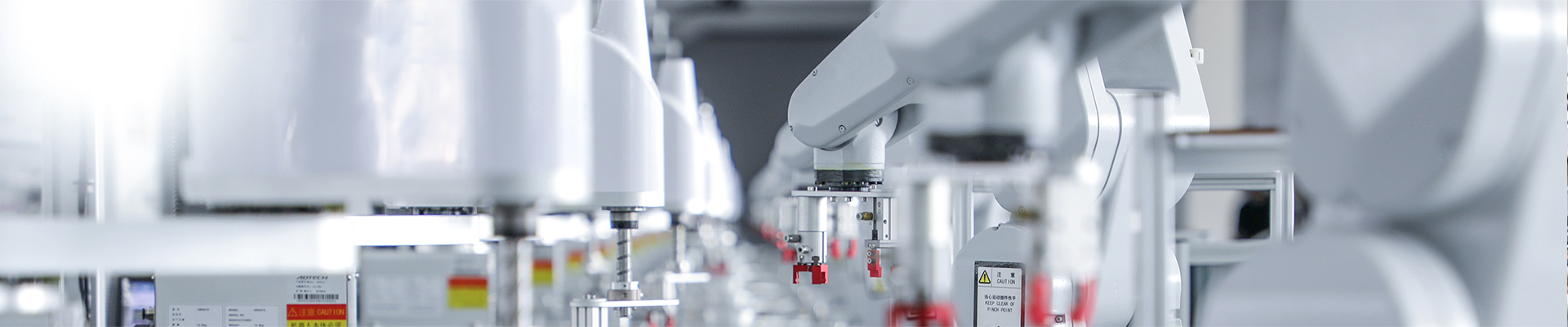
FAQ
Regular and diligent maintenance is vital for the longevity and reliable performance of stringing machines:
-
Hydraulic System Care: Regular checks of hydraulic fluid levels and quality, timely filter replacement, and inspection of hoses and connections for leaks or wear.
-
Engine Maintenance: Adherence to manufacturer's schedule for oil changes, air filter replacement, fuel filter checks, and general engine tuning.
-
Bullwheel/Capstan Inspection: Daily inspection for wear, damage, or degradation of the lining material. Any grooves or damage can lead to conductor damage.
-
Braking System Checks: Regular inspection and testing of disc brakes, calipers, and emergency brake mechanisms to ensure optimal stopping power and safety.
-
Wire Rope Inspection (if applicable): For machines using internal wire ropes, regular checks for fraying, kinks, or signs of fatigue.
-
Bearing Lubrication: Consistent lubrication of all moving parts, including bearings in bullwheels and other rotating components.
-
Structural Integrity: Periodic visual inspection of the frame, chassis, and attachment points for cracks, corrosion, or deformation.
-
Calibration: Periodic calibration of load cells, dynamometers, and control systems to ensure accurate readings for tension and pulling force. We provide comprehensive operation and maintenance manuals with all our machines, and offer training and support for optimal equipment care.
Yes, our transmission line stringing machines are designed with the versatility to handle a wide range of conductor types. Our hydraulic pullers and tensioners can be configured with bullwheel linings and groove designs specifically suited for:
-
ACSR (Aluminum Conductor Steel Reinforced): High-strength conductors with a steel core.
-
AAC (All Aluminum Conductor): Lighter, purely aluminum conductors.
-
AAAC (All Aluminum Alloy Conductor): Aluminum alloy conductors offering higher strength than AAC.
-
OPGW (Optical Ground Wire): A dual-purpose cable that combines grounding and fiber optic communication.
-
Bundle Conductors: Our machines are equipped to handle two, three, four, or even more sub-conductors simultaneously, often utilizing specialized multi-groove bullwheels and synchronized control for even tension distribution across the bundle.
The adaptability comes from adjustable settings, various bullwheel lining materials, and the precise control offered by our hydraulic systems, ensuring optimal performance and protection for each specific conductor.
