tools for routine inspection, diagnostic testing (e.g., for insulation integrity, circuit breaker timing), and condition monitoring help identify potential issues before they lead to costly failures, facilitating predictive maintenance.
-
Maintenance & Repair Tools: Specialized hand tools, hydraulic tools, and lifting equipment designed for the specific tasks involved in repairing and maintaining substation assets, improving workflow and reducing downtime.
-
Portability & Ease of Use: Many of our substation tools are designed to be portable and user-friendly, allowing technicians to perform tasks efficiently in various areas of a complex substation environment.
-
Compliance & Reliability: All our substation equipment adheres to stringent international safety and quality standards, ensuring reliable performance and operator safety in high-risk environments.
For efficient and safe OHTL work, a lineman or electrical technician relies on a comprehensive set of specialized hand tools:
-
Conductor Grips / Come-Alongs: For securely holding, pulling, and tensioning conductors during splicing, sagging, and maintenance. These vary by conductor type and size.
-
Hydraulic Cutters and Crimpers: Essential for precise cutting and strong, reliable compression splices and connections on various conductor types and sizes.
-
Insulated Hand Tools (Pliers, Wrenches, Screwdrivers): Designed with dielectric properties to protect against electrical shock when working near energized components. Certified to standards like IEC 60900.
-
Hot Sticks / Live-Line Tools: Fiberglass-reinforced insulating sticks with interchangeable heads for performing tasks on energized lines from a safe distance.
-
Grounding Sets: Temporary grounding clamps and cables for safely de-energizing lines and creating equipotential zones.
-
Voltage Detectors & Phasing Tools: Crucial for verifying the presence or absence of voltage and ensuring correct phase rotation before and during work.
-
Cable Strippers & Preparation Tools: For cleanly removing insulation and semi-conducting layers from conductors to prepare for splicing or termination.
-
Torque Wrenches: To ensure fasteners and connections are tightened to precise specifications, preventing loose connections or over-stressing components.
-
Climbing Gear (for pole/tower work): Lineman's belts, body belts, fall arrest systems, and climbing spurs, all subject to rigorous safety standards.
-
Specialized Measuring Tapes & Sagging Devices: For accurate measurement of spans, clearances, and conductor sag.
The evolution of battery technology, particularly Lithium-ion (Li-ion) and its advancements, has revolutionized portable transmission line tools:
-
Increased Power & Performance: Modern Li-ion batteries deliver higher power output, allowing tools like hydraulic crimpers and cutters to operate with greater force and speed, often matching or exceeding corded versions.
-
Extended Run-time: Improved battery capacities mean tools can run longer on a single charge, reducing downtime for battery swaps and boosting productivity.
-
Faster Charging: Quick-charge technologies enable batteries to reach significant charge levels in a fraction of the time, keeping tools ready for continuous work.
-
Reduced Weight & Ergonomics: Lighter batteries contribute to overall lighter tools, reducing operator fatigue, improving maneuverability, and enhancing safety, especially for tools used at height or for extended periods.
-
Smart Battery Technology: Many batteries now feature integrated electronics for monitoring charge status, temperature, and even tool usage, which can be connected to apps for diagnostics and asset management.
-
Interchangeability: Many manufacturers offer battery platforms where a single battery type powers a range of different tools, simplifying logistics and reducing overall equipment costs.
Safety is paramount in electrical work. When selecting transmission line hand tools, prioritize those with:
-
Insulation Ratings: For insulated hand tools, look for certifications like IEC 60900 or ASTM F1505, indicating they are tested to specific voltage ratings (e.g., 1000V). The insulation must be intact and regularly inspected.
-
Dielectric Strength: For hot sticks and live-line tools, ensure they are manufactured to standards like ASTM F711 and regularly tested for their dielectric integrity to prevent flashovers.
-
Working Load Limit (WLL) / Safe Working Load (SWL): Tools like conductor grips, hoists, and pulling accessories must clearly display their WLL, and this limit should never be exceeded. Look for supporting test certificates.
