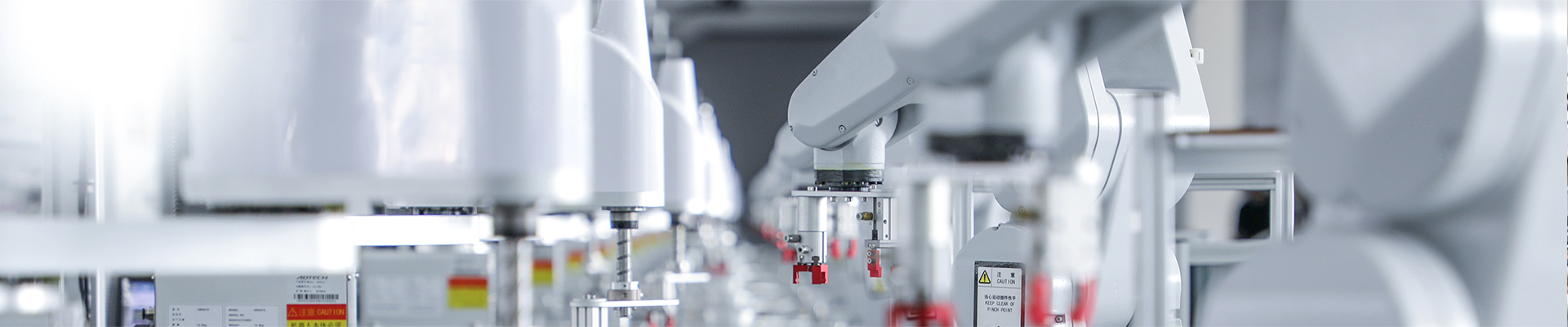
FAQ
Safety and conductor integrity are paramount. Modern power lines stringing machines incorporate numerous features to ensure both:
-
Precise Hydraulic Control: Offers incredibly smooth and infinitely variable control over pulling force and tension. This prevents sudden jerks, over-tensioning, or slack, which can damage conductors or endanger personnel.
-
Automated Overload Protection: Integrated sensors and software continuously monitor tension and pull force. If pre-set limits are exceeded, the machine automatically adjusts speed or safely stops, protecting both the conductor and the equipment.
-
Fail-Safe Braking Systems: Robust, often multiple, braking systems (e.g., negative hydraulic brakes, disc brakes) automatically engage in case of power loss or emergency stops, securely holding the conductor in place.
-
Remote Control Capability: Many machines offer wired or wireless remote control, allowing operators to manage stringing operations from a safer vantage point with enhanced visibility of the entire stringing path.
-
Bullwheel Design and Material: Bullwheels (or capstans) are designed with large diameters to minimize bending stress on conductors and are lined with non-abrasive, high-friction materials (e.g., specialized rubber, polyurethane) to grip securely without causing surface damage.
-
Synchronized Operation: When pullers and tensioners are used together, modern machines are designed for synchronized control, ensuring consistent tension across the entire span and preventing differential speeds that could lead to conductor snags or damage.
-
Safety Guards and Emergency Stops: Prominent emergency stop buttons, protective guarding around moving parts, and clear safety markings are standard.
Yes, our Power Lines Stringing Machines are specifically engineered to handle the unique characteristics of the latest generation of HTLS (High-Temperature Low-Sag) and composite core conductors. These conductors are increasingly used for re-conductoring and new line projects due to their higher current carrying capacity and reduced sag. Our machines accommodate these advanced conductors through:
-
Precise Tension Control: HTLS conductors often have different thermal and mechanical properties, requiring extremely accurate tensioning to achieve the desired sag profile without overstressing the sensitive core. Our hydraulic systems provide this precise control.
-
Specialized Bullwheel Linings: We utilize bullwheel linings made from materials that offer optimal grip and minimal abrasion, crucial for composite core conductors which can be more susceptible to surface damage than traditional aluminum conductors.
-
Larger Bullwheel Diameters: For very large diameter HTLS conductors, machines are equipped with bullwheels of increased diameter to ensure a gentler bending radius, protecting the conductor's internal structure and preventing deformation.
-
Compatibility with Specialized Accessories: Our machines seamlessly integrate with specialized conductor grips, anti-twist swivels, and running boards designed specifically for HTLS and composite core conductors, ensuring a secure and safe stringing process.