Beyond the core stringing machines and hand tools, a range of specialized accessories is crucial for safe, efficient, and damage-free conductor installation. These typically include:
-
Conductor Stringing Blocks (Sheaves/Travelers): Guide the conductor along the route, installed on poles/towers.
-
Anti-Twist Swivels: Prevent torque buildup and twisting of conductors or pulling ropes.
-
Running Boards / Pulling Socks / Conductor Connectors: Used to connect multiple conductors for bundle stringing, or to connect the pulling rope to the conductor.
-
Dynamometers / Tension Meters: Crucial for real-time measurement of pulling force and tension.
-
Reel Stands / Drum Stands / Cable Jacks: Support and allow controlled unwinding of conductor reels.
-
Grounding Devices / Earthing Equipment: Essential safety accessories for temporary grounding of conductors or equipment.
-
Pilot Wire / Anti-Twisting Steel Ropes: Used for initial pulling to establish the main pulling line.
-
Sagging Boards / Sagging Tools: Aid in precisely measuring and achieving the correct conductor sag.
-
Come-Alongs / Conductor Grips: Securely hold and tension conductors for splicing or sag adjustments.
-
Temporary Mid-Span Compression Joints / Splice Sleeves: Used for joining conductors temporarily or permanently.
These accessories work in conjunction with the primary equipment to ensure the conductor is handled correctly from the reel to its final position on the tower.
Stringing blocks are critical for conductor protection through several design features:
-
Lining Material: The inner groove of our stringing blocks is lined with high-quality, non-abrasive materials such as high-molecular polymer (e.g., polyurethane, nylon), or sometimes aluminum alloy with a smooth finish. This minimizes friction and prevents scratching or damage to the conductor's outer strands, particularly vital for sensitive OPGW cables with fiber optic cores.
-
Optimal Groove Design: The groove profile is precisely designed to accommodate the conductor's diameter, ensuring a snug fit that prevents flattening or deformation. For bundled conductors, multi-groove blocks are used to cradle each sub-conductor individually.
-
High-Quality Bearings: Low-friction, sealed bearings allow the sheave to rotate smoothly and freely, reducing wear on both the conductor and the block, while minimizing the pulling tension required.
-
Robust Frame and Anti-Jump Devices: The block's frame is robust, often made of high-strength aluminum alloy or galvanized steel, and includes features like anti-jump devices or security latches to prevent the conductor from accidentally dislodging during dynamic operations.
-
Adaptability: We offer blocks with various mounting options (e.g., universal hangers, swivel hooks) to ensure correct alignment on different tower types and under various angles, further protecting the conductor by preventing kinks or undue stress.
Dynamometers (or tension meters) are indispensable monitoring accessories in OHTL stringing because they:
-
Ensure Sag Accuracy: They provide real-time, accurate readings of the tension being applied to the conductor. This is crucial for achieving the exact sag profile specified by engineering designs, which directly impacts the line's electrical performance, mechanical stability, and ground clearances.
-
Prevent Over-Tensioning: By continuously monitoring tension, they alert operators to avoid exceeding the conductor's maximum allowable tension, preventing permanent deformation, damage, or even breakage.
-
Optimize Efficiency: Knowing the precise tension allows operators to make fine adjustments to puller and tensioner speeds, optimizing the stringing process for efficiency and reducing unnecessary stress on equipment.
-
Enhance Safety: Monitoring tension helps prevent unexpected line breaks or sudden movements, which can pose significant safety risks to personnel and equipment.
-
Quality Control & Documentation: Digital dynamometers often come with data logging capabilities, providing a verifiable record of tension throughout the stringing process, essential for quality control and project documentation.
Anti-twist swivels are crucial accessories that significantly enhance safety and efficiency in complex stringing operations by:
-
Eliminating Torsional Stress: They allow the pulling rope and conductor to rotate independently. This prevents twisting forces from building up and transferring from the pulling line to the conductor itself, which is vital for maintaining the integrity of sensitive OPGW cables and preventing damage to their optical fibers.