-
Ergonomics: Tools designed with comfortable, anti-slip grips and balanced weight distribution reduce operator fatigue and the risk of repetitive strain injuries.
-
Fail-Safe Mechanisms: For hydraulic tools, features like pressure relief valves prevent over-pressurization, and automatic retraction (or release) mechanisms ensure safe operation.
-
Durable Materials: High-strength, corrosion-resistant materials (e.g., forged steel, aircraft-grade aluminum, high-impact polymers) ensure tools withstand harsh environments and prolonged use without compromising safety.
-
Compliance with Local Regulations: Always ensure tools meet specific national or regional safety standards and regulations (e.g., OSHA in the US, specific national electrical codes).
Underground cable laying and maintenance require a distinct set of specialized tools:
-
Cable Pushers/Pullers: Hydraulic or electric machines (sometimes considered tools depending on scale) that guide and propel cables through conduits or trenches.
-
Cable Rollers/Conduit Rollers: Used to reduce friction and guide cables smoothly during installation in trenches or ducts.
-
Duct Rodders/Fish Tapes: Flexible rods or tapes used to pull pilot lines or smaller cables through underground conduits.
-
Cable Cutters & Strippers (Heavy-Duty): Designed for the thicker insulation and larger diameters of underground power cables.
-
Hydraulic Crimpers for Splicing/Terminating: Large-capacity crimpers for making robust, sealed connections and terminations in underground environments.
-
Manhole Hooks & Lifters: Tools for safely opening and maneuvering heavy manhole covers.
-
Pumping & Dewatering Equipment: To manage water in trenches and manholes, ensuring a dry working environment.
-
Cable Locators & Fault Finders: Electronic tools to precisely locate buried cables and identify fault points for efficient repair.
-
Ground Penetrating Radar (GPR) systems: For non-invasive detection and mapping of underground utilities before excavation.
-
Fusion Splicers (for fiber optic cables in composite power cables): Precision tools for joining optical fibers within OPGW or dedicated fiber optic cables run underground.
Conductor splicing and termination tools are continually evolving for faster, more reliable, and safer connections:
-
Smart Crimpers: Battery-powered hydraulic crimpers now feature sensors that provide feedback on crimp quality, ensuring proper pressure and form, often with data logging capabilities for quality assurance.
-
Ergonomic Designs: Tools are becoming lighter and more compact with improved handle designs to reduce operator strain and improve access in confined spaces.
-
Quick-Change Die Systems: Faster and easier swapping of crimping dies for different conductor sizes and types, improving workflow efficiency.
-
Automated Stripping Tools: Precision tools that automatically adjust to cable diameter and insulation thickness, ensuring clean, consistent cuts without damaging conductor strands.
-
Insulation Removal Aids: Tools designed for easier and safer removal of various types of cable insulation, including semi-conducting layers, for both overhead and underground cables.
-
Heat-Shrink & Cold-Shrink Installation Tools: Specialized tools and application methods for efficient and reliable installation of modern heat-shrink and cold-shrink splicing and termination kits.
-
Integrated Lighting: Many battery-powered tools now include integrated LED lighting to illuminate the work area, improving visibility in low-light conditions.
The accuracy of measuring tools is paramount for safety and quality in transmission line work. We ensure this through:
-
Factory Calibration: All new measuring tools, such as dynamometers (tension meters) and torque wrenches, are precisely calibrated at our factory before shipment, accompanied by a calibration certificate.
-
Traceability to International Standards: Our calibration processes are traceable to recognized international standards (e.g., NIST, ISO 17025 equivalent), ensuring their accuracy and reliability.
-
User Guidelines for Recalibration: We provide clear instructions on recommended recalibration intervals (typically annually, or after significant impact/overload) and proper storage to maintain accuracy.
-
Service & Support: We offer calibration services or guidance on authorized calibration centers for our tools to help clients maintain their equipment's accuracy throughout its lifespan.