Regular and meticulous maintenance is critical for the long operational life and reliable performance of power lines stringing machines:
-
Adhere to Manufacturer's Schedule: Strictly follow the maintenance schedule outlined in the machine's operation and maintenance manual, including daily checks, weekly inspections, and periodic major servicing.
-
Hydraulic System Care: Regularly check hydraulic fluid levels and quality, replace hydraulic filters promptly, and inspect all hoses, fittings, and cylinders for leaks or damage. Use only recommended hydraulic fluid types.
-
Engine Maintenance: Perform routine engine oil and filter changes, air filter inspections/replacements, and fuel filter maintenance. Monitor engine performance and address any unusual noises or warning lights immediately.
-
Bullwheel/Capstan Inspection: Daily inspection for wear, damage, or degradation of the lining material. Any grooves, nicks, or foreign material can damage conductors. Replace linings as needed.
-
Braking System Checks: Regularly inspect and test all braking components, including disc brakes, calipers, and emergency brake mechanisms, to ensure optimal stopping power and safety.
-
Lubrication: Consistently lubricate all grease points and moving parts (e.g., bearings, pivot points) with the recommended lubricants.
-
Structural Integrity: Periodically inspect the machine frame, chassis, and attachment points for cracks, corrosion, or deformation. Ensure all bolts and fasteners are tightened to specification.
-
Calibration: Periodically calibrate load cells, dynamometers, and control systems to ensure accurate readings for tension, speed, and length.
-
Cleanliness & Storage: Keep the machine clean, especially control panels and hydraulic components. Store the machine under cover when not in use to protect it from harsh weather.
Modern power lines stringing machines significantly reduce project timelines and operational costs through:
-
Increased Efficiency and Speed: These machines can string conductors much faster and across longer spans than manual methods, drastically cutting down project duration.
-
Reduced Labor Requirements: Automation and precision control reduce the number of personnel needed for stringing operations, leading to lower labor costs.
-
Minimized Conductor Damage: Precise tension control and specialized bullwheels prevent conductors from touching the ground or being otherwise damaged, avoiding costly repairs, replacements, and project delays.
-
Optimized Resource Utilization: Features like real-time data logging and telematics enable better planning, resource allocation, and predictive maintenance, minimizing unplanned downtime and maximizing machine utilization.
-
Enhanced Safety: By reducing manual handling risks and incorporating advanced safety features, the incidence of accidents is lowered, which translates to fewer medical costs, insurance claims, and project stoppages.
-
Versatility: Machines capable of handling various conductor types, bundle configurations, and both overhead and sometimes underground applications (for pullers) offer greater flexibility and return on investment.
-
Fuel Efficiency (for diesel/hybrid models): Newer engine technologies are more fuel-efficient, leading to lower operating expenses over the project's lifetime.
For mountainous or challenging terrains, specialized design features in power lines stringing machines are crucial:
-
Track-Mounted Systems: Instead of traditional wheels, track-mounted pullers and tensioners offer superior traction, stability, and maneuverability on steep slopes, soft ground, or uneven rocky terrain.
-
Remote Control & Autonomous Features: Allows operators to control machines from a safe distance or vantage point, particularly useful when visibility is limited or terrain is hazardous. Early autonomous features are emerging for specific tasks.
-
High Ground Clearance: Machines designed with elevated chassis prevent damage from obstacles and allow them to traverse rougher terrain more easily.
-
Powerful Winches & Auxiliary Systems: Additional winches or auxiliary pulling systems for self-recovery or for aiding in positioning on inclines.
-
Compact Design: While still powerful, some machines are designed with a more compact footprint for easier transportation and operation in confined or difficult-to-access areas.
-
Integrated Leveling Systems: Automatic or manual leveling systems ensure the machine remains stable and operates efficiently on inclines, preventing undue stress on components.
-
Helicopter Stringing Compatibility: Our machines are designed to seamlessly integrate with helicopter-assisted pilot line stringing methods, which are often the only feasible option for conductor installation in extremely remote or inaccessible mountainous regions.