-
Preventing Kinks and Tangling: For bundled conductors, swivels ensure that the individual sub-conductors maintain their correct orientation and do not twist around each other, which could lead to damage, uneven sag, or tangling.
-
Smoother Pulling: By absorbing rotational forces, swivels enable a much smoother and more controlled pulling operation, reducing friction, wear on equipment, and the risk of sudden jerks.
-
Enhanced Safety: A twisted or tangled conductor can be unpredictable and dangerous. Swivels reduce these risks by maintaining orderly conductor behavior throughout the stringing process.
-
Improved Efficiency: Preventing twists and snags means fewer interruptions, less need for manual intervention to untangle lines, and ultimately, a faster and more efficient stringing operation.
Recent innovations in conductor stringing accessories focus on increasing durability, performance, and operational ease:
-
Advanced Materials: Utilization of stronger, lighter, and more wear-resistant materials for stringing blocks (e.g., advanced polymer composites, high-strength aluminum alloys) and grips (e.g., heat-treated alloy steels).
-
Integrated Sensors: Some cutting-edge accessories, like smart stringing blocks or grips, may incorporate sensors to monitor parameters like tension, temperature, or even detect conductor surface conditions, feeding data back to operators or central systems.
-
Modular and Quick-Attach Designs: Accessories are increasingly designed for quicker and safer installation and removal, reducing setup times and minimizing the need for complex rigging.
-
Improved Corrosion Resistance: Enhanced coatings and material treatments (e.g., advanced galvanization, specialized paints) extend the lifespan of accessories, especially in harsh environments.
-
Ergonomic and Lighter Designs: Continuous refinement to reduce the weight of accessories without compromising strength, making them easier and safer for field personnel to handle and transport.
-
Higher Capacity & Versatility: Development of accessories capable of handling larger conductors, heavier loads, and a wider range of conductor types, making them more adaptable to diverse project requirements.
Proper care and maintenance are crucial for maximizing the lifespan, ensuring reliability, and maintaining the safety of stringing accessories:
-
Regular Cleaning: Remove dirt, dust, conductor debris, and corrosive elements after each use, especially for stringing blocks and grips.
-
Thorough Inspection: Before and after each use, inspect accessories for signs of wear, cracks, deformation, sharp edges, damaged linings (on blocks), or frayed wire ropes (on grips/pulling socks).
-
Lubrication: Lubricate moving parts (e.g., bearings in swivels and stringing blocks, pivot points on grips) with appropriate greases or oils as per manufacturer recommendations.
-
Proper Storage: Store accessories in a clean, dry environment, protected from extreme temperatures, direct sunlight, and physical damage.
-
Load Limit Adherence: Never exceed the stated Working Load Limit (WLL) or Safe Working Load (SWL) of any accessory. Overloading causes irreversible damage and poses significant safety risks.
-
Calibration: Periodically calibrate dynamometers and tension meters to ensure their accuracy.
-
Professional Servicing: For complex accessories or after heavy use, consider professional inspection and servicing by qualified technicians.
When sourcing transmission line stringing accessories, look for products that meet or exceed the following recognized certifications and standards to ensure quality, performance, and safety:
-
ISO 9001: For the manufacturer's quality management system.
-
CE Marking (for European markets): Indicates compliance with EU safety, health, and environmental protection requirements.
-
ASTM International Standards: Many accessories have specific ASTM standards covering materials, manufacturing processes, and testing (e.g., for conductor grips, wire ropes, and specific hardware).
-
ANSI (American National Standards Institute): Relevant ANSI standards may apply to certain tools and accessories.
-
IEC (International Electrotechnical Commission): Particularly for accessories that interact with electrical systems or for specific electrical safety requirements.
-
Manufacturer's Load Ratings: Ensure accessories are clearly marked with their Working Load Limit (WLL) or Safe Working Load (SWL), and that the manufacturer provides test certificates.
-
Material Certifications: For critical components, verify that the raw materials used meet specified strength and durability standards.
-
Regional Compliance: Always ensure accessories comply with specific national or regional safety regulations and industry best practices in the destination country.