-
Robust Design: Our measuring tools are built with durable components and protection features to minimize the impact of field conditions on their calibration.
-
Digital Readouts: Modern dynamometers often feature digital displays with high resolution and the ability to log readings, further enhancing precision and data integrity.
For safe and efficient tension stringing, several accessories are absolutely critical:
-
Conductor Stringing Blocks (Sheaves/Travelers): These guide the conductor along the route, installed on towers or poles. Their primary function is to minimize friction and prevent damage to the conductor, especially sensitive ones like OPGW, by using specialized linings (e.g., high-molecular polymer, aluminum alloy) and precise groove designs.
-
Anti-Twist Swivels: Installed between the pulling rope and the conductor/pulling sock, these prevent the buildup of torsional stress and twisting of conductors, particularly vital for bundled conductors and OPGW to protect their internal structure.
-
Conductor Pulling Grips / Pulling Socks / Running Boards: These ensure a secure and non-damaging connection between the pulling rope and the conductor(s). Running boards are specifically designed for bundle stringing to connect multiple sub-conductors seamlessly.
-
Dynamometers / Tension Meters: These provide real-time, accurate measurement of tension during stringing. This is indispensable for achieving precise sag profiles, preventing over-tensioning, and ensuring the mechanical integrity of the line.
-
Pilot Wire / Anti-Twisting Steel Ropes: Used for initial stringing to establish the main pulling line, especially in challenging terrains or where a light initial pull is needed before the main conductor. These accessories are not mere add-ons; they are integral components that ensure the safety of personnel, the integrity of the conductor, and the overall success of the stringing project.
Stringing blocks are designed with versatility and adaptability in mind to handle diverse conductor types:
-
Interchangeable Linings: Many high-quality stringing blocks offer interchangeable linings made from materials like high-molecular weight polyethylene (HMWPE), polyurethane, or aluminum alloy. This allows for optimal friction reduction and protection based on the conductor's outer material and sensitivity (e.g., specific linings for ACSR, AAAC, or delicate OPGW).
-
Variable Groove Sizes: Blocks come with a range of groove sizes to perfectly cradle conductors of different diameters, preventing flattening or deformation.
-
Multi-Groove / Bundle Blocks: For bundled conductors (e.g., 2, 3, 4, or more conductors per phase), specialized multi-groove stringing blocks are used. These blocks feature separate, precisely spaced grooves for each sub-conductor, ensuring they maintain their relative positions and share tension evenly during stringing, preventing clashing or damage.
-
Large Sheave Diameters: For very large or sensitive conductors (like UHV lines or OPGW), stringing blocks with significantly larger sheave (wheel) diameters are employed. A larger diameter reduces the bending radius of the conductor as it passes over the sheave, minimizing stress and potential damage.
-
Universal Mounting Options: Different frame designs and mounting mechanisms (e.g., universal hangers, swivel hooks, fixed-point attachments) allow blocks to be securely and correctly positioned on various tower types and structures, optimizing the conductor's path.
Anti-twist swivels are paramount for protecting OPGW (Optical Ground Wire) during installation due to OPGW's sensitive fiber optic core:
-
Preventing Torsional Stress: OPGW contains delicate optical fibers that are highly susceptible to damage from twisting. The anti-twist swivel is engineered to absorb and dissipate any rotational forces that can build up in the pulling rope during stringing. This ensures that these torsional stresses are not transferred to the OPGW itself.
-
Maintaining Fiber Integrity: By preventing the OPGW cable from twisting along its axis, the swivel safeguards the optical fibers within. Twisting can cause micro-bends, macro-bends, or even breaks in the fibers, leading to signal loss or complete failure of the communication link.
-
Smooth Passage: The swivel allows the pulling line and the OPGW to rotate independently, facilitating a much smoother passage of the cable through stringing blocks and over obstacles without snagging or kinking.