"Power Lines Stringing Equipment" refers to the specialized machinery and integrated systems specifically designed for the safe, efficient, and precise installation of overhead power line conductors (wires) and ground wires onto transmission towers or utility poles. The primary functions of this equipment are:
-
Pulling: Hydraulic pullers generate controlled force to draw pilot ropes, and subsequently conductors (single or bundled), across spans between towers.
-
Tensioning: Hydraulic tensioners apply continuous, controlled back tension to the conductor as it's being pulled. This crucial function keeps the conductor elevated off the ground, preventing damage from abrasion, snags, and contamination, while also ensuring the correct sag profile is achieved.
-
Controlling: Advanced control systems manage speed, tension, and length, often with real-time feedback, ensuring synchronization between pulling and tensioning units for optimal conductor installation.
-
Managing Reels: Integrated or auxiliary reel stands are used to safely manage and unwind large drums of conductor, ensuring smooth feeding into the stringing process.
Essentially, this equipment forms the backbone of modern overhead power line construction, enabling high-quality, safe, and rapid deployment of transmission infrastructure.
Smart technology is rapidly transforming power lines stringing equipment, enhancing efficiency, safety, and data insights:
-
Real-time Data Monitoring: Integrated sensors provide live data on pulling force, tension, speed, and length, displayed on intuitive digital interfaces. This allows operators to make immediate adjustments for optimal performance and quality.
-
Telematics and GPS Tracking: Equipment is increasingly equipped with telematics systems that allow remote monitoring of location, operational status, performance metrics, and maintenance alerts. This facilitates efficient fleet management, asset tracking, and proactive troubleshooting.
-
Automated Control Systems: Advanced Programmable Logic Controllers (PLCs) and algorithms enable more automated and precise control over tension and speed, often with self-adjusting capabilities to maintain consistent parameters even with varying conditions.
-
Wireless Synchronization: Pullers and tensioners can communicate wirelessly, ensuring perfect synchronization across long stringing sections, minimizing human error and maximizing conductor integrity.
-
Predictive Maintenance: Data collected from sensors can be analyzed to predict potential component failures, allowing for proactive maintenance scheduling, reducing unplanned downtime, and extending equipment lifespan.
-
Remote Diagnostics: Manufacturers can often access machine diagnostics remotely, providing faster and more accurate technical support.
-
Integration with Project Management Software: Data generated by stringing equipment can be integrated into broader project management platforms for progress tracking, quality assurance, and reporting.
Bundle conductor stringing, which involves installing multiple sub-conductors (typically 2, 3, 4, or more) per phase, requires specialized capabilities. Our power lines stringing equipment handles this effectively through:
-
Multi-Grooved Bullwheels: Both our pullers and tensioners are fitted with bullwheels featuring multiple, precisely designed grooves. Each groove cradles a sub-conductor of the bundle, ensuring even tension distribution and preventing individual conductors from rubbing or damaging each other.
-
High-Capacity Design: Our machines possess sufficient pulling force and tension capacity to manage the combined weight and friction of multiple conductors over long spans, ensuring smooth and uninterrupted stringing.
-
Synchronized Control: The advanced hydraulic and control systems ensure that tension is applied uniformly across all sub-conductors in the bundle, preventing twisting, snags, or uneven sag development.
-
Compatibility with Running Boards: Our equipment is designed to seamlessly integrate with specialized running boards, which are multi-conductor pulling grips that connect all sub-conductors of a bundle to the pulling rope, ensuring they are pulled together as a single unit.
-
Adjustable Tensioners: Our tensioners often feature independent tensioning capabilities per sub-conductor within the bundle setup, allowing for fine-tuning to achieve perfect balance and sag.
Modern power lines stringing equipment offers significant environmental benefits, aligning with sustainable construction practices:
-
Reduced Ground Disturbance (Tension Stringing): The core advantage of tension stringing, facilitated by our equipment, is keeping the conductor elevated above the ground throughout the entire installation process. This drastically minimizes disturbance to vegetation, soil erosion, and sensitive ecosystems within the right-of-way.
-
Lower Emissions: Our latest machines are equipped with advanced diesel engines that comply with stringent international emission standards (e.g., Tier 4 Final/Stage V), significantly reducing harmful particulate matter and nitrogen oxide emissions. We are also actively developing and exploring hybrid and electric power options to further lower carbon footprints and noise pollution.
-
Minimized Waste: Precise control and reduced conductor damage during stringing lead to less material waste.