In the context of Overhead Transmission Line (OHTL) construction, a "Transmission Line Machine" primarily refers to the specialized, heavy-duty, powered equipment used for the precise installation of conductors (wires) and ground wires on transmission towers. The two core types of these machines are:
-
Hydraulic Pullers: Designed to generate controlled pulling force to draw pilot ropes or actual conductors across spans.
-
Hydraulic Tensioners: Engineered to apply continuous, controlled back tension to the conductor as it's being strung, preventing it from touching the ground and ensuring proper sag.
These machines are distinct from general construction equipment due to their specialized functions, emphasis on precise tension and speed control, and their role in protecting the conductor's integrity during the complex stringing process.
Modern hydraulic transmission line machines offer significant advantages over older or conventional stringing methods:
-
Enhanced Precision & Control: Hydraulic systems provide incredibly fine control over pulling force and tension, enabling operators to achieve exact sag values and minimize conductor damage.
-
Increased Efficiency & Speed: These machines can string conductors much faster and across longer spans, significantly reducing project timelines and labor costs.
-
Superior Conductor Protection: By maintaining constant tension and utilizing specialized bullwheels, modern machines prevent conductors from dragging on the ground, minimizing scratches, nicks, and other damage that can compromise performance and lifespan.
-
Improved Safety: Features like automated braking, overload protection, remote control options, and precise speed regulation greatly reduce the risk of accidents for personnel and equipment.
-
Versatility: Capable of handling a wide range of conductor types (ACSR, AAC, AAAC, OPGW) and complex configurations like bundled conductors.
-
Data Logging & Monitoring: Many modern machines integrate technology for real-time data collection on tension, speed, and length, providing valuable insights for quality assurance and project management.
Bundle conductor stringing, involving multiple sub-conductors per phase, requires specialized machine capabilities for efficiency and integrity. Our transmission line machines handle this through:
-
Multi-Grooved Bullwheels: Our pullers and tensioners are equipped with bullwheels featuring multiple grooves, precisely designed to accommodate each sub-conductor of a bundle simultaneously. These grooves are often lined with non-abrasive, high-friction materials to grip each conductor securely without damage.
-
Synchronized Control Systems: The hydraulic systems in our pullers and tensioners work in precise synchronization to ensure that tension is applied evenly across all sub-conductors in the bundle, preventing twisting, tangling, or uneven sag.
-
Optimized Pulling Accessories: Our machines are designed to seamlessly integrate with specialized accessories like running boards and multi-conductor pulling socks, which ensure smooth connection and even pulling of the entire bundle.
-
High Capacity: Our machines are engineered with sufficient pulling force and tension capacity to manage the combined weight and friction of multiple conductors over long spans, ensuring efficient installation.
Traditionally, our heavy-duty transmission line stringing machines are powered by robust diesel engines. These engines are chosen for their reliability, high torque output, and ability to operate continuously in remote and demanding construction environments where grid power is unavailable.
Regarding environmentally friendly options, we are actively incorporating advancements:
-
Tier-Compliant Engines: Our latest models feature diesel engines that meet stringent international emission standards (e.g., Tier 4 Final/Stage V), significantly reducing particulate matter and nitrogen oxide emissions.
-
Improved Fuel Efficiency: Continuous R&D leads to more fuel-efficient hydraulic systems and engine designs, lowering fuel consumption and thus carbon footprint.
-
Exploring Hybrid/Electric Options: While full-electric large-scale stringing machines are still emerging for heavy-duty, continuous outdoor work, we are researching and developing hybrid electric models or integrating electric power for ancillary functions where feasible, particularly for smaller machines or specific use cases that prioritize noise reduction and zero emissions in urban or sensitive areas.
Our transmission line machines are engineered for robust performance in a wide range of challenging weather conditions:
-
Temperature Resilience: Components are selected and tested to perform reliably across extreme temperature ranges, from intense heat to freezing cold. This includes specialized hydraulic fluids, lubricants, and engine components.
