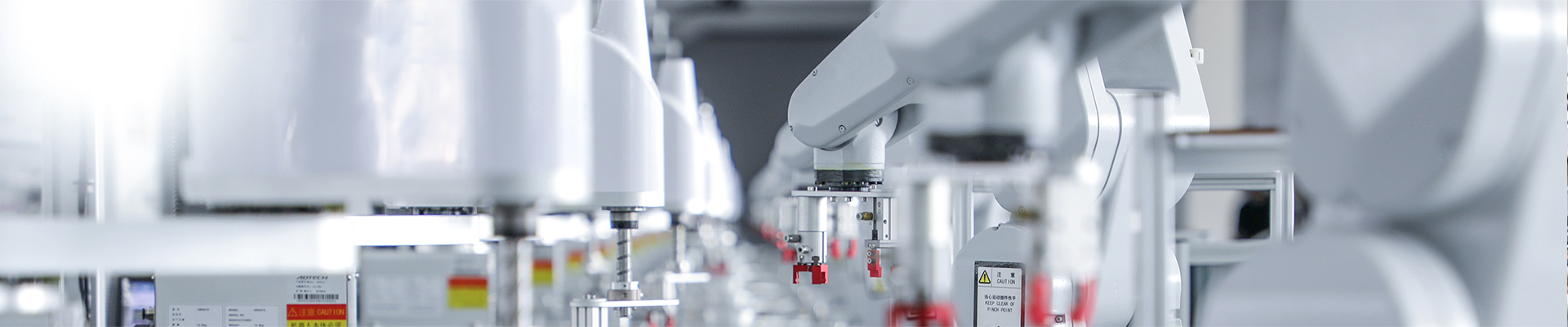
What are the key considerations for fault detection, repair, and future maintenance planning for underground cable networks?
2025-07-19Effective fault detection, efficient repair, and proactive future maintenance planning are crucial for maximizing the reliability, minimizing downtime, and extending the lifespan of underground cable networks. These considerations are often more complex than for overhead lines.
I. Fault Detection:
-
1. Common Fault Types: Underground cables are primarily susceptible to insulation breakdown (due to aging, overheating, or mechanical damage), partial discharge, and dig-ins (accidental damage during excavation).
-
2. Advanced Detection Technologies:
-
Time Domain Reflectometry (TDR) / Optical Time Domain Reflectometry (OTDR): Used for locating faults on metallic cables (TDR) and fiber optic cables (OTDR) by sending a signal and analyzing reflections. Can pinpoint faults with high accuracy.
-
Acoustic/Vibration Sensors: Increasingly deployed along cable routes or within manholes to detect abnormal sounds or vibrations indicative of partial discharge or physical stress.
-
Thermal Imaging/Distributed Temperature Sensing (DTS): Using infrared cameras or fiber optic cables embedded with the power cable to detect localized hot spots, which often precede insulation failure.
-
Partial Discharge (PD) Testing: Non-invasive tests that detect small electrical discharges that can occur in voids or defects within cable insulation, indicating impending failure.
-
Ground Penetrating Radar (GPR) & Electromagnetic Locators: Essential for accurately locating the buried cable itself before any repair excavation, preventing further damage.
-
II. Repair Strategies:
-
1. Fault Location Precision: Accurate fault location is paramount to minimize excavation, reduce repair time, and lower costs. Our equipment and services support precise fault location.
-
2. Excavation & Access: Careful excavation (often using vacuum excavation to avoid damaging adjacent utilities) to expose the damaged cable section. Providing safe working space for repair crews.
-
3. Specialized Splicing & Jointing: Repairing HV/EHV cables requires highly skilled and certified cable jointers. They use advanced, often pre-fabricated, splice kits designed for the specific cable type and voltage, ensuring a watertight and electrically robust connection. Cleanliness and environmental control (e.g., jointing shelters) are critical.
-
4. Re-testing: After repair, the repaired section (and often adjacent sections) must be thoroughly re-tested (e.g., insulation resistance, VLF testing) to verify the integrity of the new joint and the cable system.
-
5. Backfill & Restoration: Proper re-installation of thermal backfill and meticulous compaction are vital to ensure long-term thermal performance and structural integrity of the repaired section.
III. Future Maintenance Planning:
-
1. "As-Built" Documentation: Maintaining accurate and detailed "as-built" drawings and GIS records of cable routes, depths, splice locations, and conduit details. This data is invaluable for future maintenance and fault finding.
-
2. Preventative Maintenance (PM):
-
Routine Inspections: Periodic visual inspections of surface areas above cable routes for signs of subsidence or disturbance.
-
Thermographic Surveys: Infrared surveys to identify subtle temperature anomalies on the surface that may indicate hot spots below.
-
Targeted PD Testing: Regular partial discharge testing of critical joints and terminations.
-
-
3. Predictive Maintenance (PdM):
-
Digital Twins: Creating digital replicas of the underground network that integrate real-time operational data (load, temperature, environmental conditions) from embedded sensors.
-
Analytics & AI: Using predictive analytics and AI to analyze data patterns, forecast potential failures before they occur, and optimize maintenance schedules based on actual asset condition rather than fixed intervals. This allows for proactive repair or replacement, minimizing unplanned outages.
-
-
4. Spares Management: Ensuring an adequate stock of critical cable sections, splice kits, and specialized repair tools.
-
5. Training & Skill Development: Continuously training and certifying personnel in the latest fault detection, repair, and installation technologies and safety protocols.
Our commitment to a "one-stop supply" includes not just the initial underground cable laying equipment but also tools and expertise that support comprehensive fault detection, efficient repair, and intelligent long-term asset management, ensuring your network's enduring performance and reliability.