-
Efficient Fuel Consumption: Continuous improvements in engine and hydraulic system design lead to better fuel efficiency, lowering overall energy consumption for projects.
-
Support for Environmentally Sensitive Areas: For projects in protected natural areas, our equipment enables controlled and precise operations, minimizing impact compared to traditional methods that might involve more extensive clearing or manual handling.
We are committed to ensuring our clients achieve maximum operational efficiency, safety, and longevity from our power lines stringing equipment. Our comprehensive support includes:
-
Operator Training Programs: We offer detailed training sessions, which can be conducted on-site or remotely, covering machine setup, safe operation protocols, optimal stringing techniques, troubleshooting common issues, and emergency procedures.
-
Maintenance Training: Specialized workshops are provided for client maintenance teams, focusing on routine and preventive maintenance, hydraulic system diagnostics, engine care, electrical system checks, and efficient component replacement.
-
Comprehensive Documentation: Every machine comes with extensive operation and maintenance manuals, parts catalogs, and troubleshooting guides, often available in multiple languages and digital formats.
-
Dedicated Technical Support Hotline: Our experienced technical support team is available to provide timely assistance for operational queries, troubleshooting, and urgent technical issues.
-
Global Spare Parts Supply: We maintain a robust inventory of genuine spare parts and have established efficient global logistics to ensure quick and reliable delivery, minimizing machine downtime.
-
On-Site Field Service: For complex commissioning, major repairs, or specialized technical assistance, our highly skilled service engineers can be dispatched to client locations worldwide.
Our power lines stringing equipment is engineered for robust performance across diverse and challenging global terrains:
-
Track-Mounted Options: For soft, marshy, or highly uneven ground (like swamps or desert dunes), we offer track-mounted pullers and tensioners. These provide superior flotation, stability, and traction compared to wheeled counterparts, significantly reducing ground pressure.
-
High Ground Clearance: Machines are designed with ample ground clearance to navigate rough terrain, large rocks, and obstacles without damage to undercarriage components.
-
Robust Chassis & Suspension: Heavy-duty, reinforced chassis and specialized suspension systems ensure durability and stability even when operating on inclines or vibrating terrain.
-
Engine Performance at Altitude: Engines are selected and configured to maintain optimal performance and power output even at high altitudes where oxygen levels are lower.
-
Environmental Sealing: Critical components, especially electrical and hydraulic systems, are protected with high IP (Ingress Protection) ratings to prevent the ingress of dust, sand, water, and mud, common in these harsh environments.
-
Specialized Traction Systems: Advanced drive systems provide excellent grip and control on various surfaces, from loose sand to muddy conditions.
-
Designed for Transportability: Many larger machines feature modular designs or specialized transport frames to facilitate breakdown and transport to remote or difficult-to-access sites.
For efficient and safe power lines stringing, a well-equipped crew relies on a suite of essential specialized tools beyond the main machines:
-
Conductor Grips / Pulling Socks (Kellems Grips): Crucial for securely attaching the pulling rope to the conductor without damaging its surface, available in various sizes and designs for single, bundled, or specialized conductors (e.g., OPGW).
-
Anti-Twist Swivels: Installed between the pulling grip and the rope, these prevent any rotational forces from transferring to the conductor, protecting its structural integrity, especially vital for bundled conductors and fiber optic ground wire (OPGW).
-
Conductor Stringing Blocks (Sheaves/Travelers): These pulley-like devices are mounted on towers to guide the conductor along the route, minimizing friction and preventing abrasion. They come with various linings (e.g., polyurethane, aluminum alloy) to suit different conductor materials.
-
Dynamometers / Tension Meters: Precision instruments used to measure the exact tension applied to the conductor during stringing, ensuring the correct sag is achieved according to design specifications.
-
Pilot Wire / Anti-Twisting Steel Ropes: Used for the initial pull-in before the main conductor, these specialized ropes are lightweight yet strong.
-
Hydraulic Crimpers and Cutters (Portable): Essential for precise cutting of conductors and creating secure, high-integrity compression splices and terminations in the field.
-
Conductor Benders/Straighteners: Tools used to correct minor bends or kinks in conductors, ensuring smooth passage through stringing blocks and proper final sag.