-
Weather Sealing: Critical electrical components, control panels, and hydraulic systems are protected by high-grade weather sealing (IP-rated enclosures) to prevent water ingress from rain, snow, or humidity.
-
Corrosion Resistance: Machine frames and exposed metal parts are treated with advanced corrosion-resistant coatings or made from galvanized/stainless steel to withstand moisture, salt spray, and other corrosive elements.
-
Robust Chassis Design: The chassis and undercarriage are built for stability and durability on uneven or slippery terrain, often featuring heavy-duty tracks or high-traction tires.
-
Operator Comfort & Safety: Enclosed cabins with climate control (heating/AC) are available on larger machines to ensure operator comfort and focus, crucial for safety and efficiency in adverse conditions.
-
Enhanced Filtration Systems: Air intake and fuel systems are designed with robust filtration to protect the engine in dusty or sandy environments.
We are committed to ensuring our clients achieve maximum value and safe operation from our machines. We offer comprehensive support, including:
-
Operator Training: On-site or remote training programs conducted by our experienced technicians. These cover machine setup, operation protocols, safety procedures, troubleshooting, and best practices for various stringing scenarios.
-
Maintenance Training: Detailed sessions on routine and preventive maintenance, hydraulic system checks, engine care, and component replacement to extend machine lifespan and minimize downtime.
-
Comprehensive Manuals: Each machine comes with detailed operation and maintenance manuals, including schematics, parts lists, and troubleshooting guides.
-
Technical Support Hotline: Dedicated technical support available to address operational queries, troubleshooting assistance, and urgent issues.
-
Spare Parts Supply: We maintain a readily available inventory of genuine spare parts to ensure quick replacements and minimize project delays.
-
Field Service Support: Our team of skilled service engineers can be dispatched globally for on-site assistance, complex repairs, or specialized maintenance, whenever required.
Our modern transmission line machines are increasingly designed to integrate seamlessly into digital construction and project management workflows:
-
Data Acquisition & Export: Many machines come equipped with data logging capabilities, recording real-time parameters like tension, speed, and length. This data can be easily exported for analysis, reporting, and integration into project management software.
-
Telematics & Remote Monitoring: Select models offer telematics systems, allowing for remote monitoring of machine location, operational status, performance data, and maintenance alerts, facilitating proactive management and fleet optimization.
-
BIM (Building Information Modeling) Compatibility: While not directly producing BIM models, the precise data generated by our machines can be fed into BIM environments for accurate "as-built" documentation, progress tracking, and clash detection.
-
GPS/GNSS Integration: Allows for precise positioning and mapping of conductor routes and tower locations, enhancing accuracy and coordination with digital site plans.
-
Standardized Interfaces: Our machines are designed with industry-standard communication interfaces to facilitate integration with third-party software or other smart construction tools used on a project.
-
Digital Documentation: Beyond physical manuals, we provide digital documentation, training materials, and support resources, which are easily accessible and updatable for modern digital workflows.
The global transmission line equipment market is rapidly evolving, driven by several key trends:
-
Grid Modernization & Smart Grid Integration: A significant push for upgrading aging infrastructure with digital technologies, requiring equipment that can facilitate the installation of smart components, sensors, and communication systems.
-
Renewable Energy Integration: The massive growth of wind, solar, and other renewable energy sources necessitates extensive new transmission infrastructure and upgrades to connect these decentralized sources to the grid, driving demand for high-capacity and efficient stringing and laying equipment.
-
Increased Focus on Resilience & Durability: Extreme weather events and cybersecurity threats are prompting demand for equipment that helps build more resilient power lines and substations, capable of withstanding environmental stresses and ensuring operational continuity.
-
Electrification & Automation: A growing trend towards electric or hybrid-powered construction equipment to reduce emissions and noise, especially in urban or environmentally sensitive areas. Automation and remote control capabilities are also becoming standard for improved precision and safety.
-
UHV (Ultra-High Voltage) and HVDC (High-Voltage Direct Current) Projects: The need for long-distance power transmission, often from remote generation sites to consumption centers, is driving demand for specialized equipment capable of handling the heavier and larger conductors used in UHV AC and HVDC lines.