-
Enhancing Safety: A twisted cable can behave unpredictably, posing a safety risk to crew members. Swivels contribute to a more controlled and predictable stringing operation.
-
Optimizing Performance: Ultimately, the use of anti-twist swivels ensures that the OPGW's communication capabilities remain intact and perform optimally after installation, avoiding costly repairs or re-stringing.
Proper maintenance is crucial for the longevity, performance, and safety of stringing accessories:
-
Thorough Cleaning After Use: Remove all dirt, dust, conductor debris, grease, and any corrosive elements (especially after working in coastal or industrial areas). For stringing blocks, ensure grooves are free of material build-up.
-
Regular Inspection: Before and after each use, conduct a meticulous visual and tactile inspection. Look for:
-
Stringing Blocks: Worn or damaged linings, cracks in the frame, play in bearings, bent axles, missing safety latches.
-
Grips/Socks: Fraying, stretched mesh, worn jaws, damaged connections.
-
Swivels: Smooth rotation, no binding, excessive play, cracks in the body, worn bearings.
-
Dynamometers: Physical damage, clear display, and ensure they are within their calibration period.
-
-
Lubrication: Lubricate all moving parts, especially bearings in stringing blocks and swivels, according to the manufacturer's recommendations. Use appropriate, high-quality lubricants.
-
Proper Storage: Store accessories in a clean, dry, and organized manner. Protect them from extreme temperatures, direct sunlight, and physical damage. Store items like pulling grips flat to prevent mesh distortion.
-
Adherence to Load Limits: Never exceed the Working Load Limit (WLL) or Safe Working Load (SWL) clearly marked on accessories. Overloading causes irreversible damage and poses severe safety risks.
-
Timely Repair/Replacement: Any accessory showing signs of wear, damage, or malfunction that compromises its integrity or safety should be immediately removed from service, repaired by a qualified professional, or replaced.
-
Calibration (for measuring accessories): Dynamometers and other measuring accessories must be regularly recalibrated by certified facilities to maintain accuracy.
Conductor grips (often called pulling socks, Kellems grips, or cable stockings) vary significantly based on application and conductor type:
-
Single Eye Grips: Most common, used for pulling a single conductor. The pulling line attaches to a single loop or thimble at one end.
-
Double Eye Grips: Have an attachment loop at both ends, allowing for the pulling-in of a new conductor while simultaneously pulling out an old one, or for specific re-tensioning tasks.
-
Offset Eye Grips: Designed to provide a specific angle of pull or to bypass obstacles.
-
Open-End / Lace-Up Grips: These grips can be wrapped around the conductor and then laced up. They are ideal when the conductor end is not accessible or when repairing a section of line.
-
Heavy-Duty Multi-Weave Grips: Feature multiple layers of wire mesh for extremely high tensile strength, used for very large, heavy conductors or for pulling multiple conductors (bundle stringing).
-
Fiber Optic (OPGW/ADSS) Specific Grips: Designed with extra care to provide a gentle yet secure grip on sensitive fiber optic cables without crushing or damaging the delicate internal fibers. They often feature a longer length and finer weave.
-
Rotating Eye Grips: Include an integrated swivel to prevent twisting between the pulling line and the conductor, similar to standalone anti-twist swivels.
-
Live-Line Grips: Specifically designed for use on energized conductors, often with features for remote operation and enhanced insulation.
Each type is carefully selected based on the conductor material, diameter, pulling force required, and the specific stringing methodology.
Adhering to robust safety standards and regulatory compliance is paramount when sourcing transmission line accessories. Key considerations include:
-
Working Load Limit (WLL) / Safe Working Load (SWL): Every accessory designed for pulling or lifting must be clearly marked with its WLL, often with a minimum safety factor (e.g., 3:1 or 5:1). This is non-negotiable for safety.
-
ISO 9001 Certification: Ensures the manufacturer has a robust quality management system in place for consistent product quality.
-
CE Marking (for European markets): Indicates compliance with relevant EU safety, health, and environmental protection directives.