-
Cable Rollers / Duct Rollers (for underground transitions): Though primarily for underground, these are crucial where overhead lines transition to underground cables, ensuring smooth cable movement into conduits.
-
Reel Stands / Cable Jacks: Used to safely support and manage large drums of conductor at the pay-off end, ensuring controlled and consistent unwinding.
These tools are specifically designed to complement stringing machines, ensuring the highest quality of installation.
Recent breakthroughs in battery technology, particularly advanced Lithium-ion (Li-ion) systems, have dramatically enhanced the functionality and portability of power lines stringing tools:
-
Increased Power Output: Modern Li-ion batteries deliver significantly higher power, enabling tools like hydraulic crimpers, cutters, and even portable winches to operate with greater force and speed, often rivaling traditional corded or gas-powered equivalents.
-
Extended Run-Time: Improved battery chemistry and energy density mean tools can operate for longer durations on a single charge, minimizing downtime for battery swaps and boosting on-site productivity.
-
Faster Charging Capabilities: Quick-charge technologies allow batteries to reach substantial charge levels in a fraction of the time, keeping crews operational.
-
Reduced Weight & Enhanced Ergonomics: Lighter battery packs contribute to overall lighter tools, significantly reducing operator fatigue, improving maneuverability, and enhancing safety, especially when working at height or in challenging positions.
-
Smart Battery Management: Many new batteries feature integrated electronics that monitor charge status, temperature, and usage patterns. This data can be accessed via apps for diagnostics, predictive maintenance, and optimizing battery life.
-
Universal Battery Platforms: Manufacturers are increasingly offering battery platforms where a single battery type can power a wide range of different tools, simplifying logistics, reducing the number of chargers needed, and lowering overall equipment investment.
Working with HTLS and composite core conductors, which are increasingly adopted for their efficiency, requires specialized tools to protect their unique properties:
-
Precision Conductor Grips: These grips are engineered with specific jaw designs and materials that provide a secure, non-damaging hold on the outer strands of HTLS and composite conductors, preventing crushing or distortion of the sensitive core.
-
Specialized Stringing Blocks with Advanced Linings: Stringing blocks used for these conductors feature linings made from very low-friction, non-abrasive, and often softer materials (e.g., highly optimized polyurethane or HMWPE) to prevent any surface damage or wear during passage.
-
Larger Diameter Stringing Blocks: To minimize the bending stress on the conductor's composite core, blocks with significantly larger sheave diameters are employed, ensuring a gentle bend radius.
-
Ultra-Sensitive Dynamometers: Given the specific tension requirements of HTLS conductors, highly accurate and responsive dynamometers are used to ensure precise sag and tension control.
-
Non-Conductive Anti-Twist Swivels: For conductors that might incorporate internal optical fibers (like OPGW which often uses HTLS technology), swivels are paramount to prevent any torsional stress transfer.
-
Dedicated Splicing and Termination Tooling: Tools for splicing and terminating HTLS conductors are highly specialized, often involving cold-shrink or specific compression techniques tailored to the composite core, demanding precision crimpers and preparation tools.
-
Infrared Thermometers/Thermal Cameras: While not solely stringing tools, these are crucial during and after installation for monitoring the temperature of HTLS conductors under load, ensuring they operate within design parameters.
Safety is non-negotiable in power line work. When selecting stringing tools, prioritize those with:
-
Insulation Ratings & Testing: For any tool used near energized lines, look for clear markings of insulation ratings (e.g., 1000V, 10,000V) and certifications like IEC 60900 or ASTM F1505. These indicate rigorous dielectric testing.
-
Working Load Limit (WLL) / Safe Working Load (SWL): All pulling, lifting, or tensioning tools (grips, swivels, blocks, hoist) must have a clearly marked WLL, and this limit should never be exceeded. Verify supporting test certificates.
-
Fail-Safe Mechanisms: For hydraulic or mechanical tools, look for features like pressure relief valves, automatic braking on hoists, or non-spring-loaded designs for hot stick applications to prevent unintended operation or overload.
-
Ergonomics and Anti-Slip Grips: Tools designed for comfortable and secure handling reduce operator fatigue and the risk of slips, especially critical when working at height or in adverse weather.
-
Durable, High-Visibility Materials: Tools should be constructed from robust, corrosion-resistant materials (e.g., alloy steel, high-grade aluminum, impact-resistant polymers) and often feature high-visibility colors for easy identification and safety on site.