-
Predictive Maintenance & IoT Integration: Equipment increasingly incorporates IoT sensors for real-time monitoring, enabling predictive maintenance, optimizing operational efficiency, and reducing costly downtime for both stringing machines and the installed infrastructure.
Our commitment to sustainability is reflected in several aspects of our equipment:
-
Tension Stringing Expertise: Our advanced Overhead Transmission Line (OHTL) stringing equipment excels in tension stringing, which keeps conductors elevated off the ground throughout installation. This significantly minimizes environmental impact by reducing soil erosion, vegetation damage, and the overall footprint of the construction corridor.
-
Reduced Emissions: We offer machines equipped with the latest emission-compliant engines (e.g., meeting Tier 4 Final/Stage V standards), drastically reducing harmful exhaust emissions and noise pollution at construction sites. We are also actively developing and exploring hybrid and electric power options for select equipment to achieve even lower environmental impact.
-
Precision & Efficiency: Our equipment is designed for high precision and efficiency, meaning projects can be completed faster with less material waste and fewer disruptions to local ecosystems.
-
Support for Undergrounding Projects: Our comprehensive range of underground cable laying equipment facilitates the burial of power lines, which enhances aesthetics, reduces vulnerability to weather, and minimizes environmental impact above ground.
-
Durability & Longevity: By manufacturing robust and durable equipment, we contribute to a circular economy, reducing the need for frequent replacements and minimizing waste throughout the equipment's lifecycle.
High-voltage (HV) and Ultra-High Voltage (UHV) transmission lines demand specialized, high-capacity equipment due to the large, heavy conductors and extreme tensions involved. We offer:
-
Heavy-Duty Hydraulic Pullers & Tensioners: Our range includes models with significantly higher pulling and tensioning capacities, specifically designed for large diameter, heavy conductors (including bundled configurations) and very long spans common in HV and UHV projects.
-
Large Diameter Stringing Blocks: Robust stringing blocks (sheaves) with larger diameters and specialized linings to accommodate massive conductors, minimizing bending stress and protecting their integrity.
-
High-Strength Anti-Twist Ropes & Swivels: Specialized ropes with very high tensile strength and anti-twist properties, along with heavy-duty swivels, are essential for handling the immense forces and preventing damage to UHV conductors and OPGW.
-
Conductor Drum Stands with Braking Systems: Reinforced reel stands capable of supporting very large and heavy conductor drums, equipped with precise braking systems for controlled unwinding.
-
Specialized Auxiliary Equipment: This includes robust gin poles, heavy-duty conductor grips, tension meters (dynamometers) with extended ranges, and specialized safety equipment designed for UHV working environments.
-
Customization Capabilities: We also offer customized equipment solutions to meet the unique demands and complex challenges of specific UHV project requirements worldwide.
Our equipment plays a crucial role in building and maintaining power grids that are more resilient to extreme weather:
-
Precision Stringing for Optimal Sag: Our tension stringing equipment ensures conductors are installed with precise sag values, minimizing exposure to wind and ice loading, and maintaining critical ground clearances even under harsh conditions.
-
Facilitating Stronger Infrastructure: By enabling the installation of heavier, more robust conductors and components, our equipment supports the construction of lines designed to withstand higher wind speeds, ice accretion, and seismic activity.
-
Rapid Deployment & Repair: Our efficient stringing and cable laying equipment allows for faster initial construction and, critically, quicker repair and re-stringing after storm damage, significantly reducing outage durations.
-
Undergrounding Solutions: Our underground cable laying equipment provides the means to bury power lines, protecting them from direct exposure to storms, high winds, ice, and falling trees, thus enhancing grid resilience, especially in vulnerable areas.
-
Condition Monitoring (Indirectly): While our equipment builds the lines, the precision of our installation (facilitated by our machines) enables better long-term performance and reduces the likelihood of weather-induced failures that stem from initial installation deficiencies.