-
ASTM International Standards: Many accessories have specific ASTM standards governing their design, materials, manufacturing, and testing (e.g., for conductor grips, stringing blocks, hot sticks, and insulated tools).
-
ANSI (American National Standards Institute) Standards: Relevant ANSI standards apply to various tools and accessories, particularly for electrical safety and performance.
-
IEC (International Electrotechnical Commission) Standards: Crucial for electrical safety, especially for insulated tools (e.g., IEC 60900 for 1000V insulated hand tools).
-
Material Certifications: Verification that raw materials (e.g., steel, aluminum alloys, polymers) meet specified strength, durability, and corrosion resistance standards.
-
Traceability: The ability to trace the manufacturing batch, materials, and test results for critical accessories.
-
Compliance with Local Regulations: Always ensure accessories comply with specific national or regional safety regulations and industry best practices in the destination country. We provide full documentation and certifications for all our accessories, ensuring peace of mind regarding quality and safety.
Environmental factors significantly influence accessory performance and material selection:
-
Extreme Temperatures:
-
Heat: High temperatures can affect the performance of polymer linings in stringing blocks (causing softening or accelerated wear), lubricants, and battery life in powered accessories. Materials must retain their strength at elevated temperatures.
-
Cold: Low temperatures can make materials brittle (e.g., certain plastics or steels), reduce the flexibility of ropes and cables, and impact hydraulic fluid viscosity. Accessories must be able to withstand thermal cycling without degradation.
-
-
Corrosive Atmospheres:
-
Coastal/Salty Environments: Require highly corrosion-resistant materials like galvanized steel, stainless steel, or specialized protective coatings for all metallic components (frames, bolts, pins) to prevent rust and maintain structural integrity.
-
Industrial/Polluted Areas: Exposure to chemicals, acids, or industrial particulates necessitates materials resistant to specific chemical degradation.
-
-
UV Radiation: Prolonged exposure to sunlight can degrade certain plastic or polymer components, causing them to become brittle or discolored. UV-stabilized materials are essential.
-
Dust/Abrasives: Fine particulate matter can accelerate wear on moving parts (bearings, sheaves) and clog mechanisms. Sealed bearings and robust housing designs are crucial.
-
Humidity/Rain: Requires waterproof sealing for electronic components and corrosion protection for all exposed metal parts to prevent rust and electrical shorts.
Our accessories are engineered and tested to perform reliably across a wide range of global climatic conditions, with material selections specifically chosen for their resilience against these environmental challenges.
The power lines stringing machine sector has seen rapid innovation in 2024-2025, driven by demands for efficiency, safety, and reduced environmental impact. Key advancements include:
-
Enhanced Automation and AI Integration: Machines now feature more sophisticated control systems that can automate precise tension and speed control, reducing operator fatigue and increasing accuracy. AI algorithms are being explored for predictive maintenance, optimizing stringing parameters, and even obstacle avoidance.
-
Electrification and Hybrid Power Systems: There's a strong push towards more sustainable solutions. While robust diesel engines remain common for heavy-duty applications, we are seeing the emergence of hybrid-electric and even fully battery-electric stringing machines. These offer reduced emissions, lower noise levels, and sometimes even regenerative braking capabilities, especially beneficial in urban or environmentally sensitive areas.
-
Advanced Telematics and IoT Connectivity: Real-time data logging, remote monitoring, and GPS integration are becoming standard. This allows for centralized oversight of machine performance, location tracking, proactive diagnostics, and optimized fleet management from anywhere in the world.
-
Wireless Control and Communication: New systems are enabling wireless communication between pullers and tensioners, and offering remote-control capabilities for safer and more efficient operation, allowing operators to position themselves optimally.
-
Modular and Multi-Functional Designs: Machines are increasingly designed with modular components for easier transportation, rapid setup, and greater adaptability to various project types and terrains, including quick-change bullwheel configurations for different conductor types.