-
Compliance with Global/Local Standards: Ensure tools meet relevant international standards (e.g., ANSI, OSHA, CE marking for Europe) and any specific national or regional safety regulations applicable to your operational areas.
-
Traceability and Quality Control: Reputable manufacturers provide traceability for their tools, indicating quality control measures and testing at each production stage.
Proper care significantly extends the life and ensures the safe performance of stringing tools:
-
Pre-Use and Post-Use Inspection: Every tool should be visually and functionally inspected before and after each use. Look for wear, cracks, deformation, sharp edges, corrosion, or any signs of damage. Pay close attention to critical components like jaws on grips, sheave linings on blocks, and locking mechanisms.
-
Regular Cleaning: Remove all dirt, debris, grease, and any corrosive substances (especially after use in harsh environments like coastal areas or dusty regions). For tools with moving parts, ensure they are free of foreign material.
-
Proper Lubrication: Lubricate all moving parts, bearings (in stringing blocks and swivels), and pivot points according to the manufacturer's recommendations using appropriate, high-quality lubricants.
-
Calibration: Measuring tools like dynamometers and torque wrenches require periodic professional calibration (typically annually or bi-annually) to maintain accuracy.
-
Protection from Overload: Always operate tools within their specified Working Load Limits (WLL). Overloading causes irreparable damage and creates extreme safety hazards.
-
Correct Storage: Store tools in a clean, dry, and organized manner. Protect them from extreme temperatures, direct sunlight, and physical impact. Store stringing blocks off the ground, and grips uncompressed to maintain their shape.
-
Timely Repair or Replacement: Any tool showing significant wear, damage, or malfunction that could compromise its safety or effectiveness must be immediately removed from service. Repair by qualified personnel or replacement is essential.
-
Training: Ensure all personnel are properly trained on the correct use, inspection, and basic maintenance procedures for each tool.
Yes, specific categories of power lines stringing tools are designed and certified for live-line (hot-line) work, allowing maintenance and construction tasks to be performed on energized lines, thus minimizing outages. However, very specific and stringent considerations apply:
-
Insulation Rating: Tools for live-line work (e.g., hot sticks, insulated crimpers, insulated wire cutters) must have extremely high dielectric strength and be certified for the specific voltage class of the line being worked on (e.g., tested to 100kV per foot for hot sticks).
-
Regular Dielectric Testing: Live-line tools (especially hot sticks) require regular dielectric testing by certified labs to ensure their insulating properties remain intact.
-
Non-Conductive Materials: Components must be made from non-conductive materials like fiberglass-reinforced plastic (FRP) and must be kept meticulously clean and dry to maintain their insulating properties.
-
Remote Operation: Many live-line stringing tools are designed for remote manipulation using hot sticks, keeping the lineman at a safe distance from the energized conductor. This includes hot-stick operable conductor grips, tie sticks, and various clamps.
-
Grounding and Bonding Equipment: Essential for creating equipotential zones when barehanding or for de-energizing sections. This equipment itself must be regularly inspected and maintained.
-
Strict Adherence to Minimum Approach Distances (MAD): All personnel and tools must strictly observe the MAD as defined by safety regulations for the specific voltage.
-
Comprehensive Training: Live-line work requires extensive, specialized training and certification for all personnel involved, covering techniques, safety protocols, and emergency procedures.
-
Environmental Conditions: Live-line work is highly sensitive to weather conditions (e.g., rain, high humidity) which can compromise insulation, making proper planning crucial.
Only tools specifically designed, tested, and certified for live-line applications should ever be used for such work.
Beyond the primary stringing machines (pullers and tensioners), a suite of specialized accessories is crucial for safe, high-quality conductor installation:
-
Conductor Stringing Blocks (Sheaves/Travelers): These are pulley-like devices mounted on transmission towers or poles to guide conductors during stringing. Their critical role is to minimize friction, ensure smooth passage, and prevent damage to the conductor surface, especially for delicate or large-diameter cables.
-
Anti-Twist Swivels: Installed between the pulling rope and the conductor/pulling grip, these accessories are designed to prevent the buildup of torsional stress and twisting within the conductor, which is vital for maintaining the structural integrity of bundled conductors and protecting the sensitive optical fibers in OPGW (Optical Ground Wire).
-
Conductor Pulling Grips / Pulling Socks / Running Boards: These secure the connection between the pulling rope and the conductor(s). They are engineered to provide a strong, non-slip grip that distributes pulling force evenly without damaging the conductor's outer strands. Running boards are specifically for pulling multiple conductors simultaneously in bundled configurations.
-
Dynamometers / Tension Meters: Precision instruments that provide real-time measurement of the tension applied to the conductor during stringing. This is indispensable for achieving precise sag profiles, preventing over-tensioning, and ensuring the mechanical integrity of the installed line.
-
Pilot Wire / Anti-Twisting Steel Ropes: Lightweight yet strong ropes used for initial stringing, often pulled by drone or helicopter, to establish the path for the heavier pulling rope or main conductor.
-
Reel Stands / Cable Jacks: Used at the pay-off end to safely support and control the unwinding of large, heavy conductor drums, ensuring a consistent and smooth feed into the stringing setup.
-
Come-Alongs / Wire Grips (Handheld): Smaller, portable grips used for temporary holding, tensioning, or repositioning conductors during splicing, sagging adjustments, or hardware installation.
Preventing damage to sensitive conductors like OPGW (Optical Ground Wire) and HTLS (High-Temperature Low-Sag) is a top priority, and accessories are specifically designed for this:
-
Specialized Sheave Linings: Stringing blocks for OPGW and HTLS conductors feature highly optimized linings. These are typically made from non-abrasive, low-friction materials such as high-molecular weight polyethylene (HMWPE), polyurethane, or specific aluminum alloys, which cradle the conductor gently, minimizing surface wear and crushing.
-
Large Sheave Diameters: For these sensitive and often large-diameter conductors, stringing blocks are designed with significantly larger sheave (wheel) diameters. A larger diameter reduces the bending radius of the conductor as it passes over the sheave, minimizing stress on the internal optical fibers (in OPGW) or the composite core (in HTLS).
-
Anti-Twist Swivels: As mentioned, these are critical for OPGW, ensuring that no rotational forces are transferred to the cable, which could otherwise damage the delicate optical fibers.
-
Precision Pulling Grips: OPGW-specific pulling grips are longer and have a finer, more flexible weave to distribute the pulling force over a greater surface area, ensuring a secure grip without localized pressure points that could crush the cable.
-
Careful Material Selection: All components that come into contact with the conductor are made from materials that will not abrade, scratch, or chemically react with the conductor's outer layer.
-
Integrated Design with Machines: The accessories are designed to work seamlessly with modern tension stringing machines, where precise control of tension and speed further reduces the risk of conductor damage.
Stringing accessories are instrumental in enhancing safety on power line construction sites in multiple ways:
-
Controlled Conductor Movement: Stringing blocks, anti-twist swivels, and pulling grips ensure that the conductor moves predictably and smoothly. This prevents sudden jerks, uncontrolled runaway, or snagging, which are major hazards for ground crews and equipment.
-
Prevention of Conductor Drop/Ground Contact: Tension stringing, facilitated by correctly chosen accessories, keeps the conductor elevated off the ground, significantly reducing the risk of accidental contact with personnel, vehicles, or obstacles. This minimizes electrocution hazards if the line becomes energized unexpectedly.
-
Accurate Load Monitoring: Dynamometers provide real-time tension readings, allowing operators to remain within safe working load limits, preventing conductor breakage due to over-tensioning, which could cause snapped lines or uncontrolled recoil.
-
Structural Integrity: Accessories like robust tower attachment devices for stringing blocks are designed to safely bear the immense forces during stringing, preventing structural failure of the temporary setup.
-
Reduced Manual Handling: By streamlining the stringing process, accessories reduce the need for manual lifting, pulling, and manipulation of heavy conductors, thereby lowering the risk of sprains, strains, and other physical injuries to workers.
-
High-Visibility Features: Many accessories are designed with bright, high-visibility colors to make them easily identifiable on a busy construction site, further improving worker awareness.
-
Compliance with Safety Standards: Reputable manufacturers design and test their accessories to meet stringent international and local safety standards (e.g., related to Working Load Limits, material strength), ensuring they perform reliably under demanding conditions.